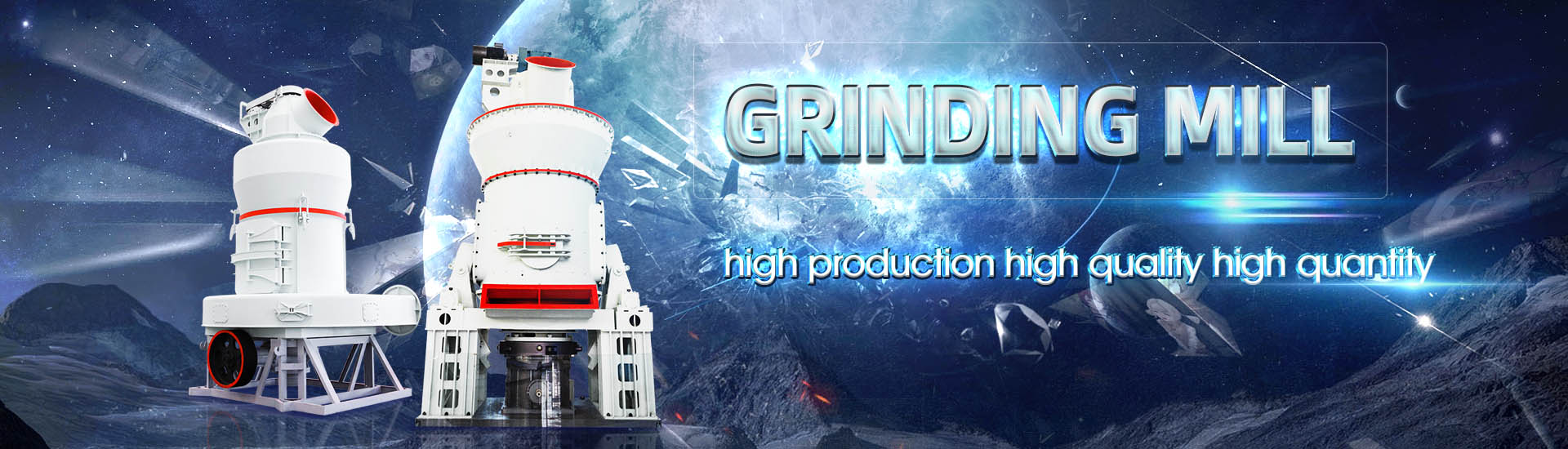
Ball mill ratio ball mill ratio ball mill ratio
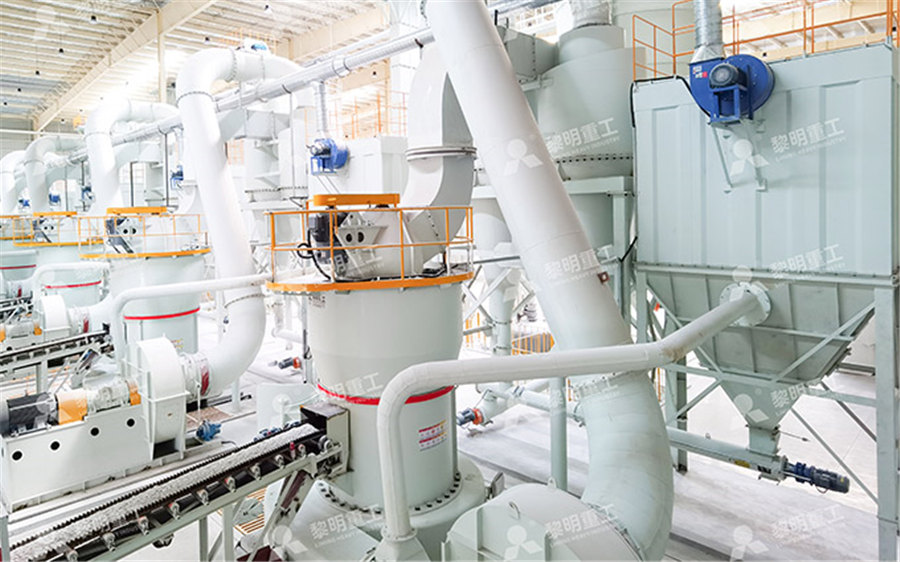
Comparative Study on Improving the Ball Mill Process
2021年2月19日 Optimization results confirmed that the balls to powder weight ratio were the most influential process parameter The optimum process parameters setting concluded that balls to powder weight ratio are 20:1, the optimum ball mill working capacity is 2 L while the 2018年11月1日 It increases the milling efficiency of ball milling Tungsten powder and grinding balls were weighed by the precision balance (with the accuracy of 00001 g) respectively to The ball to powder ratio (BPR) dependent morphology and microstructure 2004年12月10日 The L/D ratio of the ball mill was varied in four steps of 175, 21, 279 and 349, and the ball charge filling ratio was varied in three steps of 15%, 20% and 25% The Optimization of continuous ball mills used for finishgrinding 2024年11月23日 The major influencing factors in ball milling process are ball mill type, ball milling speed, balltopowder weight ratio, ball milling media (grinding media), the temperature Mechanism of Ball Milling and the Factors Affecting the

Navigating Ball Mill Specifications for Theory‐to‐Practice
2024年8月15日 Considering that for efficient milling results ball mill manufacturers recommend a filling factor of ~30 % in planetary ball mills, using lowdensity balls will thus exceed the 2022年1月1日 The effects of the balltopowder diameter ratio (BPDR) and the shape of the powder particles on EDEM simulation results and time in the planetary ball mill was Effects of balltopowder diameter ratio and powder particle 2021年3月12日 Ball mill optimisation As grinding accounts for a sizeable share in a cement plant’s power consumption, optimisation of grinding equipment such as ball mills can provide BALL MILLS Ball mill optimisation Holzinger Consulting2024年1月11日 Nanostructured SAF2507 super duplex stainless steel powders were prepared in a Retsch PM100 planetary ball mill for 20 h at 5:1 and 10:1 ball to powder ratios, Effect of Ball to Powder Ratios on the Phase Transformation
.jpg)
Three rules for the optimum ball mill setup RETSCH
Three rules for the optimum ball mill setup Author: Retsch Subject: The success of a ball milling application depends on the correct selection of accessories and process parameters This 2024年6月27日 In this paper, we introduce a novel planetary ball mill device featuring an interchangeable speed ratio, allowing users to manually adjust this parameter to suit the needs A new planetary ball mill device with adjustable speed ratio 2021年11月1日 The filling ratio, ratio of particle to ball and mineral weight were varied to control the mill load The initial ratio of grading ball was 30 mm: 40 mm: 50 mm: 70 mm = 30: 20: 30: 20 It should be noted that the diameter of instrumented grinding media is 70 mm Rotation speed of cement ball mill was set to 80% The grinding time was 10 min for Assessing load in ball mill using instrumented grinding media2017年2月13日 Ball Mills or Rod Mills in a complete range of sizes up to 10′ diameter x 20′ long, offer features of operation and convertibility to meet your exact needs They may be used for pulverizing and either wet or dry grinding Ball Mills 911Metallurgist
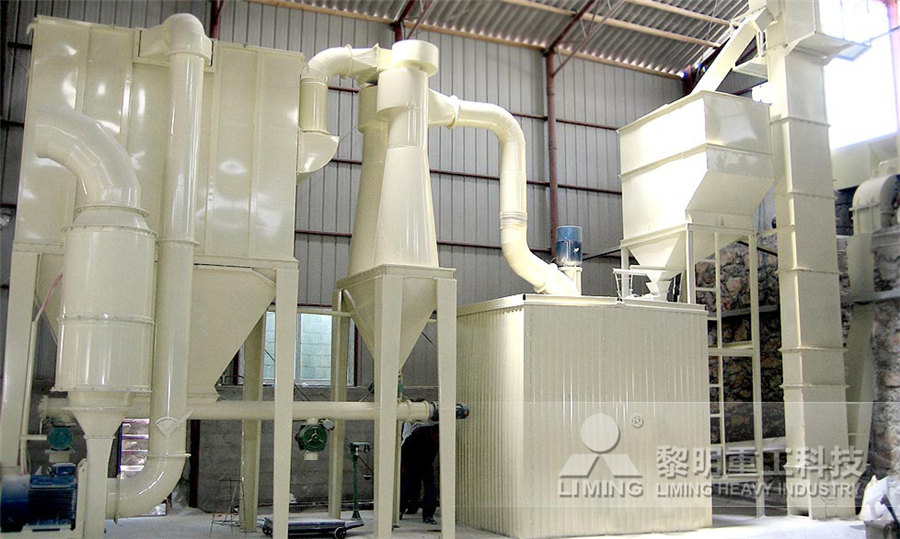
Optimization of continuous ball mills used for finishgrinding
2004年12月1日 The L/D ratio of the ball mill was varied in four steps of 175, 21, 279 and 349, and the ball charge filling ratio was varied in three steps of 15%, 20% and 25% The experiments clearly 2024年6月27日 When impact energy and milling power is plotted against the different speed ratios, this relationship is clear to observe, that at the point of optimal impact energy there is a dip in the milling powerSuch nonlinear behavior makes the PBM performance difficult to predict There is also the fact that this idealized model does not take the influence of balltoball A new planetary ball mill device with adjustable speed ratio If a ball mill uses little or no water during grinding, it is a ‘dry’ mill If a ball mill uses water during grinding, it is a ‘wet’ mill A typical ball mill will have a drum length that is 1 or 15 times the drum diameter Ball mills with a drum length to diameter ratio greater than Ball Mill (Ball Mills Explained) saVRee saVReeThe term ball mill is restricted to those having a length to diameter ratio of 2 to 1 and less Ball mills in which the length to diameter ratio is between 3 and 5 are designated tube mills The latter are sometimes divided into several longitudinal compartments, each having a different charge composition; the charges can be steel balls or rods Ball Mill an overview ScienceDirect Topics
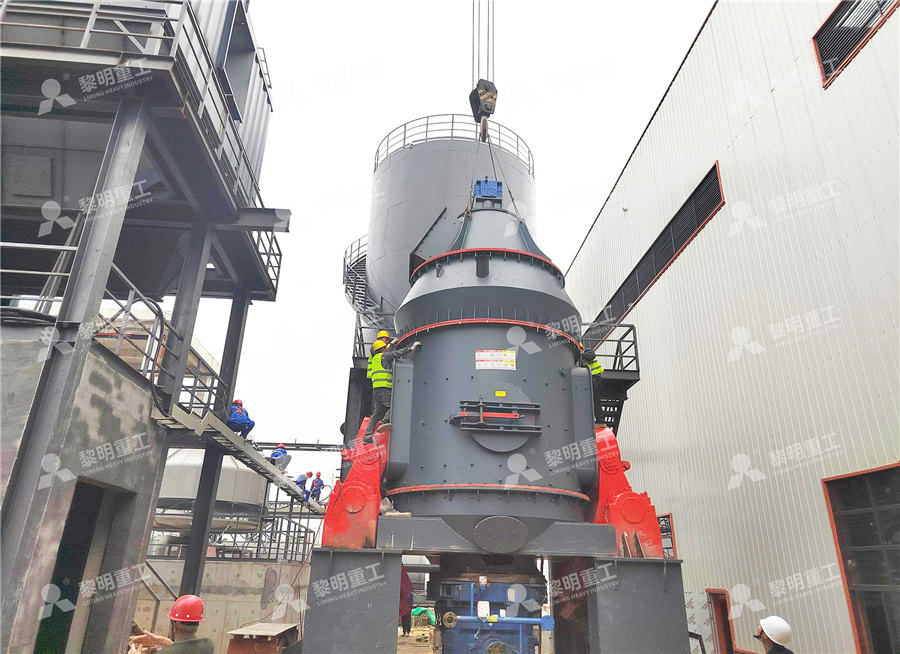
Optimization of continuous ball mills used for finishgrinding
2004年12月10日 The L/D ratio of the ball mill was varied in four steps of 175, 21, 279 and 349, and the ball charge filling ratio was varied in three steps of 15%, 20% and 25% The experiments clearly indicated that the optimal L/D ratio and the optimal ball charge filling ratio are different for each feed fineness2024年6月27日 When impact energy and milling power is plotted against the different speed ratios, this relationship is clear to observe, that at the point of optimal impact energy there is a dip in the milling powerSuch nonlinear behavior makes the PBM performance difficult to predict There is also the fact that this idealized model does not take the influence of balltoball A new planetary ball mill device with adjustable speed ratio 2013年8月3日 In Grinding, selecting (calculate) the correct or optimum ball size that allows for the best and optimum/ideal or target grind size to be achieved by your ball mill is an important thing for a Mineral Processing Engineer AKA Metallurgist to do Often, the ball used in ball mills is oversize “just in case” Well, this safety factor can cost you much in recovery and/or mill liner Calculate and Select Ball Mill Ball Size for Optimum GrindingWhen the ball mill is used for pulverizing material, the ball milling ratio of the following steel balls is the highest: In production, the twostage ratio and the multistage ratio are more common Generally, the multistage ratio follows the principle of “less at both ends and more in the middle”How to choose the ball loading and loading ratio of ball mill?
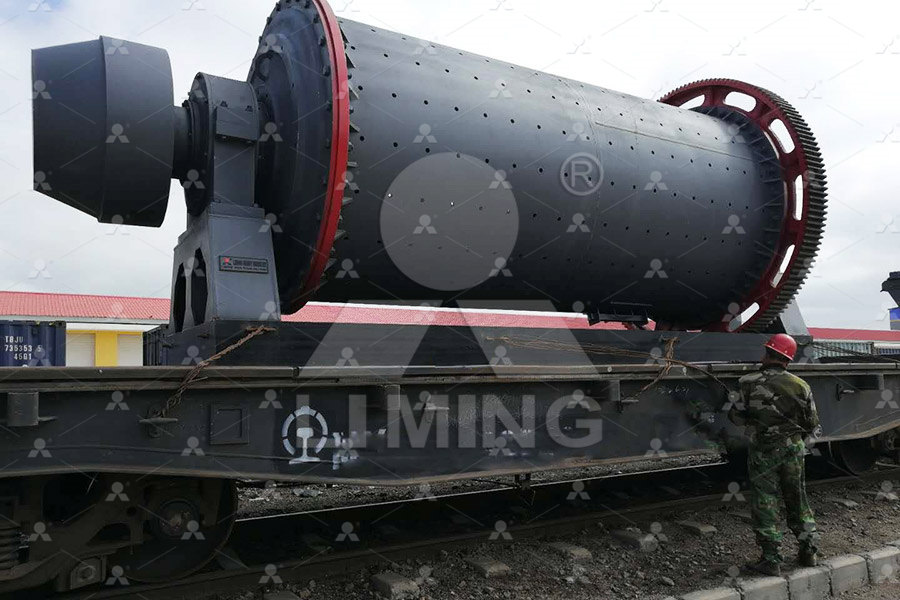
Comparison of Particle Shape, Surface Area, and
2023年1月8日 DIA results showed that particles produced by the ball mill had higher aspect ratio values than those by the stirred mill This was attributed to the impact, and attrition breakage modes produced by the ball and stirred mill, 2020年7月2日 In recent research done by AmanNejad and Barani [93] using DEM to investigate the effect of ball size distribution on ball milling, charging the mill speed with 40% small balls and 60% big balls (PDF) Effects of Ball Size Distribution and Mill Speed and 2017年10月26日 Ball mill shape factors in the period prior to 1927 averaged 11/1 for 29 center discharge mills and 10/1 for 30 peripheral discharge mills With the resumption of new plant construction after the 1930’s depression, the Morenci concentrator continued the 1/1 ratio with its 31 x 31 m (10 x 10 ft) millsL / D Ratio in Overflow Ball Mill Design Operation2002年7月1日 The rotational direction of a pot in a planetary ball mill and its speed ratio against revolution of a disk were studied in terms of their effects on the specific impact energy of balls calculated from the simulation on the basis of the Discrete Element Method (DEM) and structural change of talc during milling Effects of rotational direction and rotationtorevolution speed ratio
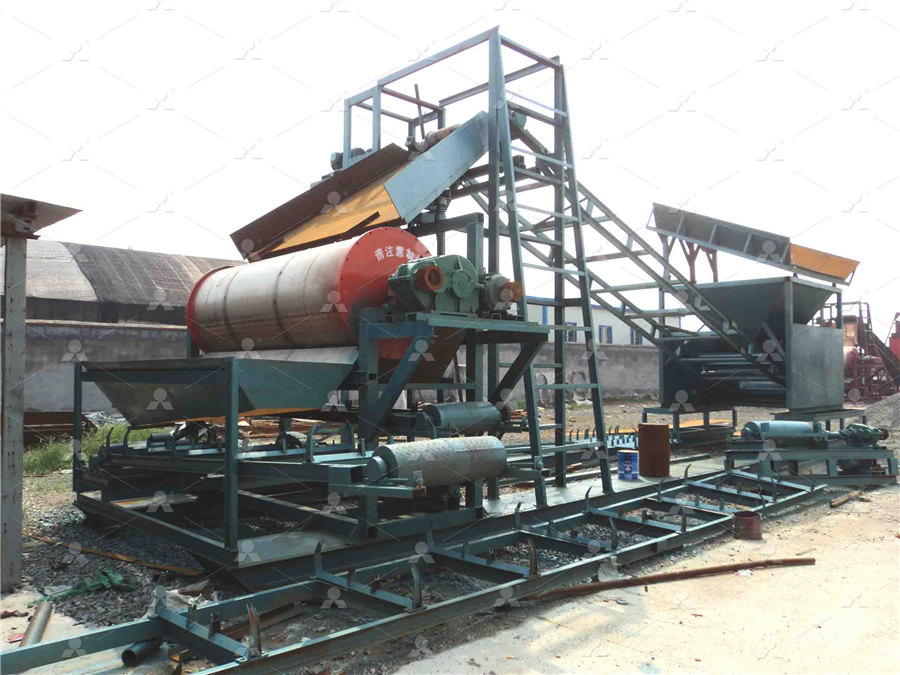
Navigating Ball Mill Specifications for Theory‐to‐Practice
2024年8月15日 Therefore, each ball mill model will feature a different energy profile dependent on its planetary disk and jar dimensions, irrespective of the chosen milling conditions (rpm, time, and balls) a constant while varying the balls’ material with a different density will directly affect the total volumetomass ratio of the balls that, in 2022年1月1日 The effects of the balltopowder diameter ratio (BPDR) and the shape of the powder particles on EDEM simulation results and time in the planetary ball mill was investigated BPDR was varied from 1 to 40/3 by changing the powder particle diameter from 8 to 06 mm The size and shape of the powder particles do not give a significant change in both the ball motion Effects of balltopowder diameter ratio and powder particle 2023年4月28日 The ratio of balls to powder affects both how the milling works and how good the powder is that comes out of it By changing the ratio of balls to powder, you can find the best ratio to get the particle size and distribution The milling process and the size distribution of the particles can be affected by how fast the ball mill turnsParametric study on four station ball mill for synthesis of 2019年8月14日 According to the shape of the ball mill cylinder (the ratio of length to diameter) : • Short cylinder ball mill: the cylinder length(L) is less than two times of the cylinder diameter(D),that is, the ball mill with L≤2D is the short cylinder ball mill It is usually a singlebin structure, mainly used for coarse grinding or firststage The Ultimate Guide to Ball Mills Miningpedia
7TOCS.jpg)
Optimization of continuous ball mills used for finishgrinding
2004年12月10日 The L/D ratio of the ball mill was varied in four steps of 175, 21, 279 and 349, and the ball charge filling ratio was varied in three steps of 15%, 20% and 25% The experiments clearly indicated that the optimal L/D ratio and the optimal ball charge filling ratio are different for each feed finenessExplain the role of ball mill in mineral industry and why it is extensively used Describe different types of ball mill design Rod Mill Autogenous Mill; Length: Diameter Ratio: 14 to 18: 05 to 35: 025 to 050: Feed Size: 25 cm maximum19 cm125 to 09cm: Coarse Ore Normal Ore: Reduction Ratio:AMIT 135: Lesson 7 Ball Mills Circuits – Mining Mill 2012年6月1日 As the cylinder starts to rotate, the grinding balls inside the cylinder crush and grind the feed material, generating mechanical energy that aids in breaking bonds, activating the catalyst, and (PDF) Grinding in Ball Mills: Modeling and Process ControlA new planetary ball mill device with adjustable speed ratio for enhanced mechanochemical processes† Frank Yntema,ab Cameron Webstera and Emmanouil Broumidis *ab In this paper, we introduce a novel planetary ball mill device featuring an interchangeable speed ratio, allowing users to manually adjust this parameter to suit the needs of each A new planetary ball mill device with adjustable speed
.jpg)
Intelligent optimal control system for ball mill grinding
2017年8月27日 First, the water feed rate to the ball mill should be ratio to the feed fresh ore to satisfy the required grinding density in the ball mill Second, the sump level is controlled to be constant by regulating the pump speed without considering the effect of feeding pressure to2021年1月22日 Grinding operation is used extensively in the industry of beneficiation, metallurgy, chemical engineering, and electric power Assisted by the impact and abrasion between media (steel ball, steel rod, gravel, ceramic ball) and ore, the grinding operation reduces the particle size in the mill [[1], [2], [3]]To produce the qualified size and high liberation of An innovative approach for determining the grinding media 2023年10月27日 The ball mill is a rotating cylindrical vessel with grinding media inside, which is responsible for breaking the ore particles Grinding media play an important role in the comminution of mineral ores in these mills This work reviews the application of balls in mineral processing as a function of the materials used to manufacture them and the mass loss, as A Review of the Grinding Media in Ball Mills for Mineral OPTIMUM BALL MILL SETUP The success of a ball milling application depends on the correct selection of accessories and process parameters This includes jar sizes, jar materials, ball sizes, number of balls, Mechanochemistry: In mechanochemistry, the jar filling ratio is very individual and closely related to the reaction achieved Here, the Three rules for the optimum ball mill setup RETSCH
.jpg)
how to calculate circulating load in ball mill – stone cruxder
By calculating this ratio, you can determine whether your system is operating optimally or if adjustments need to be made To calculate the circulating load ratio, divide the mass of solids in each stream by their respective flow rates The sum of these ratios represents the overall circulating load ratio for your ball mill2021年12月1日 The effects of the balltopowder diameter ratio (BPDR) and the shape of the powder particles on EDEM simulation results and time in the planetary ball mill was investigated(PDF) Effects of balltopowder diameter ratio and powder The grinding jars are arranged eccentrically on the sun wheel of the planetary ball mill The direction of movement of the sun wheel is opposite to that of the grinding jars in the ratio 1:2 (or 1:25 or 1:3) The grinding balls in the grinding jars are subjected to superimposed rotational movements, the socalled Coriolis forcesPlanetary Ball Mill PM 400 RETSCH powerful and quick 2023年4月30日 Ball mill is a type of grinding equipment that uses the rotary cylinder to bring the grinding medium and materials to a certain height and make them squeeze, impact, and grind and peel each other to grind materials Generally, the larger the size of the ball mill, the lower the grinding medium charging ratio When the ball mill rotates at a Ball Mill SpringerLink
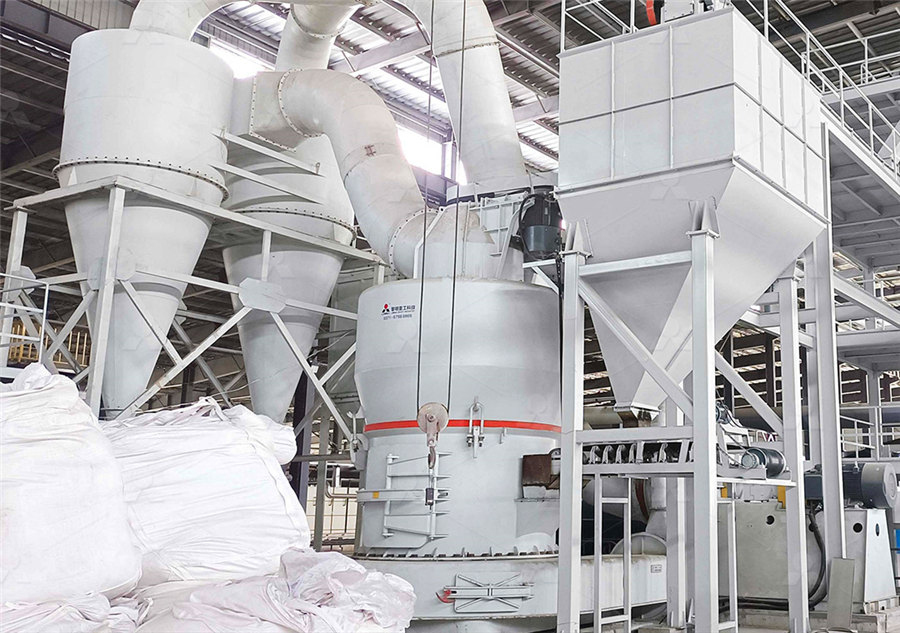
Assessing load in ball mill using instrumented grinding media
2021年11月1日 The filling ratio, ratio of particle to ball and mineral weight were varied to control the mill load The initial ratio of grading ball was 30 mm: 40 mm: 50 mm: 70 mm = 30: 20: 30: 20 It should be noted that the diameter of instrumented grinding media is 70 mm Rotation speed of cement ball mill was set to 80% The grinding time was 10 min for 2017年2月13日 Ball Mills or Rod Mills in a complete range of sizes up to 10′ diameter x 20′ long, offer features of operation and convertibility to meet your exact needs They may be used for pulverizing and either wet or dry grinding Ball Mills 911Metallurgist2004年12月1日 The L/D ratio of the ball mill was varied in four steps of 175, 21, 279 and 349, and the ball charge filling ratio was varied in three steps of 15%, 20% and 25% The experiments clearly Optimization of continuous ball mills used for finishgrinding 2024年6月27日 When impact energy and milling power is plotted against the different speed ratios, this relationship is clear to observe, that at the point of optimal impact energy there is a dip in the milling powerSuch nonlinear behavior makes the PBM performance difficult to predict There is also the fact that this idealized model does not take the influence of balltoball A new planetary ball mill device with adjustable speed ratio
.jpg)
Ball Mill (Ball Mills Explained) saVRee saVRee
If a ball mill uses little or no water during grinding, it is a ‘dry’ mill If a ball mill uses water during grinding, it is a ‘wet’ mill A typical ball mill will have a drum length that is 1 or 15 times the drum diameter Ball mills with a drum length to diameter ratio greater than The term ball mill is restricted to those having a length to diameter ratio of 2 to 1 and less Ball mills in which the length to diameter ratio is between 3 and 5 are designated tube mills The latter are sometimes divided into several longitudinal compartments, each having a different charge composition; the charges can be steel balls or rods Ball Mill an overview ScienceDirect Topics2004年12月10日 The L/D ratio of the ball mill was varied in four steps of 175, 21, 279 and 349, and the ball charge filling ratio was varied in three steps of 15%, 20% and 25% The experiments clearly indicated that the optimal L/D ratio and the optimal ball charge filling ratio are different for each feed finenessOptimization of continuous ball mills used for finishgrinding 2024年6月27日 When impact energy and milling power is plotted against the different speed ratios, this relationship is clear to observe, that at the point of optimal impact energy there is a dip in the milling powerSuch nonlinear behavior makes the PBM performance difficult to predict There is also the fact that this idealized model does not take the influence of balltoball A new planetary ball mill device with adjustable speed ratio
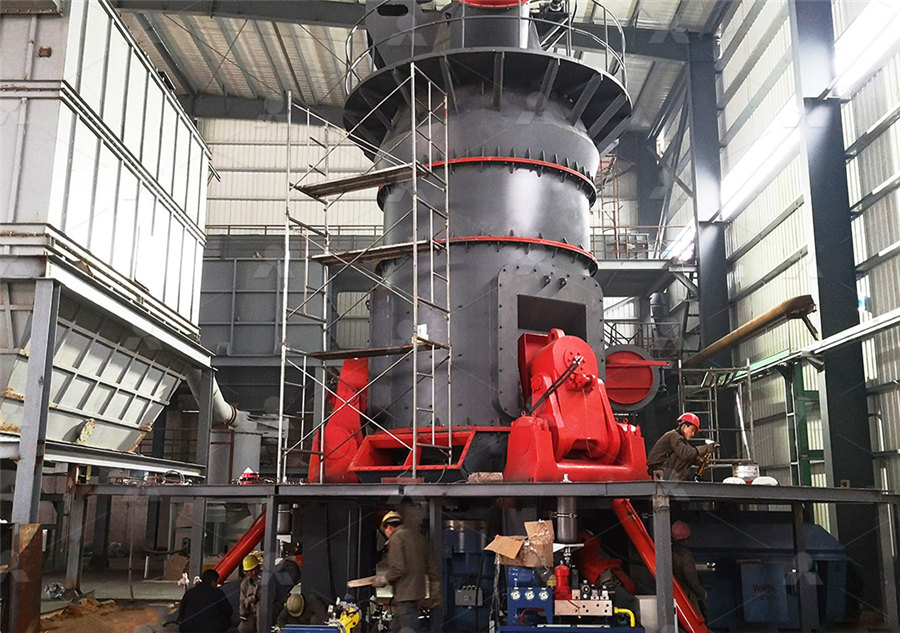
Calculate and Select Ball Mill Ball Size for Optimum Grinding
2013年8月3日 In Grinding, selecting (calculate) the correct or optimum ball size that allows for the best and optimum/ideal or target grind size to be achieved by your ball mill is an important thing for a Mineral Processing Engineer AKA Metallurgist to do Often, the ball used in ball mills is oversize “just in case” Well, this safety factor can cost you much in recovery and/or mill liner When the ball mill is used for pulverizing material, the ball milling ratio of the following steel balls is the highest: In production, the twostage ratio and the multistage ratio are more common Generally, the multistage ratio follows the principle of “less at both ends and more in the middle”How to choose the ball loading and loading ratio of ball mill?