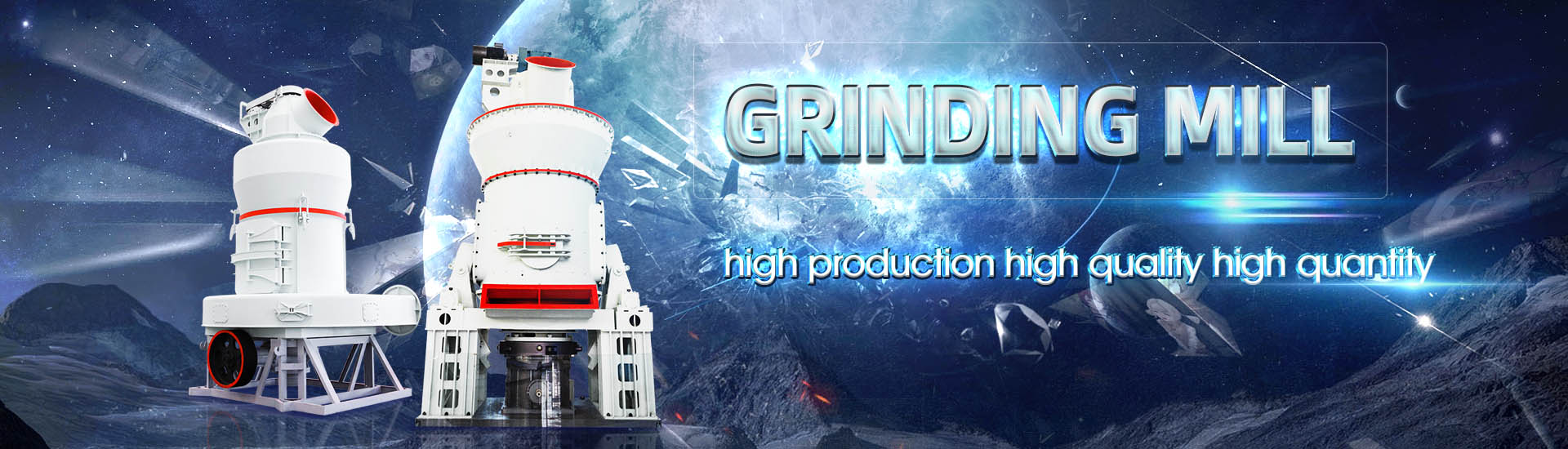
Water atomization iron oxide equipment
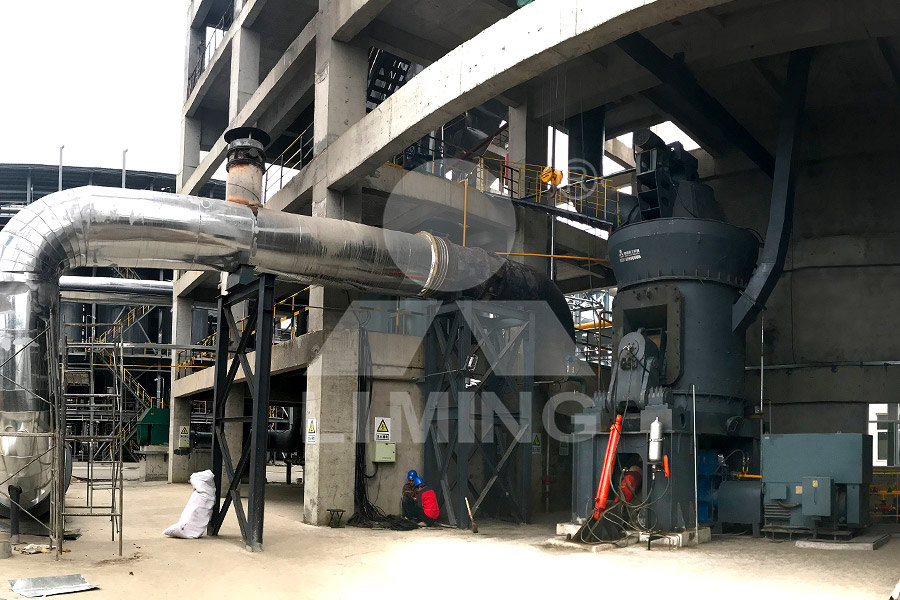
Reduction of surface oxide layers on wateratomized iron
2020年10月1日 Increase in chromium content with layer removal implies involvement in reduction The reduction of surface oxide layers covering commercial wateratomized iron and 2017年3月1日 This capability removes the assumed limitations of water atomised powder, in the context of AM, and reduces the differences between water and gas atomised powder to chemical composition differences, Additive Manufacturing: Opportunities for water 2022年1月1日 This study will consider the cooling, solidification and collision of droplets during water atomisation of molten ironcarbon alloys and investigate the feasibility that collisions Particle morphology of water atomised iron‑carbon powders2014年12月1日 This review discusses the water atomization process in general terms and then discusses the use of the technique to produce powders based on iron, low alloy steels, Oxidation of Water Atomized Metal Powders Request PDF
.jpg)
Oxide reduction and oxygen removal in wateratomized iron
2020年5月9日 In this study, the oxide reduction and oxygen removal in wateratomized iron powder was investigated by means of thermogravimetric analysis in pure hydrogen Two 2014年4月9日 This study focuses on the oxidation of water atomized metal powders Pilot plant experiments were performed using liquid iron alloyed with manganese and carbon The Oxidation of Water Atomized Metal Powders Persson1999年4月1日 A water atomisation experiment was performed to investigate if variations of these elements could affect quality Effects of water pressure, melt superheat, and sulphur New insights into influencing variables of water atomisation of iron2021年10月4日 The meltatomization method that uses water is the most economically feasible method [1], which is widely used to obtain powders of iron and lowalloy steel with a branched OXIDATION PROCESS OF HIGHALLOY STEEL POWDERS
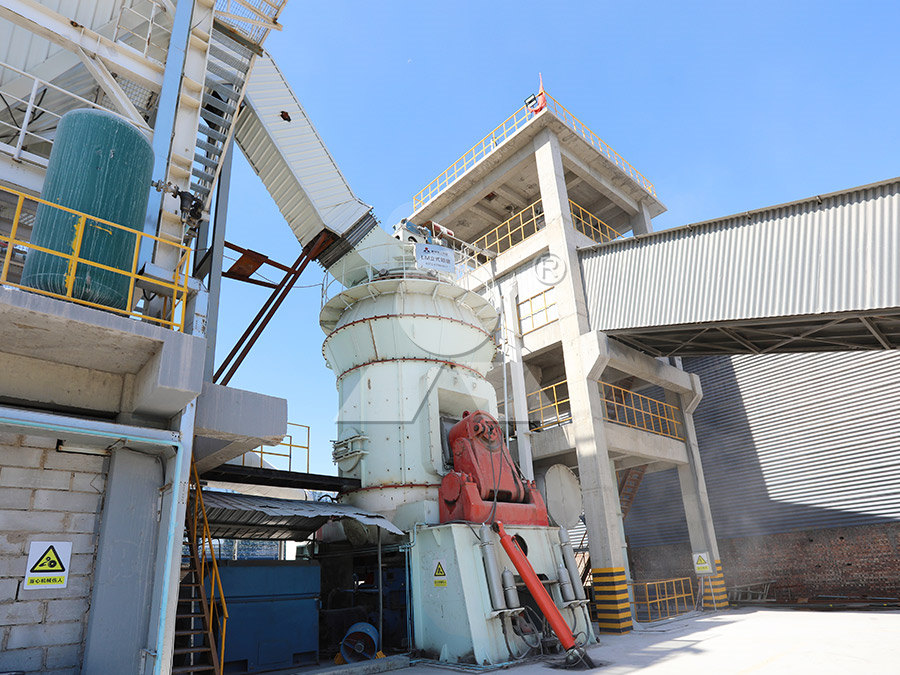
the water atomizing process 1 Total Materia
Highpressure water atomization has proven to be a viable, lowcost process to achieve fine particle size distributions for iron, stainless and lowalloy metal powders The economic advantages and prealloying capability provide 2020年6月1日 The results showed that the surface oxides consisted of a thin (~4 nm) iron oxide (Fe2O3) layer with particulate oxide phases rich in Cr, Mn, and Si, with a varying composition(PDF) Effect of atomization on surface oxide 2024年11月10日 The most widely used are gas atomization Equipment and water atomization Equipment In the process of atomization powder producing process, melt the metal raw materials into qualified alloy liquid (generally Metal powder water atomization equipmentASL offers a wide range of atomisation technologies such as Water Atomisation, Gas Atomisation, Centrifugal Atomisation Oil Atomisation We have the expertise and experience to help you optimise your equipment Centrifugal Atomising Equipment Technologies
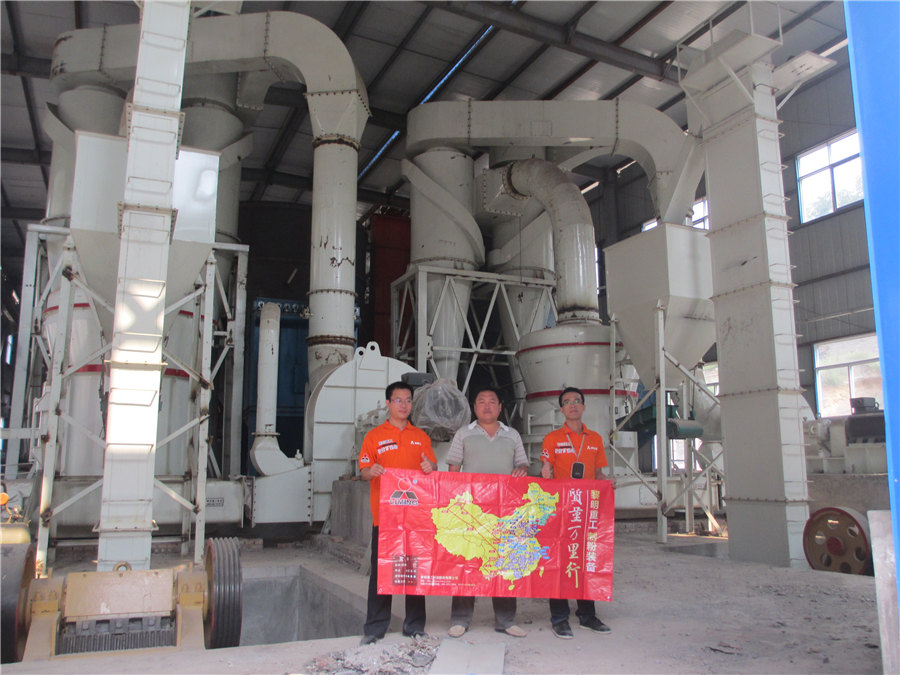
Atomisation an overview ScienceDirect Topics
Advances in atomisation techniques for the formation of metal powders JJ Dunkley, in Advances in Powder Metallurgy, 2013 111 Atomisation This may be defined as breaking liquid into droplets Items like fire sprinklers, crop sprayers, aerosols and so on utilise atomisation methods for cold liquids There is a very extensive literature on this surveyed in Yule and Dunkley 2 and 2021年2月3日 Iron and steel are increasingly being used worldwide in various traditional and modern applications with the vast majority of production among all metallic materials, reaching an annual global demand of around 3 billion tons by 2050 1,2 Currently, the blast furnaces that employ carbonaceous reductants are widely used to reduce iron oxides, causing a global WaterAssisted Green Production of Steel Powder in Molten 2022年1月1日 Three melts were produced for this study from highpurity iron and briquettes containing iron and graphite by atomisation in a typical water atomiser (Fig 1)Each melt was an ironcarbon alloy with small amounts of other elements (Table 1)The contents of carbon, oxygen, nitrogen and sulfur were measured using a LECO analysis in accordance with standards ISO Particle morphology of water atomised iron‑carbon powders2022年7月1日 The meltatomization method that uses water is the most economically feasible method [], which is widely used to obtain powders of iron and lowalloy steel with a branched particle shape and oxygen content after recovery annealing at the level of several tenths of percentThis content is quite acceptable for their use in traditional powder metallurgyOxidation Process of HighAlloy Steel Powders During Melt Atomization
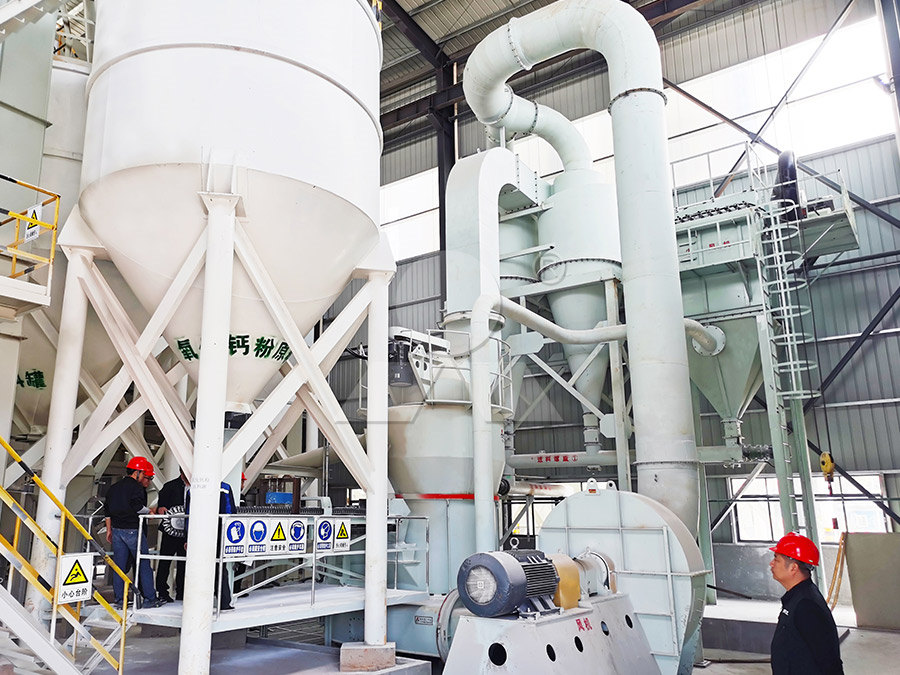
Reduction of surface oxide layers on wateratomized iron
2020年10月1日 Metal powder particles are covered by thin oxide layers as a result of their exposure to air or oxygencontaining atmospheres These surface layers account for up to 30–50 % of the total oxygen in typical commercial wateratomized ferrous powder grades used in the powder metallurgy (PM) industry [1], with layer thicknesses commonly reported to be in the 2023年10月10日 Water atomization is the simplest and most cost effective especially for coarser powders above 100 microns Vacuum systems allow superior control over powder characteristics but are far more expensive The optimum atomization method depends on the metal alloy being processed, production volumes, final application requirements, and budget The Atomizing Metal Powder Industry Additive Time, Cost, and Equipment The analysis time when using flame atomization is short, with sample throughputs of 250–350 determinations per hour when using a fully automated system Electrothermal atomization requires substantially more time per analysis, with maximum sample throughputs of 20–30 determinations per hour43B: Atomic Absorption Spectroscopy (AAS) Chemistry 2023年8月28日 The demand for soft magnetic amorphous metal powders with high saturation magnetization values and low energy loss has increased to achieve highperformance inductors for mobile electronic devices In this study, Febased Fe923Si35B30C07P05 (wt%) amorphous metal powders were prepared using different atomization methods for controlling Effects of Surface Oxidation on the Magnetic Properties of
.jpg)
Characterization of Fine Metal Powders Produced by Hybrid by Water
2017年11月14日 Many new atomization techniques have been developed in recent years, such as ultrasonic capillary wave atomization , rotating disk atomization, swirl water jet atomization and hybrid centrifugal hydraulic atomization (CHA) with gas atomization , super highpressure water atomization [5, 6] Water atomization is the most common way for metal 2012年8月30日 Water atomization is one of the prominent methods used in production of powders for conventional PM application Oxygen content of the powders produced by water atomization plays an important role in determining it’s as sintered properties In this work, oxide formation during various stages of water atomization and annealing wereSTUDY OF TOTAL OXYGEN CONTENT AND OXIDE 2021年5月18日 Iron (III) oxide is a compound that appears in at least four different polymorphs: αFe 2 O 3, βFe 2 O 3, γFe 2 O 3, and εFe 2 O 3However, Fe 3+ ions are also present in another form of iron oxide: Fe 3 O 4, which is an iron crystal structure with both Fe 2+ and Fe 3+ ions And in its turn, Fe 2+ ions are also present in the FeO form of iron oxide Each of these Synthesis, Properties, and Applications of Iron OxidesThe wateratomizing process, as practiced there, can be followed on the flowsheet shown in Figure 2, and is described in detail on the next page Figure 2: Flowsheet for the Höganäs WaterAtomizing Process The raw material for this process is a carefully selected iron scrap and sponge iron from the process described in the preceding paragraphthe water atomizing process 2 Total Materia
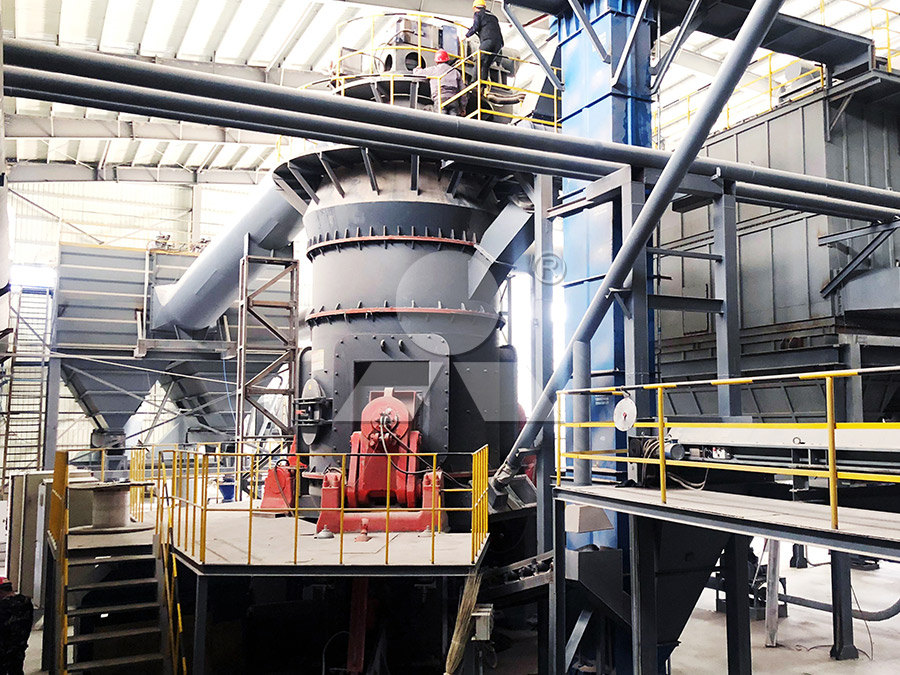
OXIDATION PROCESS OF HIGHALLOY STEEL POWDERS
2021年10月4日 Hoeganas [2] and Ametek SMP) using melt atomization with water Meanwhile, the oxygen content in the powder after atomization is at the level of 02‒03%, which enables their application to mass production of sintered products In addition, evidence is available that proves that the method of melt atomization with water al2020年6月30日 From the powder metallurgical field, it is known that wateratomized prealloyed iron powders with strong oxide forming elements like, Cr and Mn form, besides the dominant Ferich thin oxide film, minor amounts of oxide particles 13 If not reduced, these more stable oxsides remain within the consolidated sample 46 Similar correlations have Effect of atomization on surface oxide composition in 316L 2024年4月25日 a highpressure water or gas atomization method On the other hand, an amorphous alloy powder with a high Fe content of 93 wt% or more could not be manufactured by a highpressure water or gag atomization method because of its low amorphous formation ability Furthermore, the highpressure water atomization method is unsuitable forEffects of Surface Oxidation on the Magnetic Properties 2022年8月4日 iron ore and even after the reduction process can still contain significant levels of unreduced iron oxide and impurities such as SiO 2 and V 2 O 5 Most iron powders that are produced by atomization utilize water as the atomizing medium In addition, due to the oxidation of the molten iron, the powders are generally annealed in hydrogen PROPERTIES AND APPLICATIONS FOR IRON POWDER
.jpg)
Characterization of oxide on the wateratomized FeMn
2014年3月15日 The low compressibility of the unreduced wateratomized Fe031Mn powder may due to the high oxygen content and the quenching effect of water atomization Hard phase of iron and manganese oxides formed in the process of water atomization lead to high hardness and poor pressing performance of the unreduced powder [34], [35] So the subsequent 2021年3月15日 Fe 735 Si 13 B 11 Cr 1 C 15 soft magnetic powder with amorphous microstructure is produced by gaswater combined atomization The cooling rate of gaswater combined atomization is close to water atomization, but higher than gas atomization • The magnetic powder cores made of gaswater combined atomized powder have the high DC FeSiBCrC amorphous magnetic powder fabricated by gaswater 2012年8月30日 Water atomization is one of the prominent methods used in production of powders for conventional PM application Oxygen content of the powders produced by water atomization plays an important role in determining it’s as sintered properties In this work, oxide formation during various stages of water atomization and annealing wereSTUDY OF TOTAL OXYGEN CONTENT AND OXIDE 2012年8月30日 Water atomization is one of the prominent methods used in production of powders for conventional PM application Oxygen content of the powders produced by water atomization plays an important role in determining it’s as sintered properties In this work, oxide formation during various stages of water atomization and annealing wereSTUDY OF TOTAL OXYGEN CONTENT AND OXIDE
.jpg)
Economic Additive Manufacturing using Water Atomized
2018年9月24日 size required for its particular use, the yield from the atomization process will be sorted to a final particle size [4][9] Water atomization When analyzing the production path of water atomized powder, it is very important to begin with the raw materials Firstly, the melting procedure of stainless steel meant to be water atomized is quite2021年8月27日 Milling equipment: The equipments are generally classified as crushers mills Crushing => for making ceramic materials such as oxides of metals; Grinding => for reactive metals such as titanium, zirconium, niobium, tantalum Types: water atomization, gas atomization, soluble gas or vacuum atomization,Powder metallurgy – basics applications IIT Guwahati1999年4月1日 Trace amounts of surfactants have an acute influence on measured surface tension of melts and may influence viscosity A water atomisation experiment was performed to investigate if variations of these elements could affect quality Effects of water pressure, melt superheat, and sulphur content, iron scrap oxygen content, and aluminium content were New insights into influencing variables of water atomisation of iron2013年3月1日 Characterization of oxide products on the surface of wateratomized steel powder is essential in order to determine the reducing conditions required for their removal during the sintering stage Characterization of Surface Oxides on WaterAtomized
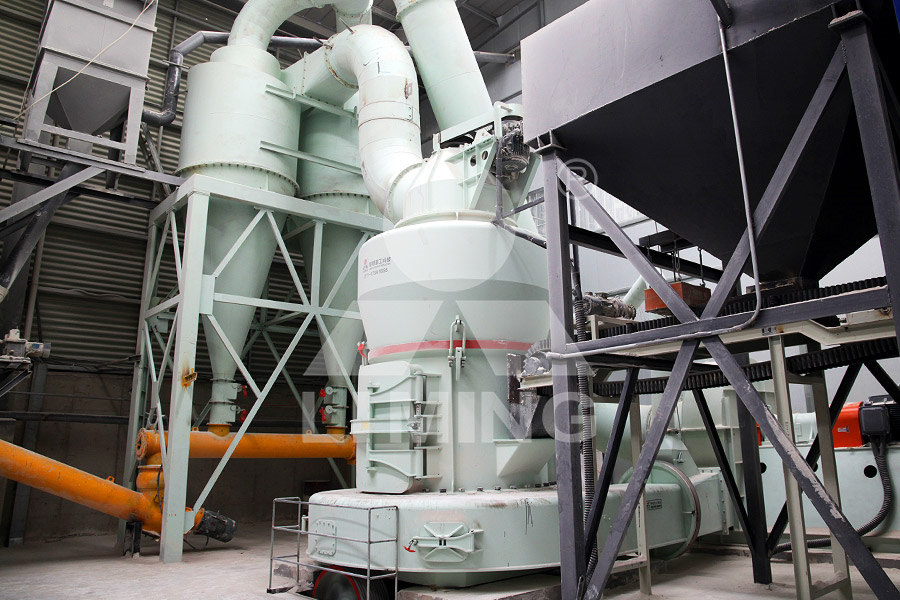
Roles of Iron Metal Powders in SemiMetallic Friction
2018年6月14日 Wateratomization of molten iron or alloy is a primary mechanical manufacturing method today, while chemical reduction of iron oxides is the least expensive, largescale chemical manufacturing method compared to other chemical methods However, the atomization and reduction methods create iron powders with completely different particle morphology2023年1月28日 Graphene oxide/Iron III oxide (GO: Fe2O3) nanocomposites (NCs) have been topical in recent times owing to the enhanced properties they exhibit GO acting as a graphene derivative has demonstrated superior features as obtainable in a graphene sheet Furthermore, the attachment of oxygen functional groups at its basal and edge planes of graphene has Graphene oxide: Fe2O3 nanocomposite: synthesis, "Water Atomization Process" refers to a process that sprays and collides water at a high pressure of about 50150 MPa against a molten metal melted at a high temperature to produce fine metal powder (atomized powder) at the micron level Water Atomization Equipment STAR BURST: Wet Pulverization and Dispersion Device BiNFis: Cellulose Water Atomization Equipment SUGINO MACHINE2020年6月1日 The results showed that the surface oxides consisted of a thin (~4 nm) iron oxide (Fe2O3) layer with particulate oxide phases rich in Cr, Mn, and Si, with a varying composition(PDF) Effect of atomization on surface oxide
.jpg)
Metal powder water atomization equipment
2024年11月10日 The most widely used are gas atomization Equipment and water atomization Equipment In the process of atomization powder producing process, melt the metal raw materials into qualified alloy liquid (generally ASL offers a wide range of atomisation technologies such as Water Atomisation, Gas Atomisation, Centrifugal Atomisation Oil Atomisation We have the expertise and experience to help you optimise your equipment Centrifugal Atomising Equipment TechnologiesAdvances in atomisation techniques for the formation of metal powders JJ Dunkley, in Advances in Powder Metallurgy, 2013 111 Atomisation This may be defined as breaking liquid into droplets Items like fire sprinklers, crop sprayers, aerosols and so on utilise atomisation methods for cold liquids There is a very extensive literature on this surveyed in Yule and Dunkley 2 and Atomisation an overview ScienceDirect Topics2021年2月3日 Iron and steel are increasingly being used worldwide in various traditional and modern applications with the vast majority of production among all metallic materials, reaching an annual global demand of around 3 billion tons by 2050 1,2 Currently, the blast furnaces that employ carbonaceous reductants are widely used to reduce iron oxides, causing a global WaterAssisted Green Production of Steel Powder in Molten
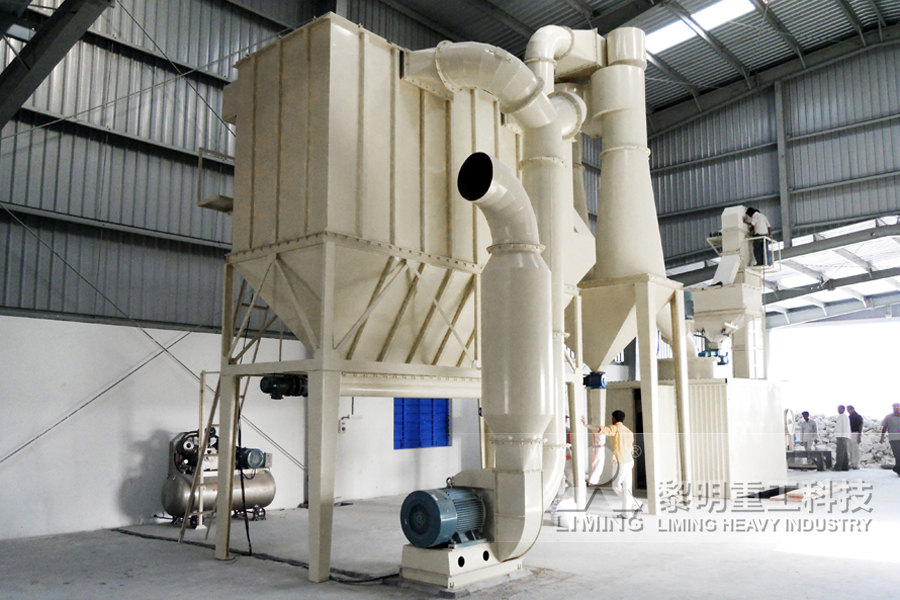
Particle morphology of water atomised iron‑carbon powders
2022年1月1日 Three melts were produced for this study from highpurity iron and briquettes containing iron and graphite by atomisation in a typical water atomiser (Fig 1)Each melt was an ironcarbon alloy with small amounts of other elements (Table 1)The contents of carbon, oxygen, nitrogen and sulfur were measured using a LECO analysis in accordance with standards ISO 2022年7月1日 The meltatomization method that uses water is the most economically feasible method [], which is widely used to obtain powders of iron and lowalloy steel with a branched particle shape and oxygen content after recovery annealing at the level of several tenths of percentThis content is quite acceptable for their use in traditional powder metallurgyOxidation Process of HighAlloy Steel Powders During Melt Atomization 2020年10月1日 Metal powder particles are covered by thin oxide layers as a result of their exposure to air or oxygencontaining atmospheres These surface layers account for up to 30–50 % of the total oxygen in typical commercial wateratomized ferrous powder grades used in the powder metallurgy (PM) industry [1], with layer thicknesses commonly reported to be in the Reduction of surface oxide layers on wateratomized iron 2023年10月10日 Water atomization is the simplest and most cost effective especially for coarser powders above 100 microns Vacuum systems allow superior control over powder characteristics but are far more expensive The optimum atomization method depends on the metal alloy being processed, production volumes, final application requirements, and budget The Atomizing Metal Powder Industry Additive
.jpg)
43B: Atomic Absorption Spectroscopy (AAS) Chemistry
Time, Cost, and Equipment The analysis time when using flame atomization is short, with sample throughputs of 250–350 determinations per hour when using a fully automated system Electrothermal atomization requires substantially more time per analysis, with maximum sample throughputs of 20–30 determinations per hour