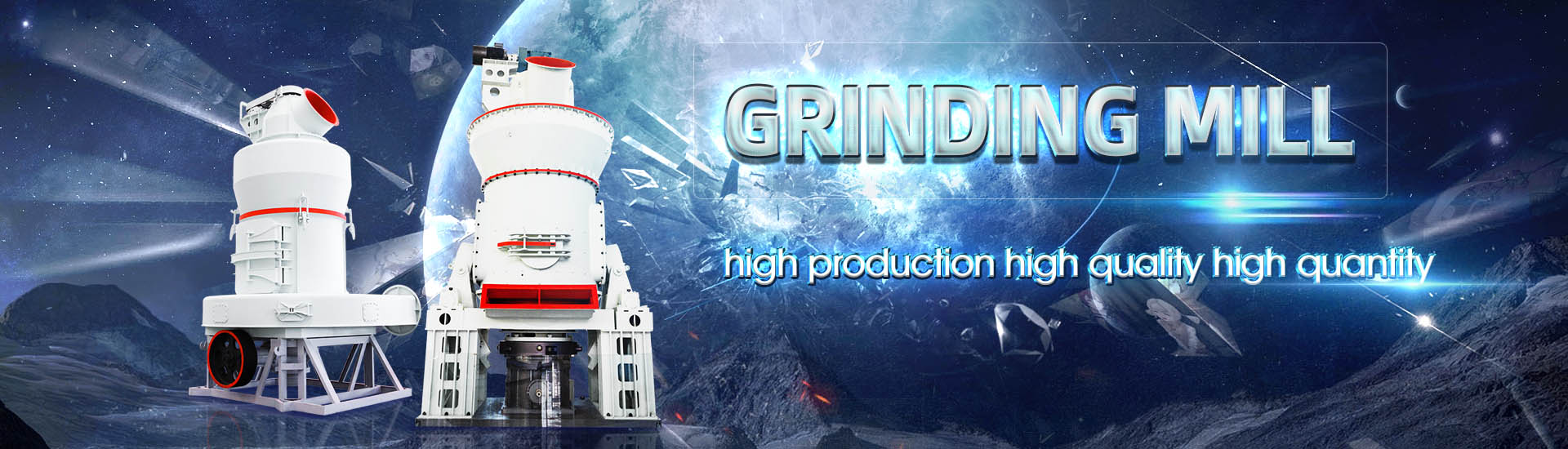
HOME→Wet Limestone Desulfurization Technology for Thermal Power Plants Wet Limestone Desulfurization Technology for Thermal Power Plants Wet Limestone Desulfurization Technology for Thermal Power Plants
Wet Limestone Desulfurization Technology for Thermal Power Plants Wet Limestone Desulfurization Technology for Thermal Power Plants Wet Limestone Desulfurization Technology for Thermal Power Plants
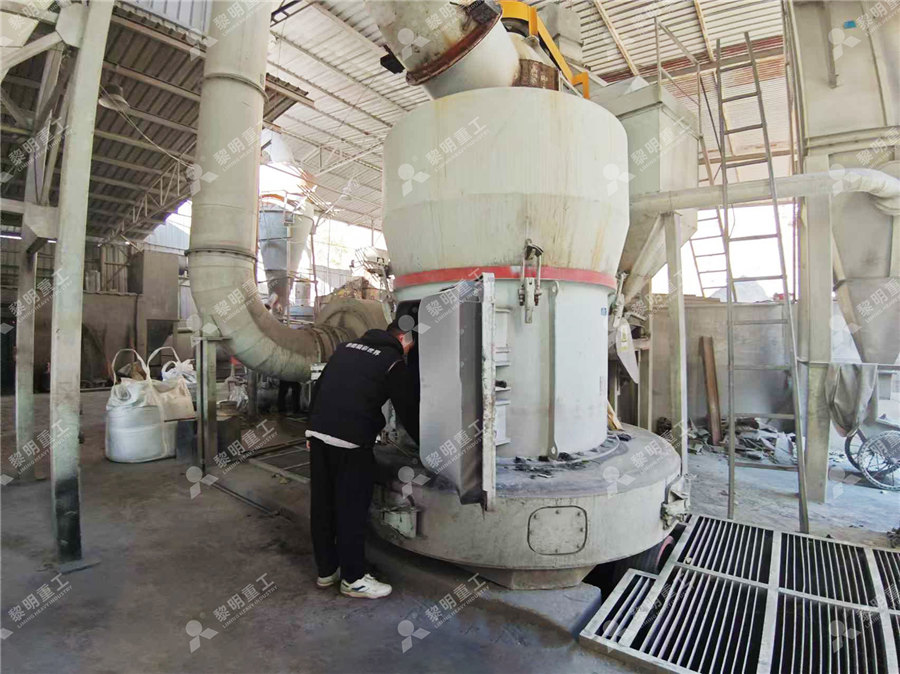
Status of Flue Gas Desulphurisation (FGD) systems from coalfired
2015年3月15日 This paper presents a general review of the Flue Gas Desulphurisation (FGD) technologies used to abate sulphur emissions from coalfired power plants, and exposes the 2008年11月1日 In this paper, a model of limestone/gypsum wet flue gas desulfurization (WFGD) system was developed based on unsteady theory The models of processes of absorption A model for performance optimization of wet flue gas 2015年3月1日 Circulating fluidized bed (CFB) boilers with wet flue gas desulfurization (WFGD) system is a popular technology for SO2 removal in the coalfired thermal power plantStatus of Flue Gas Desulphurisation (FGD) systems from coalfired 2019年3月13日 Most coalfired power plants in China use wet flue gas desulfurization (WFGD) as the main method for SO 2 removal Presently, the operating of WFGD lacks accurate modeling method to predict outlet Full article: Modeling and optimization of wet flue gas
.jpg)
Model of the Wet Limestone Flue Gas Desulfurization Process for
2001年5月19日 A detailed process model of the wet limestone flue gas desulfurization system has been presented This model can be used to calculate indispensable parameters for 2021年2月1日 In this paper, chemical precipitation process is used for the treatment of the desulfurization wastewater generated by the waste gas treatment system of the limestone LimestoneGypsum Wet Flue Gas Desulfurization Wastewater 2022年5月15日 Among the power plants having FGD units installed worldwide, approximately 80 to 85% of them use wet limestone as opposed to other technologies FGD technology Limestone supplier selection for coal thermal power plant by 2019年7月22日 Limestone–gypsum wet desulfurization technology is an effective flue gas desulfurization technology (Yan et al 2017), and it is commonly used in coalfired power Evaporation and concentration of desulfurization wastewater with
.jpg)
Mitsubishi Power Flue Gas Desulfurization (FGD) Plants
Max Capacity 1,050 MW Max Inlet SO 2 Concentration 80,000 mg/Nm 3 (Coal fired) Max SO 2 Removal Efficiency 99% High Reliability The flue gas desulfurization (FGD) plant removes sulfur dioxides (SO 2) from flue gas produced by boilers, furnaces, and other sourcesMitsubishi Power effectively contributes to the prevention of air pollution through its wet limestone 2024年3月20日 Desulfurization wastewater is industrial wastewater with a high salt content, high metal ions, and high hardness produced by flue gas desulfurization of the limestonegypsum method in coalfired power plants Current Status of Zero Liquid Discharge Technology 2001年5月19日 Wet Flue Gas Desulfurization (WFGD) unit based upon spray scrubber has been widely employed to control SO2 emissions from flue gas in coalfired power plantModel of the Wet Limestone Flue Gas DesulfurizationPDF On Jan 1, 2016, YunYang Wang published Zero Discharge of wastewater Treatment Technology of Wet Desulfurization in Coalfired Power Plants Find, read and cite all the research you need on Zero Discharge of wastewater Treatment Technology of Wet
.jpg)
Wet Flue Gas Desulfurization (FGD) ARCOR Epoxy
In most developed countries, wet scrubber (fluegas desulfurization; FGD) technology is a wellestablished process for removing SO 2 Also, costs have been reduced significantly from 150200 $/KW in the 1980s to 70150 $/kW in the late 1990s Wet FGD Technology A simplified process flow diagram of a conventional wet scrubber is shown in the figure2014年8月1日 In wet limestone gypsum Flue Gas Desulfurizers, flue gas is washed with CaCO3–water slurry on the wet walls of a vertical absorption tower, where SO2 and O2 are absorbed to form CaSO3 and CaSO4Features of Use of Limestone and Lime in Wet Desulphurisation Technology2015年10月30日 A Review of Desulfurization Technology using Limestone in Circulating Fluidized Bed Boiler Type Power Plant October 2015 Journal of the Korean Institute of Resources Recycling 24(5):314(PDF) A Review of Desulfurization Technology using Limestone in 2017年1月1日 Synthetic gypsum CaSO42H2O (also called flue gas desulpurizationFGD gypsum) is a coproduct resulted from the wet process of flue gas desulphurisation in thermal power plants(PDF) Study on synthetic gypsum obtained from wet flue gas

STANDARD TECHNICAL SPECIFICATION FOR RETROFIT OF WET LIMESTONE
Retrofit of Wet Limestone Based FGD System in a Typical 2 x 500 MW Coal Based Thermal Power Plant” with valuable inputs from the committee members This document can be used for installation of FGD system in a new thermal power plant also The document reflects pooledWet limestone scrubbing has high capital and operati ng cost due to the handling of liquid reagent and waste Nonetheless, it is the preferred process for coalfired electric utility power plants burning coal due to the low cost of limestone and SO 2 control efficiencies from 90% up to 98% (Schnelle, 2002) SemiDry SystemsAir Pollution Control Technology Fact Sheet US EPA2021年11月1日 Flue gas desulfurized gypsum mainly comes from thermal power plants, smelters, and largeenterprise boilers, and contains industrial byproducts produced through a wet desulfurization combustion process, where SO 2 gas and lime slurry react under strong oxidation conditions The main component of this gypsum is calcium sulfate dihydrate, which also Production and resource utilization of flue gas desulfurized 2008年11月1日 The limestonegypsum wet flue gas desulfurization is the most widely used technology for SO2 removal in coalfired power plants due to its high efficiency, reliability, and costeffectiveness [29]A model for performance optimization of wet flue gas desulfurization
.jpg)
A model for performance optimization of wet flue gas desulfurization
DOI: 101016/JFUPROC200804004 Corpus ID: ; A model for performance optimization of wet flue gas desulfurization systems of power plants @article{Zhong2008AMF, title={A model for performance optimization of wet flue gas desulfurization systems of power plants}, author={YiJun Zhong and Xiang Gao and Wangtu Huo and Zhongyang Luo and 2021年2月1日 In this paper, chemical precipitation process is used for the treatment of the desulfurization wastewater generated by the waste gas treatment system of the limestonegypsum flue gas desulfurization process of a thermal power plant After one year of operation, the technology is reliable and stableLimestoneGypsum Wet Flue Gas Desulfurization Wastewater 2020年11月19日 In early 2019, Power Engineering published a report on a chemistry that can significantly enhance limestone reactivity and sulfur dioxide (SO2) removal in wet flue gas desulfurization (WFGD Wetlimestone scrubber enhancement chemistry improves heat In thermal power industry of the developed countries, the plants for the wet desulphurization most often use limestone or lime as a sorbent with gypsum obtaining First wet lime desulfurization plants was used the lime as a chemically active substance At the present time, are increasingly used as a sorbent limestone as a widespread mineralFeatures of Use of Limestone and Lime in Wet Desulphurisation Technology
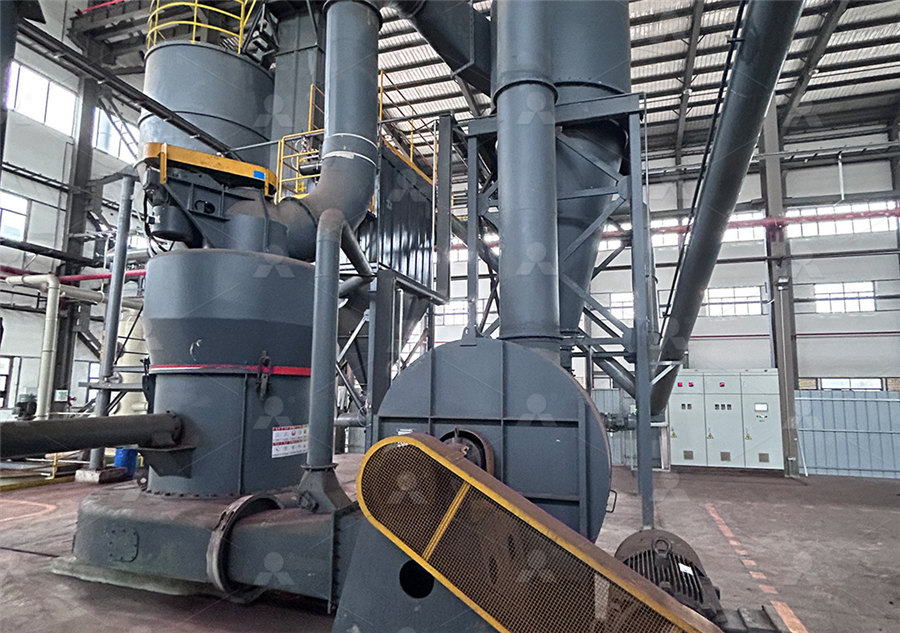
Summary of research progress on industrial flue gas desulfurization
2022年1月15日 Wet desulfurization technology includes limestonegypsum desulfurization, dualalkali desulfurization, magnesium oxide desulfurization, zinc oxide Prospects Based on the study of dry desulfurization, semidry desulfurization, and wet desulfurization, the research progress of various desulfurization processes, mass transfer mechanisms and process parameters are Types of FGD Systems for Thermal Power Plants Wet FGD Systems Wet FGD systems are the most common type used in thermal power plants They use a liquid absorbent, typically a limestone slurry, to remove SO2 from the flue gas High Efficiency: Wet FGD systems can achieve SO2 removal efficiencies of up to 95%Flue Gas Desulfurization in Thermal Power Plants by AcmefilLimestone preparation system in flue gas desulfurization (FGD) consists of following subsystems: 1 Limestone Handling System Limestone will be delivered to the limestone storage shed by truck Limestone will be delivered from the limestone unloading hopper to the limestone day silo by limestone transfer conveyor and bucket elevator 2Flue Gas Desulfurization (FGD) Working Thermal Power Plant2002年4月1日 The magnesium ion concentration was the input parameter of this calculation formula Warych et al [43, 44] established a model of the thermal power plant flue gas desulfurization process based on Optimum Values of Process Parameters of the “Wet Limestone
.jpg)
Evaporation and concentration of desulfurization wastewater with
2019年7月22日 Limestone–gypsum wet desulfurization technology is an effective flue gas desulfurization technology (Yan et al 2017), and it is commonly used in coalfired power plants because of its high maturity and stable operation (Bogacki et al 2018, Zheng et al 2019)A desulfurization system replenishes process water regularly and discharges desulfurization 2019年1月1日 Introduces the test applying desulfurization catalyst in WFGD (wet flue gas desulfurization) system of 320MW generating units operating in thermal power plant Desulfurization efficiency is Research Progress of Desulfurization Wastewater A new wet limestone−gypsum process for flue gas desulfurization (FGD) has been developed The main difference compared to a conventional wet FGD process is the ability of the new process to A comparison between limestone grinding systems of the wet 2001年5月19日 A detailed process model of the wet limestone flue gas desulfurization system has been presented This model can be used to calculate indispensable parameters for estimating costs and next to minimize capital and operating costs The process model describes most important stage of SO2 removal running in an absorber and a holding tank It includes Model of the Wet Limestone Flue Gas Desulfurization Process
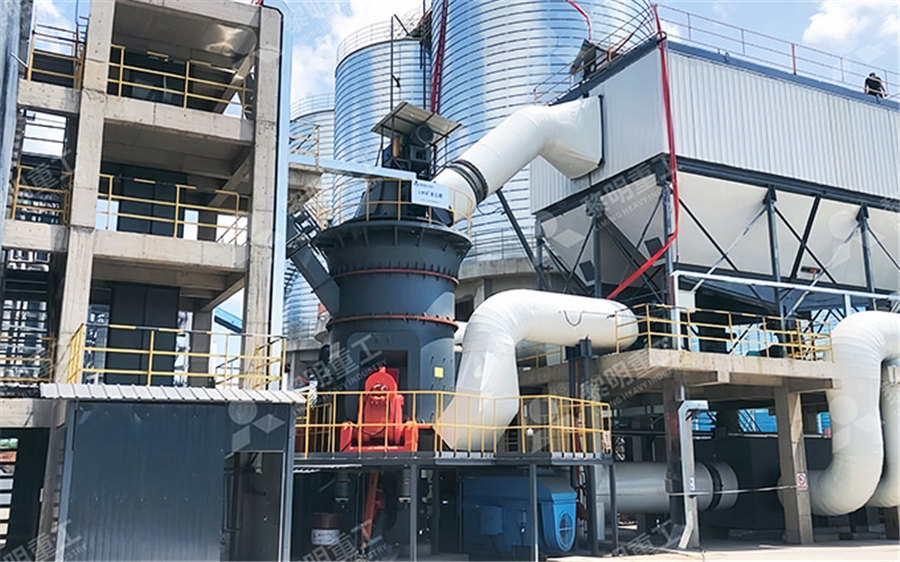
Study on Operation Optimization and Control Model for Desulfurization
June 2017; Reneng Dongli Gongcheng/Journal of Engineering for Thermal Energy and Power 32(6):95年3月15日 The limestone scrubbing process is a commercialized technology for desulfurization in largescale thermal power plants In this process, SO 2 in the exhaust gas is removed via absorption in the alkaline limestone slurry, and gypsum is obtained as a byproduct [5] , Desulfurization characteristics of limestone slurry with added Before flue gas desulfurization was installed, the emissions from the Four Corners Generating Station in New Mexico contained a significant amount of sulfur dioxide The G G Allen Steam Station scrubber (North Carolina) Fluegas desulfurization (FGD) is a set of technologies used to remove sulfur dioxide (SO 2) from exhaust flue gases of fossilfuel power plants, and from the Fluegas desulfurization Wikipediaplants, but also it can damage the ecological environment SO 2 is the main precursor for acid rain The limestone gypsum wet desulfurization process is a common way to achieve flue gas desulfurization, which has been used for Chinese coalfired power plants [1–3] In order to guarantee the stability of the desulfurization system and the qualityAdvanced treatment technology for FGD wastewater in coalfired power
.jpg)
Water Consumption Management for Thermal Power Plant
2020年2月18日 Based on the notification issued by MoEF, all the existing thermal power plants are expected to reduce specific water consumption up to 35 m 3 /MWH (Mishra et al in Paper on water resource management for 2 × 660 MW coalbased power plant and comparatives for wet and dry cooling system, New Delhi, India, 2016)2022年5月15日 The flue gas desulfurization (FGD) process eliminates Sulphur dioxides from flue gas produced by the combustion of fossil fuels in furnaces, boilers, and other sources Limestone is an essential element for the FGD process in coalfired thermal power plants FGD system contributes efficaciously to the prevention of air pollution through its limestone/gypsum Limestone supplier selection for coal thermal power plant by Max Capacity 1,050 MW Max Inlet SO 2 Concentration 80,000 mg/Nm 3 (Coal fired) Max SO 2 Removal Efficiency 99% High Reliability The flue gas desulfurization (FGD) plant removes sulfur dioxides (SO 2) from flue gas produced by boilers, furnaces, and other sourcesMitsubishi Power effectively contributes to the prevention of air pollution through its wet limestone Mitsubishi Power Flue Gas Desulfurization (FGD) Plants2024年3月20日 Desulfurization wastewater is industrial wastewater with a high salt content, high metal ions, and high hardness produced by flue gas desulfurization of the limestonegypsum method in coalfired power plants Current Status of Zero Liquid Discharge Technology
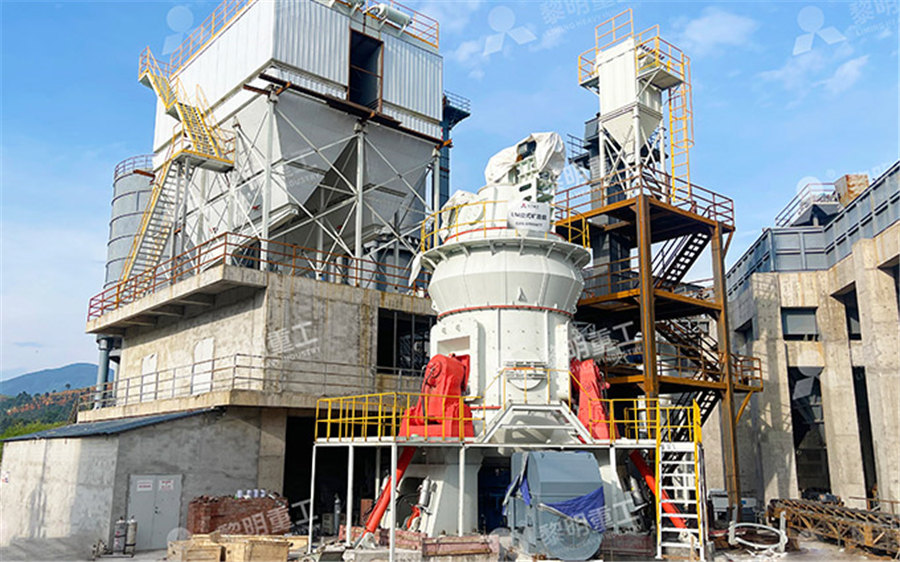
Model of the Wet Limestone Flue Gas Desulfurization
2001年5月19日 Wet Flue Gas Desulfurization (WFGD) unit based upon spray scrubber has been widely employed to control SO2 emissions from flue gas in coalfired power plantPDF On Jan 1, 2016, YunYang Wang published Zero Discharge of wastewater Treatment Technology of Wet Desulfurization in Coalfired Power Plants Find, read and cite all the research you need on Zero Discharge of wastewater Treatment Technology of Wet In most developed countries, wet scrubber (fluegas desulfurization; FGD) technology is a wellestablished process for removing SO 2 Also, costs have been reduced significantly from 150200 $/KW in the 1980s to 70150 $/kW in the late 1990s Wet FGD Technology A simplified process flow diagram of a conventional wet scrubber is shown in the figureWet Flue Gas Desulfurization (FGD) ARCOR Epoxy2014年8月1日 In wet limestone gypsum Flue Gas Desulfurizers, flue gas is washed with CaCO3–water slurry on the wet walls of a vertical absorption tower, where SO2 and O2 are absorbed to form CaSO3 and CaSO4Features of Use of Limestone and Lime in Wet Desulphurisation Technology
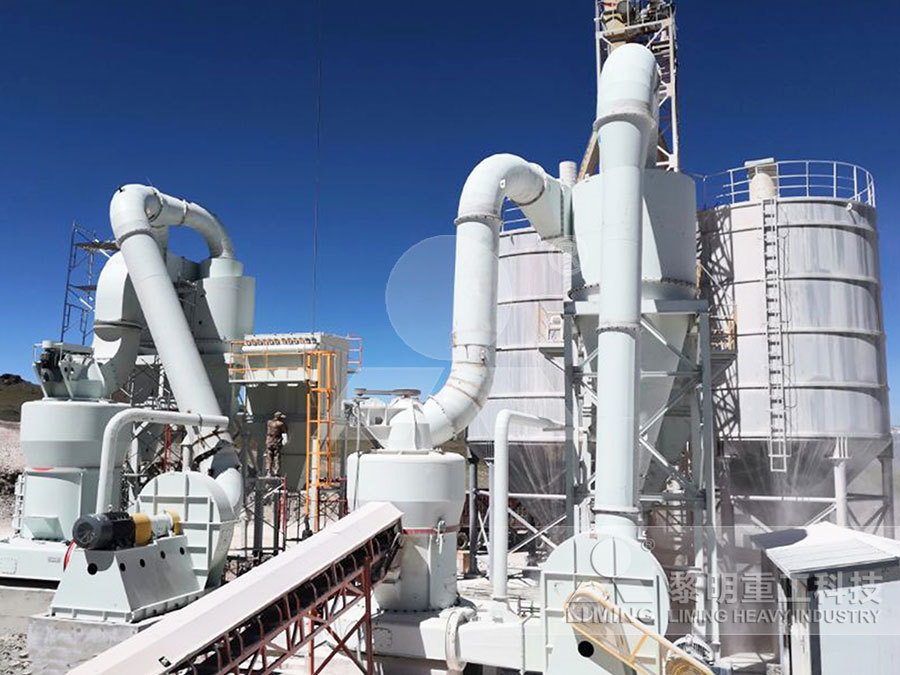
(PDF) A Review of Desulfurization Technology using Limestone in
2015年10月30日 A Review of Desulfurization Technology using Limestone in Circulating Fluidized Bed Boiler Type Power Plant October 2015 Journal of the Korean Institute of Resources Recycling 24(5):3年1月1日 Synthetic gypsum CaSO42H2O (also called flue gas desulpurizationFGD gypsum) is a coproduct resulted from the wet process of flue gas desulphurisation in thermal power plants(PDF) Study on synthetic gypsum obtained from wet flue gas Retrofit of Wet Limestone Based FGD System in a Typical 2 x 500 MW Coal Based Thermal Power Plant” with valuable inputs from the committee members This document can be used for installation of FGD system in a new thermal power plant also The document reflects pooledSTANDARD TECHNICAL SPECIFICATION FOR RETROFIT OF WET LIMESTONE Wet limestone scrubbing has high capital and operati ng cost due to the handling of liquid reagent and waste Nonetheless, it is the preferred process for coalfired electric utility power plants burning coal due to the low cost of limestone and SO 2 control efficiencies from 90% up to 98% (Schnelle, 2002) SemiDry SystemsAir Pollution Control Technology Fact Sheet US EPA