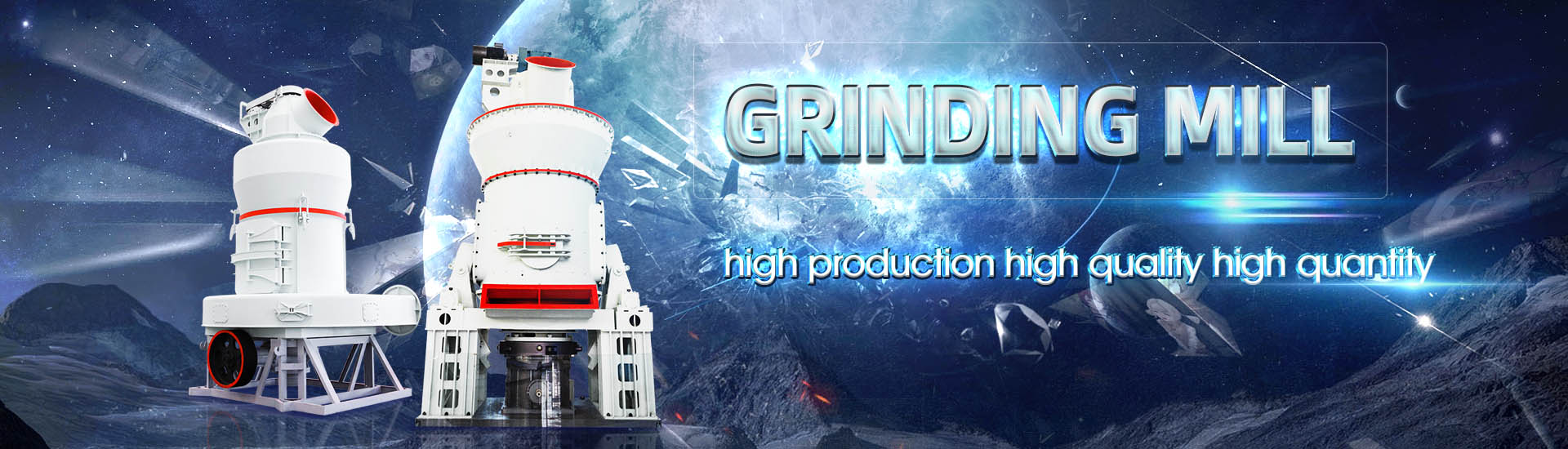
Large pig iron block crushing method
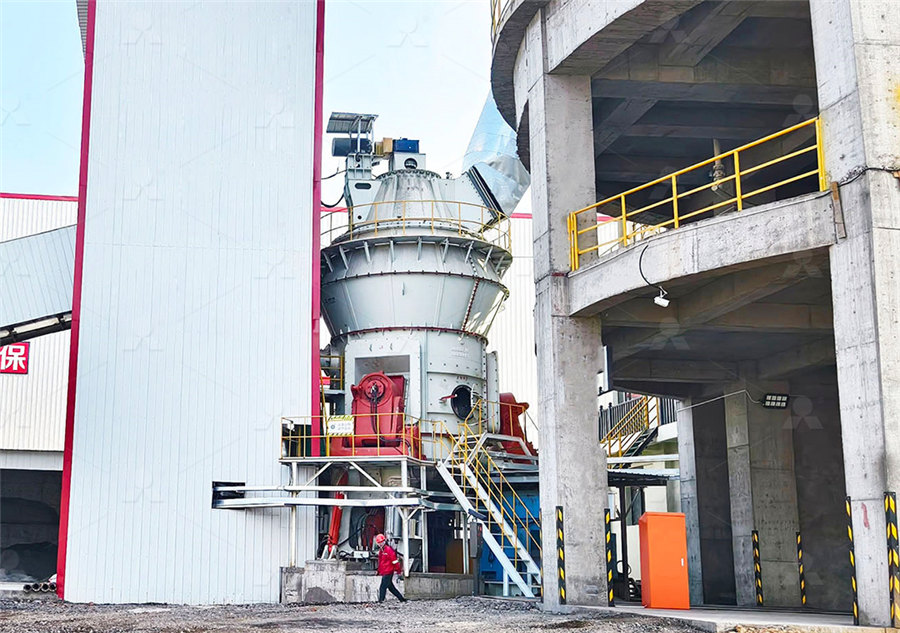
Original ArticleThe production of pig iron from crushing plant
2018年3月1日 A production of pig iron has been conducted from crushing plant waste The process of preparing pig iron was using hot blast cupola (HBC) furnace which was injected with charcoal powder to improve temperature process and reduction zone in the furnace2016年11月1日 The process of preparing pig iron was using hot blast cupola (HBC) furnace which was injected with charcoal powder to improve temperature process and reduction zone in the furnace The process(PDF) The production of pig iron from crushing plant 2016年11月24日 Novel machine learning models are designed, developed, and deployed on a rich data sample covering more than 20 production variables spanning nine years of actual [PDF] The production of pig iron from crushing plant waste using major steelmaking method involves the melting and refining of steel scrap in an Electric Arc Furnace Pig iron and refined iron ore pellets (briquetted iron) can also be used, and because The Making of Iron Steel SEAISI
.jpg)
A novel recycling and reuse method of iron scraps from machining
2020年9月1日 Disperse iron scraps have been compressed into block/cakes state by neither adding any additives nor heating them Iron scraps block possesses high green density and The process of preparing pig iron was using hot blast cupola (HBC) furnace which was injected with charcoal powder to improve temperature process and reduction zone in the furnace The processThe result of pig iron analysis composition Download First the process requires a great amount of carbon input (around 430 kg of C/ t of liquid iron), which can be introduced in two ways: either loaded as lumps at the top with the sinter, or Using Biomass for Pig Iron Production: A Technical, Environmental attention should be given to technical solutions that will reduce the cost of making pig iron and speed up the return on invest ments The following Paul Wurth innovations are particularly EQUIPMENT AND TECHNOLOGY OF THE PAUL WURTH
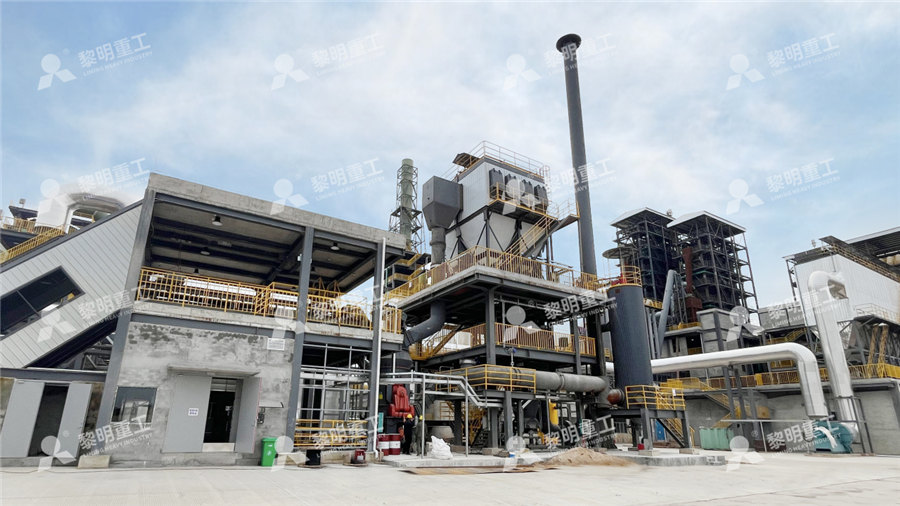
A critical review on metallurgical recovery of iron from iron ore
2024年4月1日 Ion exchange demonstrates effectiveness and selectivity in recovering iron value from ironcontaining leachate This method involves selective exchange between iron ions in This guide refers to the handling of merchant pig iron produced in blast furnaces, electric smelting furnaces, and other iron making processes The term “pig iron” can be traced back to the Pig Iron: Guide for Transportation and Handling Metallics2020年6月10日 where D = hearth diameter (m), Q = coke throughput (tonnes/24 h), C = throughput coefficient, which varies between 02 and 03, for large size blast furnace, C = 02; P = hot metal production rate (T/day), K = coke consumed (tonnes/THM)THM—ton of hot metal Example 1 A blast furnace plans to produce 10,000 tons iron per day, with an optimum coke Blast Furnace Refractory SpringerLinkIron processing Smelting, Refining, Alloying: The primary objective of iron making is to release iron from chemical combination with oxygen, and, since the blast furnace is much the most efficient process, it receives the most attention Iron processing Smelting, Refining, Alloying Britannica
.jpg)
How to Manufacture Pig Iron: How Pig Iron is made?
Guide for manufacturing and making Pig Iron Following three distinct operations are involved in the manufacturing process of pigiron: (1) Dressing (2) Calcination and roasting (3) Smelting (1) Dressing: The iron ores as obtained from mines are crushed into pieces of size of 25 mm diameter This is achieved in the rock crushers of ordinary type The crushing of ores helps in the shortage of scrap supply throughout the world and its fluctuating prices [1] Fine iron ore smelting process in cupola furnace can be considered to be similar with the process in blastThe production of pig iron from crushing plant waste2022年8月17日 Application field of iron ore crushing material Iron ore is deeply processed by the crusher and can be widely used in the following industries 1 Treat pig iron Pig iron smelting adopts the hightemperature solidstate reduction method, that is, it is smelted under the condition that the furnace temperature is increased to 11501300 °CIron ore crushing equipment and process flow2024年7月17日 Understanding material characteristics and defining production needs can help you choose the right crushing method, saving costs throughout the production process Types of crushers Crushing is a multistage process that includes primary crushing, secondary crushing, and tertiary crushing Different types of crushing equipment are used at each Types of Crushers: Choosing the Right One for Each Stage
.jpg)
SIMULTANEOUS DEPHOSPHORIZATION AND DESULPHURIZATION OF MOLTEN PIG IRON
1984年1月1日 pig iron for steel making is not only useful for in a largescale trial bath agitation I, ncccxsary t o crucible, and cavt into a block After crushing the materialBy the manufacture method of lowphosphorous lowsulfur nickelcontained pig iron of the present invention, can adopt nickel oxide ore, nickel sulfide ore, nickeliferous sulfate slag is nickel sourceThrough ore dressing or after without ore dressing, sinter abovementioned raw materials into piece, then in conventional blast furnace, smelt into the rough pig iron of nickeliferous > CNA Lowphosphorus lowsulphur nickelcontaining pig iron 2017年2月16日 Sintering is a thermal agglomeration process that is applied to a mixture of iron ore fines, recycled ironmaking products, fluxes, slagforming agents and solid fuel (coke)(PDF) Iron Ore Sintering: Process ResearchGateCast iron is a group of ironcarbon alloys with a carbon content greater than 2% It is made by melting iron and adding carbon and other elements to the molten metal, which is then poured into a mold to cool and solidify The resulting material has a crystalline structure that is Cast Iron Explained: How's It Made, Casting Methods, Types and
.jpg)
Iron Ore Processing, General SpringerLink
2022年10月20日 Iron ore handling, which may account for 20–50% of the total delivered cost of raw materials, covers the processes of transportation, storage, feeding, and washing of the ore en route to or during its various stages of treatment in the mill Since the physical state of iron ores in situ may range from friable, or even sandy materials, to monolithic deposits with hardness of 2023年10月6日 The blast furnace can also produce ferromanganese and ferrosilicon needed for steelmaking The main product of blast furnace ironmaking is pig iron, and its byproducts are blast furnace slag and blast furnace gas Pig iron can be divided into steelmaking pig iron, casting pig iron, and special pig iron according to its composition and useBlast Furnace Ironmaking SpringerLinkIron ore mining methods vary by the type of ore being mined Currently, there are four main types of iron ore deposits, depending on the mineralogy and geology of the ore deposits These are magnetite, titanomagnetite, massive hematite, and pisolitic ironstone deposits For taconite iron ores, mining iron ore begins at ground levelIron Ore Processing, General2020年12月15日 Pig iron was also acquired in the West in Roman times, but was abandoned as waste by blacksmiths Chinese casters, however, did not throw away the brittle and hard pig iron but reformed the properties of pig iron by the method of iron mold casting and technique of softening cast iron And then the wide use of pig iron pushed China into the Iron Pig IronBased Steel Smelting Technology SpringerLink
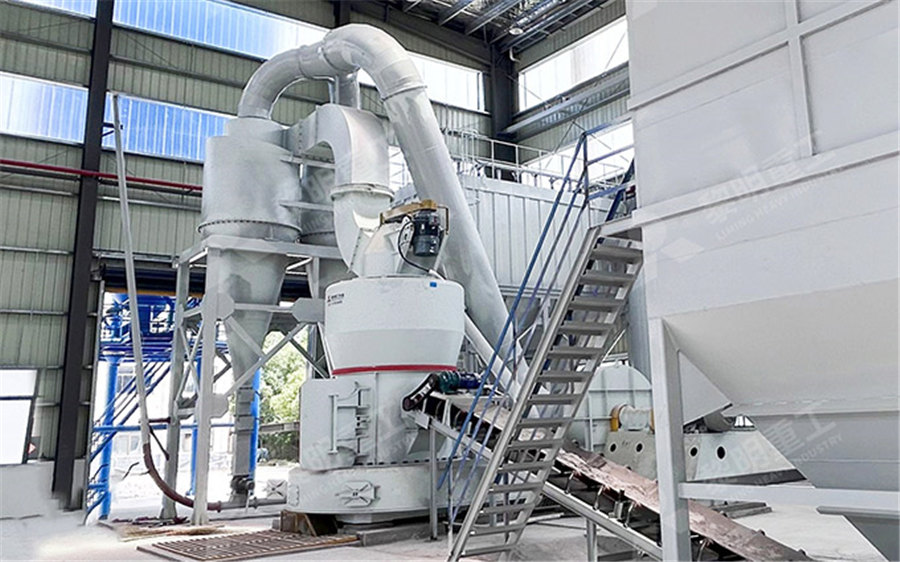
Development of Fully Controlled Rock Crushing Method and Its
2024年10月22日 The free rock crushing method involves breaking or shattering a risky block using explosive or crushing material without taking any preventive measures This method is not preferred in areas where archaeological sites and settlements are located Free rock crushing is generally used in openpit mines, for opening highway routes, and in tunnels2020年2月5日 Breaking large blocks; Breaking large blocks MineralLoy offers unique solutions for the breaking or crushing of large blocks of material in the mining, amongst others; pig iron skulls, pool iron, steel skulls, steel, ferrochrome, ferromanganese, granite, iron Breaking large blocks MineralLoy2019年9月3日 Nickel Laterite Smelting Processes and Some Examples of Recent Possible Modifications to the Conventional Route(PDF) Nickel Laterite Smelting Processes and Some ResearchGate2023年12月27日 The cone crusher is widely used for the intermediate crushing processing of steel slag and adopts the laminated crushing method Due to its strong crushing capacity and large output, it is widely used for crushing mediumhard materials Dry magnetic separation mainly recovers large blocks of iron, Steel Slag Processing Plant Equipment Selection
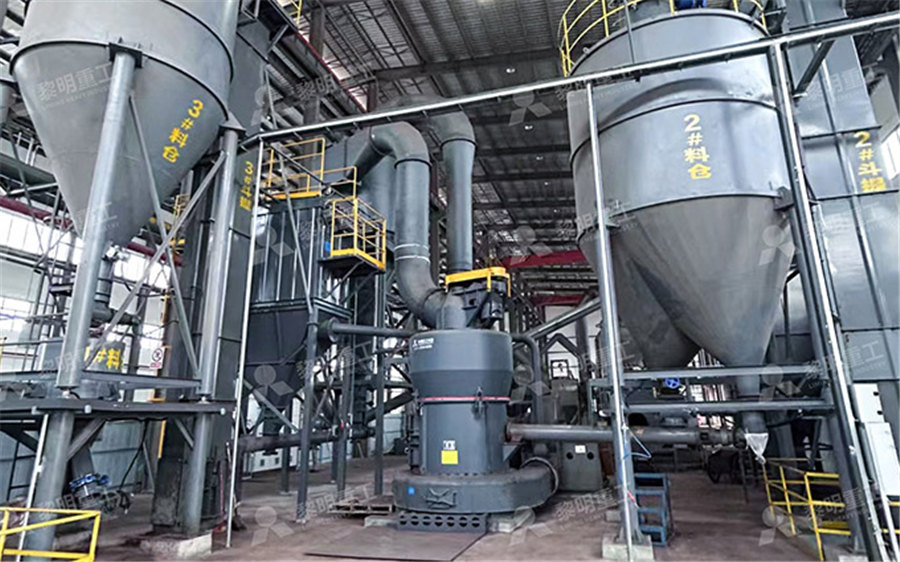
Recovery of Iron from HighIron Bayer Red Mud by Melting
2022年2月5日 Figure 2 was the XRD pattern of the cathode carbon block It could be seen from the figure that the main component of the cathode carbon block was C, followed by NaF, and it also contained fluorides such as CaF 2 and Na 3 AlF 6, and oxides of Al and SiTable 2 was the chemical composition table of the cathode carbon block The main chemical components of iron) (kg slag /t steel) ARCELORMITTAL OSTRAVA as Total B t e 3 159 Pig iron Slag 1 092 346 ks Steel 3 006 g 648 216 Tandem furnace 580 193 Ladle 68 23 TŘINECKÉ ŽELEZÁRNY, as ks e 2 033 SLAG FROM PRODUCTION OF PIG IRON AND STEEL MAKING 2023年10月13日 Improve the crushing quality of ore rock, and its large block rate is 40% to 50% less than that of single row hole blasting; The efficiency of drilling equipment is increased by about 10% to 15% This is due to the 6 Common Blasting Methods in Open Pit MiningThe first step is commonly crushing, in which large pieces of ore are reduced to a Extraction Method; Potassium: K: Electrolysis: Sodium: N a: Calcium: C a: Magnesium: M Cast iron is primarily used to make pans, drain covers, engine blocks, and fences The rest of the pig iron is usually turned into steel because steel is harder and Lesson Explainer: Extracting Iron Nagwa
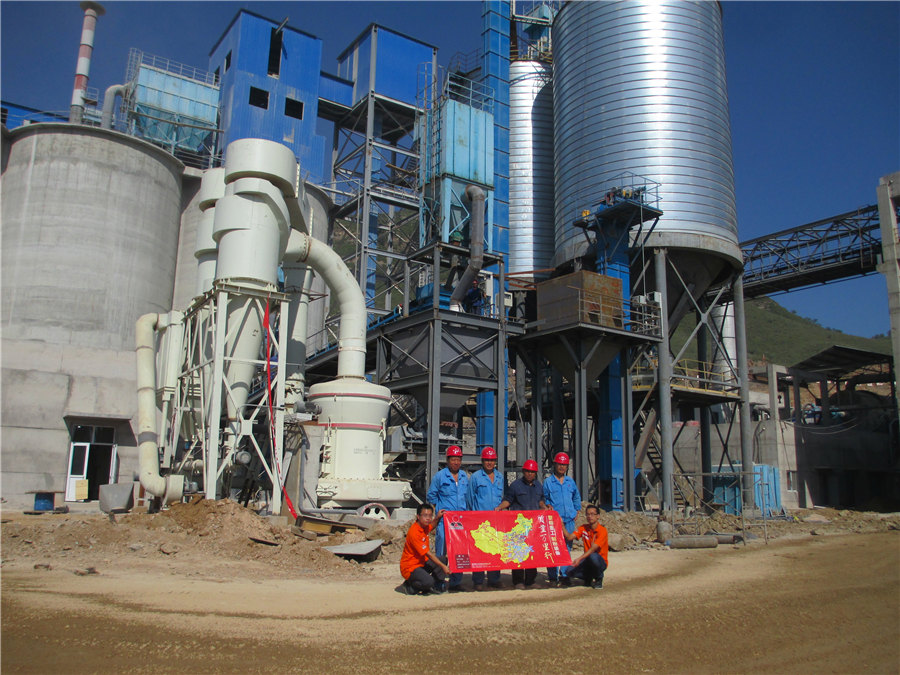
Iron processing Definition, History, Steps, Uses,
Although the Romans built furnaces with a pit into which slag could be run off, little change in ironmaking methods occurred until medieval times By the 15th century, many bloomeries used low shaft furnaces with water power to drive The utility model belongs to the technical field of pig iron crushing, in particular to a pig iron crusher for crushing large cast iron, wherein a crushing device is arranged on a machine body, a first roller is arranged near one side in the machine body, first output shafts are arranged at two ends of the first roller, a first gear is arranged on each first output shaft, a second roller is Pig iron crusher for crushing large cast iron Google Patents2020年7月31日 BASIC OXGEN FURNACE [BOF] : This method of production converts molten pig iron into steel by blowing Oxygen into the mixture of liquid iron [Pig Iron], steel scraps, limestone alloys at high SERIES 003: FERROUS METALLURGY PIG IRON LinkedIn2023年2月28日 Learn everything you need to know about primary crushing, secondary crushing, and tertiary crushing in this comprehensive guide Discover the types of crushers used in each stage, their working principles, and the advantages and disadvantages of each process Get answers to frequently asked questions and improve your understanding of the comminution The Complete Guide to Primary Crushing, Secondary Crushing,
.jpg)
From Ancient to Modern Methods Steel Technology
As societies progressed, humans began to extract iron from terrestrial sources, marking the transition from the use of meteoric iron to smelting iron ore One of the earliest known methods of iron smelting was the bloomery process This ancient technique, dating as far back as 1200 BCE, involved heating iron ore in a furnace with charcoal2018年5月30日 Corrosion and anodic performance of newly developed composite sacrificial anodes based on high phosphorus pig iron, Al, and Zn with the stoichiometry xPyAl and xPy(Al075Zn025) (x = 15, 35 Possibility of High Phosphorus Pig Iron as Sacrificial AnodeJaw Crushers have found their extensive application for the mid crushing of the various ores and largesize materials block in the field of mining, smelting, building material, highway, railway, waterSIZE REDUCTION BY CRUSHING METHODS By ResearchGate2024年8月27日 Pig Iron Pig iron is obtained by smelting iron ore with coal, which is coke, and limestone as a fluxing agent It is made in a blast furnace and comes with high carbon levels, averaging 4% About 5 percent of impurities are present in Cast Iron vs Pig Iron: Differences, Pricing Properties Sree
.jpg)
Blast Furnace Refractory SpringerLink
2020年6月10日 where D = hearth diameter (m), Q = coke throughput (tonnes/24 h), C = throughput coefficient, which varies between 02 and 03, for large size blast furnace, C = 02; P = hot metal production rate (T/day), K = coke consumed (tonnes/THM)THM—ton of hot metal Example 1 A blast furnace plans to produce 10,000 tons iron per day, with an optimum coke Iron processing Smelting, Refining, Alloying: The primary objective of iron making is to release iron from chemical combination with oxygen, and, since the blast furnace is much the most efficient process, it receives the most attention Iron processing Smelting, Refining, Alloying BritannicaGuide for manufacturing and making Pig Iron Following three distinct operations are involved in the manufacturing process of pigiron: (1) Dressing (2) Calcination and roasting (3) Smelting (1) Dressing: The iron ores as obtained from mines are crushed into pieces of size of 25 mm diameter This is achieved in the rock crushers of ordinary type The crushing of ores helps in How to Manufacture Pig Iron: How Pig Iron is made?the shortage of scrap supply throughout the world and its fluctuating prices [1] Fine iron ore smelting process in cupola furnace can be considered to be similar with the process in blastThe production of pig iron from crushing plant waste
.jpg)
Iron ore crushing equipment and process flow
2022年8月17日 Application field of iron ore crushing material Iron ore is deeply processed by the crusher and can be widely used in the following industries 1 Treat pig iron Pig iron smelting adopts the hightemperature solidstate reduction method, that is, it is smelted under the condition that the furnace temperature is increased to 11501300 °C2024年7月17日 Understanding material characteristics and defining production needs can help you choose the right crushing method, saving costs throughout the production process Types of crushers Crushing is a multistage process that includes primary crushing, secondary crushing, and tertiary crushing Different types of crushing equipment are used at each Types of Crushers: Choosing the Right One for Each Stage1984年1月1日 pig iron for steel making is not only useful for in a largescale trial bath agitation I, ncccxsary t o crucible, and cavt into a block After crushing the materialSIMULTANEOUS DEPHOSPHORIZATION AND DESULPHURIZATION OF MOLTEN PIG IRONBy the manufacture method of lowphosphorous lowsulfur nickelcontained pig iron of the present invention, can adopt nickel oxide ore, nickel sulfide ore, nickeliferous sulfate slag is nickel sourceThrough ore dressing or after without ore dressing, sinter abovementioned raw materials into piece, then in conventional blast furnace, smelt into the rough pig iron of nickeliferous > CNA Lowphosphorus lowsulphur nickelcontaining pig iron
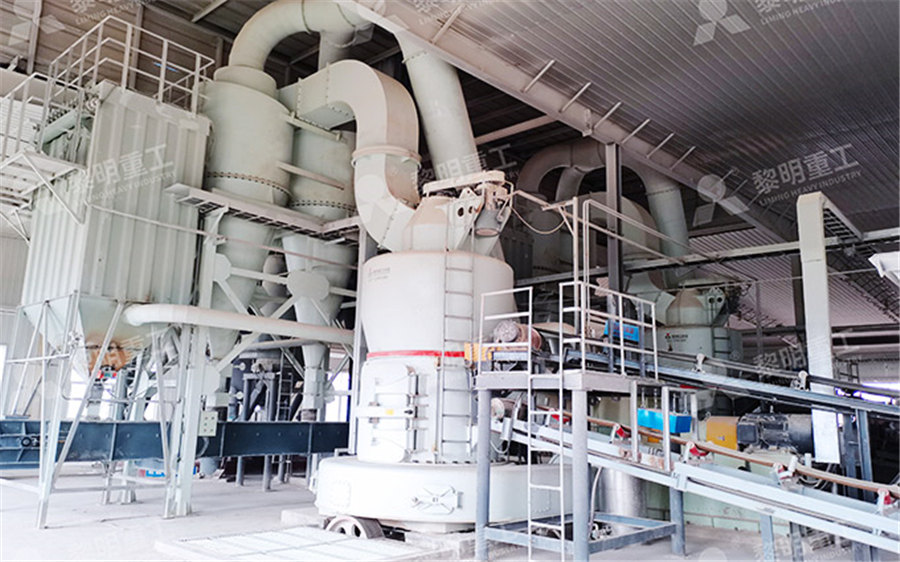
(PDF) Iron Ore Sintering: Process ResearchGate
2017年2月16日 Sintering is a thermal agglomeration process that is applied to a mixture of iron ore fines, recycled ironmaking products, fluxes, slagforming agents and solid fuel (coke)Cast iron is a group of ironcarbon alloys with a carbon content greater than 2% It is made by melting iron and adding carbon and other elements to the molten metal, which is then poured into a mold to cool and solidify The resulting material has a crystalline structure that is Cast Iron Explained: How's It Made, Casting Methods, Types and