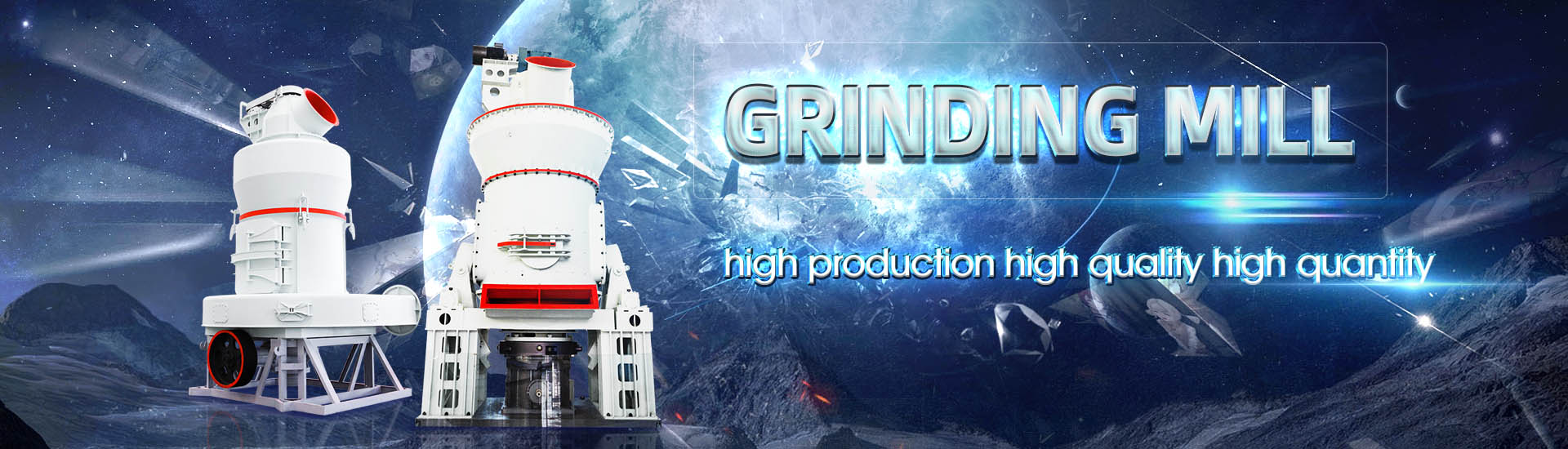
Cement plant clinker processing
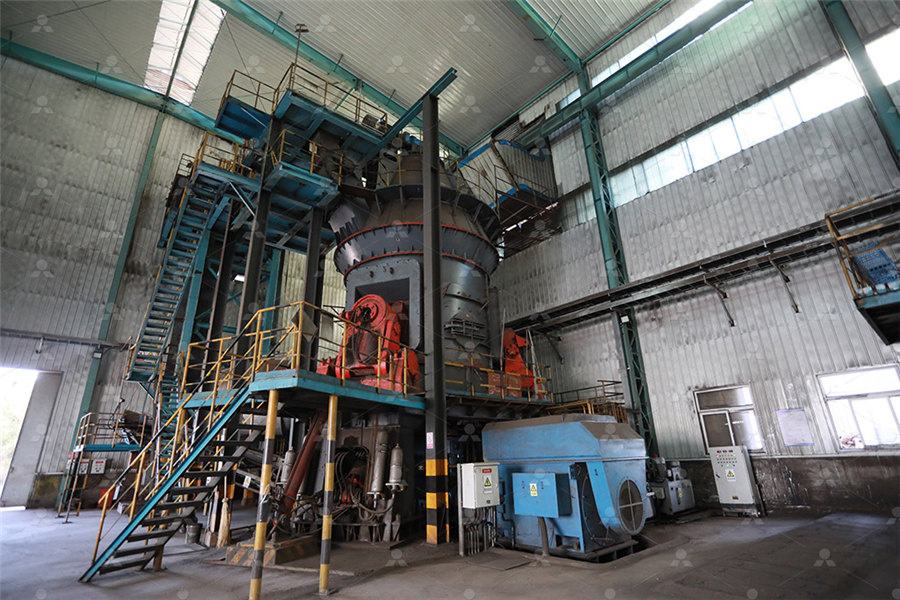
Process characteristics of clinker and cement production
2018年11月30日 New ratebased model was developed and used to validate fullscale CAP simulations for cement plants Upcoming work: CAP optimization CEMCAP framework document: ready for use! (what to do with the captured CO2 if you are in the cement industry?) The full The process of clinkerization signifies conversion of raw meal into clinker minerals mainly consisting of C4AF(Aluminoferite), C3A(Aluminite), C2S(Belite) and C3S (Alite) phases along with small percentage of free lime CaO, MgO, Alkalies, Clinkerization Cement Plant Optimization2024年3月1日 Additionally, the optimization of cement clinker composition is a crucial step toward reducing the environmental impact Cement plants have used new grinding equipment, Toward smart and sustainable cement manufacturing process3 天之前 The Cement Plant Operations Handbook is a concise, practical guide to cement manufacturing and is the standard reference used by plant operations personnel worldwide The Cement Plant Operations Handbook International
.jpg)
Clinker Production an overview ScienceDirect Topics
Clinker production is the most energyintensive stage in cement production, accounting for more than 90% of total industry energy use and virtually all the fuel use The main kiln type used 2023年11月1日 Cement plants of tomorrow will have to implement all CO 2 abatement and saving measures to the best extent possible Reducing the clinker factor, optimising the The cement plant of tomorrow ScienceDirect2023年3月3日 Clinker is the fundamental component of the cement, which is produced through a baking process in a kiln and a subsequent cooling process in a cooler, and large amounts of thermal and electric energy are required [1]Advanced Process Control for Clinker Rotary Kiln 2023年10月16日 This study proposes a raw meal proportioning methodology for optimising coprocessing of natural feedstocks with alternative raw materials in clinker production, intending Thermodynamic modelling of cements clinkering process as
.jpg)
Modelling the cement process and cement clinker quality
2015年9月24日 Manufacturers of clinker and cement must enact environmental measures but at the same time maintain the production of goodquality cement while preserving stable running 2022年4月12日 To provide highquality data to estimate China’s processrelated emissions from cement production, this study developed a panel dataset for the cement industries of China’s China’s provincial process CO2 emissions from cement2023年12月20日 Handheld XRF analyzers can identify material composition and contaminants or obtain geochemical data in the field, or anywhere in the plant Laboratory XRay Fluorescence (XRF) systems are used by cement QC The Cement Manufacturing Process Thermo Cement grinding plant process clinker into the required size, and finished cement is obtained What is clinker plant? As we all know, cement production line can be generally divided into three main parts, raw material production, clinker Cement Equipment For Clinker Production
.jpg)
Cement Plant: The Manufacturing Process 4 5 World
2019年10月23日 Cement Plant: The Manufacturing Process worldcementassociation 1 Limestone (CaCO3) is taken from a quarry 2 4 3 The limestone is fed into a crusher and then stored until needed The clinker is mixed with additives, such as gypsum, and then ground in a cement mill, which creates cement The cement is then packed and distributed to consumers2021年2月8日 Process heat overview Clinker, and clinker substitutes, are the active components that confer cement its binding properties Producing traditional cement clinker is an extremely energy and CO 2 intensive process In the EU, 90% of clinker is now made via the more energy efficient dry clinkermaking process (2) Older, less efficient wetDeep decarbonisation of industry: The cement sectorSpecific brick Consumption in grams/tonclinker The overall process of conversion from raw meal to clinker being endothermic demands a theoretical heat of about 380420 kcal/kgclinker Five stagecyclones are commonly existing in cement plants In order to increase heat utilization in kiln system, six stage cyclones are as well installed Clinkerization Cement Plant OptimizationWhile each cement plant may differ in layout, equipment, and appearance, the general process of manufacturing portland cement is the same: crushed limestone and sand are mixed with ground clay, shale, iron ore, fly ash and alternative raw materials Each step of the cement production process is carefully monitored to ensure efficiency and How Cement is Made Portland Cement Association
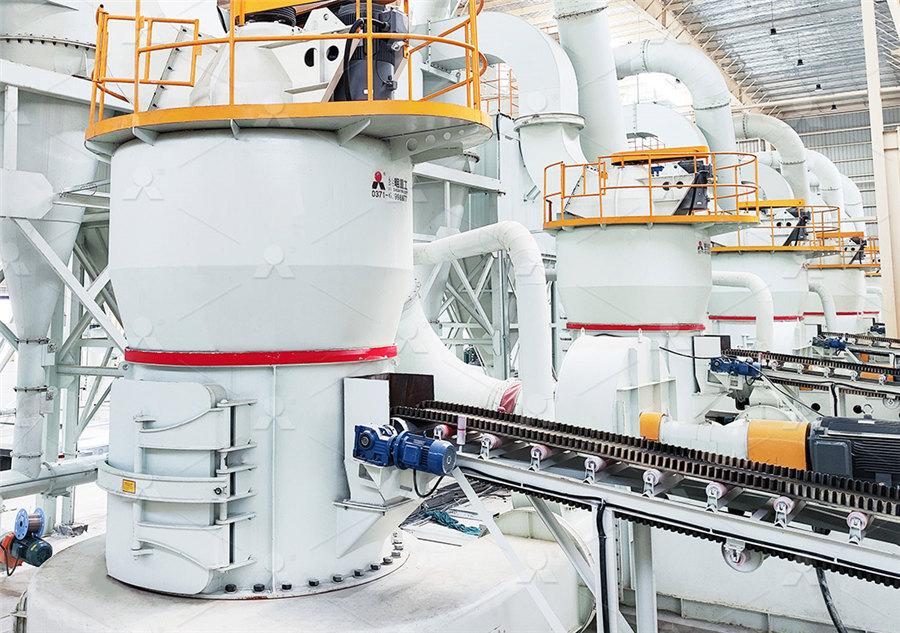
Pyroprocessing and Kiln Operation Indian Cement Review
2023年1月16日 Pyroprocessing in a cement plant comprises a preheater, rotary kiln and clinker cooler Pyroprocessing section is considered to be the heart of a cement plant as actual cement clinker production takes place in kilns The size of a cement plant is determined based on the pyroprocessing section and the sizes of all other equipment are AGICO Cement provides cement equipment of clinker production, including rotary kiln, preheater, and precalciner, start cement plant now! Skip to content +86 Clinker Production Clinker Plant Cement Plant EquipmentThe limit has to be individually adjusted to each cement plant and clinker With the close control of the phosphate level of the respective alternative fuels, the maximum proportion of the fuel can easily be calculated Calcination is the main process of clinker production, calcining calcium carbonate (CaCO 3) at about 900 °C to form Clinker Production an overview ScienceDirect Topics2024年11月16日 The main part of the manufacturing process of clinker takes place in the kiln The stages in the kiln phase are as follows: Evaporation of free water: A pressure above atmospheric is required to vaporize the water from the slurry mixture of raw materialsCement Clinker Manufacturing Process with Reactions
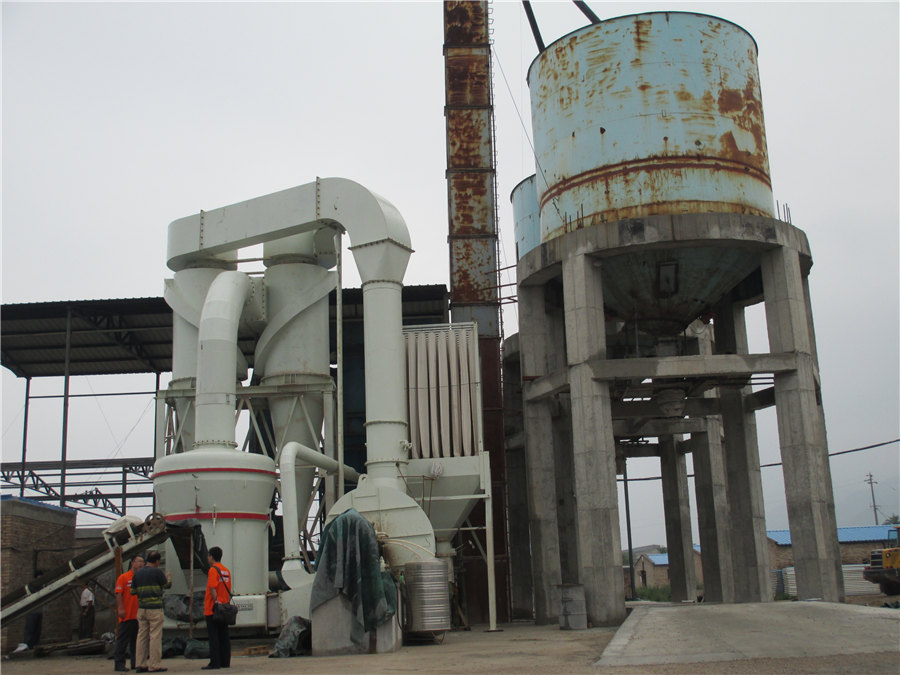
Clinker Production Clinker Manufacturing
The production of cement can be divided into dry process and wet process, while because of the high output, low heat consumption and steady running, the dry process has become the most commonly used manufacturing method in 2024年3月1日 Cement plants have used new grinding equipment, dryprocess instead of the wetprocess kiln, modern clinker kilns, and multistage preheaters that can save energy [1] The use of blends with renewable fuel and fossil fuel [ 2 ] or the use of solar calcination reactors [ 3 ] can reduce emissions and save energy in cement manufacturingToward smart and sustainable cement manufacturing process2019年8月27日 The major raw materials used as a source of CaO for cement manufacturing are limestone, chalk, marl, etc These raw materials by virtue of their natural occurrence contains other mineral impurities eg, MgO, SiO 2, Al 2 O 3, Fe 2 O 3, alkali compounds, and sulfidesThese impurities play an important role to influence the cement manufacturing Cement Manufacturing and Process Control SpringerLink2020年9月22日 The use of cement and concrete, among the most widely used manmade materials, is under scrutiny Owing to their largescale use, production of cement and concrete results in substantial emission Environmental impacts and decarbonization strategies in the cement
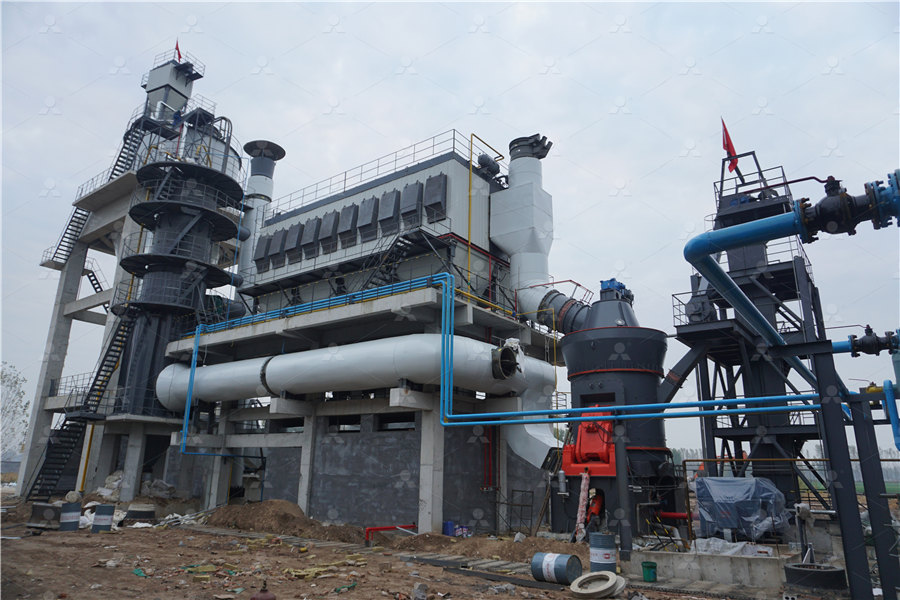
Reactions in the cement kiln clinkering Understanding Cement
Clinker: reactions in the kiln However, reading an article or two is perhaps not the best way to get a clear picture of a complex process like cement production To get a more complete and integrated understanding of how cement is made, do have a look at the Understanding Cement book or ebook This easytoread and concise book also 2023年10月19日 Clinker grinders are an important part of the cement manufacturing process They are used to grind clinker into a fine powder and are typically located at the end of the cooler in a cement plant Clinker is a nodular material produced during the cement manufacturing process and is the primary raw material for making cement Here are some common Understanding the Role of Clinker Grinding in Cement 2018年7月31日 In cement plants clinker outlet temperature is directly evaluated by clinker cooler process efficiency Cooling processes may be evaluated as one of the energy input considering demand of secondary air and carrier gas In this study the clinker cooler performanceDevelopment of Cooling Performance of Clinker Cooler Process Rotary cooler is one kind of cement cooler applied for cement manufacturing plantsAs an essential part of the cement kiln system, a rotary cooler is used to cool the clinker discharged from the cement rotary kilnThe rotary cooler also helps air to absorb the large amounts of heat carried by clinker, heating the combustion air up to the high temperature, strengthen the calcination, Rotary Cooler Clinker Cooler In Cement Plant AGICO CEMENT
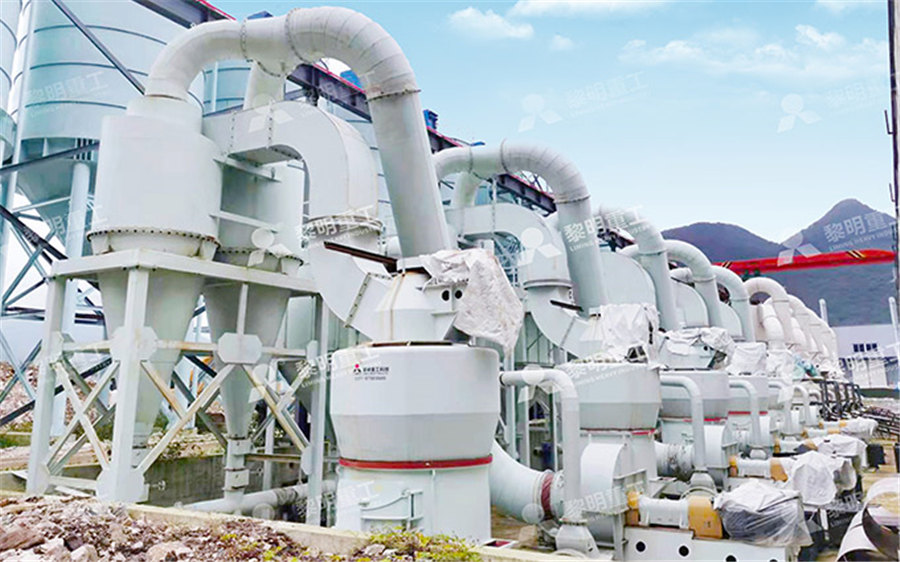
China’s provincial process CO2 emissions from cement
2022年4月12日 Measurement(s) carbon dioxide emission process Technology Type(s) computational modeling technique Factor Type(s) cement production • clinker production • the emission factor of clinker Sample 2023年5月22日 The cement plant has a rated capacity of ~ 15 tpd clinker and producing approx 1450 tpd There were reducing conditions prevailing at kiln inlet Specific heat consumption works out to 960 kcal/kg clinker based upon the heat balance, operating parameters and plant data for entire pyro processing sectionRefuse Derived Fuel (RDF) Coprocessing in Kiln Main Burner in a Cement 2020年9月9日 Italian cement industries are among the major cement producers in the European panorama In the last decades, because of the increasingly stringent specifications on environmental impact and energy saving, technology in the cement plant has been significantly improved []In this context, Advanced Process Control (APC) systems have become the Optimization of the Clinker Production Phase in a Cement Plant2015年5月5日 A process model that included plantspecific parameters of a cement plant using thermochemical data from Fact, where no mixed solution phases were included, was developed by Modigell et al (2002) The linking of coupled chemical equilibrium reactors for modelling the alkali and sulfur chemistry in the cement kiln due to the utilisation of used Modelling the cement process and cement clinker quality
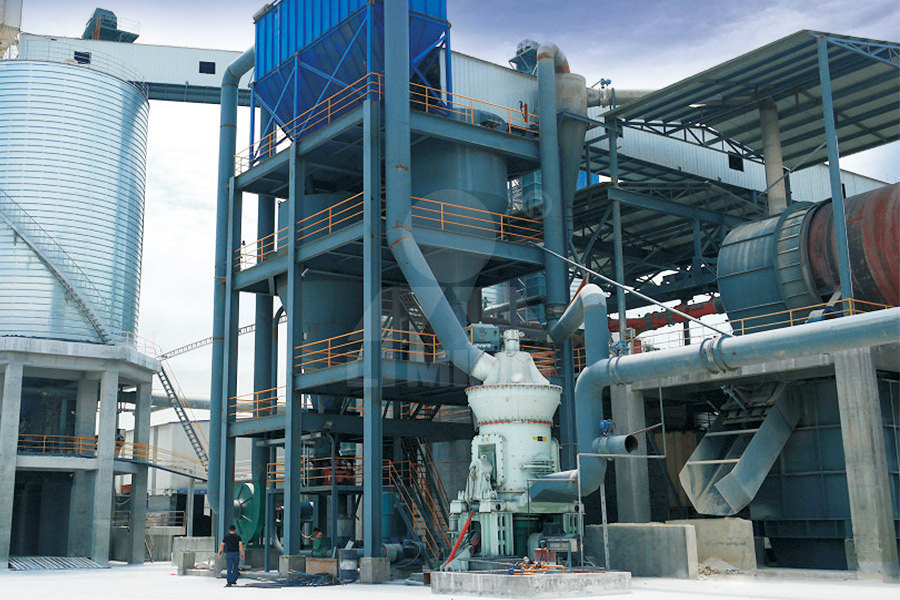
Cement Grinding Unit Clinker Grinder AGICO Cement
It can not only grind cement clinker but also process cement admixture, such as gypsum, fly ash, furnace slag, coal gangue, etc, realizing a stable, highquality and automated cement production Unlike the cement production line , the cement grinding plant is usually established around the sales market, which saves a lot of transportation costs2019年4月23日 Wet process cement plants impact their surroundings by slurry disposal while dry and semidry plants also create solid waste, which is an environmental concern Figure 3A and B show clinker obtained from a cement plant that does not use any waste in their process The clinker phases formed in these processes are alite and beliteAn overview of alternative raw materials used in cement and clinker 2021年3月24日 Cement manufacturing requires cooling down of hot clinker at temperature of about 1350o C to temperature lower than 100 o C in a cooling system known as clinker cooler Many plants are unable to Modelling of clinker cooler and evaluation of its 2019年8月26日 Cement Manufacturing and Process Control 41 Cement Manufacturing: Basic Process and Operation To design the Refractory for the lining of different equipments in a cement plant, it is necessary to understand the total operational process of a cement plant in depth It is necessary to know the conditions prevailing in different equipments and theChapter 4 Cement Manufacturing and Process Control
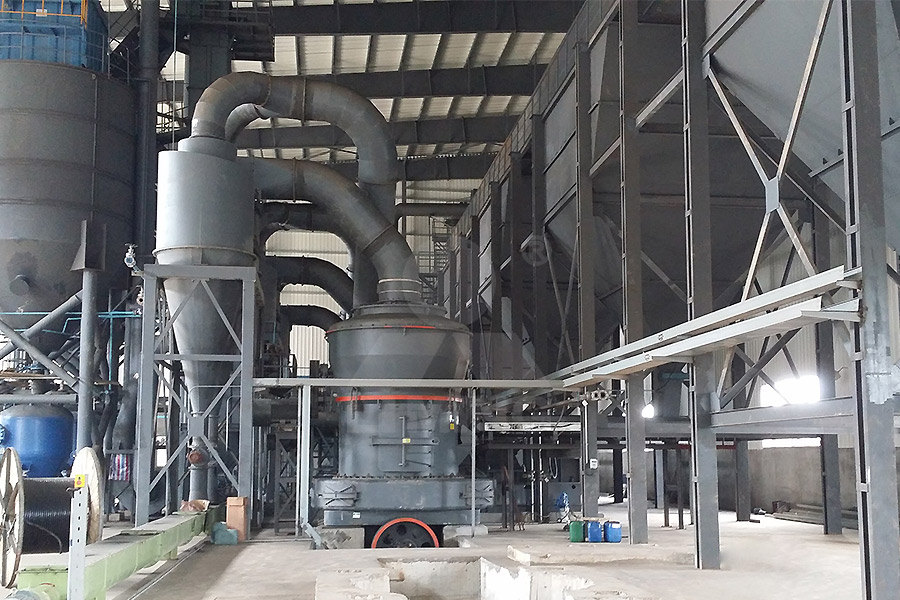
Cement Plant, Cement Equipment Cement Plant
Cement plant is necessary for cement production, and mainly consists of a series of cement equipment apply for the preparation of cement raw materials, clinker production, and finished cement production, such as a cement mill, cement crusher, rotary kiln, cement roller press, cement dryer, clinker cooler, cement silo, and related cement plant equipment2024年6月1日 The cement industry is the secondlargest source of direct CO 2 emissions and the thirdlargest energy consumer in the industrial sector (IEA, 2018)The heat required for the pyroprocessing (clinker production phase) is obtained primarily by combusting fossil fuels (mainly, coal) (Ige et al, 2022)Efforts are underway to decrease the dependence on fossil A life cycle assessment of clinker and cement ScienceDirect2023年12月20日 Handheld XRF analyzers can identify material composition and contaminants or obtain geochemical data in the field, or anywhere in the plant Laboratory XRay Fluorescence (XRF) systems are used by cement QC The Cement Manufacturing Process Thermo Cement grinding plant process clinker into the required size, and finished cement is obtained What is clinker plant? As we all know, cement production line can be generally divided into three main parts, raw material production, clinker Cement Equipment For Clinker Production
制粉项目-2023.11.17.jpg)
Cement Plant: The Manufacturing Process 4 5 World
2019年10月23日 Cement Plant: The Manufacturing Process worldcementassociation 1 Limestone (CaCO3) is taken from a quarry 2 4 3 The limestone is fed into a crusher and then stored until needed The clinker is mixed with additives, such as gypsum, and then ground in a cement mill, which creates cement The cement is then packed and distributed to consumers2021年2月8日 Process heat overview Clinker, and clinker substitutes, are the active components that confer cement its binding properties Producing traditional cement clinker is an extremely energy and CO 2 intensive process In the EU, 90% of clinker is now made via the more energy efficient dry clinkermaking process (2) Older, less efficient wetDeep decarbonisation of industry: The cement sectorSpecific brick Consumption in grams/tonclinker The overall process of conversion from raw meal to clinker being endothermic demands a theoretical heat of about 380420 kcal/kgclinker Five stagecyclones are commonly existing in cement plants In order to increase heat utilization in kiln system, six stage cyclones are as well installed Clinkerization Cement Plant OptimizationWhile each cement plant may differ in layout, equipment, and appearance, the general process of manufacturing portland cement is the same: crushed limestone and sand are mixed with ground clay, shale, iron ore, fly ash and alternative raw materials Each step of the cement production process is carefully monitored to ensure efficiency and How Cement is Made Portland Cement Association
.jpg)
Pyroprocessing and Kiln Operation Indian Cement Review
2023年1月16日 Pyroprocessing in a cement plant comprises a preheater, rotary kiln and clinker cooler Pyroprocessing section is considered to be the heart of a cement plant as actual cement clinker production takes place in kilns The size of a cement plant is determined based on the pyroprocessing section and the sizes of all other equipment are AGICO Cement provides cement equipment of clinker production, including rotary kiln, preheater, and precalciner, start cement plant now! Skip to content +86 Clinker Production Clinker Plant Cement Plant EquipmentThe limit has to be individually adjusted to each cement plant and clinker With the close control of the phosphate level of the respective alternative fuels, the maximum proportion of the fuel can easily be calculated Calcination is the main process of clinker production, calcining calcium carbonate (CaCO 3) at about 900 °C to form Clinker Production an overview ScienceDirect Topics2024年11月16日 The main part of the manufacturing process of clinker takes place in the kiln The stages in the kiln phase are as follows: Evaporation of free water: A pressure above atmospheric is required to vaporize the water from the slurry mixture of raw materialsCement Clinker Manufacturing Process with Reactions