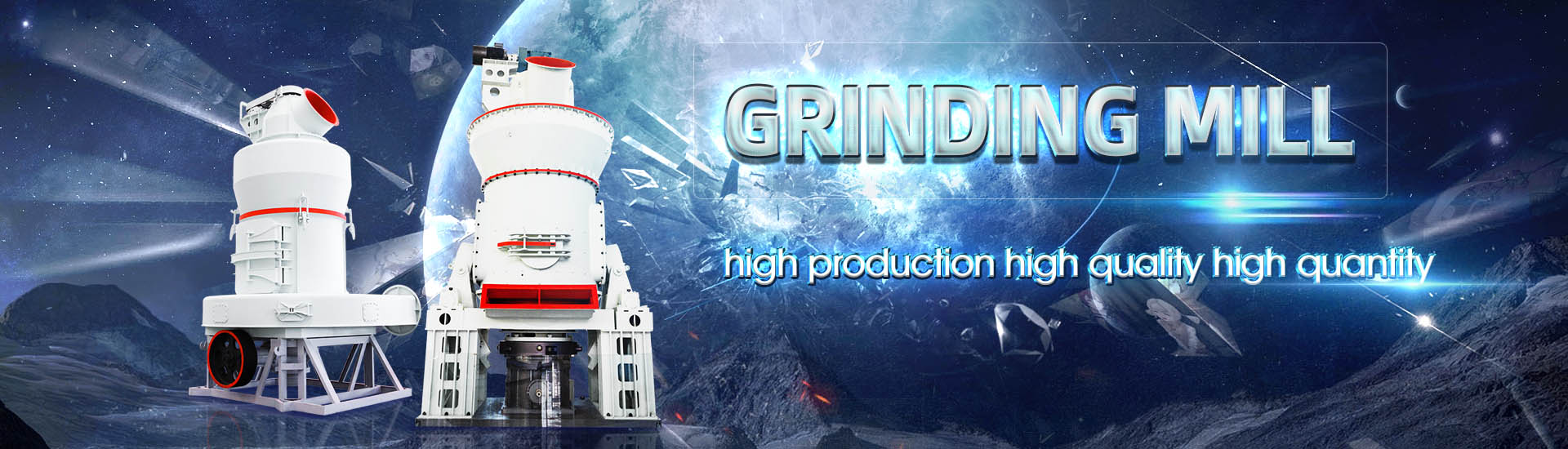
Highefficiency and energysaving 200mesh coal powder mill
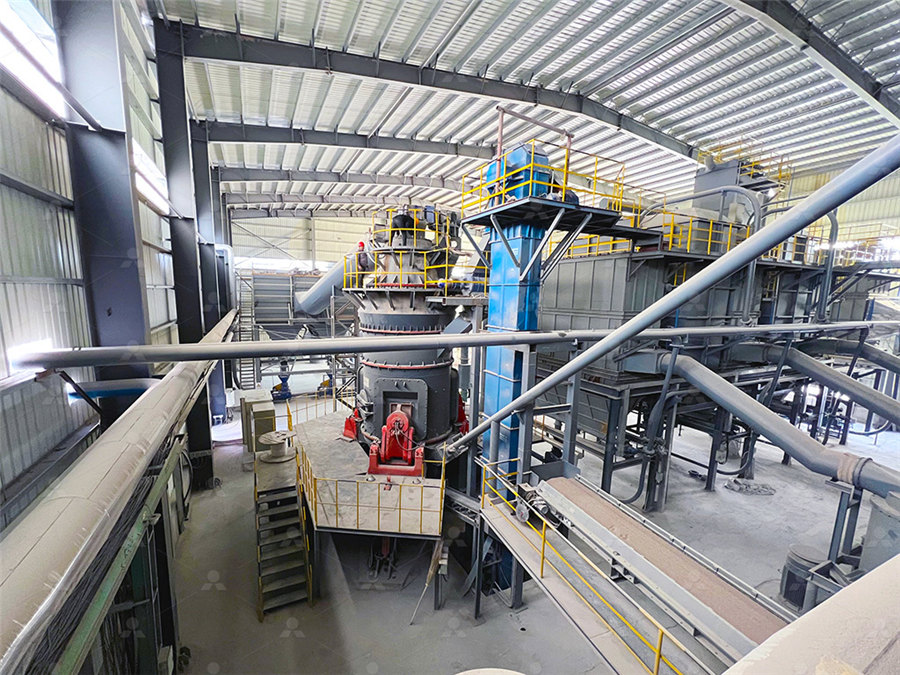
Choosing the right vertical mill for 200 mesh coal powder
2024年10月13日 Vertical Roller Mill: These mills are known for their high efficiency and energy savings The vertical roller mill is capable of producing highquality 200 mesh coal powder, 2024年9月25日 High Efficiency Air Swept Coal Mill 200mesh Size US$10,00000 / set: 1 set (MOQ) : Product Details[Hot Item] High Efficiency Air Swept Coal Mill 200mesh Size2020年8月12日 Obtained results indicate that grinding pressure, primary air (PA) temperature and mill motor current have a tendency to rise by increasing coal feeding mass flow rates for all used coalAn investigation of performance characteristics Activated carbon is widely used in the field of environmental protection, such as sewage treatment, wastewater purification, flue gas purification, etc 200 mesh coalbased activated 200 Mesh Coal Activated Carbon Processing Technology And 200 Mesh Coal
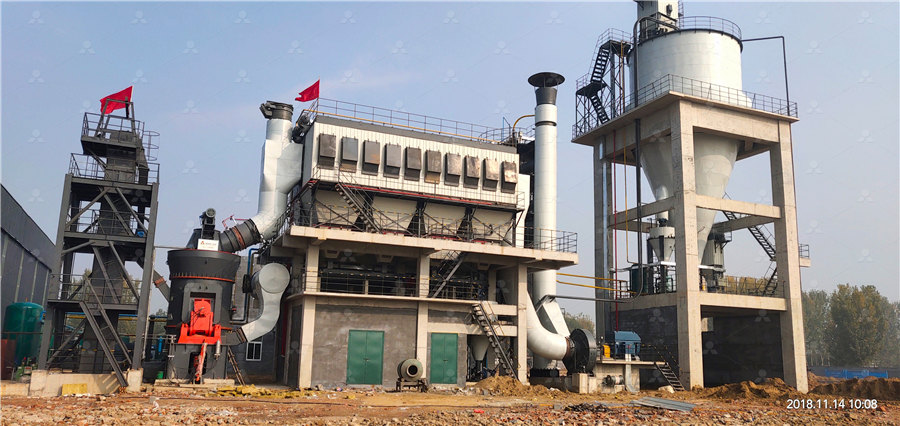
200 mesh coal mill equipment manufacturers price understanding of coal mill
After the coal is finely ground to 200 mesh by a coal mill, it becomes coal powder, which has a higher combustion utilization rate and more economic value So, what is the manufacturer's coal passing through 200 mesh (75 µm) is weighed and the HGI is derived from the empirical equation: HGI = 693W +13 where W is the weight of crushed coal passing through 200 mesh A Study on 500 MW Coal Fired Boiler Unit’s Bowl Mill 2020年11月11日 The roller mill’s ability to reduce materials to a uniform particle size provides more control of product characteristics and minimizes waste, as shown in Figure 1 The mill’s Roller mills: Precisely reducing particle size with greater 2022年1月23日 This work concentrates on the energy consumption and grinding energy efficiency of a laboratory vertical roller mill (VRM) under various operating parameters For design of experiments (DOE), the response surface method Analysis and Optimization of Grinding
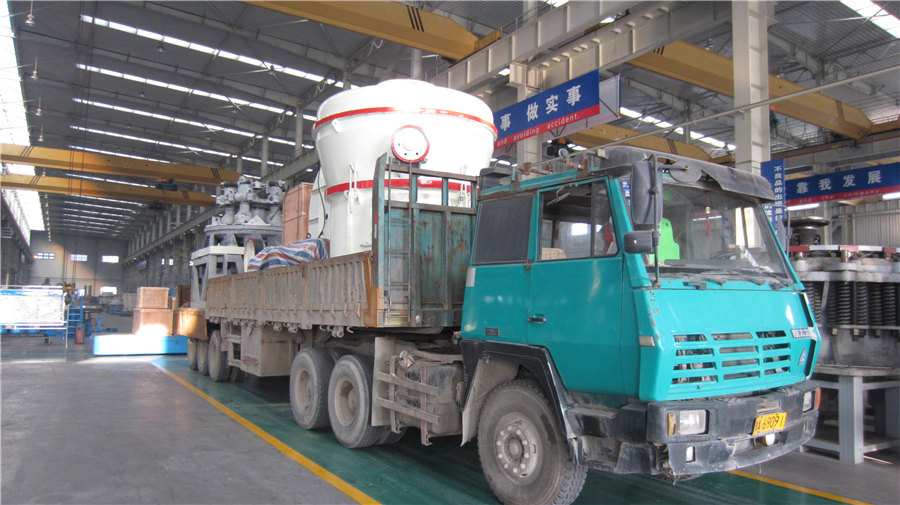
Coal Mill an overview ScienceDirect Topics
Mills are mechanical devices used to break different types of solid materials in small pieces by grinding, crushing or cutting In pulverised coalfired power plants, a pulveriser coal mill grinds 2020年3月19日 ONLINE COAL FLOW MEASURING AND BALANCING (CONTROL) AND ONLINE COAL FINENESS MEASURING SYSTEM FOR COMBUSTION OPTIMISATION IN A THERMAL BOILER Suresh G Chandwani1, Dr Francesco Turoni2, Reinhardt Kock2, Dr Michael Haug2, Dr Michael Schreiber2 1NSGuzder Company Pty Ltd, Neville House, Currimbhoy CPRI Online Coal Flow Balancing and Fineness 2020年8月12日 In a power plant, the coal mill is the critical equipment, whose effectiveness impacts the overall power plant efficiency Uniform coal feeding mass flow rate and required particle size and temperature at the outlet channel throughout with better classifier performance are crucial indicators that characterize the coal mill performanceAn investigation of performance characteristics and 2021年11月1日 Semantic Scholar extracted view of "Highefficiency and energyconservation grinding technology using a special ceramicmedium stirred mill: A pilotscale study" by Xiaolong Zhang et al Vertical stirred mills (VSM) are widely used for powder processing in many situations like mechanical alloying preparation and raw material crushing and Highefficiency and energyconservation grinding
.jpg)
Strategies of High Efficiency Recovery and Energy Saving
我们已与文献出版商建立了直接购买合作。 你可以通过身份认证进行实名认证,认证成功后本次下载的费用将由您所在的图书馆支付 您可以直接购买此文献,1~5即可下载全文,部分资源由于网络原因可能需要更长时间,请您耐心等待哦~2023年4月23日 high speeds of about 90%, causing breakage o f large ore particles wh ilst reducing the mill’s energy efficiency The num The num ber of cataracting media increases as mill speed increases (PDF) Grinding Media in Ball MillsA Review ResearchGate2022年1月1日 A pilotscale grinding technology of ceramic medium stirred mill was proposed in this study Based on the specific productivity and grinding efficiency, the appropriate grinding parameters were ascertained as follows: material ball ratio of 07, ceramic ball medium size ratio (10 mm: 15 mm: 20 mm = 3:2:5), stirring speed of 110 rpm, grinding concentration of 50%, Highefficiency and energyconservation grinding technology using 2021年3月1日 Rapid progress in sustainable technologies is the main trait of the modern industrial society (Ma et al, 2019; Zayed et al, 2021)Recently, modeling, optimization and control of industrial reheating furnaces (IRFs) have received much interest since the 1970s, due to the increase in global energy demand and the development of a highspeed rolling mill for the Industrial reheating furnaces: A review of energy efficiency
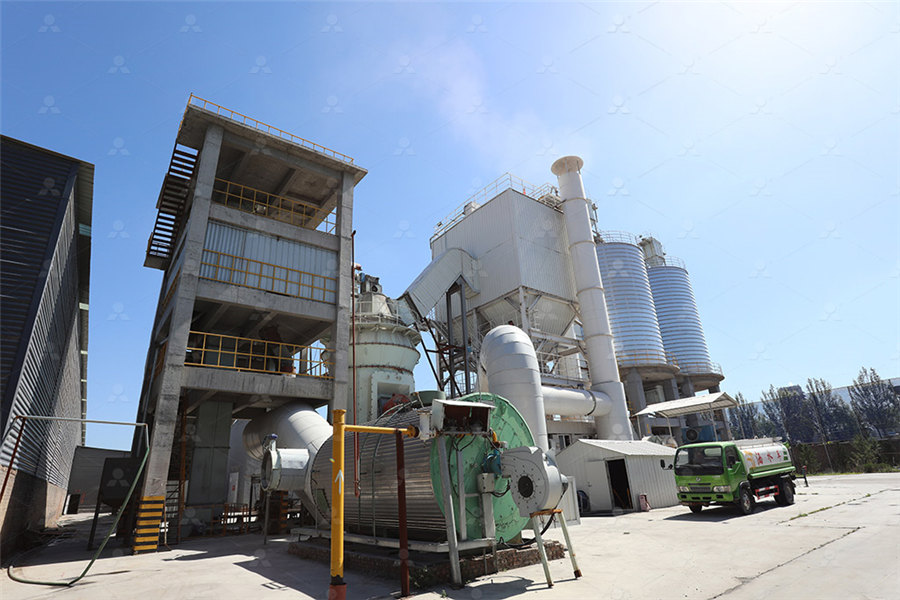
A Review of the Grinding Media in Ball Mills for Mineral
2023年10月27日 The ball mill is a rotating cylindrical vessel with grinding media inside, which is responsible for breaking the ore particles Grinding media play an important role in the comminution of mineral ores in these mills This work reviews the application of balls in mineral processing as a function of the materials used to manufacture them and the mass loss, as 2022年1月23日 This work concentrates on the energy consumption and grinding energy efficiency of a laboratory vertical roller mill (VRM) under various operating parameters For design of experiments (DOE), the response surface method (RSM) was employed with the VRM experiments to systematically investigate the influence of operating parameters on the energy Analysis and Optimization of Grinding Performance of 2021年11月1日 A pilotscale grinding technology of ceramic medium stirred mill was proposed in this study Based on the specific productivity and grinding efficiency, the appropriate grinding parameters were Highefficiency and energyconservation grinding 2009年6月1日 The present literature review explores the energyefficient ultrafine grinding of particles using stirred mills The review provides an overview of the different techniques for size reduction and Comparison of energy efficiency between ball mills and stirred mills
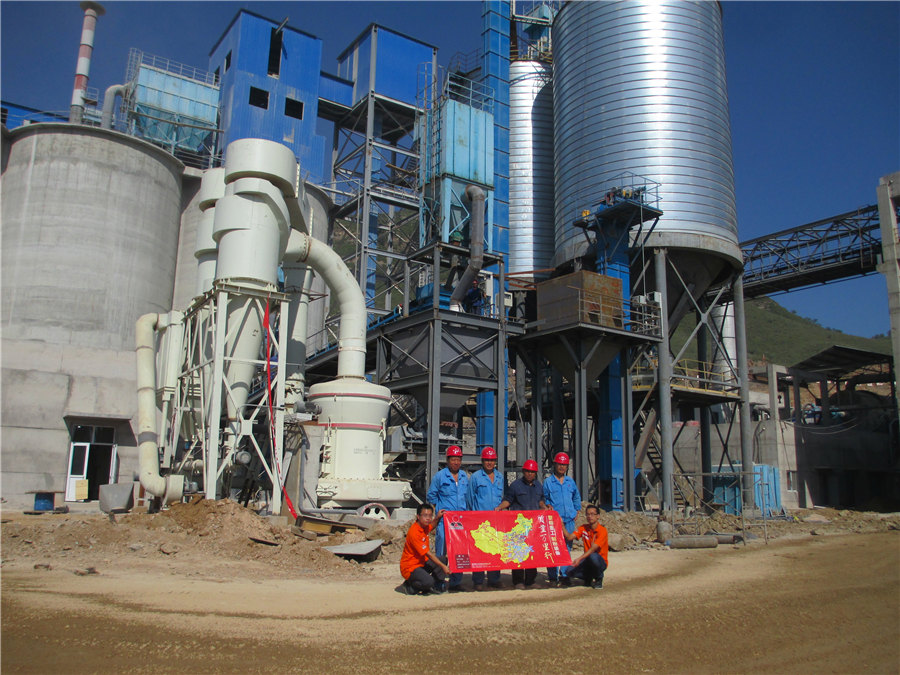
Fact sheet Energy use in the steel industry
2022年5月27日 Table 1 shows the main energy inputs of steel production and their applications as energy and reducing agents Energy input Application as energy Application as energy and reducing agent Coal Blast furnace (BF), sinter and coking plant Coke production, BF pulverised coal injection Electricity EAF, rolling mills and motors Natural gas Furnaces 2021年1月22日 In the whole process of cement production, the electricity consumption of a raw material mill accounts for about 24% of the total Based on the statistics of the electricity consumption of the raw material mill system of 1005 production lines in China between 2014 and 2019, it is found that the average electricity consumption of the raw material preparation A Survey and Analysis on Electricity Consumption of Raw Material Mill 2020年12月1日 Pulp making is a highenergyconsumption process that obtains its energy by directly combusting coal and black liquor in boiler, which is low efficiency and high emission Minisulfide sulfite anthraquinone (MSSAQ) pulp making technology can reach 55%–66% pulping yield but suffers from bad economic performanceIntegrated chemical looping combustion in pulp mill for high energy 2021年3月23日 New ball mill drive system with the prototype energysaving SMH motor [37] Startup of the LSPMSM SMH1732T motor with a filled ball mill after two hours of downtime: (a) active power, (b Energy Efficiency Analysis of Copper Ore Ball Mill Drive
.jpg)
SBM Ultrafine Powder Technology Industrial Grinding Mill,
This Coal Powder Making Plant in Bhutan utilizes our CLRM1300 Raymond grinding mill to achieve 80400 mesh coal powder production with high capacity The customer celebrated the factory’s commencement with prayers for a bright and successful future Equipment: HGM Series Ultrafine Grinding Mill; Feeding size: 200325 Mesh, D97; Output 2017年1月1日 Conventional milldrying systems are included in the usual scope of supply of MHPSE DGS mills (Fig 520) with raw coal capacity up to a 240 t/h and NV mills raw coal capacity ranging from 10 to 140 t/h can be used as the drying technology in the overall predrying concept DGS technology involves the raw coal and flue gases being initially put Highefficiency pulverized coal power generation using low 2020年11月11日 The roller mill’s ability to reduce materials to a uniform particle size provides more control of product characteristics and minimizes waste, as shown in Figure 1 The mill’s controlled reduction action requires less energy than other grinding methods, improving production efficiency and saving energy dollars Roller mill components and Roller mills: Precisely reducing particle size with greater Activated carbon is widely used in the field of environmental protection, such as sewage treatment, wastewater purification, flue gas purification, etc 200 mesh coalbased activated carbon is the mainstream of activated carbon in northern China What is the processing technology of 200 mesh coalbased activated carbon? What type of equipment is the 200 200 Mesh Coal Activated Carbon Processing Technology And 200 Mesh Coal
.jpg)
MICRONIZER JET MILL Sturtevant Inc
2020年7月13日 highefficiency cyclone collector, single batch bag, or continuous cleaning dust ENERGY REQUIREMENTS CAPACITY MILL 1 COMPRESSED AIR 2 SUPERHEATED 3 HP LBS/HR SIZE/DIA STEAM 2" 30 80 10 1/2 1 200 mesh 100% 20 mesh 100% 325 mesh 100% 80 mesh 100% 100 mesh2019年12月11日 Upgrading and efficiency improvement in coalfired power plants 5 The efficiencies of coalfired plants will normally decrease over time as components suffer deterioration with age and use The losses that develop in the earlier part of the life of a plant are generally containable by employing good operating and maintenance practicesUpgrading and efficiency improvement in coalfired 2022年10月1日 Coal is a very vital and widely used fossil fuel that supports the rapid development of China's economy Meanwhile, coal consumption will still account for more than half of China's primary energy consumption in the next 30 years [1, 2]Coal is mainly used for thermal power generation, city heating, and coal chemical conversion [3]To improve Critical parameters and risk evaluation index for spontaneous 2021年10月26日 Fully utilizing the energy generated by the explosion of pulverized coal will contribute to realize the clean and efficient exploitation of coal resources The pulverized coal explosion characteristics will be a farreaching and important task to explore In this paper, ten kinds of lowquality coals such as high sulfur, high ash, and low metamorphic degree coals Evaluation on explosion characteristics and parameters of
.jpg)
Study on the Damage Mechanism and Energy Evolution
2022年11月18日 In this study, cyclic loading–unloading experiments on coal samples with different moisture contents were conducted The damage mechanism was investigated through acoustic emission (AE) monitoring The validity of the average frequency and rise angle (RA–AF) correlation for the fracture evolution of waterbearing coal samples under cyclic loading was 2002年11月1日 Unfortunately, the energy efficiency is extremely low in mining operations For instance, the energy efficiency is about 10% in percussive rock drilling (Carrol 1985), 35% in rock crushing The energy efficiency of ball milling in comminution2011年10月1日 Pulverizing system is the main energyconsumption equipment in coalfired power plant, so it is of great significance to study energysaving and optimization of pulverizing systemEnergySaving and Optimization of Pulverizing System in Coal Predating the development of pulverized coal firing came the development of pulverizers used in the processing of minerals In preparing coal, or other materials, in sizes approximating talcum powder or finer (eg, coal produced at >70% 50 mesh), two fundamental methods apply: impaction and attrition [13]Pulverised Coal an overview ScienceDirect Topics
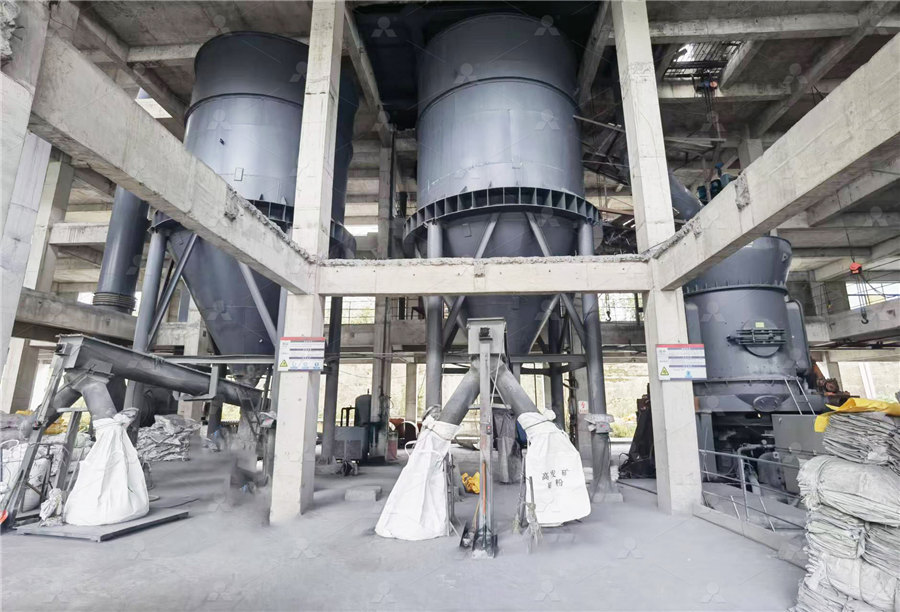
Design and Application of HighEfficiency and EnergySaving
2011年8月1日 The process of liner wear and the changing characteristics of the ability of crushing and grinding in the coal pulverizer are analyzed, a new type of cylinder liner is developed, which has a multistep wave crest The small balls on the liner are stuck by the steps, in this way, the wear of the liner wave crest is lightened, so it can keep a longterm stability, it High efficiency and energy saving raymond mill grinder stone raymond ygm 95 raymond pendulum mill for calcite suppliers new Manufacturer: Raymond; Model: YGM95; YGM raymond grinding mill is a highefficiency and energysaving mill and has been widely used in material processing field involving mining, construction, metallurgy, etc It is Used Raymond Vertical Mills for sale Raymond equipment Readers of this article are urged to also study articles about energy audits at pulp and paper mills (Sweet 1991; Kong et al 2016; Reese 2018; Reese and Deodar 2018; Gilbreath 2019; Reese et al 2020) The largest and quickest savings in energy in pulp and paper mills usually are achieved as a result of system auditsEnergy efficiency challenges in pulp and paper 2020年3月19日 ONLINE COAL FLOW MEASURING AND BALANCING (CONTROL) AND ONLINE COAL FINENESS MEASURING SYSTEM FOR COMBUSTION OPTIMISATION IN A THERMAL BOILER Suresh G Chandwani1, Dr Francesco Turoni2, Reinhardt Kock2, Dr Michael Haug2, Dr Michael Schreiber2 1NSGuzder Company Pty Ltd, Neville House, Currimbhoy CPRI Online Coal Flow Balancing and Fineness
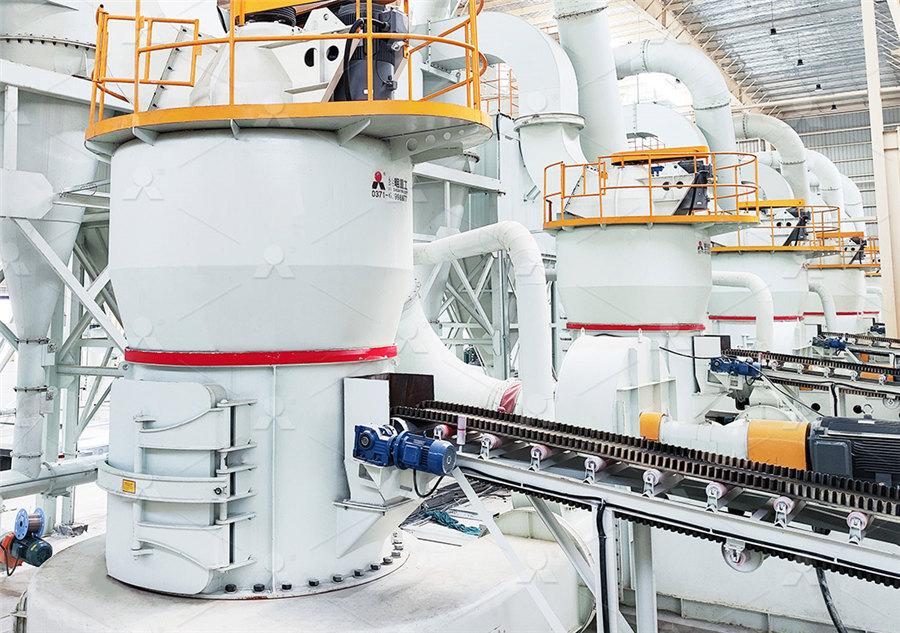
An investigation of performance characteristics and
2020年8月12日 In a power plant, the coal mill is the critical equipment, whose effectiveness impacts the overall power plant efficiency Uniform coal feeding mass flow rate and required particle size and temperature at the outlet channel throughout with better classifier performance are crucial indicators that characterize the coal mill performance2021年11月1日 Semantic Scholar extracted view of "Highefficiency and energyconservation grinding technology using a special ceramicmedium stirred mill: A pilotscale study" by Xiaolong Zhang et al Vertical stirred mills (VSM) are widely used for powder processing in many situations like mechanical alloying preparation and raw material crushing and Highefficiency and energyconservation grinding 我们已与文献出版商建立了直接购买合作。 你可以通过身份认证进行实名认证,认证成功后本次下载的费用将由您所在的图书馆支付 您可以直接购买此文献,1~5即可下载全文,部分资源由于网络原因可能需要更长时间,请您耐心等待哦~Strategies of High Efficiency Recovery and Energy Saving 2023年4月23日 high speeds of about 90%, causing breakage o f large ore particles wh ilst reducing the mill’s energy efficiency The num The num ber of cataracting media increases as mill speed increases (PDF) Grinding Media in Ball MillsA Review ResearchGate
.jpg)
Highefficiency and energyconservation grinding technology using
2022年1月1日 A pilotscale grinding technology of ceramic medium stirred mill was proposed in this study Based on the specific productivity and grinding efficiency, the appropriate grinding parameters were ascertained as follows: material ball ratio of 07, ceramic ball medium size ratio (10 mm: 15 mm: 20 mm = 3:2:5), stirring speed of 110 rpm, grinding concentration of 50%, 2021年3月1日 Rapid progress in sustainable technologies is the main trait of the modern industrial society (Ma et al, 2019; Zayed et al, 2021)Recently, modeling, optimization and control of industrial reheating furnaces (IRFs) have received much interest since the 1970s, due to the increase in global energy demand and the development of a highspeed rolling mill for the Industrial reheating furnaces: A review of energy efficiency 2023年10月27日 The ball mill is a rotating cylindrical vessel with grinding media inside, which is responsible for breaking the ore particles Grinding media play an important role in the comminution of mineral ores in these mills This work reviews the application of balls in mineral processing as a function of the materials used to manufacture them and the mass loss, as A Review of the Grinding Media in Ball Mills for Mineral 2022年1月23日 This work concentrates on the energy consumption and grinding energy efficiency of a laboratory vertical roller mill (VRM) under various operating parameters For design of experiments (DOE), the response surface method (RSM) was employed with the VRM experiments to systematically investigate the influence of operating parameters on the energy Analysis and Optimization of Grinding Performance of
.jpg)
Highefficiency and energyconservation grinding
2021年11月1日 A pilotscale grinding technology of ceramic medium stirred mill was proposed in this study Based on the specific productivity and grinding efficiency, the appropriate grinding parameters were