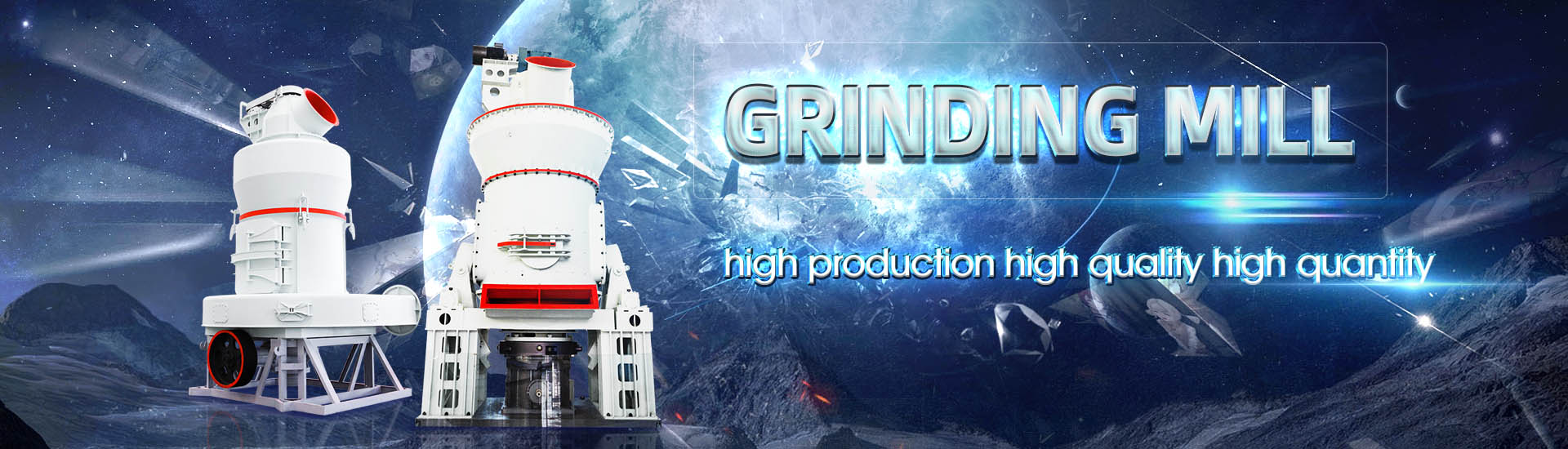
Which ore mills have a higher output
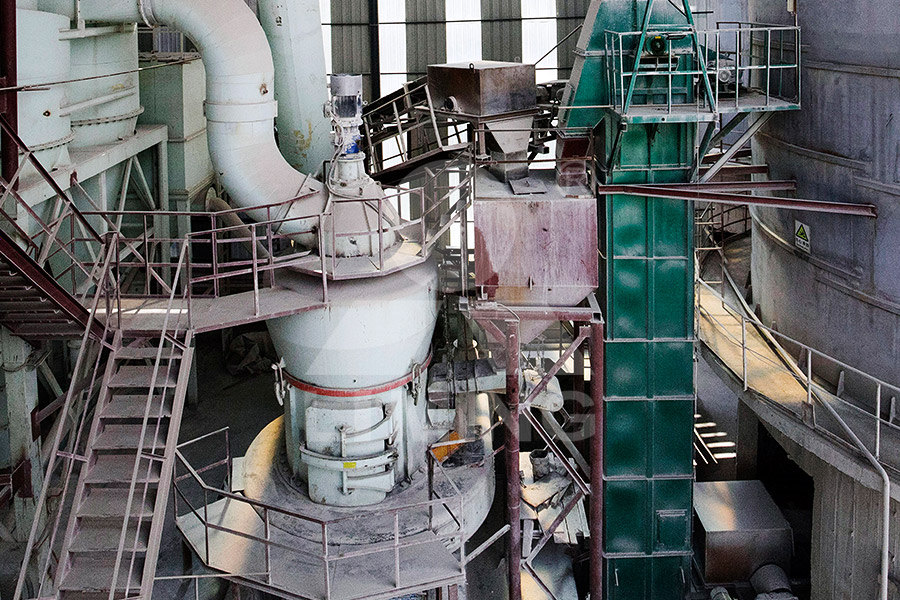
ReviewStirred media mills in the mining industry: Material
2020年6月1日 Stirred media mills are used by the mining industry for ultrafine grinding to enhance liberation, and to decrease particle sizes of industrial minerals to tailor functional properties2024年9月22日 Highcapacity ball mills offer several advantages over traditional mills in terms of production capabilities, efficiency, and costeffectiveness: a Increased Throughput: High Maximizing output: The role of highcapacity ball mills in 2017年9月1日 In platinum group mineral (PGM) ore processing, stirred mills are used for both mainstream grinding applications at high throughputs, and concentrate regrind applications at Fine grinding: How mill type affects particle shape characteristics 2024年9月1日 In summary, compared to fine grinding products of the ball and vertical stirred mills, the fine grinding products of the horizontal stirred mill have a higher fine particle Effect of different mills on the fine grinding characteristics
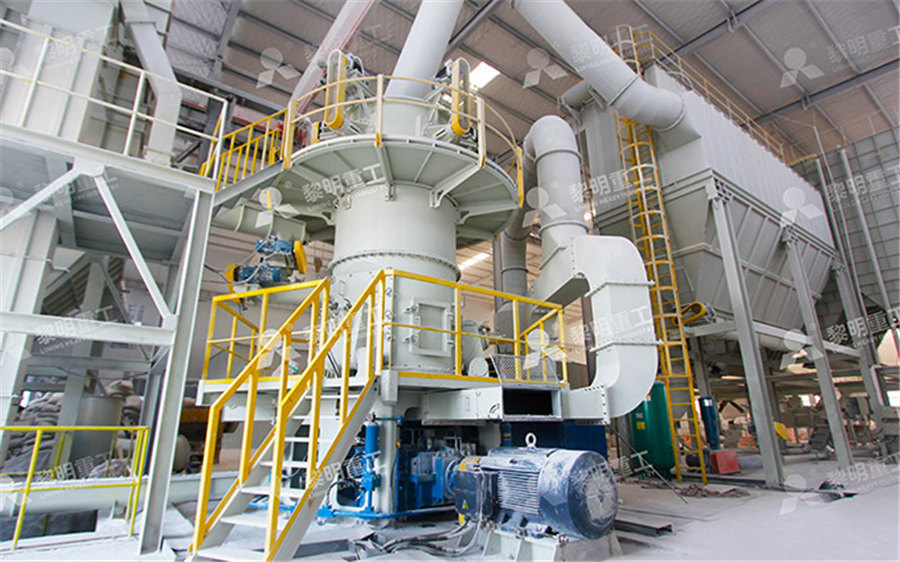
Stirred media mills in the mining industry: Material
2020年5月1日 Stirred media mills are used by the mining industry for ultrafine grinding to enhance liberation, and to decrease particle sizes of industrial minerals to tailor functional First, the output of comminution devices generally consists of polymineralic, not monomineralic, ore particles Consequently, sorting devices do not act on pure mineral properties, but on All About Particles: Modelling Ore Behaviour in Mineral In general, for highaspect mills, higher ratios of D:L permit operation at higher mill speeds for a given rated power output Lower ratios of D:L have been frequently rated at 72% CS to 74% Mill drives: the desire for increased power and the2024年5月29日 operation increased throughput by almost 15% for a particular hard ore type and 6% across all ore types, while the SAG specific energy was reduced by over 9% The major Complete Optimisation from MinetoMill to Maximise
.jpg)
Complete Optimisation from MinetoMill to Maximise Profitability
2024年11月27日 As high grade deposits are depleted, new ore bodies are expected to be of lower grade and more difficult to extract Furthermore, the industry is facing increasing cost 2016年6月6日 Ball Charge Motion inside a SAG Mill With a higher density mill charge SAG mills have a higher installed power density for a given plant footprint relative to AC mills With the combination of finer grind and a lower installed SAG Mill Grinding Circuit Design 911Metallurgist2024年5月29日 certain hard ore types while also reducing the specific energy consumption (Valery et al, 2012) Figure 1 MinetoMill Improvements at Cerro Corona (after Diaz et al 2015) 145 150 155 160 165 Complete Optimisation from MinetoMill to Maximise SAG mills typically have a higher power consumption than AG mills due to their larger diameter and longer length The power consumption of SAG mills is also influenced by the ore hardness, feed size, and mill speed AG Mill Power Consumption AG mills generally have a lower power consumption than SAG mills, as they have a smaller diameter and SAG vs AG Mills: Understanding the Key Differences ball mills
.jpg)
Stirred media mills in the mining industry: Material
2020年5月1日 Vertical stirred mills have become increasingly popular in size reduction operations in the fine and ultrafine range, being normally used in industry in continuous operation2021年5月11日 The price of iron ore leapt for a third consecutive trading day it has surged more than 20 per cent in the last week as Chinese steel mills continue to crank out as much steel as they canIron ore reaches $US230 a tonne, China’s steel mills output 2022年6月17日 Semiautogenous (SAG) mills are widely used grinding equipment, but some ore with critical particle sizes cannot be effectively processed by SAG mills and turned into pebbles This research aims to analyze and compare the properties of raw ore and pebbles from a zinc and tinbearing ore The results show that the contents of sphalerite, cassiterite, biotite, Differences in Properties between Pebbles and Raw Ore from a SAG Mill 2024年4月26日 The beneficiation process aims to increase the iron content and reduce impurities in the ore, resulting in a higherquality concentrate suitable for further processing and utilization The specific beneficiation method employed depends on factors such as the mineralogy of the ore, the presence of specific impurities, and the desired iron contentIron Ore Processing: From Extraction to Manufacturing
.jpg)
Unlocking the Secrets of Gold Ore Mill: A Comprehensive
The choice of grinding circuit configuration is critical for optimizing gold recovery Common configurations include singlestage AG/SAG mills followed by ball mills or twostage AG/SAG mills followed by a ball mill circuit The selection depends on factors such as hardness of the ore, desired grind size, and energy requirements 32019年4月16日 Vertical roller mills (VRM) have been used extensively for comminuting both cement raw materials and minerals like limestone, clinker, phosphate, manganese, magnesite, feldspar and titanium(PDF) LEARNING FROM OTHER INDUSTRIES; WHY THE VRM In addition, very high throughput rates up to 40 000 t/d can be achieved with largesized mills (Fig 6) Moreover, these mills can be designed for both wet and dry grinding Up to now, SAG mills with diameters up to 128 m have been designed for copper ore, at which the mills have reached the limits of their capacityTrends in der Minenindustrie Mineral Processing2022年8月29日 pinion is set on an output shaft of the gearbox The nominal mill efficiency, at optimum speed, is 80 Mg/h The dimensions and the high mass of the rotating elements cause the drive system to be overloaded when the mill filled with copper ore is started For this reason, the mill is stopped only in the case of a failure or planned maintenance Energy Efficiency Analysis of Copper Ore Ball Mill Drive
.jpg)
Monitoring ore loss and dilution for minetomill
The study revealed that fragmentation, underground accumulation of ore, and dilution have a significant influence on the mine call factor and mine output It was difficult to quantify the total ore loss due to the time lag between mining and 2021年7月5日 Most steel mills in Tangshan have resumed production at 70percent capacity, which they plan to maintain until the end of the year, according to a report by industry portal mysteel, citing its Major steel mills in N China resume operations 2024年9月26日 The present article focuses on incorporating mill scale, a steel plant solid waste, into the iron ore pelletization process The characterization results indicated that the mill scale contained about 71% of Fe and predominantly consists of magnetite and wustite mineral phases A detailed pelletization study is conducted using the mill scale at different proportions (0%, Evaluation of Quality Parameters and Mineralogy of Iron Ore 2024年9月22日 Highcapacity ball mills offer several advantages over traditional mills in terms of production capabilities, efficiency, and costeffectiveness: a Increased Throughput: Highcapacity ball mills have a larger feed size and a higher grinding drum rotation speed, allowing for a greater amount of material to be processed per unit of time This Maximizing output: The role of highcapacity ball mills in
.jpg)
(PDF) A Method of Ore Blending Based on the Quality of
2021年5月31日 the ore natures, it can be divided into ore’s physical pr operties, ore’s chemical properties, and quantity of ore The first method is adopted in this researchStudy with Quizlet and memorize flashcards containing terms like Which of the following is most likely to be an implicit cost of production? a property taxes on a building owned by the firm b transportation costs paid to a trucking supplier c rental payments for a building utilized by the company and rented from another party d interest income foregone on funds invested in the econ final 2 Flashcards Quizlet2023年10月25日 Iron ore is a crucial raw material for the global steel industry, and its supply chain is a complex network that involves multiple stakeholders and activities The iron ore supply chain begins with the mining of iron ore, which is then transported to processing plants for beneficiation and further refinement The refined iron ore is then transported to steel mills for Iron Ore Supply Chain: From Mining to Steel Production2024年8月14日 In modern mining production, ball mill is a kind of key grinding equipment, and their performance directly affects the efficiency and output of ore processing Improving the output of ball mills can not only improve the economic benefits of mining companies, but also optimize production processes and reduce resource waste To this end, it is particularly important to How to Improve Ball Mill Output? Xinhai
.jpg)
China's strong iron ore imports diverge from weak steel output
2024年4月22日 LAUNCESTON, Australia, April 22 (Reuters) China's first quarter imports of iron ore and its domestic production of the steel raw material both rose strongly, but output of crude steel fell2018年7月11日 Before 2000, China ’ s iron ore output has been stable at an annual of less than 200 In terms of quantity, the output of domestic ore is much higher China ’ s steel mills have paid (PDF) The Chinese Iron Ore Deposits and Ore Production2022年7月26日 • mill scale (small flakes of iron oxide from the rolling mills); and • flue dust and precipitator dust (fine ore bearing particles) collected from the blast furnace and BOS furnace exhaust gases This moistened mixture is coarsened by a granulation process and is then spread as a layer up toThe Making of Iron Steel SEAISI2018年8月17日 The Kirunavaara ore, Leveäniemi ore and the Mertainen ore have been the considered for ore blending purposes and as a preliminary assessment to the f easibility of blending these ores, anThe effects of ore blending on comminution behaviour and
.jpg)
The Chinese Iron Ore Deposits and Ore Production
2018年7月11日 In terms of quantity, the output of domestic ore is much higher than that of imports Although the growth of China’s ownproduced iron ore is rapid, it has been found in actual research that the actual growth of China’s domestic iron ore production is much lower than the statistic data China’s steel mills have paid a huge price for 2017年7月26日 The rod mill was needed to reduce feed size to the ball mill because crushing plant output was normally coarser than 80% passing 10,000 microns Such feed causes power inefficiency if fed directly to a ball millHow Ball Mill Ore Feed Size Affects Tonnage Capacity2017年9月1日 The first stirred mill was installed in the platinum industry in 2002, and by the year 2010, forty stirred mills had been installed at various platinum operations in South Africa, and these led to a step change in flotation recoveries (Rule, 2011, Rule, 2010)Over the last decade, approximately 200 Automated Scanning Electron Microscopy (AutoSEMEDS) systems have Fine grinding: How mill type affects particle shape characteristics 2023年12月28日 For ball mills of the exact specifications, the output of the closedcircuit process is 15 to 20% higher than that of the opencircuit process During closedcircuit operation, choosing the appropriate powder selection efficiency and cycle Factors Affect The Output and Quality of Ball Mills And How
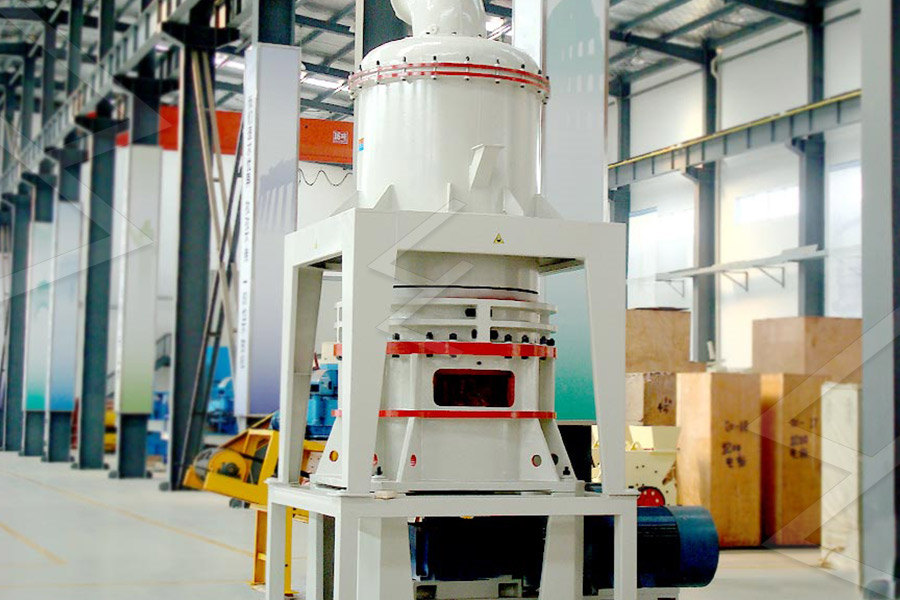
Comparison of SAG mill feed size throughputs
January 2007, two complete grinding circuit surveys were performed followed by a SAG mill crash stop and grindout After stopping the mill, a SAG mill feed sample was also collected from Conveyor 1higher reduction ratios Profiled 102 5 × 100 Compression 3–12 Comminution of soft to intermediate materials; profiles allow high reduction ratios Tumbling Mill Rod Mill 5 × 101 10−1 Shear Compression 20 Coarse milling down to 03–05 mm Autogenous Mill 102 (100)* 10−2 Shear Compression up to 100 Coarser particles act as grinding All About Particles: Modelling Ore Behaviour in Mineral 2016年6月6日 Ball Charge Motion inside a SAG Mill With a higher density mill charge SAG mills have a higher installed power density for a given plant footprint relative to AC mills With the combination of finer grind and a lower installed SAG Mill Grinding Circuit Design 911Metallurgist2024年5月29日 certain hard ore types while also reducing the specific energy consumption (Valery et al, 2012) Figure 1 MinetoMill Improvements at Cerro Corona (after Diaz et al 2015) 145 150 155 160 165 Complete Optimisation from MinetoMill to Maximise
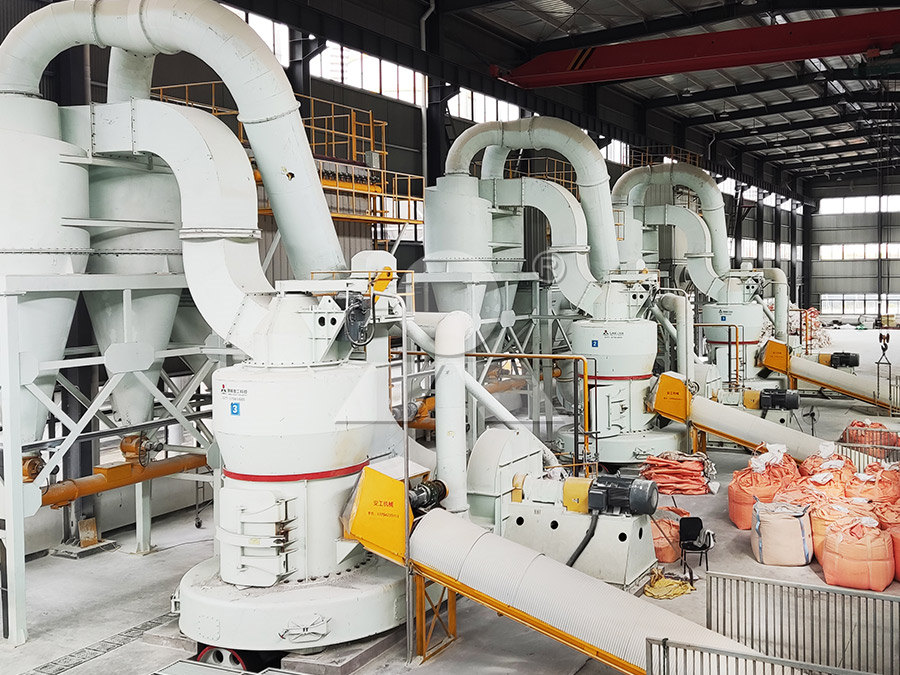
SAG vs AG Mills: Understanding the Key Differences ball mills
SAG mills typically have a higher power consumption than AG mills due to their larger diameter and longer length The power consumption of SAG mills is also influenced by the ore hardness, feed size, and mill speed AG Mill Power Consumption AG mills generally have a lower power consumption than SAG mills, as they have a smaller diameter and 2020年5月1日 Vertical stirred mills have become increasingly popular in size reduction operations in the fine and ultrafine range, being normally used in industry in continuous operationStirred media mills in the mining industry: Material 2021年5月11日 The price of iron ore leapt for a third consecutive trading day it has surged more than 20 per cent in the last week as Chinese steel mills continue to crank out as much steel as they canIron ore reaches $US230 a tonne, China’s steel mills output 2022年6月17日 Semiautogenous (SAG) mills are widely used grinding equipment, but some ore with critical particle sizes cannot be effectively processed by SAG mills and turned into pebbles This research aims to analyze and compare the properties of raw ore and pebbles from a zinc and tinbearing ore The results show that the contents of sphalerite, cassiterite, biotite, Differences in Properties between Pebbles and Raw Ore from a SAG Mill
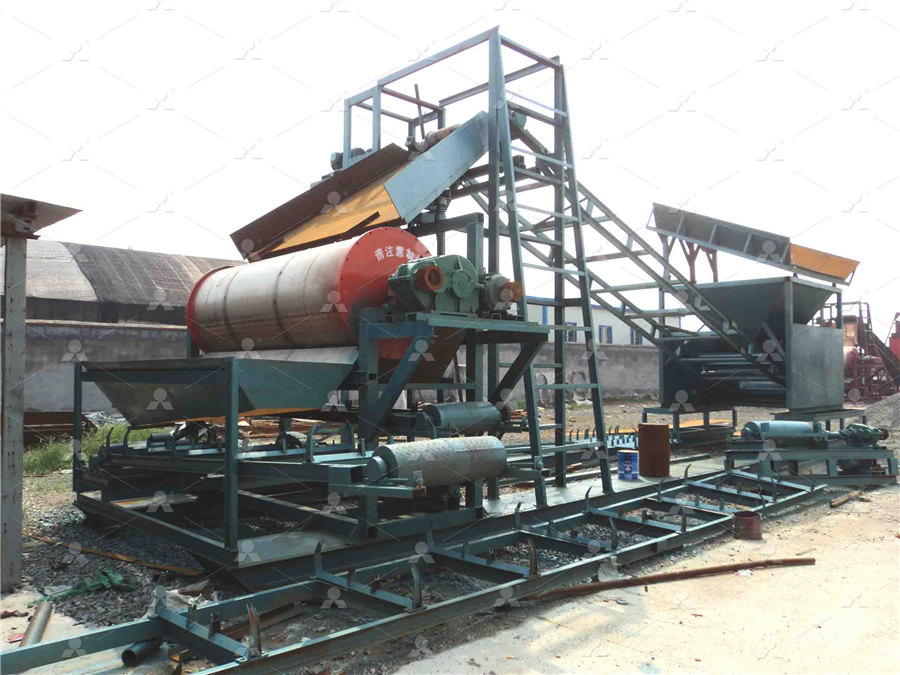
Iron Ore Processing: From Extraction to Manufacturing
2024年4月26日 The beneficiation process aims to increase the iron content and reduce impurities in the ore, resulting in a higherquality concentrate suitable for further processing and utilization The specific beneficiation method employed depends on factors such as the mineralogy of the ore, the presence of specific impurities, and the desired iron contentThe choice of grinding circuit configuration is critical for optimizing gold recovery Common configurations include singlestage AG/SAG mills followed by ball mills or twostage AG/SAG mills followed by a ball mill circuit The selection depends on factors such as hardness of the ore, desired grind size, and energy requirements 3Unlocking the Secrets of Gold Ore Mill: A Comprehensive 2019年4月16日 Vertical roller mills (VRM) have been used extensively for comminuting both cement raw materials and minerals like limestone, clinker, phosphate, manganese, magnesite, feldspar and titanium(PDF) LEARNING FROM OTHER INDUSTRIES; WHY THE VRM In addition, very high throughput rates up to 40 000 t/d can be achieved with largesized mills (Fig 6) Moreover, these mills can be designed for both wet and dry grinding Up to now, SAG mills with diameters up to 128 m have been designed for copper ore, at which the mills have reached the limits of their capacityTrends in der Minenindustrie Mineral Processing