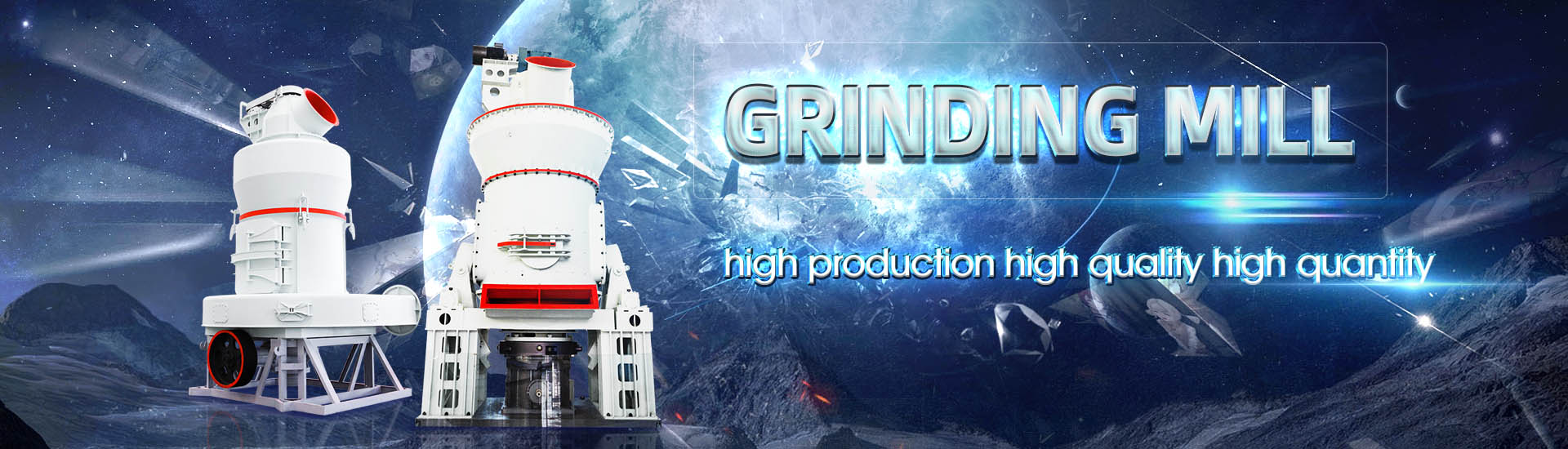
Cement plant raw material preparation process
.jpg)
Manufacture of Cement Materials and Manufacturing
Manufacturing of cement involves various raw materials and processes Each process is explained chemical reactions for manufacture of Portland Cement The most important raw materials for making cement are limestone, clay and marl These are extracted from quarries by blasting or by ripping using heavy machinery Wheel loaders and From raw materials Extracting raw materials Raw material While each cement plant may differ in layout, equipment, and appearance, the general process of manufacturing portland cement is the same: crushed limestone and sand are mixed with ground clay, shale, iron ore, fly ash and How Cement is Made Portland Cement AssociationThe preparation of cement involves mining; crushing, and grinding of raw materials (princi pally limestone and clay); calcining the materi als in a rotary kiln; cooling the resulting clinker; Cement Manufacturing International Finance Corporation
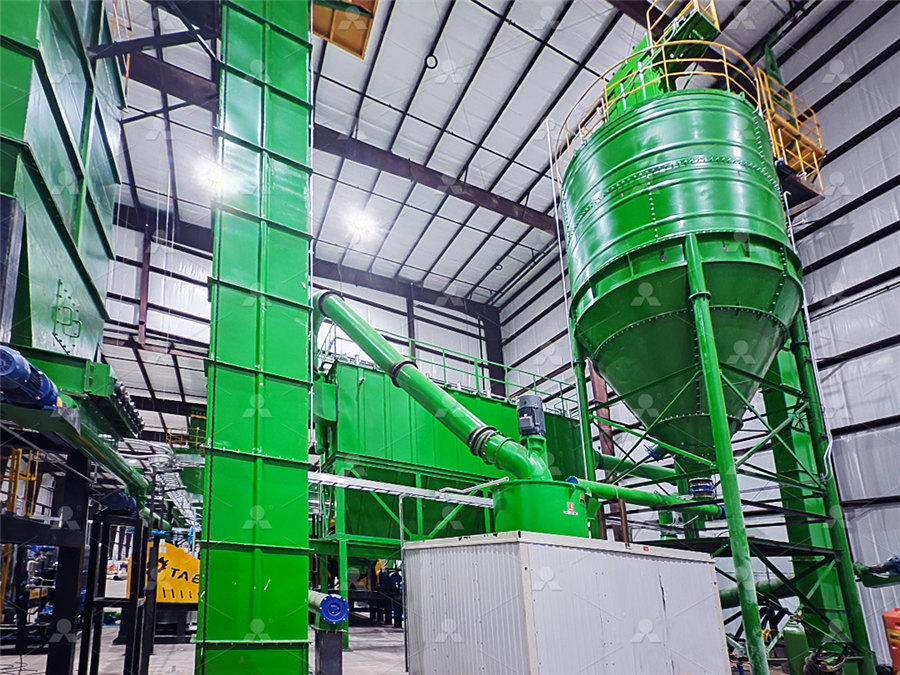
116 Portland Cement Manufacturing US EPA
1971年8月17日 The initial production step in portland cement manufacturing is raw materials acquisition Calcium, the element of highest concentration in portland cement, is obtained from 2015年12月9日 materials by a combination of chemical processes known collectively as setting Cements are dry can be characterized as being either hydraulic or nonhydraulic resulting cement will have the(PDF) Cement Manufacturing ResearchGateProviding a comprehensive guide to the entire cement production process from raw material extraction to the finished product, the industry’s favourite technical reference book is now fully The Cement Plant Operations Handbook International Cement together in a raw mill to a particle size of 90 micrometres, producing “kiln feed” Cement Plant: The Manufacturing Process worldcementassociation 1 Limestone (CaCO3) is taken from a Cement Plant: The Manufacturing Process 4 5 World Cement
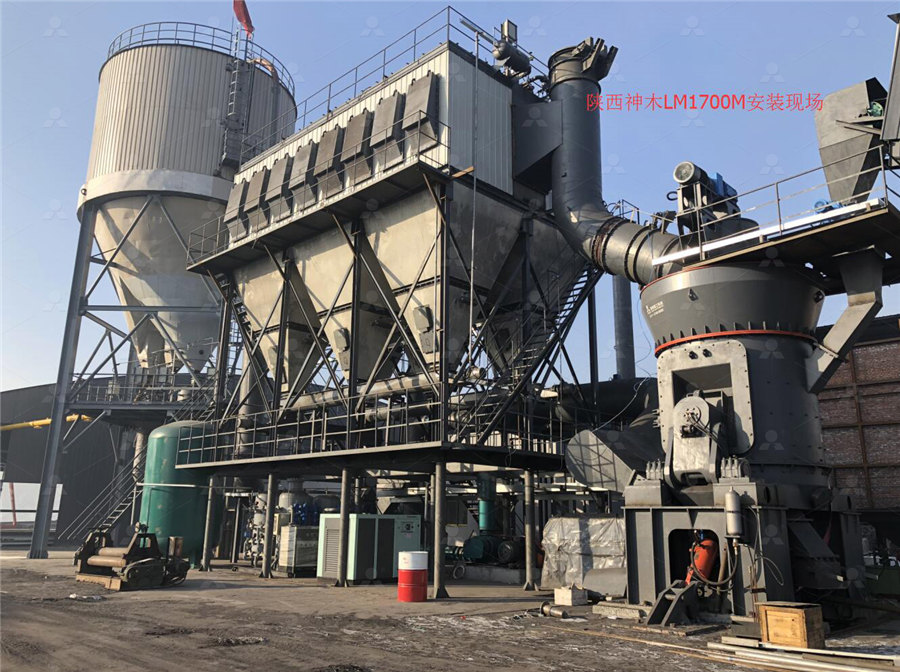
Cement Production Process Cement Manufacturing
2020年8月25日 Feeding raw meal into cement kiln to make clinker, the clinker, and some mixed materials will be ground together by cement grinding plant, the finished cement will be done Cement raw material preparation: Limestone is The cyclone preheating system Phase IV: Calcination The calcination is the core phase of the cement making dry process The calcination of the preheated raw meal takes place in the rotary kiln of the cement plant The rotary kiln is a How Is Cement Produced in Cement Plants Cement Raw material preparation / raw mix preparation Crushing Homogenization Proportioning of raw materials Grinding Storing and Blending Burning of raw mix Clinker grinding along with gypsum – Cement Grinding Storing PackingKnow All About Cement Manufacturing Process in India mycem cementMaintenance – 17 Process – 18 Materials analysis –19 Plant capacity summary – 20 Storage capacity 15 Cement plant construction and valuation 244 1 New plant construction – 2 Project management – 3 Cement plant investment costs – 4 Project phases – 5 Plant valuation Section B – Process calculations and miscellaneous The Cement Plant Operations Handbook International Cement
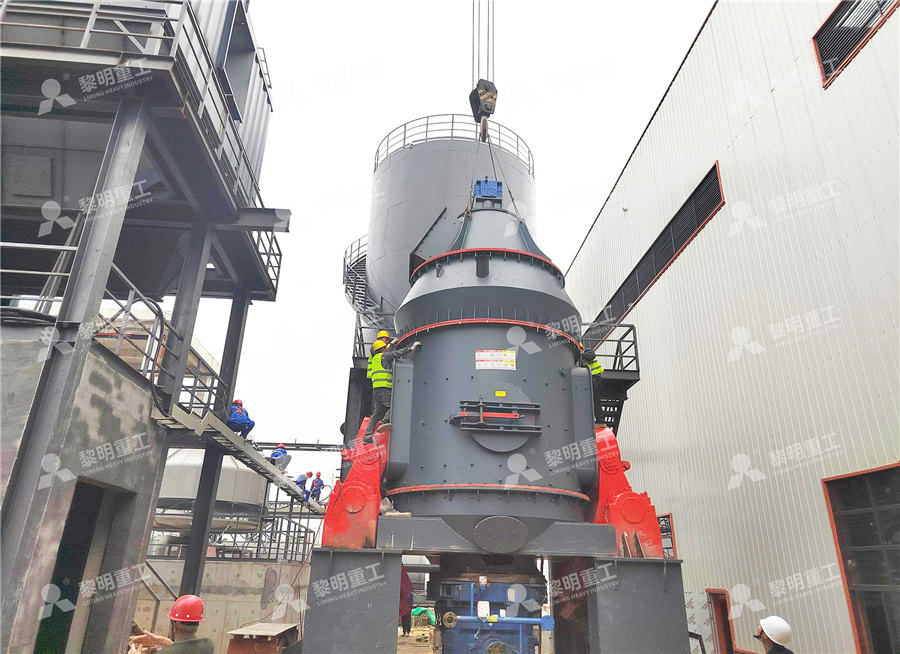
Cement Manufacturing Process and Its Environmental Impact
2023年7月10日 The cement manufacturing process involves the extraction and processing of raw materials, such as limestone, clay, and shale, which are then heated in a kiln at high temperatures to form clinkerCement manufacturing process components of a cement plant from quarry to kiln to cement mill Understanding Cement Interpreting Cement Science Since 2005 Menu Home; Cement Blog; Article Directory; This blended raw material is called the 'raw feed' or 'kiln feed' and is heated in a rotary kiln where it reaches a temperature of about Cement manufacturing components of a cement plant Understanding CementThe process route for raw materials preparation is multistage and complex It generally consists of such steps as: • Crushing (one, two or threestage) Figure 232 A primary jaw crusher used in crushing limestone rock at a cement plant quarry Jaw CrushersEverything you need to know about cement Materials Preparation and Raw Lime Component Limestone: Common forms of calcium carbonate used as raw material for cement manufacturing are limestone and chalkLimestone is of predominantly fine grained crystalline structure, its hardness is between 18 to 30 of the Mohs scale of hardness and specific gravity 2 To 28 Limestone usually contains admixtures of clay substance or iron compounds, Raw materials for cement manufacturing Cement Plant
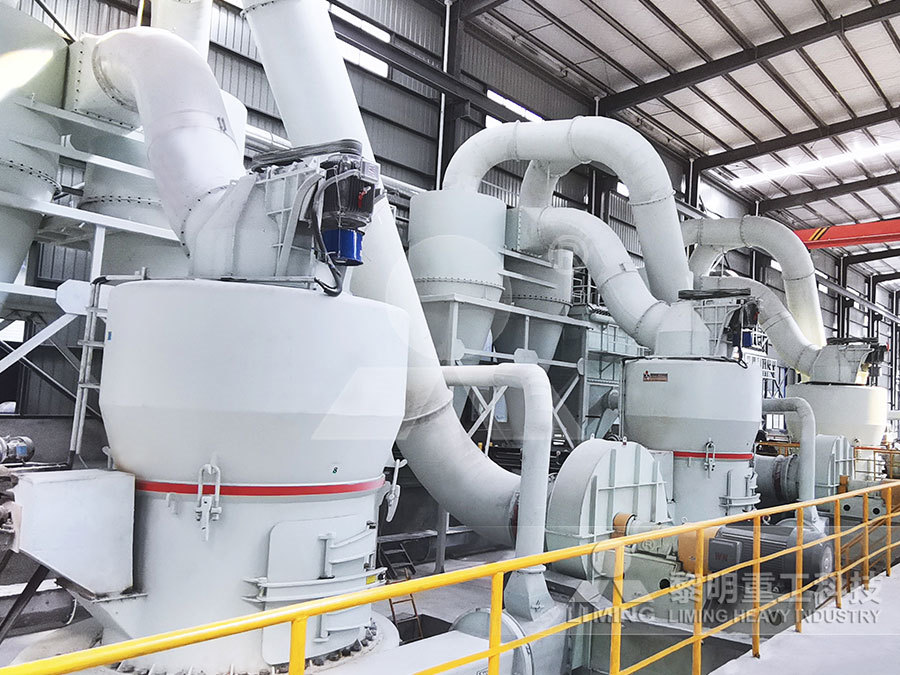
Raw material preparation From the quarry to raw meal
2 Futureoriented raw material preparation solutions made by Polysius: Innovative – Individual – Ideal The manufacturing of cement begins with the extraction and preparation of raw material – a process covering the stages from raw material quarrying to feeding the raw meal into the preheater The purpose of optimum raw material 2012年8月30日 Cement Manufacturing Process Phase 1: Raw Material Extraction Cement uses raw materials that cover calcium, silicon, iron and aluminum Such raw materials are limestone, clay and sand Limestone is for calcium It is combined with much smaller proportions of sand and clay Sand clay fulfill the need of silicon, iron and aluminumCement Manufacturing Process Engineering IntroThe production of raw cement involves the extraction and procurement of raw materials like limestone and clay or iron ore These materials are then crushed and finely ground to form the raw mix The raw mix is then subjected to high Explore Raw Material Used For Cement ProductionTake a look at our interactive animation of the cement production process to learn how cement is made by us at CEMEX Products Services Mining the raw material employed 2 Transporting the raw material Once the huge rocks have been fragmented, they are transported to the plant in dump trucks or by conveyor belt 3Cement Production: How Cement Is Manufactured CEMEX UK
.jpg)
Raw Material Preparation an overview ScienceDirect Topics
Cement and Energy Ernst Worrell, in Encyclopedia of Energy, 2004 32 Kiln Feed Preparation Raw material preparation is an electricityintensive production step generally requiring approximately 25–35 kWh/tonne raw material, although it can require as little as 11 kWh/tonne The raw materials are further processed and ground The grinding differs with the 2018年8月28日 CEMENT MANUFACTURING PROCESS PHASE 1: RAW MATERIAL EXTRACTION Cement uses raw materials that cover calcium, silicon, iron and aluminum Such raw materials are limestone, clay and sand Limestone is for calcium It is combined with much smaller proportions of sand and clay Sand clay fulfill the need of silicon, iron and aluminum Cement Manufacturing Process The Engineering CommunityMini Cement Plant Hot Sale; Cement Plant 700 ~ 2000tpd; Cement Plant 2500~7000tpd; What Is Cement Raw Meal Cement raw meal is the raw material for producing cement clinker, The raw meal preparation process of the cement industry includes four links: mining, prehomogenization, Cement Raw Meal Homogenization Process in The Cement † Raw materials preparation † Fuel Preparation † Clinker Manufacturing Process † Cement grinding † Cement dispatch All these steps are described in detail in the next sections 421 Quarrying The major raw material used in cement manufacture is lime It is derived fromCement Manufacturing—Technology, Practice, and Development
.jpg)
The cement raw material blending process and its control system
Raw material blending is an important process affecting cement quality The aim of this process is to mix a variety of materials such as limestone, shale (clay), sandstone and iron to produce 2015年8月1日 The results show that approximately 248t, 469t, and 341t of materials are required to produce a ton of the product in raw material preparation, clinker production, and cement grinding stages Analysis of material flow and consumption in cement production processA Dry Process Kiln 06 B Raw material unloading 07 C Raw material piles 08 D Primary crushing 09 E Secondary crushing 10 F Screening 11 G Raw material transfer 12 H Raw material grinding/drying 13 I Clinker cooler 14 J Clinker piles 15 K Clinker transfer 16 L Clinker grinding 17 M Cement silos 18116 Portland Cement Manufacturing US Environmental The cement manufacturing process starts from the mining of raw materials that are used in cement manufacturing, mainly limestone and clays A limestone quarry is inside the plant area and a clays quarry is as far from the plant area as 25 kmManufacturing process Lafarge
.jpg)
Cement Manufacturing Process: Know Extraction,
2024年9月10日 Steps of Cement Manufacturing The steps involved in cement manufacturing are as follows: Quarrying: Raw materials such as limestone and clay are extracted from quarries or mines; Crushing and Grinding: The 1 天前 The manufacture of Portland cement is a complex process and done in the following steps: grinding the raw materials, mixing them in certain proportions depending upon their purity and composition, and burning them to sintering in Manufacturing of Portland Cement – Process and Materials Preparation Technology The crusher should therefore, in an effective time of 35 to 45 hours, be able to produce sufficient raw material to feed the kiln plant for a whole (7 However, its use for cement raw materials is advantageous only under very special conditionsEverything you need to know about Crushers in Cement industry2023年12月20日 Cement manufacturing is a complex process that begins with mining and then grinding raw materials that include limestone and clay, to a fine powder, called raw meal, which is then heated to a sintering temperature as high as 1450 °C in a cement kiln In this process, the chemical bonds of the raw materials are broken down and then they are The Cement Manufacturing Process Thermo Fisher Scientific
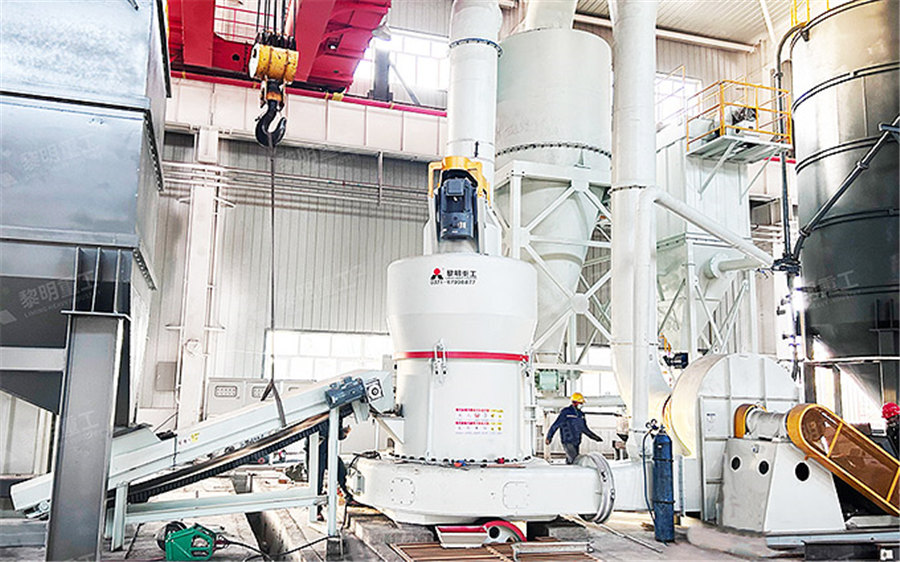
Understanding the Raw Materials for Manufacturing Cement
2024年8月20日 Raw Materials Used in the Manufacturing of Cement The preparation of cement using the raw materials involves the following process: Step 1: MiningThe extraction of raw materials such as limestone and clay from mines and quarries Step 2: Grinding processThese raw materials are grinded and crushed into a fine powderlike form This is called Raw meal grinding is a vital link in the cement raw material preparation process After the cement raw material is crushed, it will be sent into the raw mill for further grinding until a certain degree of fineness is reached, and then enter the clinker calcination processRaw Mill – Raw Mill In Cement Plant AGICO Cement Raw Mill2019年9月27日 Cement manufacturing process In general, we can divide the cement production line into three main steps: raw material preparation of cement, clinker production, and cement grinding Each step has some cement manufacturing machines, such as raw mill, cement crusher, cement mill, cement kiln, cement cooler, cement dryer, cement silo, cement Cement Euipment Overview Cement Making Machines Cement Plant1971年8月17日 116 Portland Cement Manufacturing 1161 Process Description17 Portland cement is a fine powder, gray or white in color, that consists of a mixture of hydraulic cement materials comprising primarily calcium silicates, aluminates and aluminoferrites More than 30 raw materials are known to be used in the manufacture of portland cement, and these116 Portland Cement Manufacturing US EPA
.jpg)
Cement manufacturing raw materials Understanding Cement
If you happen to be a geologist, the raw materials quarry is probably the most interesting part of a cement works, maybe unless you view the clinkering process as igneous rocks in the making The most common raw rock types used in cement production are: Limestone (supplies the bulk of 2015年12月9日 Raw materials are used to produce the main cement elements (Mohsen, 2015) • Quarry The process of obtaining raw materials for cement manufacturing involves mining and quarrying natural materials (PDF) Cement Manufacturing ResearchGate2020年8月25日 Feeding raw meal into cement kiln to make clinker, the clinker, and some mixed materials will be ground together by cement grinding plant, the finished cement will be done Cement raw material preparation: Limestone is Cement Production Process Cement Manufacturing The cyclone preheating system Phase IV: Calcination The calcination is the core phase of the cement making dry process The calcination of the preheated raw meal takes place in the rotary kiln of the cement plant The rotary kiln is a How Is Cement Produced in Cement Plants Cement
.jpg)
Know All About Cement Manufacturing Process in India mycem cement
Raw material preparation / raw mix preparation Crushing Homogenization Proportioning of raw materials Grinding Storing and Blending Burning of raw mix Clinker grinding along with gypsum – Cement Grinding Storing PackingMaintenance – 17 Process – 18 Materials analysis –19 Plant capacity summary – 20 Storage capacity 15 Cement plant construction and valuation 244 1 New plant construction – 2 Project management – 3 Cement plant investment costs – 4 Project phases – 5 Plant valuation Section B – Process calculations and miscellaneous The Cement Plant Operations Handbook International Cement 2023年7月10日 The cement manufacturing process involves the extraction and processing of raw materials, such as limestone, clay, and shale, which are then heated in a kiln at high temperatures to form clinkerCement Manufacturing Process and Its Environmental ImpactCement manufacturing process components of a cement plant from quarry to kiln to cement mill Understanding Cement Interpreting Cement Science Since 2005 Menu Home; Cement Blog; Article Directory; This blended raw material is called the 'raw feed' or 'kiln feed' and is heated in a rotary kiln where it reaches a temperature of about Cement manufacturing components of a cement plant Understanding Cement
.jpg)
Everything you need to know about cement Materials Preparation and Raw
The process route for raw materials preparation is multistage and complex It generally consists of such steps as: • Crushing (one, two or threestage) Figure 232 A primary jaw crusher used in crushing limestone rock at a cement plant quarry Jaw CrushersLime Component Limestone: Common forms of calcium carbonate used as raw material for cement manufacturing are limestone and chalkLimestone is of predominantly fine grained crystalline structure, its hardness is between 18 to 30 of the Mohs scale of hardness and specific gravity 2 To 28 Limestone usually contains admixtures of clay substance or iron compounds, Raw materials for cement manufacturing Cement Plant 2 Futureoriented raw material preparation solutions made by Polysius: Innovative – Individual – Ideal The manufacturing of cement begins with the extraction and preparation of raw material – a process covering the stages from raw material quarrying to feeding the raw meal into the preheater The purpose of optimum raw material Raw material preparation From the quarry to raw meal2012年8月30日 Cement Manufacturing Process Phase 1: Raw Material Extraction Cement uses raw materials that cover calcium, silicon, iron and aluminum Such raw materials are limestone, clay and sand Limestone is for calcium It is combined with much smaller proportions of sand and clay Sand clay fulfill the need of silicon, iron and aluminumCement Manufacturing Process Engineering Intro