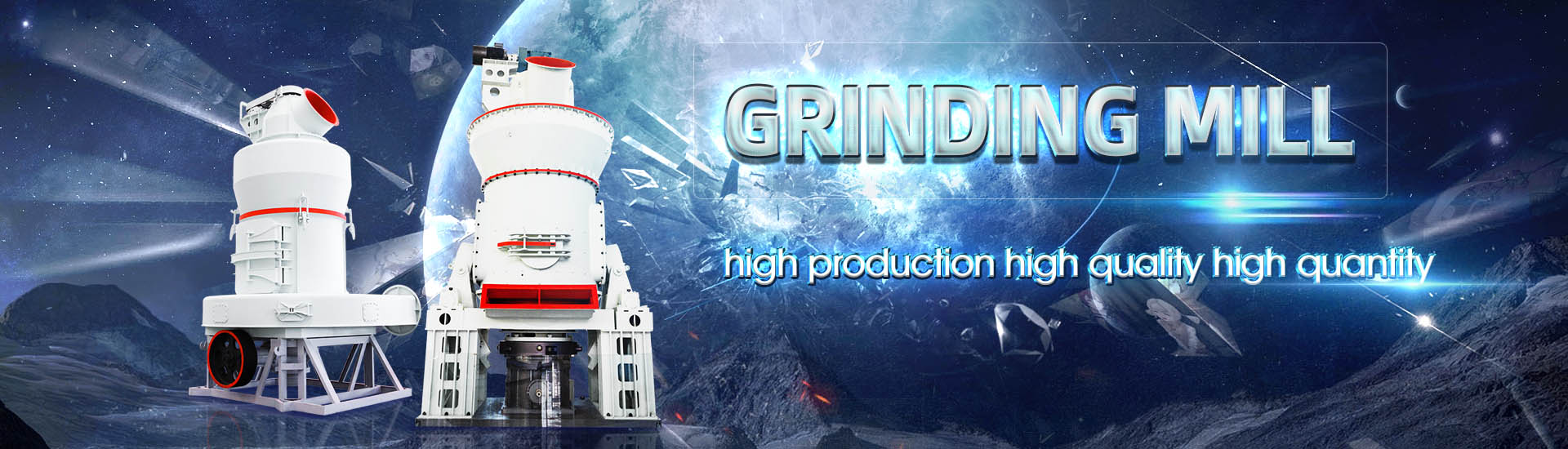
Laterite nickel grinding equipment
.jpg)
Hydrometallurgical nickel and cobalt plants and processes
Metso Outotec can perform laterite leaching in HPAL and atmospheric conditions Depending on your mineralogical requirements, nickel laterite highpressure acid leaching (HPAL) solutions Nickel ore divides into nickel sulfide ore and nickel oxide ore (laterite nickel ore) The Main beneficiation process of nickel sulfide is flotation, and the subsidiary process is magnetic and gravity separation Nickel oxide ores usually use Nickel Ore Processing Plant JXSC Mineral2024年11月1日 Saprolitic nickel laterite ore, with its high nickel content and low iron content, is more suitable for pyrometallurgical processes In contrast, limonitic nickel laterite ore, Review on comprehensive utilization of nickel laterite oreSXEW, or the Solvent Extraction – Electrowinning approach to lateritic ore beneficiation, is a hydrometallurgical method that relies on leaching, extractants, and electrowinning to produce nickel from ore This process is often referred Processing of Nickel Laterite Ores on the Rise FEECO
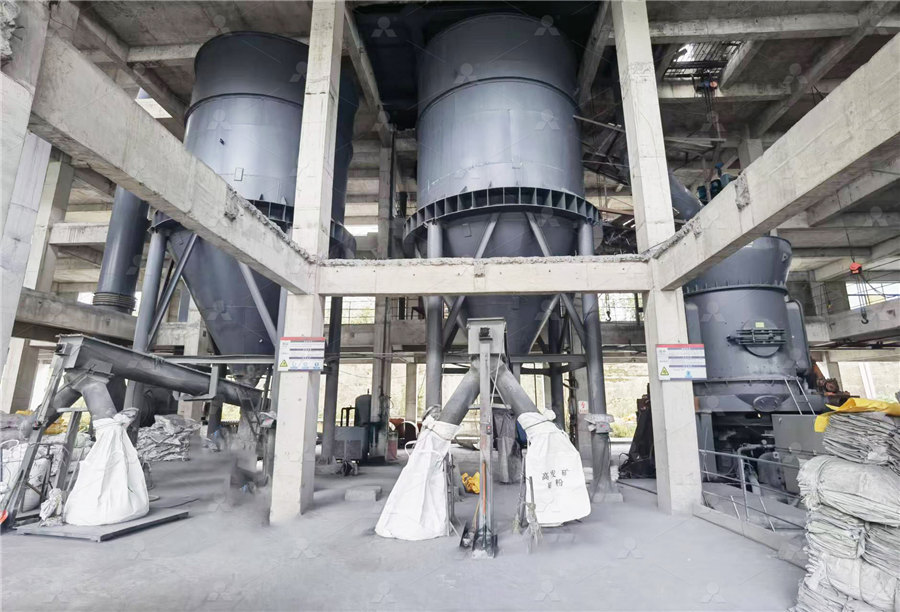
Preconcentration strategies in the processing of nickel laterite ores
2015年8月1日 By far the most common preconcentration process used ahead of commercial hydrometallurgical processing of Ni laterites is the removal of a coarse fraction from the feed Laterite ores are upgraded before smelting or leaching The upgrading entails gently crushing and/or grinding the ore and then separating the resulting small, soft, lowdensity Nirich Laterite Ore an overview ScienceDirect Topics2023年5月28日 Nickel laterite metallurgy is a nickel metallurgy technology using nickel laterite as raw material to produce metallic nickel or other products containing nickel In nature, nickel Nickel Laterite Metallurgy SpringerLink2024年5月3日 Ore is often processed near the mine site, but there is substantial regional and global trade in nickel laterite ores, and some trade in nickel sulfide concentrates Laterite ores occur as surface deposits and are traditionally Nickel industry Part 1 Processing nickel laterites and
.jpg)
Separation and Recovery of Iron and Nickel from LowGrade
2018年10月1日 The lowgrade nickel laterite ore used in this study was successfully upgraded through selective reduction by industrialized rotary kilns followed by magnetic separation The EQUIPMENT FEECO offers a variety of custom equipment and process solutions for the processing of nickel From agglomeration drums for use in the heap leaching process to nickel pelletizing systems, we can develop a Nickel Processing Equipment FEECO International Inc2024年11月21日 The washing equipment used in the nickel mining process mainly includes trommel scrubber, spiral washing machine and stirring scrubbing tank The laterite nickel mine washing system is composed of a cylindrical Nickel Ore Beneficiation And Equipment JXSC 2020年3月1日 The laterite nickel ore had an endothermic peak at 13597 °C, which was the melting point of the studied lowgrade laterite nickel ore, and the ore began to melt at this temperature To satisfy the feed size requirement of the experimental grinding equipment and the size required for the deep reduction test, Efficient enrichment of nickel and iron in laterite nickel ore by
.jpg)
Factors affecting nickel upgrade during selective grinding of low
2018年9月16日 The nickel and iron recoveries were 8936% and 9587% respectively, which achieved the highly efficient recovery and utilization of iron and nickel of lowgrade laterite nickel ore View Show abstract12224 j mater res technol 2020;9(6):12223–12235 1 Introduction In general, increasing attention has been paid to laterite ores as an alternative to nickel sulfide ore [1–5]Separation and recovery of iron and nickel from lowgrade laterite 2018年10月1日 The lowgrade nickel laterite ore used in this study was successfully upgraded through selective reduction by industrialized rotary kilns followed by magnetic separation The results indicated that both iron metallization extent and nickel metallization extent showed obvious linear correlation In addition, rational roasting temperature and prolonged grinding time could Separation and Recovery of Iron and Nickel from LowGrade Laterite 2023年5月28日 The nickel laterite in upper layer of the ore HPAL has developed into the mainstream technology for processing nickel laterite of limonite type, and its equipment, control, and production technology have become crushing, and grinding, the ferronickel particles of 1–20 mm are separated by magnetic separation or gravity Nickel Laterite Metallurgy SpringerLink
.jpg)
The Comprehensive Guide to Nickel Processing Miningpedia
2024年1月19日 Crushing is essential to facilitate efficient grinding and improve the liberation of nickel minerals from the surrounding rock 2 Grinding After the ore is crushed, it undergoes grinding to further reduce its particle size Grinding is typically performed in ball mills, which are rotating cylinders filled with steel balls1 Crushing Screening The raw ore enters the jaw crusher through the feeder for primary crushing and then enters the cone crusher for medium crushing After the vibrating screen screening, the materials under the screen enter the grinding process while the screened materials enter the finecrushing process And select the cone crusher for the finecrushing operationNickel Ore Processing Plant JXSC MineralWe offer the best in rotary dryers and coolers for processing nickel, as well as engineered material handling equipment, and even rotary kilns for nickel recovery For more information on our nickel capabilities, contact us today! SOURCES: Dalvi, Ashok D, Dr, W Gordon Bacon, Dr, and Robert C Osborne The Past and the Future of Nickel Processing of Nickel Laterite Ores on the Rise FEECO 2022年5月31日 The processing methods of laterite nickel ore is mainly divided into two types: pyrometallurgy process and hydrometallurgy process According to the difference of nickel, cobalt content and ore type, and different working How to Extract Laterite Nickel Ore? 7 Processing
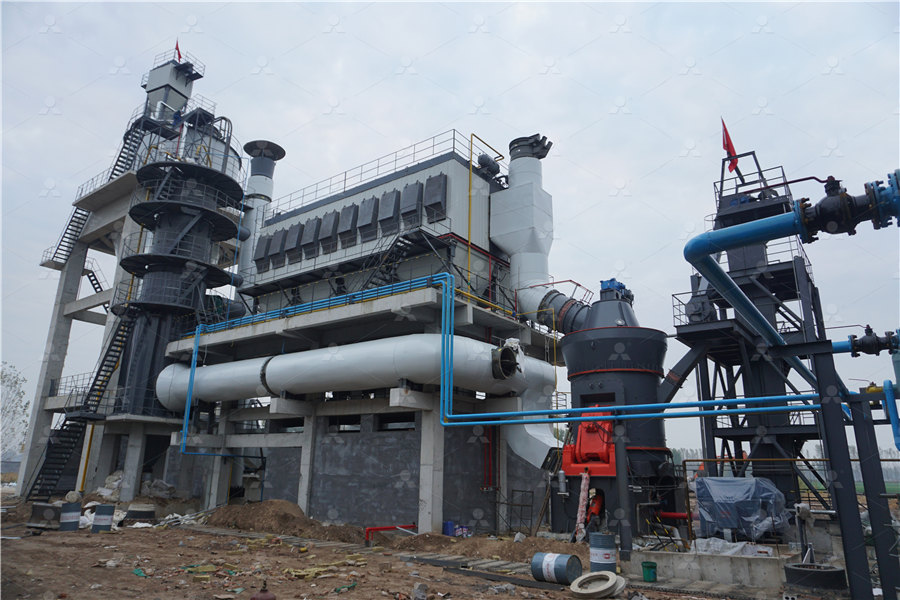
Preconcentration strategies in the processing of
2015年4月2日 Despite the growth in nickel laterite processing, upgrading these ores remains a challenge This is mainly because of their complex and variable mineralogy and the lack of definite nickelbearing 2013年8月1日 Optimum grinding time with respect to Ni upgrade was 025 min for SG nickel laterite samples Generally, grinding larger particles and/or collecting finer product size yielded better Ni selective grinding was strengthened by adjusting operational conditions and by choosing proper grinding equipment (Han et al, 2010; Ou et Stirred milling kinetics of siliceous goethitic nickel laterite for 2024年6月5日 This study investigates the characterization of Fanibi Laterite and the efficiency of froth flotation to beneficiate nickel from its host rock sourced in Akure, Ondo State, NigeriaCharacterization and Beneficiation of Fanibi Laterite for Nickel 2015年7月27日 1 Mineral Engineering Technical Services PO Box 5778 St Georges Tce WA 6831 P: (+61 8) 9421 9000 F: (+61 8) 9325 8311 ABN 66 009 357 171 W: metsengineering E: info@metsengineering A division of Midas Engineering Group Nickel Ore Processing Trends The Rise of Nickel Laterites and Advances in Sulphide ProcessingNickel Processing and The Rise of Laterites SlideShare
.jpg)
Nickel Processing Equipment, Process Flow, Cases JXSC Machine
2019年8月26日 Eightyfour million tons, or 60 percent of the total available nickel is in laterite deposits A deposit in which rain and surface water leached nickelrich rock and concentrated the nickel at or near the surface of the Earth is a laterite deposit Nickel sulfide deposits contain the remaining forty percent (56 million tons)2013年8月1日 Optimum grinding time with respect to Ni upgrade was 025 min for SG nickel laterite samples Generally, grinding larger particles and/or collecting finer product size selective grinding was strengthened by adjusting operational conditions and by choosing proper grinding equipment (Han et al, 2010; Ou et al, 2007, Yusupov Stirred milling kinetics of siliceous goethitic nickel laterite for 2015年9月20日 Optimum grinding time with respect to Ni upgrade was 025 min for SG nickel laterite samples Generally, grinding larger particles and/or collecting finer product size yielded better Ni upgrade STIRRED MILLING OF NICKEL LATERITES FOR SELECTIVE COMMINUTION2020年4月15日 In this study, segregation roasting and magnetic separation are used to extract nickel from a garnierite laterite ore The garnierite laterite ore containing 072% Ni, 0029% Co, 865% Fe, 2966% Extraction of Nickel from Garnierite Laterite Ore Using Roasting
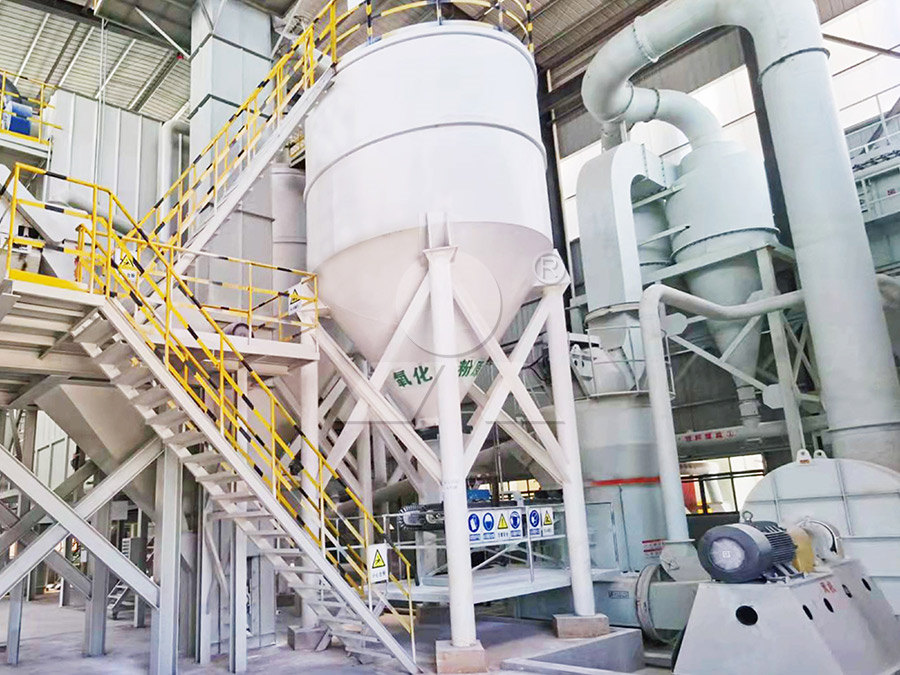
(PDF) Nickel Laterite Smelting Processes and Some
2019年9月3日 Lowgrade ferronickel is simply an iron–nickel alloy that contains lower nickel than standard ferronickel does (ie, minimum of 15%) According to the literature, within a very short2020年6月18日 Separation and recovery of iron and nickel from low‒grade laterite nickel ore using reduction roasting at rotary kiln followed by magnetic separation technique Mining, Metallurgy Exploration Efficient Synchronous Extraction of Nickel, Copper, 2019年12月12日 The production of ferronickel concentrate from lowgrade nickel laterite ore containing 131% nickel (Ni) was studied by the nonmelting reduction magnetic separation processProduction of Ferronickel Concentrate from LowGrade Tuxingsun Mineral Mining provides comprehensive solutions for nickel mining, beneficiation, and processing We offer a wide range of services, from exploration and mine development to mineral processing and refining Our experienced team utilizes cuttingedge technologies and equipment to deliver highquality results for our clientsNickel Ore Mining, Beneficiation, and Processing: A
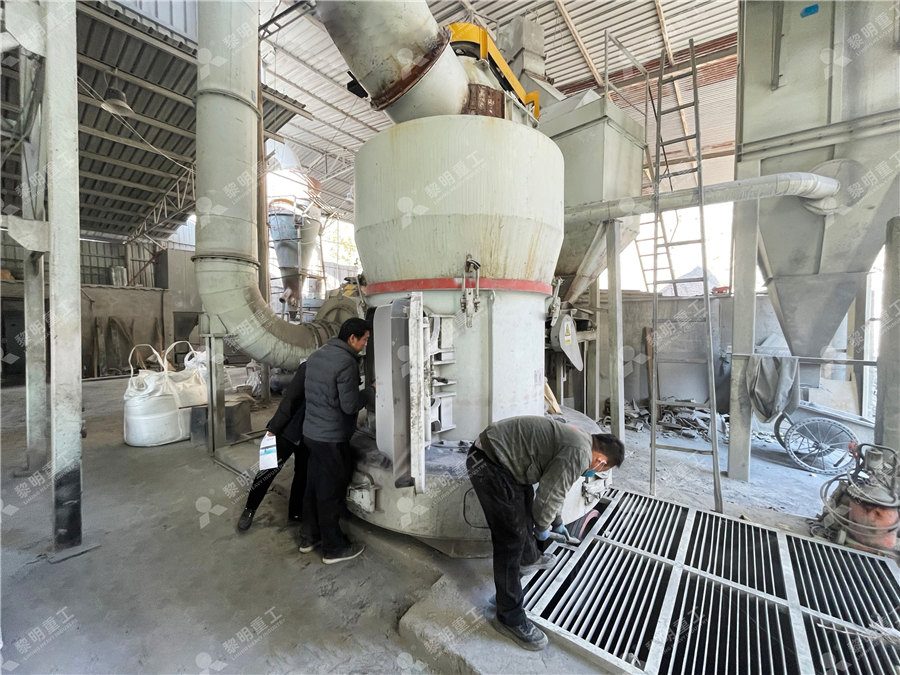
Magnetic separation for recovering iron resources from acid
2024年8月21日 The acidleaching tailings of laterite nickel ore are a hazardous waste generated by the laterite nickel ore industry [1], [2], [3]As global demand for nickel continues to rise and nickel sulfide resources decrease, the extraction of nickel resources from laterite nickel ores the main development trend of the global nickel industry in the coming years [4]mineral phases of laterite nickel ore are limonite, serpentine, chlorite, quartz, chromite and magnetite In order to further study the beneficiability of laterite nickel ore, it is necessary to analyze the mineralogical characteristics of its main minerals by modern analytical means such as Table 1 Chemical composition of laterite nickel ore Relationship between process mineralogical characterization and INTRODUCTION Nickel laterite ores comprise a significant resource in Australia and according to United States Geological Survey data nearly a quarter of world reserves are located there (USGS, 2016)DEVELOPMENTS IN THE HYDROMETALLURGICAL PROCESSING OF NICKEL reduction roasting process of laterite nickel ore in order to efficiently enrich lowgrade laterite nickel ore, the process was short, low energy consumption, good economic and environmental benefits 2 Material and Methods 21 Experimental materials The raw material used in the experiment was silicomagnesite laterite nickel oreExtraction of Ferronickel Concentrate by Reduction Roasting
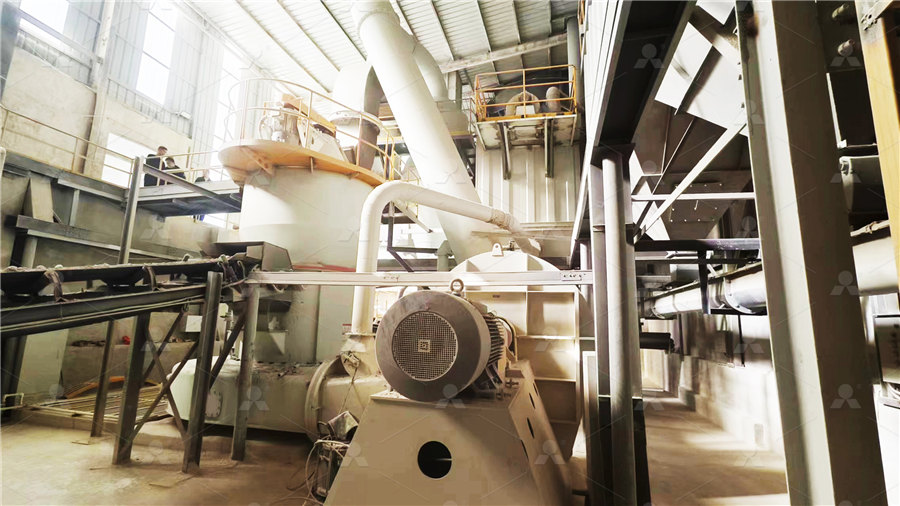
HighGrade Ferronickel Concentrates Prepared from Laterite Nickel
2023年11月11日 (a) Particle size distributions of asprepared ferronickel concentrates with different fine grinding time, and (b) chemical analysis of ferronickel concentrates with different CaF 2 additive amounts2021年8月23日 Lowgrade saprolite nickel laterite, characterized by complicated minerals composition and finegrained and complex dissemination, was commonly treated with a low recovery efficiency of Ni and Fe by conventional methods Hence, an improved direct reduction and magnetic separation process was proposed Meanwhile, the mechanisms on the Upgrade of nickel and iron from lowgrade nickel laterite by Nickel laterite makes up 70% of the world’s nickel reserves, and at the rate that nickel sulphide deposits are being depleted, production is switching to laterites which now account for 60% of the world’s nickel Nickel laterite is normally processed by pyrometallurgy (ie heat), hydrometallurgy (ie acid), or in some cases blending with What is nickel laterite? Homeland NickelEQUIPMENT FEECO offers a variety of custom equipment and process solutions for the processing of nickel From agglomeration drums for use in the heap leaching process to nickel pelletizing systems, we can develop a Nickel Processing Equipment FEECO International Inc
.jpg)
Nickel Ore Beneficiation And Equipment JXSC
2024年11月21日 The washing equipment used in the nickel mining process mainly includes trommel scrubber, spiral washing machine and stirring scrubbing tank The laterite nickel mine washing system is composed of a cylindrical 2020年3月1日 The laterite nickel ore had an endothermic peak at 13597 °C, which was the melting point of the studied lowgrade laterite nickel ore, and the ore began to melt at this temperature To satisfy the feed size requirement of the experimental grinding equipment and the size required for the deep reduction test, Efficient enrichment of nickel and iron in laterite nickel ore by 2018年9月16日 The nickel and iron recoveries were 8936% and 9587% respectively, which achieved the highly efficient recovery and utilization of iron and nickel of lowgrade laterite nickel ore View Show abstractFactors affecting nickel upgrade during selective grinding of low 12224 j mater res technol 2020;9(6):12223–12235 1 Introduction In general, increasing attention has been paid to laterite ores as an alternative to nickel sulfide ore [1–5]Separation and recovery of iron and nickel from lowgrade laterite
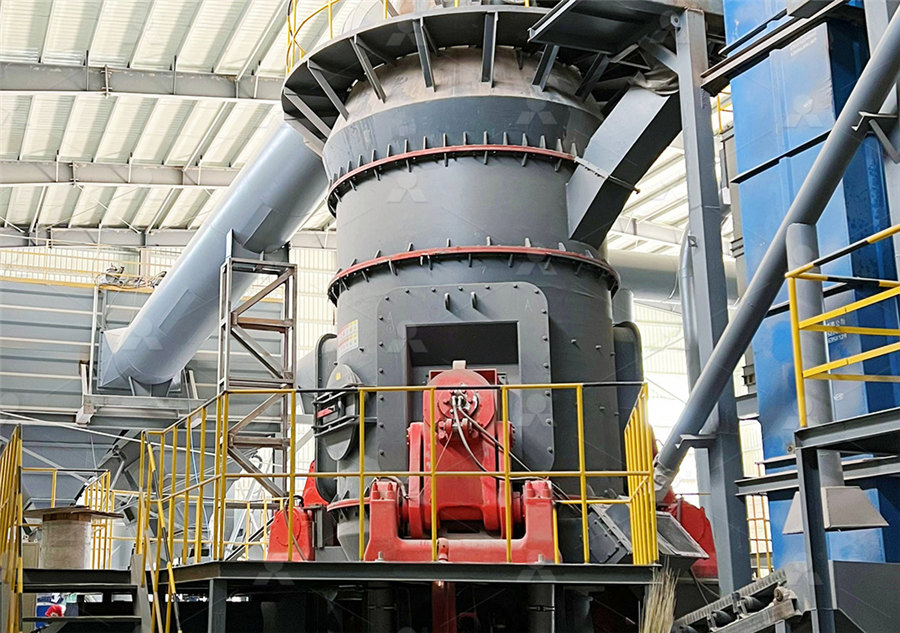
Separation and Recovery of Iron and Nickel from LowGrade Laterite
2018年10月1日 The lowgrade nickel laterite ore used in this study was successfully upgraded through selective reduction by industrialized rotary kilns followed by magnetic separation The results indicated that both iron metallization extent and nickel metallization extent showed obvious linear correlation In addition, rational roasting temperature and prolonged grinding time could 2023年5月28日 The nickel laterite in upper layer of the ore HPAL has developed into the mainstream technology for processing nickel laterite of limonite type, and its equipment, control, and production technology have become crushing, and grinding, the ferronickel particles of 1–20 mm are separated by magnetic separation or gravity Nickel Laterite Metallurgy SpringerLink2024年1月19日 Crushing is essential to facilitate efficient grinding and improve the liberation of nickel minerals from the surrounding rock 2 Grinding After the ore is crushed, it undergoes grinding to further reduce its particle size Grinding is typically performed in ball mills, which are rotating cylinders filled with steel ballsThe Comprehensive Guide to Nickel Processing Miningpedia1 Crushing Screening The raw ore enters the jaw crusher through the feeder for primary crushing and then enters the cone crusher for medium crushing After the vibrating screen screening, the materials under the screen enter the grinding process while the screened materials enter the finecrushing process And select the cone crusher for the finecrushing operationNickel Ore Processing Plant JXSC Mineral
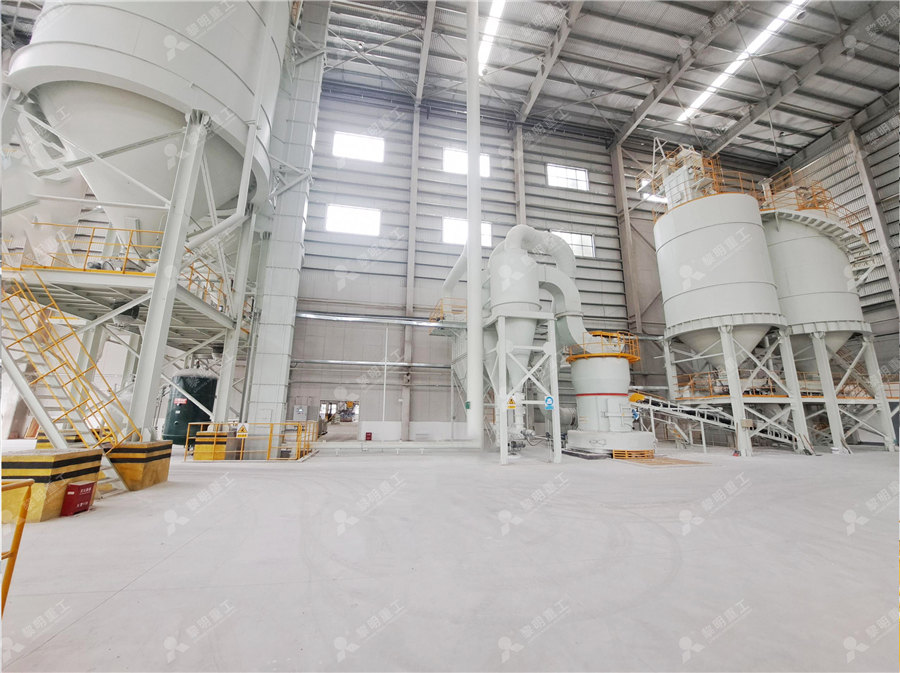
Processing of Nickel Laterite Ores on the Rise FEECO
We offer the best in rotary dryers and coolers for processing nickel, as well as engineered material handling equipment, and even rotary kilns for nickel recovery For more information on our nickel capabilities, contact us today! SOURCES: Dalvi, Ashok D, Dr, W Gordon Bacon, Dr, and Robert C Osborne The Past and the Future of Nickel