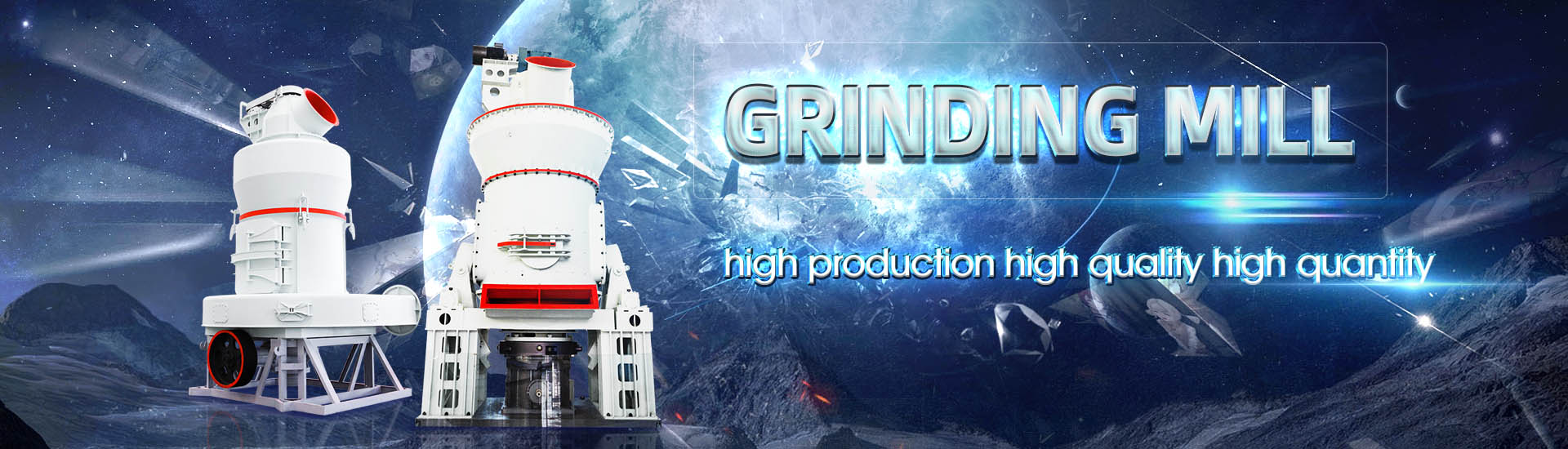
Dry quenching water slag mill test machine
.jpg)
Process and Equipment Design for the Dry Slag Granulation
2017年1月7日 The 100% crystalline sample can be obtained by heating blast furnace slag for 12 h at 1 0001 200 degrees C, and the 100% noncrystalline sample can be obtained by Dry quenching method saves water (around 05–10 m 3 per ton of gross coke); reduced water pollution as well gives opportunity for waste heat recovery Stable coke quality and energy Dry Quenching an overview ScienceDirect Topics2023年9月6日 Dry slag granulation is based on molten slag atomization using a variable speed rotating cup or dish (see Fig 1) The slag is fed from the slag runner via a vertical refractory Dry Slag Granulation – The Future Way to Granulate Blast Furnace The granulation of blast furnace (BF) slag with water quenching has many disadvantages, such as high water consumption and difficulty in heat recycling The dry granulation technology to treat Process and Equipment Design for the Dry Slag Granulation
.jpg)
(PDF) RECENT DEVELOPMENTS IN DRY SLAG GRANULATION: A
2017年9月1日 Here we review common slag handling practices, the developments in dry slag granulation over the last three decades, introduce the EcomaisterHatch dry slag granulation The present paper covers some of the fundamental aspects of the reactions taking place during dry granulation of molten slag In particular, the cut in sulphur emission from slag during DSG Some Fundamental Aspects of Dry Slag Granulation Process2016年6月1日 The hightemperature blast furnace slag is conventionally treated by water quenching (WQ) method with enormous waste heat unrecovered To address this issue, dry Energy–environment–economy evaluations of ScienceDirect2021年11月3日 A magnification in the feed rate and water pressure, together with an increase in the rate of suction (vacuuming capacity) and granulation of liquid slag, intensifies the heat A new technological approach to the granulation of slag melts of
.jpg)
A Review of Granulation Process for Blast Furnace Slag Semantic
In blunt box, high pressure water from porous nozzle jet will quench the molten BF slag In the next case, water quenching slag pours through graining tank and flows into the settling pond Water granulation is sometimes applied to BF slag It involves quenching, fragmenting, and granulating molten slag with water The resulting granulated slag is glassy in structure and is RECENT DEVELOPMENTS IN DRY SLAG GRANULATION: A PATH Since its first introduction, coke dry quenching is being widely spread worldwide For example, in Japan, the number of dry quenching coking plants increased from six in the 1970s to 42 in the 2010s (Okazaki and Yamaguchi, 2011); China has 117 dry quenching plants, accounting for 80% of the coke production in the country (Huo et al, 2012)Dry Quenching an overview ScienceDirect Topics2021年11月3日 The technological factors required to improve the operational properties of granulated metallurgical slags demanded in the building industry have been analyzed In order to satisfy these factors, a new technology for hydrovacuum granulation of slag melts (HVG) has been developed It is shown that the main advantage of the proposed HVG process is the A new technological approach to the granulation of slag melts of

Analysis of Blast Furnace Slag Quenching Dry Granulation Process
Three types of BF slag quenching dry granulation process including drum granulation,air blast granulation ,which have been subjected to industrial test were introducedThe advantage and disadvantage of those processes were analyzedThe effects Dry slag granulation vs water quenching Hong Wang Junjun Wu Xun Zhu Q Liao Liang ZhaoOur dry slag granulation technology involves pouring molten slag from above our rig down to a spinning disc That disc is spinning at high speed and it atomises the molten slag into small granules [Image changes to show molten slag being atomised and collected in the taurus]Dry slag granulation: producing valuable byproducts from waste2017年9月1日 Following different test series, where the slag quality and suitability for cement production was proven, Paul Wurth built a full scale dry slag granulation pilot plant at Rogesa's blast furnace No 4(PDF) RECENT DEVELOPMENTS IN DRY SLAG GRANULATION: ASmelting Slag Produced by Water Quenching* by Hojin RYUI, Kazumasa SUGIYAMA2 and Fumio SAITO 3 〔UDC 669551; 621745 58〕 The strength and grindability of copper smelting slag produced by water quenching have been investigated in the framework of single particle crushing and corrective grinding testsA Study on the Strength and Grindability of Granulated Copper Smelting
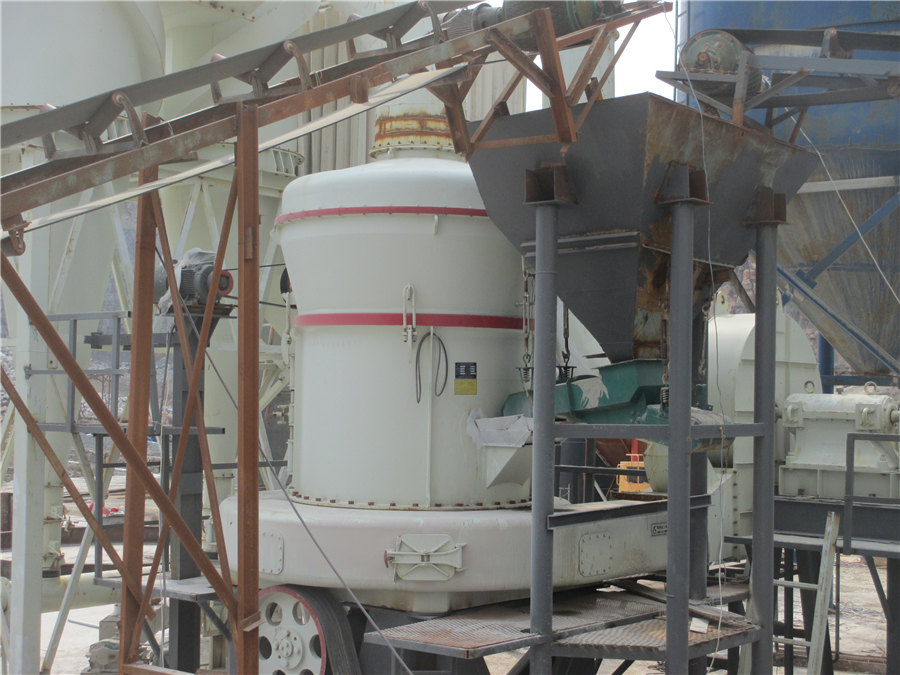
Energy–environment–economy evaluations of ScienceDirect
2016年6月1日 During water quenching process, highpressure water is employed to shatter the molten slag However, the water quenching methods not only fail to recover the hightemperature waste heat but also consume a huge amount of fresh water by the evaporation of 1000–1500 l of water per ton of slag [13]balls The reaction between the ground slag and water, by which calcite is formed in the drying process, becomes active with the progress of grinding KEY WORDS: Grinding Aids, Dry Fine Grinding, Blast Furnace Slag, Xray Diffraction, Mechanochemical Effect, Ball Mill 1 Introduction Blast furnace slag is obtained as metallurgical waste producDry Fine Grinding of Granulated Blast Furnace Slag Quenched by Water 5000tpd Dry Process Cement Plant Project In Liaoning; is obtained by quenching molten iron slag from a blast furnace in water or steam As the name implies, the GGBS plant is designed to process blast furnace vibrating feeder, slag mill, fan, powder collector, bag filter, etc 1 Crushing equipment The slag needs to be crushed into Slag Grinding Plant GGBS Plant Slag Mill, Slag Grinding Mill2023年5月11日 To overcome the shortcomings of the water quenching technique, several dry granulation techniques have been proposed, such as rotating drums, centrifugal granulation, and gas quenching The gas quenching granulation process is noted to have lower water consumption, higher waste heat recovery efficiency, and be more environmentally friendly than Numerical Simulation of the Slag Granulation Process in Gas Quenching
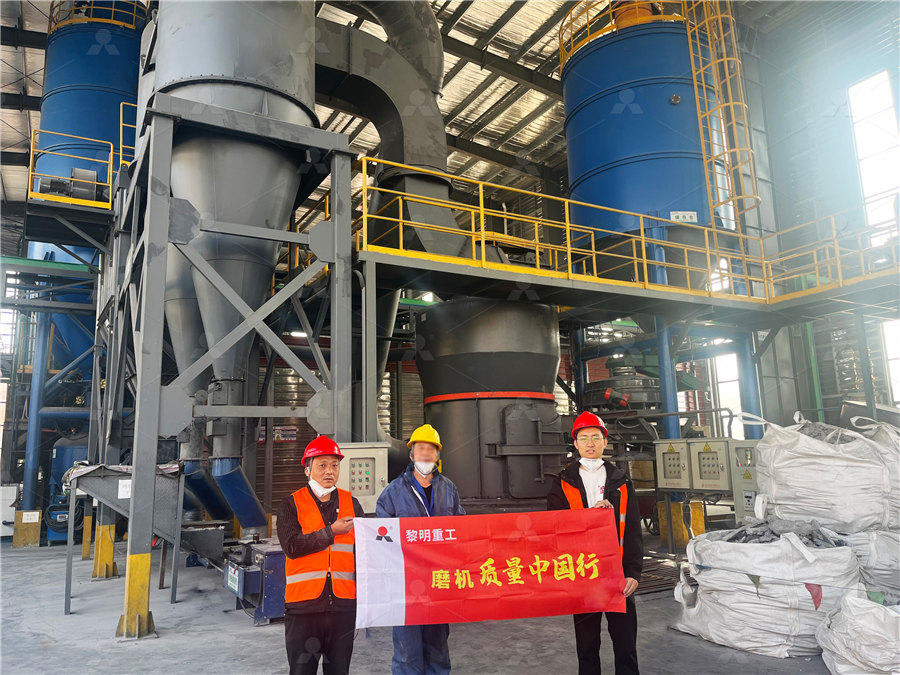
Exergy Analysis of a Coke Dry Quenching System CSC
conventional wet quenching process Figure 1 illustrats the process flow diagram of the installed CDQ system As described above, the coke dry quenching process involves sophisticated heat, mass transfer and combustion phenomena For the purposes of process control and of getting more insight into the CDQ system, the exergyLaboratory scale tests, similar to those conducted during this project, ^ would help determine the feasibility fl of using coke plant wastewater as a quenching medium for BF slag quenching 3 Tests conducted at a plant site that practices hard slag quenching with mill water, blast furnace blowdown water, and (if possible) coke plant wastewater Assessment Of Atmospheric Emissions From Quenching Of Blast 2021年12月15日 Depending on how hard the water is, as the water evaporates from quenching or just low humidity, the inorganic content can change the quenching characteristics of the quench These contaminants decrease the Using water as a quenchant Thermal Processing 2019年12月12日 Blast furnace slag, as bulk solid waste produced in the ironmaking process, will inevitably pollute the environment and occupy a large amount of land resources if it is not treated and utilized [1,2]The traditional water quenching method of blast furnace slag (BFS) will consume a lot of new water in the process, pollute the atmosphere by gases such as H 2 S and SO 2, Granulation Effect Analysis of Gas Quenching Blast Furnace Slag
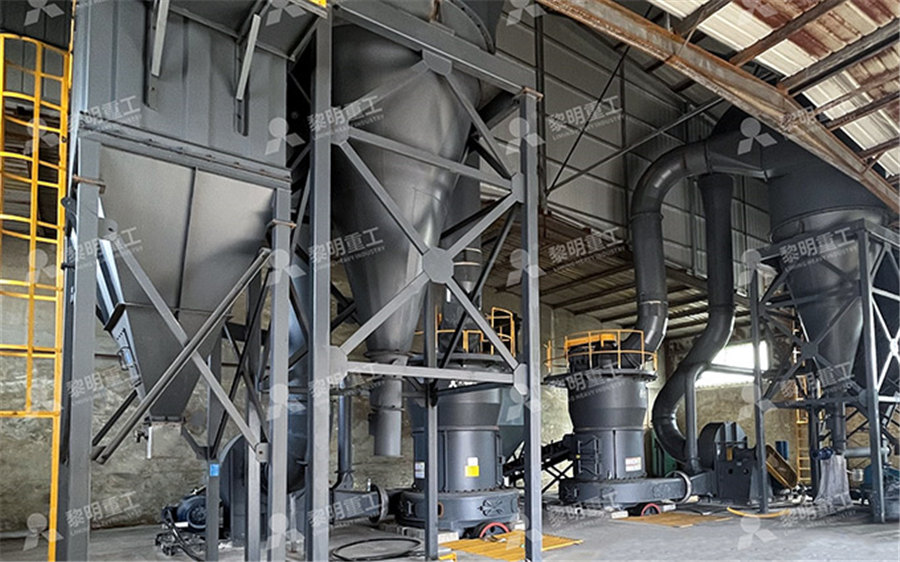
Treatment procedure of water quenching blast furnace slag
Water quenching blast furnace slag (WQBFS) is widely produced in the blast furnace iron making process It is mainly composed of CaO, MgO, Al2O3, and SiO2 with low contents of other metal elements Request PDF On Jul 1, 2016, Lei Deng and others published A Study on Waterquenching Waste Heat Recovery from Molten Slag of Slagtap Boilers Find, read and cite all the research you need on A Study on Waterquenching Waste Heat Recovery from Molten Slag of Slag pelletized blastfurnace slag, expanded slag ball and dry slag, have different function 3 WaterQuenching process So far, water treatment method is widely used in the cooling method of blast furnace slag There are many kinds of water treatment method for BF SLAG, such as Advection Sedimentation Tank, RASA, INBA, MTC, TYNA, and RASAA Review of Granulation Process for Blast Furnace Slag Semantic 2014年9月1日 Dry granulation, as a new process of molten blast furnace slag (BFS) treatment, is an attractive alternative to water quenching The performance of BFS obtained from dry granulation must be assessedExperimental investigation of glass content of blast furnace slag
.jpg)
Breaking boundaries in slag waste heat recovery: Review and
2024年11月1日 As the largest output of solid waste in the ISI, the production of blast furnace slag (BFS) by the blast furnace method exceeded 1279 billion tons with extremely high temperature of 1500–1600 ℃ based on the global iron production estimation in 2022 (Duan et al, 2024b)The slag contained total residual waste heat of 755×10 8 GJ, equivalent to 2777 The Experimental Study of the Strength Characteristics of Blast Furnace Water Quenching SlagHigh Sulfur Tailings Filling WANG Fulin1, a, WANG Zhongkang1,b, YANG Shijiao1,c*, TANG Zian2,d, LIU Jie1,e 1 Sc holf N uea rR esE ng ine ,U nv t yf Cna H a g 42 10 , a 2 Y iyang Cen tr alHosp ,ang, h na a wan gfl 209 @1 6, b anzh ngk m,c cute1088@sina om,The Experimental Study of the Strength Characteristics of Blast 2021年1月22日 The increasing focus on sustainability of Steel Industries worldwide has brought in new trends, viz maximizing utilization of assets and reduction of energy consumption and carbon footprint Coke dry quenching (CDQ) technology for recovery of waste heat from hot coke to generate process steam and power is well established and adopted worldwide that meets Design and Engineering Challenges for Installation of Coke Dry 2017年1月1日 In China, many technologies have been applied to improve the energy efficiency of the processes Among these technologies, the waste energy recovery technology, for example, CDQ (coke dry Waste Energy Recovery Technology of Iron and
.jpg)
INTRODUCTION OF CURRENT TECHNOLOGIES FOR COKE DRY QUENCHING
CDQ compared to the wet quenching method The reason is that the coke is cooled gradually with the cooling gas in CDQ chamber instead of quenching by sprinkling water And the watergas reaction is also avoided In particular, both 15 % improvement in mechanical strength (DI) 2016年5月20日 Dry quenched coke is harder and stronger, and its moisture content is much lower than that of wet quenched coke Furthermore, water is not wasted from the process and not contaminated with toxic pollutants In North America, dry quenching has been repeatedly rejected as unnecessary and costly In summary, the dry quenching of coke introduced in Dry Quenching: Clean Technology in Coke Production2024年3月28日 To promote the resource utilization of steel slag and improve the production process of steel slag in steelmaking plants, this research studied the characteristics of three different processed steel slags from four steelmaking plants The physical and mechanical characteristics and volume stability of steel slags were analyzed through density, water Research on the Properties of Steel Slag with Different MDPIratus, namely integrated dry quenching system, was designed, developed, and commissioned, which helps to replace the existing wet quenching used for carbonization tests Test results of this apparatus were compared with Carbolite make 250kgcapacity pilot coke oven 11 Description of the Integrated Dry Quenching SystemLaboratoryScale Integrated Coke Dry Quenching System for Coal
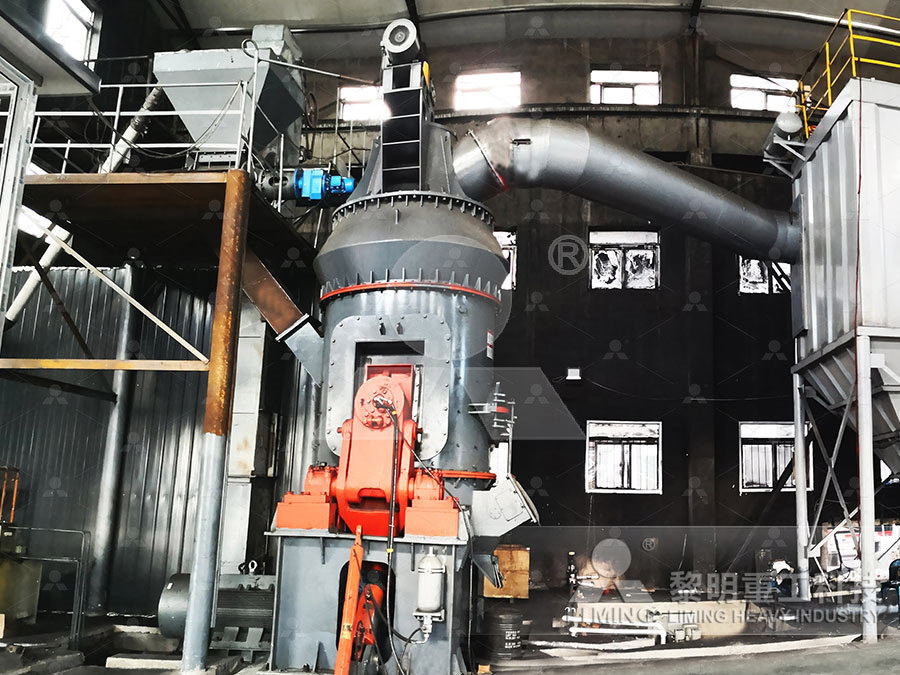
Numerical investigation of breakup process of molten blast furnace slag
2020年9月14日 Molten slag is broken up by supersonic air into droplets through the air quenching dry slag granulation technique The breakup process of blast furnace slag directly determines the droplet diameter and the waste heat recovery In order to gain deep insight into the granulation mechanism and visualize the breakup process, threedimensional unsteady 2014年2月19日 Slags are byproducts of the metallurgical industry It is of importance to recycle materials and recover heat from metallurgical slags to reduce the energy consumption and environmental impact of steel industry China is the largest iron and steelmaking slag producer in the world, and intensive efforts have been made during last decades for slag valorisation, Current Development of Slag Valorisation in ChinaProduct Name: GGBS Production Line / Slag Mill Capacity: 3,6000 – 1,000,000 T/Y Grinding Systems: VRM system, Ball mill open circuit system, Ball mill closed circuit system, Roller press final grinding systemGGBS Production Line Slag Mill for Slag Powder Grinding AGICO2024年4月15日 The test samples were taken from the lead slag produced by a smelter, which has a fine particle size The taken ore samples contain more water, cannot directly on the ore samples for mixing and scaling, so the lead slag in the clean ground to dry, and then use the roller crusher for breaking, crushing to −2 mm particle size bagging spareIron recovery from lead smelting waterquenching slag by
.jpg)
Dry Quenching an overview ScienceDirect Topics
Since its first introduction, coke dry quenching is being widely spread worldwide For example, in Japan, the number of dry quenching coking plants increased from six in the 1970s to 42 in the 2010s (Okazaki and Yamaguchi, 2011); China has 117 dry quenching plants, accounting for 80% of the coke production in the country (Huo et al, 2012)2021年11月3日 The technological factors required to improve the operational properties of granulated metallurgical slags demanded in the building industry have been analyzed In order to satisfy these factors, a new technology for hydrovacuum granulation of slag melts (HVG) has been developed It is shown that the main advantage of the proposed HVG process is the A new technological approach to the granulation of slag melts of Three types of BF slag quenching dry granulation process including drum granulation,air blast granulation ,which have been subjected to industrial test were introducedThe advantage and disadvantage of those processes were analyzedThe effects Dry slag granulation vs water quenching Hong Wang Junjun Wu Xun Zhu Q Liao Liang ZhaoAnalysis of Blast Furnace Slag Quenching Dry Granulation ProcessOur dry slag granulation technology involves pouring molten slag from above our rig down to a spinning disc That disc is spinning at high speed and it atomises the molten slag into small granules [Image changes to show molten slag being atomised and collected in the taurus]Dry slag granulation: producing valuable byproducts from waste
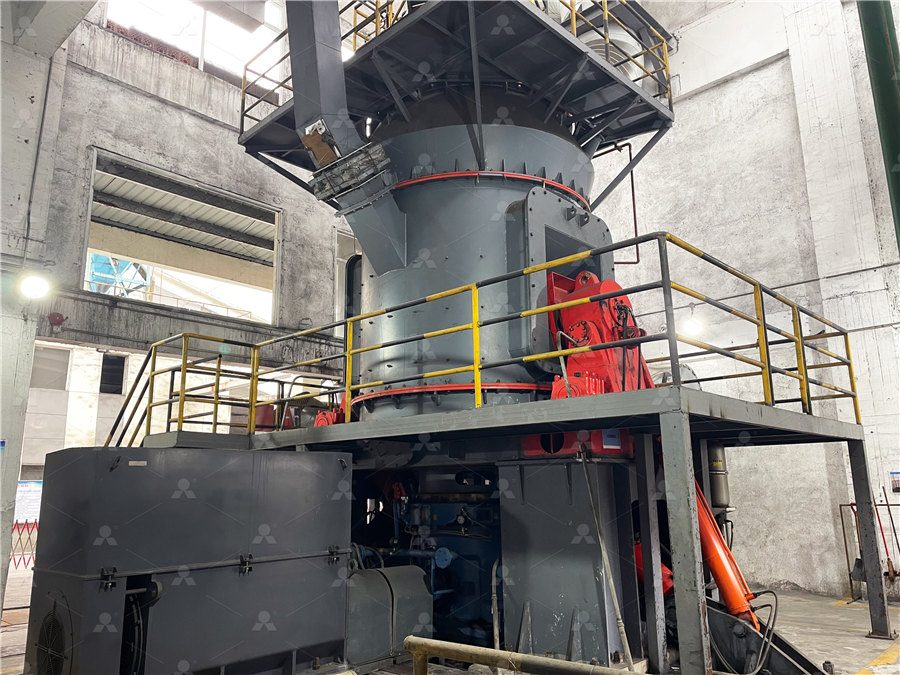
(PDF) RECENT DEVELOPMENTS IN DRY SLAG GRANULATION: A
2017年9月1日 Following different test series, where the slag quality and suitability for cement production was proven, Paul Wurth built a full scale dry slag granulation pilot plant at Rogesa's blast furnace No 4Smelting Slag Produced by Water Quenching* by Hojin RYUI, Kazumasa SUGIYAMA2 and Fumio SAITO 3 〔UDC 669551; 621745 58〕 The strength and grindability of copper smelting slag produced by water quenching have been investigated in the framework of single particle crushing and corrective grinding testsA Study on the Strength and Grindability of Granulated Copper Smelting 2016年6月1日 During water quenching process, highpressure water is employed to shatter the molten slag However, the water quenching methods not only fail to recover the hightemperature waste heat but also consume a huge amount of fresh water by the evaporation of 1000–1500 l of water per ton of slag [13]Energy–environment–economy evaluations of ScienceDirectballs The reaction between the ground slag and water, by which calcite is formed in the drying process, becomes active with the progress of grinding KEY WORDS: Grinding Aids, Dry Fine Grinding, Blast Furnace Slag, Xray Diffraction, Mechanochemical Effect, Ball Mill 1 Introduction Blast furnace slag is obtained as metallurgical waste producDry Fine Grinding of Granulated Blast Furnace Slag Quenched by Water
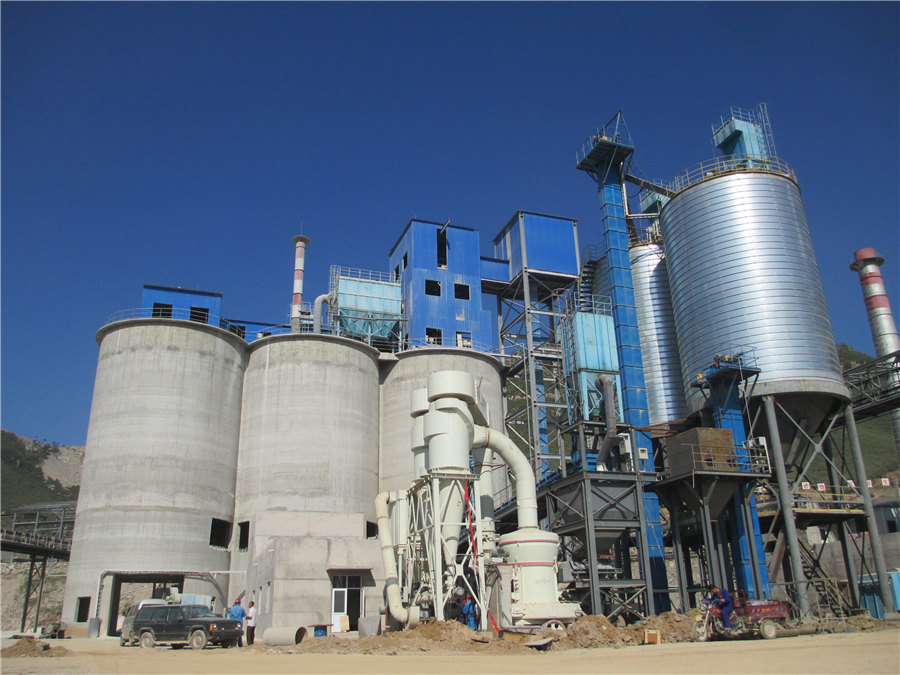
Slag Grinding Plant GGBS Plant Slag Mill, Slag Grinding Mill
5000tpd Dry Process Cement Plant Project In Liaoning; is obtained by quenching molten iron slag from a blast furnace in water or steam As the name implies, the GGBS plant is designed to process blast furnace vibrating feeder, slag mill, fan, powder collector, bag filter, etc 1 Crushing equipment The slag needs to be crushed into 2023年5月11日 To overcome the shortcomings of the water quenching technique, several dry granulation techniques have been proposed, such as rotating drums, centrifugal granulation, and gas quenching The gas quenching granulation process is noted to have lower water consumption, higher waste heat recovery efficiency, and be more environmentally friendly than Numerical Simulation of the Slag Granulation Process in Gas Quenching