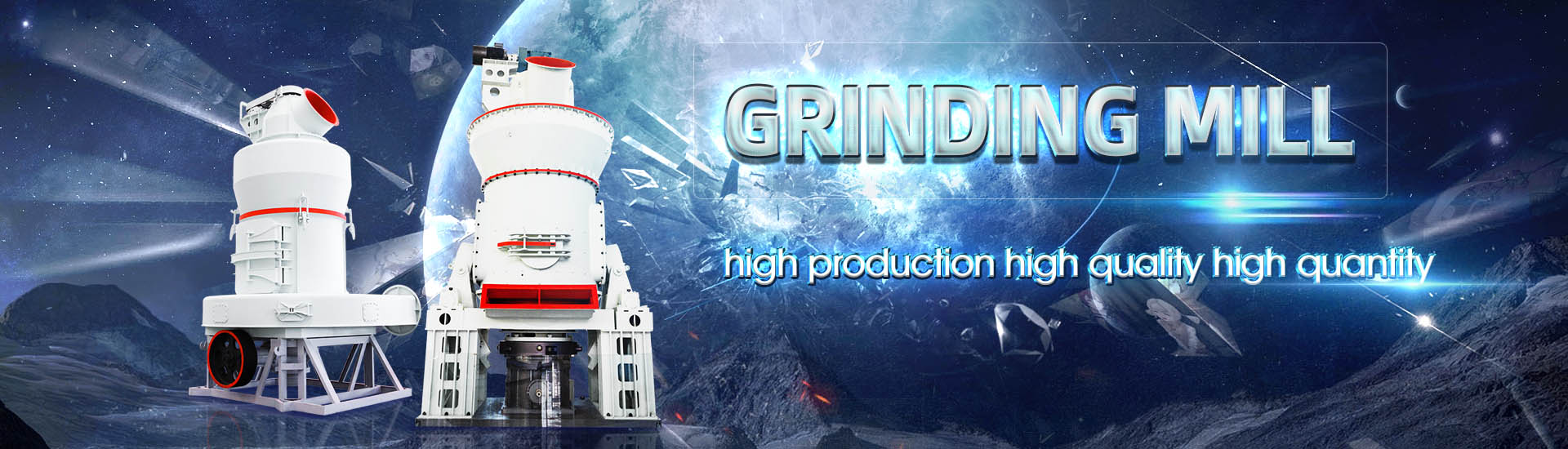
Dry grid ball mill steel ball loading Filling ratio
.jpg)
Influences of operating parameters on dry ball mill
Within the context, the influence of operating parameters such as mill speed, ball filling ratio, ball size distribution, powder filling ratio, grinding aid dosage and grinding time were studied The 2021年1月22日 The dry grinding experiment was operated in the ball mill (Φ460 × 600 mm) with steel ball as grinding media at mill speed 47 r/min, spacefilling factor φ 30%, and material ball An innovative approach for determining the grinding media 2018年5月18日 GRINDING STEEL BALLS FOR BALL MILLS Specifications Date of validity: 2016 07 – 01 1 FIELD OF APPLICATION This standard applies to steel grinding balls STEEL MILLING BALLS FOR BALL MILLS Energosteel2023年5月28日 Relevant parameters such as the materialball ratio, grinding concentration, filling ratio, and medium filling ratio can accurately reflect the mill load condition For example, Mill Load Measurement SpringerLink
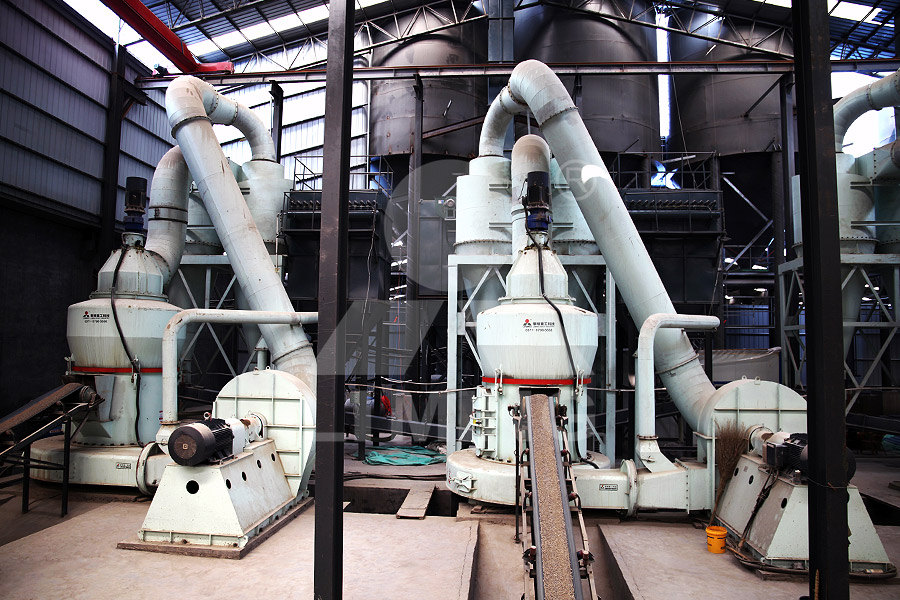
An improved method for grinding mill filling measurement and
2021年1月1日 Monitoring mill load is vital for the optimization and control of grinding process This study proposed the use of an instrumented grinding media to assess solid loading inside 2021年9月23日 Monitoring mill load is vital for the optimization and control of grinding process This study proposed the use of an instrumented grinding media to assess solid loading inside Assessing load in ball mill using instrumented grinding media2023年4月13日 The effect of ball size and interstitial filling on the performance of dry ball mill grinding was investigated for a limestonetype brecciated uranium ore The optimum grinding Optimization of Ball Mill Grinding of a LimestoneType 2021年3月12日 increase the proportion of 90mm • Check filling level of the first chamber: if mill axis in the second chamber We can then measure the material fineness evolution of BALL MILLS Ball mill optimisation Holzinger Consulting
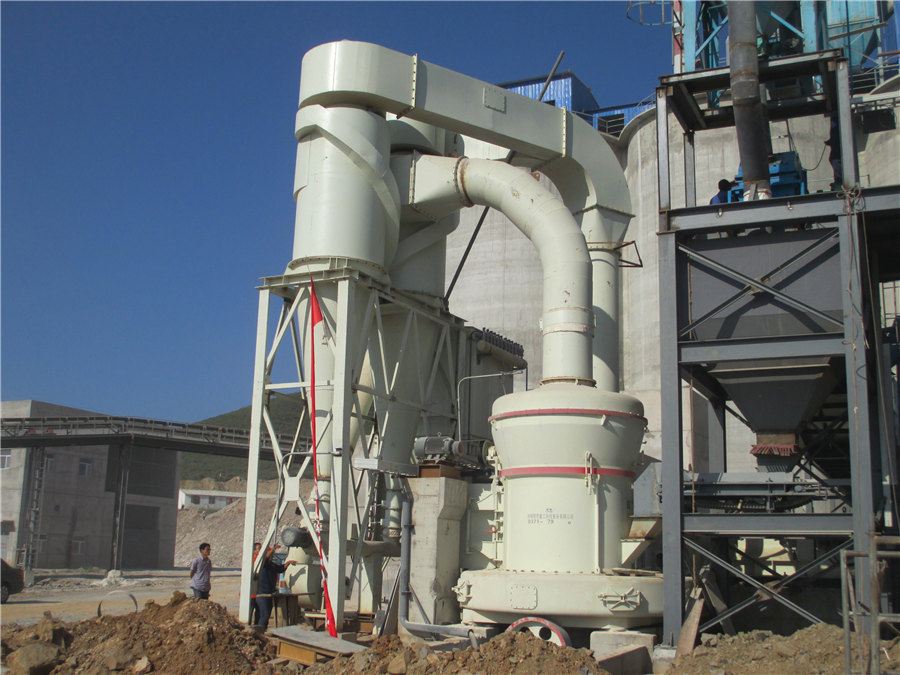
Three rules for the optimum ball mill setup RETSCH
In a dry grinding process, the balls should be at least a factor of 3 larger than the largest particle of the sample material The jar filling situation should follow the 1/3 rule, to protect the grinding 2023年2月15日 A beneficiation plant in Singapore loads balls into a ϕ 1500mm×3000mm wet grid type ball mill, determines the filling rate ϕ = 50%, and selects cast steel grinding balls δ = 45 t/m 3 The ball mill processes the Method of Steel Grinding Ball Proportioning and 2020年10月1日 Note that increasing the mass of product (thus the filling ratio) reduces the stroke of the ball All the samples were first dried in an oven at 65 °C during 24 h A first series of experiments were conducted at 20 Hz for different values of powder mass (6, 13, 17 and 20 g) and a second series were then conducted with a fixed mass (13 g) for Evolution of grinding energy and particle size during dry ball 2022年3月6日 A ball mill is important grinding equipment in a concentrator, and the accurate detection of the load status ensures that the ball mill runs in the best state, which helps optimize the grinding process, ensure the stable operation of the ball mill equipment, and save energy The current mainstream detection methods cannot easily detect the movement inside the ball mill Ball mill load status identification method based on the
.jpg)
(PDF) Effects of Ball Size Distribution and Mill Speed and
2020年7月2日 The effect of ball size distribution increased with increasing mill filling and for the mill filling of 35%, the ball size distribution had the maximum effect on the power draw2017年2月13日 These ball mills are relatively small, bearing mounted on a steel frame All ball mills are sold with motor, gears, steel liners and optional grinding media charge/load Ball Mills or Rod Mills in a complete range of sizes up to 10′ diameter x 20′ long, offer features of operation and convertibility to meet your exact needs They may be Ball Mills 911Metallurgistparameters such as mill speed, ball filling ratio, ball size distribution, powder filling ratio, grinding aid dosage and grinding time were studied The results of grinding tests were evaluated based on the product particle size (d 50, d 80) and surface area (m2/kg) As a Influences of operating parameters on dry ball mill According to the actual results of laboratory, when the filling quantity of steel balls in cylinder is 40%, the output is the highest, while the filling rate of steel balls in production is about 35%, that is to say, keeping the volume of steel balls is lower than that of the horizontal center lineHow to choose the ball loading and loading ratio of ball mill?

ratio of balls size of balls in ball mill Mining Quarry Plant
2013年3月19日 Ball Mill – Free download as PDF File down to the particle size of 20 to 75 microns The bulk volume of balls charge ratio to the volume of mill is known as 2016年7月1日 The importance of this new parameter for ball milling process, filling ratio of vial, was investigated in this study work, dry ZnO nanoparticles are produced, with different FRV values (40% Filling ratio of vial: An important parameter for ball milling2017年8月26日 speed of 300 rpm and balltopowder weight ratio of 10:1 The milling process was performed under argon atmosphere (with purity of 9999 %) by using a Fritsch planetary ball mill using steelmade balls (using various balls diameters of 5, 10, 15, and 20 mm, based on the required balls mass) and vial (150 cm3 capacity) To prevent aFilling ratio of vial SpringerStone loading amount = 314X the square radius of the ball mill X the specific gravity of the ball X the length of the ball mill X25%*1000 Regarding the gradation of the high alumina ceramic ball of the ball mill: Due to the different grinding aids added to How to choose the size, filling amount and ratio of alumina
.jpg)
ball mill calculations, grinding media filling degree, ball size, mill
online live calculators for grinding calculations, Ball mill, tube mill, critical speed, Degree of filling balls, Arm of gravity, mill net and gross power Optimization Online Training2015年6月19日 The basic parameters used in ball mill design (power calculations), rod mill or any tumbling mill sizing are; material to be ground, characteristics, Bond Work Index, bulk density, specific density, desired mill Ball Mill Design/Power Calculation2024年2月19日 The ratio of steel balls in the ball mill depends on the effective length of your mill, whether it has a roller press, the size of the feed particles, the lining and structure used, the expected sieve residue fineness and ratio, how many chromium balls to operate, and the rotation speed How much and other factors make a comprehensive judgmentBall Mill Steel Balls: Quality And Gradation JXSC Mineral2023年5月28日 where L b stands for steel ball load, L w for water load, L m for material load, φ mb for materialball ratio, φ mw for grinding concentration, φ bf for medium filling ratio, φ bmw for filling ratio, ρ b for steel ball density, ρ m for material density, ρ w for water density, μ for void content, generally 038, V mill for the effective volume of the mill, V m for the material volume Mill Load Measurement SpringerLink
.jpg)
RoM BALL MILLS A COMPARISON WITH AG/SAG
2024年7月24日 RoM ball mill is pebble ported most of the steel balls can discharge through the pebble ports and cause logistic problems of separating steel balls from rocks prior to sending the pebbles for 2021年1月1日 Measuring filling is also necessary to estimate the composition of the load for mill modelling: rock and slurry for AG mills; rock, balls and slurry for SAG mills; or balls and slurry for ball mills In the case of SAG mills, this requires two separate filling measurements: one for a crashstop and one following a complete grindout to quantify An improved method for grinding mill filling measurement and 2022年6月30日 In summary, we can draw the following conclusions Grid Type Ball Mill Advantages: The discharge speed is fast, which can reduce the overgrinding of the crushed stone, and at the same time can increase the output per unit volume, which is higher than the overflow type ball mill; Disadvantages: The structure is complex, the grid plate is easy to be OverflowTypeBallMillVSGridTypeBallMill Miningpedia2016年4月1日 The grinding machine was a laboratoryscale ball mill made of stainless steel with the dimensions 200 As increased grinding media filling ratios in ball mills use more energy, Particle filling and size effects on the ball load behaviour and power in a dry pilot mill: experimental study Powder Technol, 187 An experimental study on the ultrafine grinding of gypsum ore in a dry
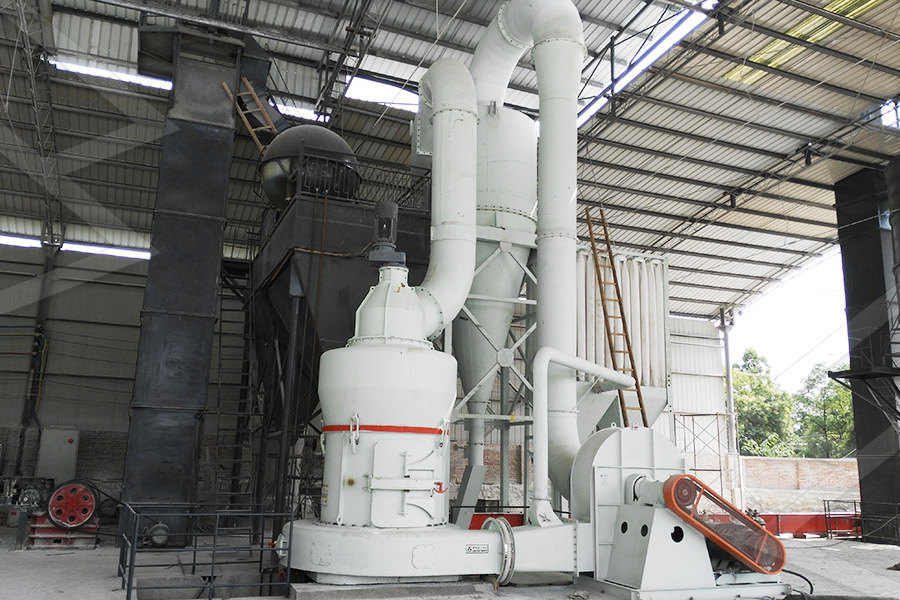
The ball to powder ratio (BPR) dependent morphology and microstructure
2018年11月1日 It increases the milling efficiency of ball milling Tungsten powder and grinding balls were weighed by the precision balance (with the accuracy of 00001 g) respectively to make samples with the BPR (the ratio of milling balls mass to powder mass) of 4:1, 10:1 and 15:1The ball mill is the most widely used equipment in industyr grinding, the grid type ball mill and overflow ball millis used in the mineral processing industry and other industrial sectors Dry type grid type ball mill is mainly used for industrial Ball mill sinoninetechBall Mill Loading (dry milling) When charging a ball mill, ceramic lined mill, pebble mill, jar mill or laboratory jar use on a jar rolling mill it is important to have the correct amount of media and correct amount of product Charging a Dry Mill Ball Mill Loading Dry Milling Paul O Abbe2020年10月9日 The mill speed, fill level ratio, and steel ball ratio can significantly affect mill operation, and our conclusions can provide a reference for an actual situation (also called steel ball Operation Analysis of a SAG Mill under Different
.jpg)
A Review of the Grinding Media in Ball Mills for Mineral
2023年10月27日 The ball mill is a rotating cylindrical vessel with grinding media inside, which is responsible for breaking the ore particles Grinding media play an important role in the comminution of mineral ores in these mills This work reviews the application of balls in mineral processing as a function of the materials used to manufacture them and the mass loss, as 2013年8月3日 In Grinding, selecting (calculate) the correct or optimum ball size that allows for the best and optimum/ideal or target grind size to be achieved by your ball mill is an important thing for a Mineral Processing Engineer AKA Metallurgist to do Often, the ball used in ball mills is oversize “just in case” Well, this safety factor can cost you much in recovery and/or mill liner Calculate and Select Ball Mill Ball Size for Optimum Grinding2015年12月1日 Firstly, the conventional ball mill parameters such as mill speed (% of critical speed), material filling ratio (Jb), ball filling ratio (fc), ball size distribution (10203040 mm, %), grinding An experimental study on the ultrafine grinding of gypsum ore in a dry 2012年6月1日 As the cylinder starts to rotate, the grinding balls inside the cylinder crush and grind the feed material, generating mechanical energy that aids in breaking bonds, activating the catalyst, and (PDF) Grinding in Ball Mills: Modeling and Process Control

AMIT 135: Lesson 7 Ball Mills Circuits
Mill Type Overview Three types of mill design are common The Overflow Discharge mill is best suited for fine grinding to 75 – 106 microns; The Diaphram or Grate Discharge mill keeps coarse particles within the mill for additional grinding and typically used for grinds to 150 – 250 microns; The CenterPeriphery Discharge mill has feed reporting from both ends and the product With 37 years of industry experience, JXSC has built a reputation as a leading ball mill manufacturer among ball mill manufacturers Since 1985, With over 200 successful mining projects in more than 40 countries, JXSC has been providing premium services, from RD and production to installation and free operation training Applying steel balls as grinding media, Ball Mills Manufacturer JXSC2023年2月15日 A beneficiation plant in Singapore loads balls into a ϕ 1500mm×3000mm wet grid type ball mill, determines the filling rate ϕ = 50%, and selects cast steel grinding balls δ = 45 t/m 3 The ball mill processes the Method of Steel Grinding Ball Proportioning and 2020年10月1日 Note that increasing the mass of product (thus the filling ratio) reduces the stroke of the ball All the samples were first dried in an oven at 65 °C during 24 h A first series of experiments were conducted at 20 Hz for different values of powder mass (6, 13, 17 and 20 g) and a second series were then conducted with a fixed mass (13 g) for Evolution of grinding energy and particle size during dry ball
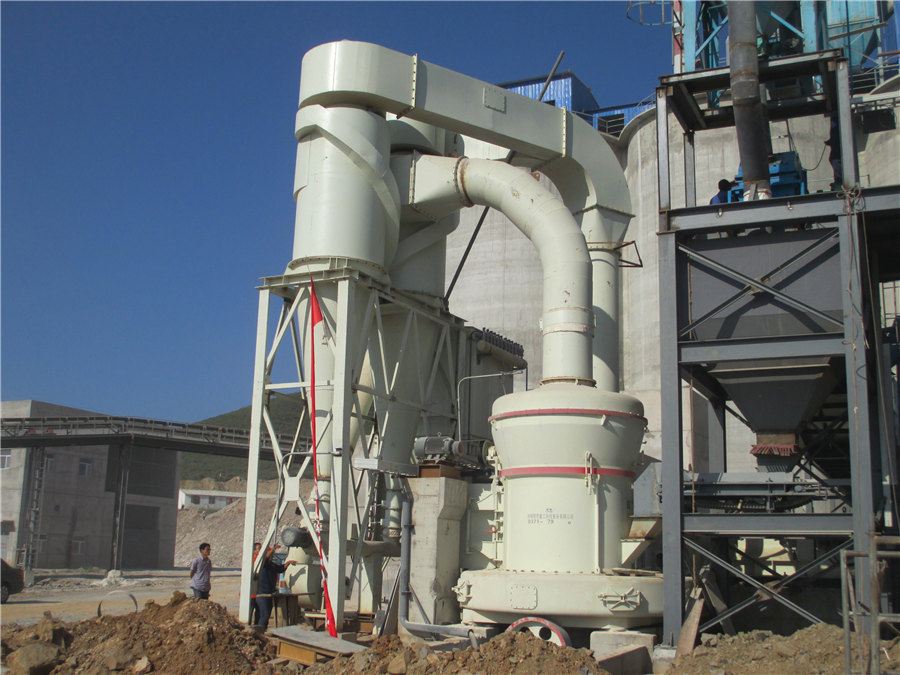
Ball mill load status identification method based on the
2022年3月6日 A ball mill is important grinding equipment in a concentrator, and the accurate detection of the load status ensures that the ball mill runs in the best state, which helps optimize the grinding process, ensure the stable operation of the ball mill equipment, and save energy The current mainstream detection methods cannot easily detect the movement inside the ball mill 2020年7月2日 The effect of ball size distribution increased with increasing mill filling and for the mill filling of 35%, the ball size distribution had the maximum effect on the power draw(PDF) Effects of Ball Size Distribution and Mill Speed and 2017年2月13日 These ball mills are relatively small, bearing mounted on a steel frame All ball mills are sold with motor, gears, steel liners and optional grinding media charge/load Ball Mills or Rod Mills in a complete range of sizes up to 10′ diameter x 20′ long, offer features of operation and convertibility to meet your exact needs They may be Ball Mills 911Metallurgistparameters such as mill speed, ball filling ratio, ball size distribution, powder filling ratio, grinding aid dosage and grinding time were studied The results of grinding tests were evaluated based on the product particle size (d 50, d 80) and surface area (m2/kg) As a Influences of operating parameters on dry ball mill
.jpg)
How to choose the ball loading and loading ratio of ball mill?
According to the actual results of laboratory, when the filling quantity of steel balls in cylinder is 40%, the output is the highest, while the filling rate of steel balls in production is about 35%, that is to say, keeping the volume of steel balls is lower than that of the horizontal center line2013年3月19日 Ball Mill – Free download as PDF File down to the particle size of 20 to 75 microns The bulk volume of balls charge ratio to the volume of mill is known as ratio of balls size of balls in ball mill Mining Quarry Plant2016年7月1日 The importance of this new parameter for ball milling process, filling ratio of vial, was investigated in this study work, dry ZnO nanoparticles are produced, with different FRV values (40% Filling ratio of vial: An important parameter for ball milling2017年8月26日 speed of 300 rpm and balltopowder weight ratio of 10:1 The milling process was performed under argon atmosphere (with purity of 9999 %) by using a Fritsch planetary ball mill using steelmade balls (using various balls diameters of 5, 10, 15, and 20 mm, based on the required balls mass) and vial (150 cm3 capacity) To prevent aFilling ratio of vial Springer