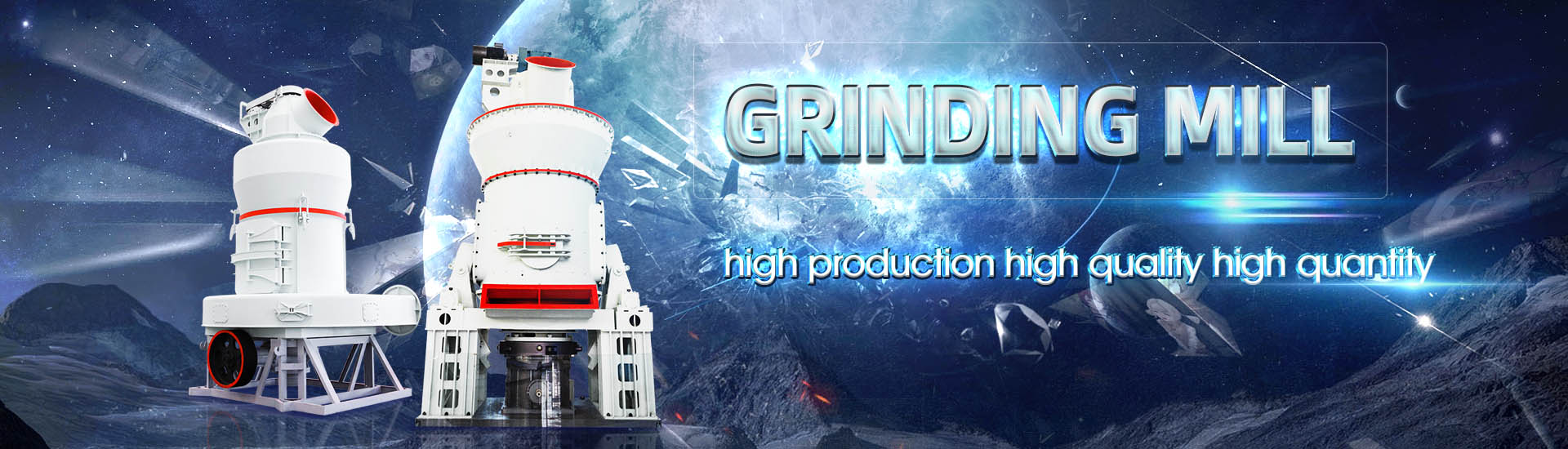
Iron ore powder processing plant highfine vertical mill
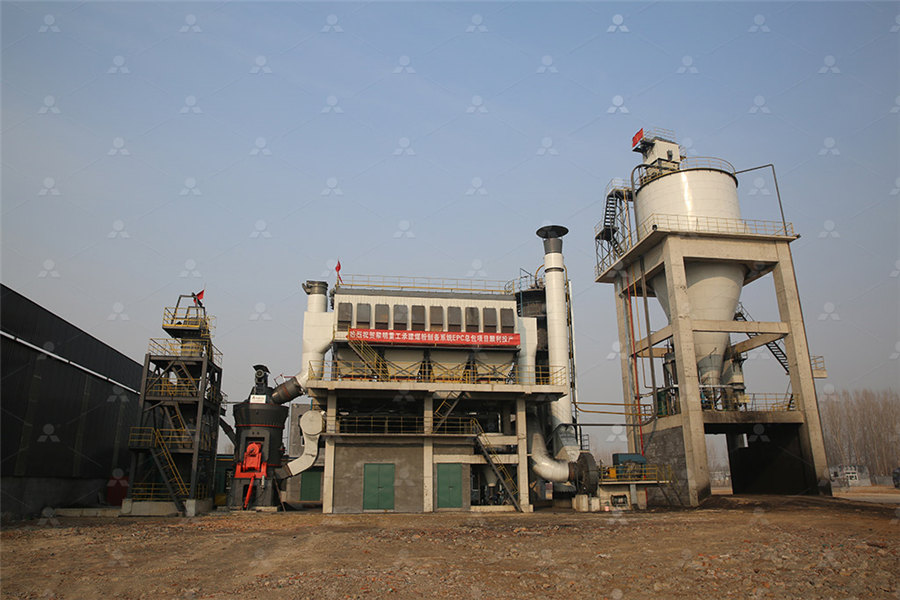
SBM Ultrafine Powder Technology Industrial Grinding Mill,
In the Iron Oxide Grinding Production Line, HGM80 ultrafine mill is used to process 1250 mesh iron oxide powder, with an hourly output of 12 tons This Coal Powder Making Plant in Bhutan 1,000 square meters of exhibition hall, covering 200+ mining equipment SBM's About Us2017年4月1日 Pilot plant test results with various ores showed that low energy consumption feature of vertical roller mills is applicable to the ore industry Grinding test results for zinc ore Operational parameters affecting the vertical roller mill 2015年3月15日 Schematic operation principle of a verticalrollermill nantly occurs by particleparticlecontacts or phasephasecontacts (Fandrich et al, 2007) Both breakage modes Research of iron ore grinding in a verticalrollermill
.jpg)
Research of iron ore grinding in a verticalrollermill
2015年3月15日 Two magnetite iron ores were comminuted with a pilot scale verticalrollermill The effect of three mill parameters was quantified using DoE methods The developed 2015年4月1日 Four different samples of iron ore were tested in a pilotscale grinding circuit with a vertical mill (Metso) and a high frequency screen (Derrick) The tests were performed using Vertical mill simulation applied to iron ores ScienceDirect2014年10月20日 In Brazil, during the last 10 years, regrind P80 sizes of approximately 40 to 20 μm have been necessary in all new iron and copper plants The use of conventional ball mills, adequate forRegrind of metallic ores with vertical mills: An 2022年10月20日 Making iron and steel from iron ore requires a long process of mining, crushing, separating, concentrating, mixing, agglomeration (sintering and pelletizing), and Iron Ore Processing, General SpringerLink
36.jpg)
Production of ultrafine iron powder by lowtemperature
2024年5月18日 With the microngrade highpurity iron ore concentrate processed by sand mill fine grinding as raw material, hydrogen reduction can produce microngrade ultrafine iron 2020年5月15日 Modern iron ore pelletizing process operations may be divided into two main process sections: feedstock preparation and agglomeration processes In most plants, the Development of a Novel Grinding Process to Iron Ore2024年1月3日 Investigation on the particle size and shape of iron ore pellet feed using ball mill and HPGR 909 areas of 500–1600 cm2 g1The concentrate must therefore be reground in order toInvestigation on the particle size and shape of iron ore 2014年11月1日 The sample of coarse iron ore was characterized in laboratory tests carried out in a small batch ball mill Selection and breakage function parameters were determined from the laboratory tests(PDF) Vertical mill simulation applied to iron
.jpg)
Iron Ore Processing, General SpringerLink
2022年10月20日 Iron ore handling, which may account for 20–50% of the total delivered cost of raw materials, covers the processes of transportation, storage, feeding, and washing of the ore en route to or during its various stages of treatment in the mill Since the physical state of iron ores in situ may range from friable, or even sandy materials, to monolithic deposits with hardness of 2024年9月16日 Highgrowth markets in copper, ironore, gold, leadzinc ores, mineral sands and rareearth the horizontal chamber of the tumbling ball mill into a vertical position, while adding an agitator screw to A TowerMill installation offers processing plants a simple, proven technology combined with reduced operating costs, to produce premium EIRICH TowerMill Vertical agitated media mill2015年3月15日 VRM has been widely researched in processing of cement (Ito et al 1997;Jorgensen 2005;Wang et al 2009, Ghalandari et al 2021), coal (Tontu 2020), iron ore (Reichert et al 2015), zinc ore (van Research of iron ore grinding in a verticalrollermill2022年3月8日 processing of iron ore slimes by state of art vertical pulsating wet high intensity high gradient magnetic separation The wash plant tails assayed 4645%Fe, 1803%SiO 2, 525% Al 2 O 3, and 610%LOI The process comprises of high pressure cycloning of dispersed pulp to remove slimes less than 10 micronsFine Particle Processing Of Iron Ore Slimes From Wash
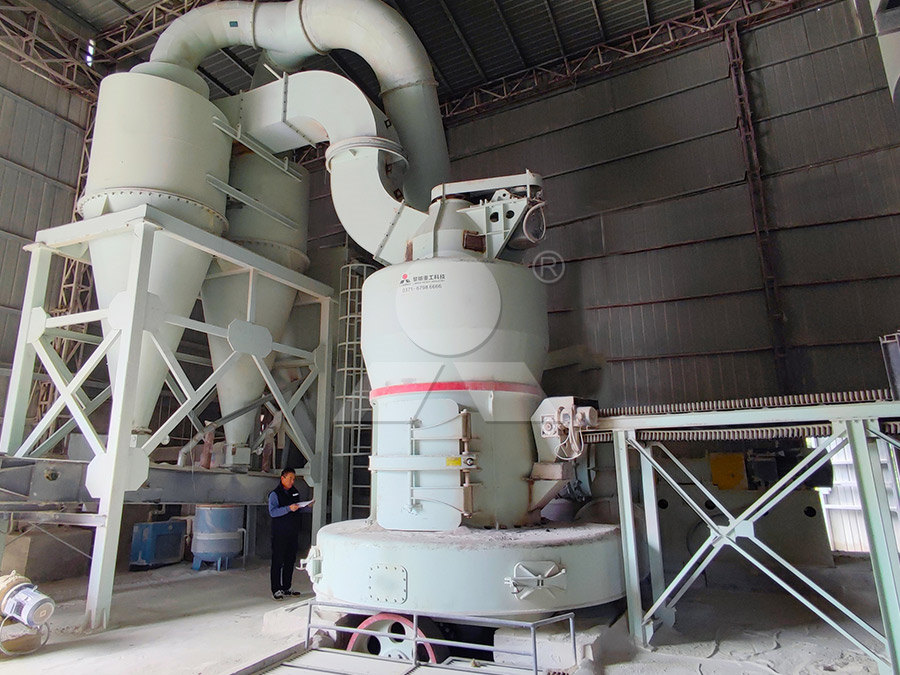
Recycling of steel plant mill scale via iron ore sintering plant
2012年4月1日 Adding mill scale as an ingredient into the iron ore sintering or pelletizing process is the main utilization approach for mill scale because of its high iron content and positional advantages [10 When iron ore is extracted from a mine, it must undergo several processing stages Six steps to process iron ore 1 Screening We recommend that you begin by screening the iron ore to separate fine particles below the crusher’s CSS before the crushing stage A static screen is used to divert the fine particles for crushingThe six main steps of iron ore processing Multotec2014年10月20日 Hematite and magnetite, the two predominant iron ores, require different processing routes Highgrade hematite direct shipping ores generally only require crushing and screening to meet the size Regrind of metallic ores with vertical mills: An overview of 1, Raymond Mill, HC series pendulum grinding mill: low investment costs, high capacity, low energy consumption, equipment stability, low noise; is the ideal equipment for wollastonite powder processing But the degree of largescale is relatively lower compared to vertical grinding mill 2, HLM vertical mill: largescale equipment, high capacity, to meet the largescale production Iron ore grinding mill Grinding plants for Iron Ore
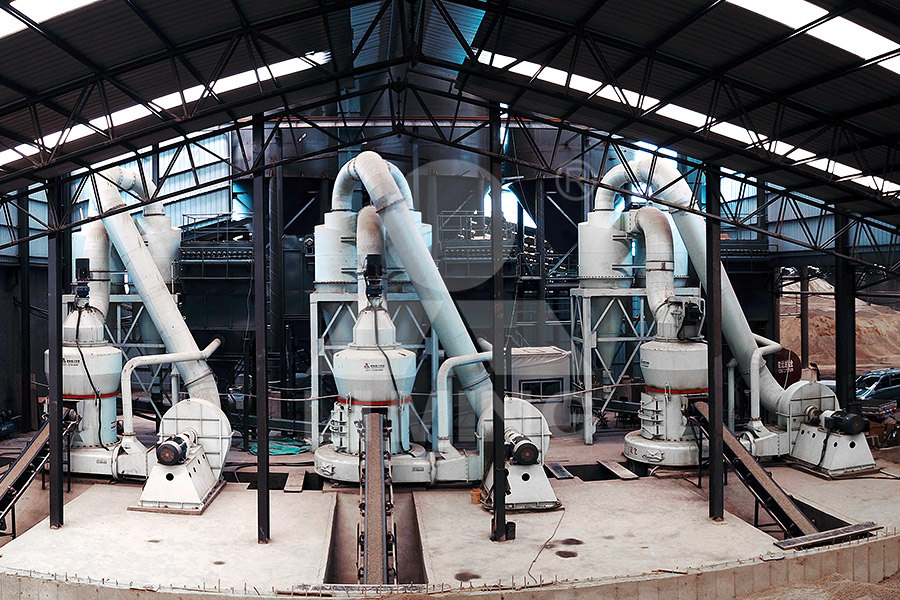
Comminution and classification technologies of iron ore
2022年1月1日 Rio Tinto Iron ore processing plants in the Pilbara region of Western Australia do not involve any chemical treatment The stirred mill is a fine grinding device capable of producing product particle sizes less than 1 μm A vertical or horizontal cylindrical vessel is charged with small grinding media made of steel or ceramic and the Star Trace offers turnkey solutions for Iron Ore processing plants We are one of the leading project suppliers for Iron ore processing plants and we work closely with our customers to fulfill their specific needs An internal cascading effect Iron Ore Processing Tools Iron Ore Processing 5 天之前 Copper industrial minerals include: natural copper, chalcopyrite, chalcocite, tetrahedrite, azurite, malachite, etc Chalcopyrite (a compound of copper, sulfur, and iron) is mined mainly, followed by chalcocite and bornite If Copper Ore Processing Plants, Flow And Iron ore with a high iron content above 62 % has become scarce and expensive While higher prices can be obtained for highgrade iron ore, the extraction of lowgrade iron ore is becoming increasingly uneconomic owing to falling prices In the meantime, there are also plants and process steps that can be designed as dry processes These Dry beneficiation of iron ore Mineral Processing
.jpg)
News Iron ore mineral processing with standing grinding
Iron ore dry grinding dry magnetic process of iron ore dressing mill for dry fine grinding, grinding fine reading can guarantee200 above 80%, equivalent to the common process of ball mill and screw grading machine or ball mill and cyclone grinding closed process, at the same time, iron ore dressing mill processing capacity is much higher than 2022年8月17日 Introduction of iron ore crusher: iron ore crusher is a kind of mechanical equipment that crushes iron ore raw ore step by step, from large pieces of raw iron ore (about 500mm) to millimeterlevel fine materials Usually, the iron ore dry separator is used to enrich the lean ore, and the enriched iron ore rich ore is sent to the ball mill for Iron ore crushing equipment and process flow sbmmill2023年3月21日 At present, the nonmetallic ore dry ultrafine grinding process equipment mainly includes Raymond mill, stirring mill, vibration mill, ring roller mill, ball mill and ultrafine vertical mill Ball mill can process 40200 mesh powder, the production capacity of a single machine is large, the performance is stable and reliable, but the energy The advantages of ultrafine vertical mill in the processing 2016年1月28日 There are large fine dumps which are still lying unutilised Demand for plants in iron ore processing were installed in Barbil region by BRPL based on allflux separator, wet high intensity magnetic separator, rod mill and ball mill Bhushan group has also installed beneficiation plant The JSPL, SAIL and EMIL are in process of Advances in Low Grade Iron Ore Beneficiation MECON
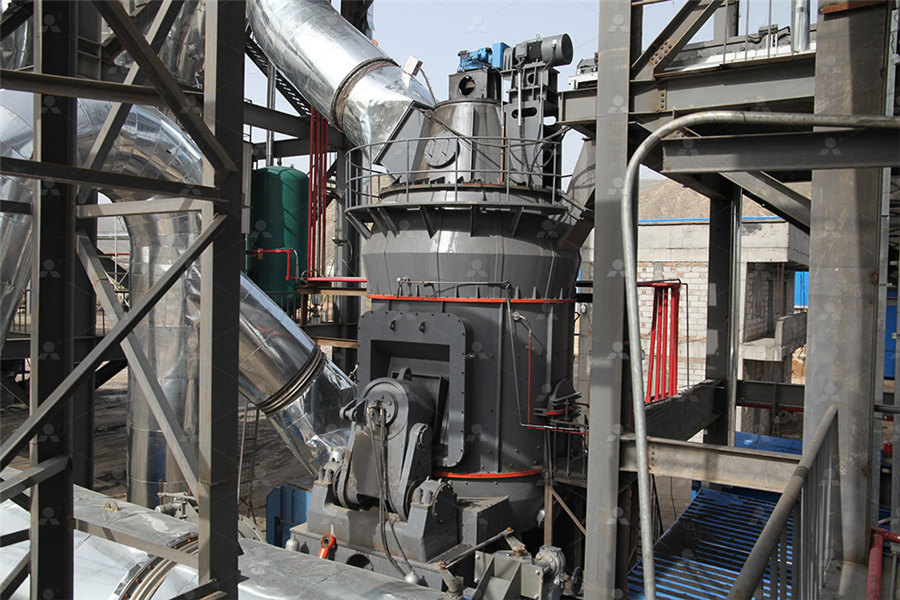
Equipment Required To Build A Manganese Ore Processing Plant
2024年11月21日 This is usually achieved using jaw crushers or impact crushers, which can effectively reduce the size of the ore to facilitate subsequent processing Once the ore is crushed to the appropriate size, it enters the grinding stage, where the manganese ore is refined into a fine powder using specialized equipment such as ball mills or vertical 2018年9月17日 The use of vertical stirred mills in the mining industry has increased remarkably over the past few decades, as a result of growing requirement for finer ore grindingDEVELOPMENT OF A LABORATORY TEST TO DESIGN VERTICAL STIRRED MILLS 2023年5月9日 * Technical contribution to the 44th Ironmaking and Raw Materials Seminar, 15rd Brazilian Symposium on Iron Ore and 2nd Brazilian Symposium on Agglomeration of Iron Ore, September 15th to 18th, 2014, Belo Horizonte, MG, Brazil Figure 5Improvement of the granulation capacity In addition, with regard to wet granule and when the intensive mixer is in VERTICAL INTENSIVE MIXING FOR PROCESSING FINER 2024年10月15日 Vertical stirred mills are a fine grinding equipment that covers advantages of low rotation speed, high reliability and long life cycle The significant advantages that the vertical stirred mills have over the ball mills are Vertical Stirred Mill Mineral Processing
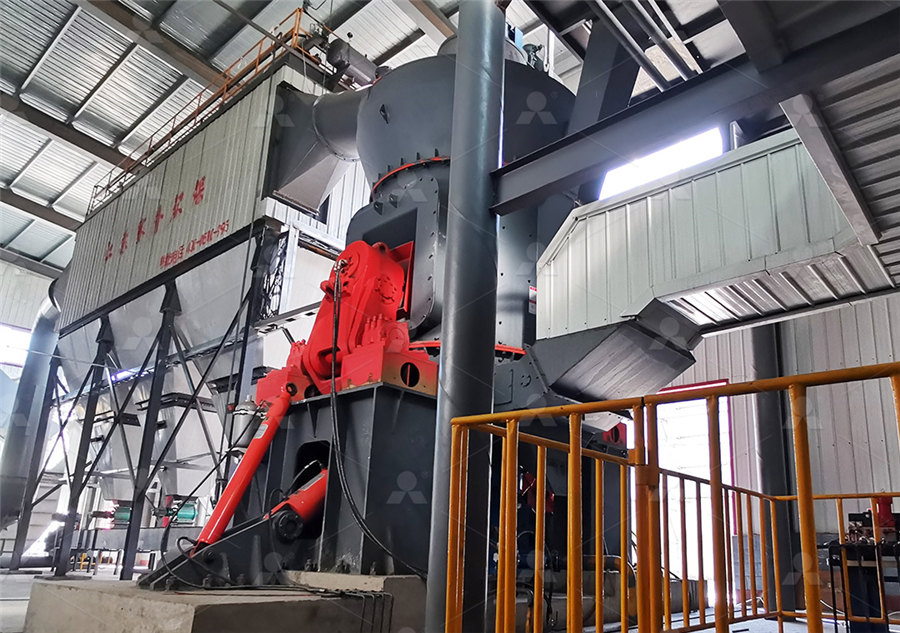
Ultra fine grinding of silver plant tailings of refractory
2013年12月3日 UFG Group, Division of Mineral Coal Processing, Department of Mining Engineering, Karadeniz Technical University, Trabzon 61080, Turkiye Received 21 March 2013; accepted 25 April 2013 Abstract: Ultra fine grinding of the plant tailings of a refractory silver ore was studied using a laboratory type vertical stirred media mill2023年4月23日 Comminution is a very important and resultdetermining step in mineral processing This is because further downstream processes in the beneficiation chain depend entirely on it(PDF) Grinding Media in Ball MillsA Review ResearchGate2022年1月1日 This chapter introduces the principle of how lowgrade iron ores are upgraded to high quality iron ore concentrates by magnetic separation From the plant results, an iron ore concentrate containing 675% Fe could be produced from a runofmine ore containing 301% Fe, at a mass yield of 349% to the iron ore concentrate, an iron recovery Physical separation of iron ore: magnetic separationRaw mill is generally called cement raw mill, raw mill in cement plant, it refers to a common type of cement equipment in the cement plantIn the cement manufacturing process, raw mill in cement plant grind cement raw materials into the raw mix, and the raw mix is sent to the cement kiln to make cement clinker, next, clinker and other admixtures will be ground into finished cement by Raw Mill, Cement Raw Mill, Raw Mill In Cement Plant
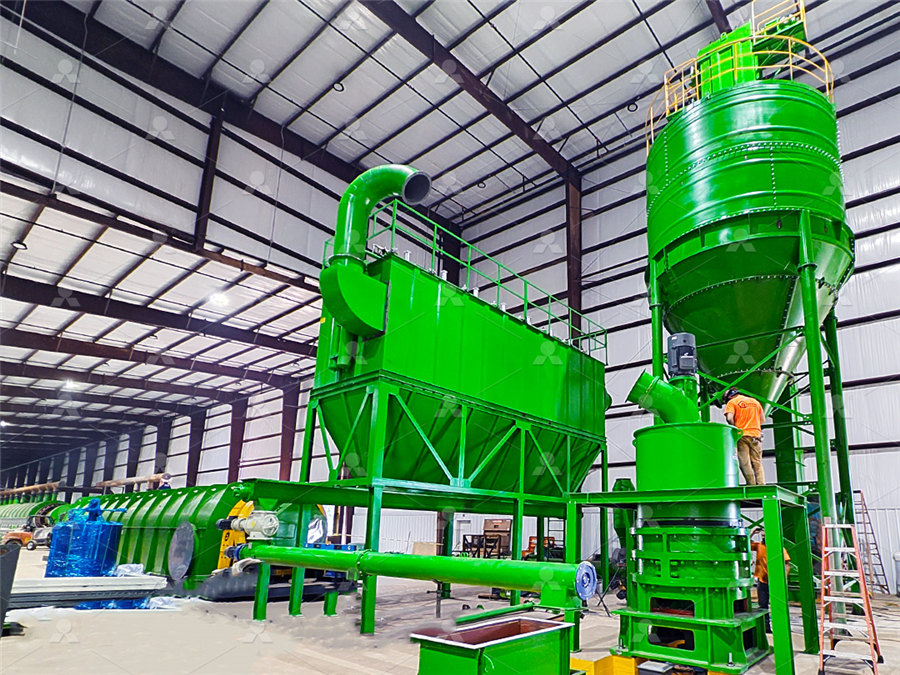
Effects of process parameters on the growth behavior and
2022年8月10日 This work proposes a novel horizontal highshear granulator for iron ore granulation before sintering process The granulation behavior such as growth process and structure of granules were firstly analyzed, followed by the effects of operation conditions such as water content, initial particle size distribution, and the concentrate ratio The results show that 2009年8月1日 Adding mill scale as an ingredient into the iron ore sintering or pelletizing process is the main utilization approach for mill scale because of its high iron content and positional advantages [10 Recycling of steel plant mill scale via iron ore pelletisation process 2016年12月31日 Sahoo et al (1980) and Krishna et al (2013), also discussed mineralogical characteristics of some off grade Iron ore in India and the use of Heavy Medium Separation in the processing of Iron Ore (PDF) An Study on Preparation and Utilization of Tourmaline Table 3 Power Consumption Of Roller Press Grinding System Overall, we can conclude the three tables: After the longterm operation, although unit raw material grinding power consumption of the cement roller press grinding system is still low, the indexes of the vertical roller mill grinding system are very close to it, among which the output power of the vertical mill and the roller Comparison Of Vertical Roller Mill And Roller Press Mill
.jpg)
Investigation on the particle size and shape of iron ore
2024年1月3日 Investigation on the particle size and shape of iron ore pellet feed using ball mill and HPGR 909 areas of 500–1600 cm2 g1The concentrate must therefore be reground in order to2014年11月1日 The sample of coarse iron ore was characterized in laboratory tests carried out in a small batch ball mill Selection and breakage function parameters were determined from the laboratory tests(PDF) Vertical mill simulation applied to iron 2022年10月20日 Iron ore handling, which may account for 20–50% of the total delivered cost of raw materials, covers the processes of transportation, storage, feeding, and washing of the ore en route to or during its various stages of treatment in the mill Since the physical state of iron ores in situ may range from friable, or even sandy materials, to monolithic deposits with hardness of Iron Ore Processing, General SpringerLink2024年9月16日 Highgrowth markets in copper, ironore, gold, leadzinc ores, mineral sands and rareearth the horizontal chamber of the tumbling ball mill into a vertical position, while adding an agitator screw to A TowerMill installation offers processing plants a simple, proven technology combined with reduced operating costs, to produce premium EIRICH TowerMill Vertical agitated media mill
.jpg)
Research of iron ore grinding in a verticalrollermill
2015年3月15日 VRM has been widely researched in processing of cement (Ito et al 1997;Jorgensen 2005;Wang et al 2009, Ghalandari et al 2021), coal (Tontu 2020), iron ore (Reichert et al 2015), zinc ore (van 2022年3月8日 processing of iron ore slimes by state of art vertical pulsating wet high intensity high gradient magnetic separation The wash plant tails assayed 4645%Fe, 1803%SiO 2, 525% Al 2 O 3, and 610%LOI The process comprises of high pressure cycloning of dispersed pulp to remove slimes less than 10 micronsFine Particle Processing Of Iron Ore Slimes From Wash 2012年4月1日 Adding mill scale as an ingredient into the iron ore sintering or pelletizing process is the main utilization approach for mill scale because of its high iron content and positional advantages [10 Recycling of steel plant mill scale via iron ore sintering plantWhen iron ore is extracted from a mine, it must undergo several processing stages Six steps to process iron ore 1 Screening We recommend that you begin by screening the iron ore to separate fine particles below the crusher’s CSS before the crushing stage A static screen is used to divert the fine particles for crushingThe six main steps of iron ore processing Multotec
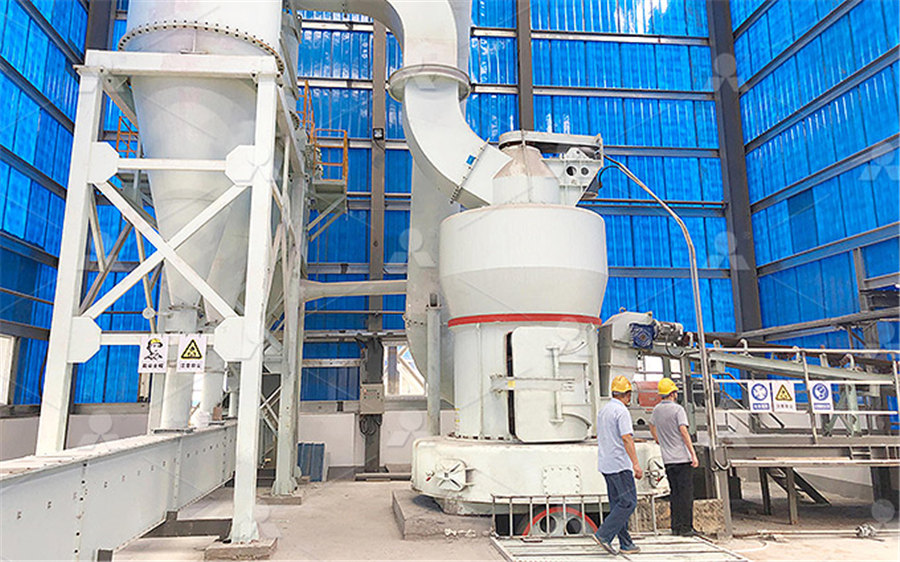
Regrind of metallic ores with vertical mills: An overview of
2014年10月20日 Hematite and magnetite, the two predominant iron ores, require different processing routes Highgrade hematite direct shipping ores generally only require crushing and screening to meet the size 1, Raymond Mill, HC series pendulum grinding mill: low investment costs, high capacity, low energy consumption, equipment stability, low noise; is the ideal equipment for wollastonite powder processing But the degree of largescale is relatively lower compared to vertical grinding mill 2, HLM vertical mill: largescale equipment, high capacity, to meet the largescale production Iron ore grinding mill Grinding plants for Iron Ore