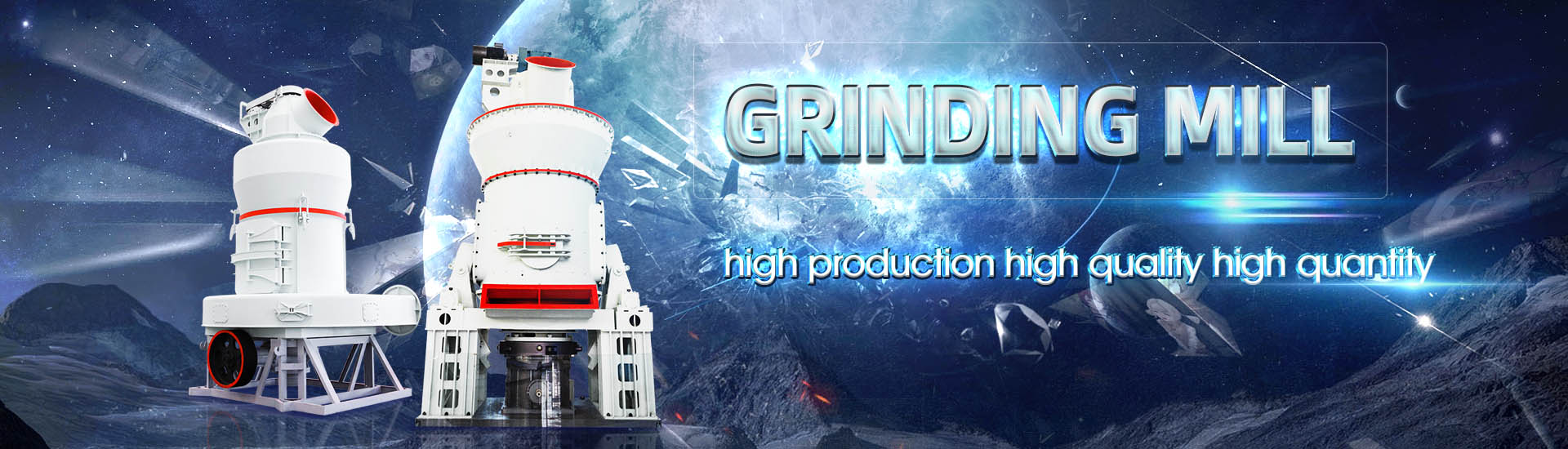
Is ore crushed during steelmaking
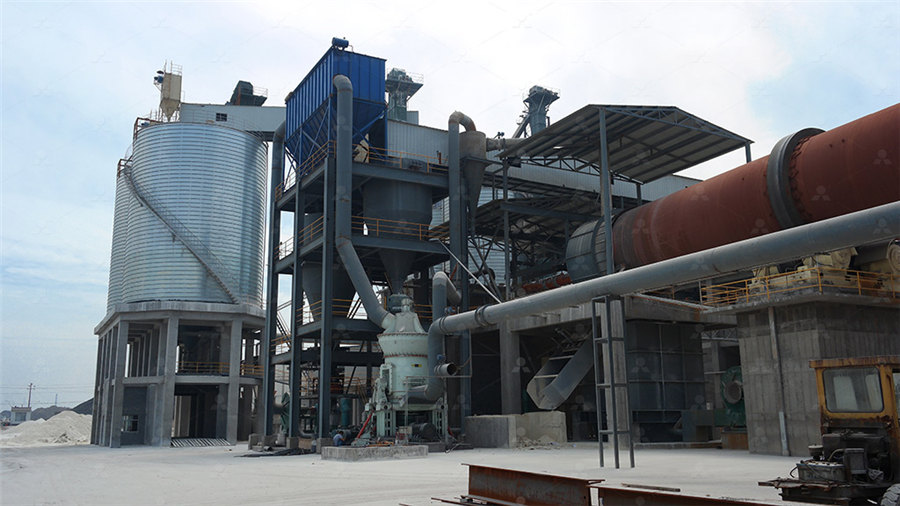
Iron Ore Processing: From Extraction to
2024年4月26日 Iron ore processing is a crucial step in the production of steel, one of the most essential materials in modern society Iron ore, a naturally occurring mineral composed primarily of iron oxides, is mined and processed 2024年1月1日 Pig iron and directreduction iron are primary resources with natural iron ore as raw material While scrap steel is a recycling resource, which belongs to secondary resources Steelmaking SpringerLinkThe blast furnace uses coke, iron ore and limestone to produce pig iron Coal traditionally has been a key part of the cokemaking process The coal is crushed and ground into a powder and then charged into an oven where it is heated to Steel Production American Iron and Steel 2017年7月20日 Steelmaking begins by the processing of iron ore The rock containing iron ore is crushed and pulverized to separate the gangue from the ore using magnetic rollers A coking furnace coal removes impurities and Technology and Processes Behind Steel
.jpg)
The recycling and reuse of steelmaking slags — A review
2019年7月1日 All iron ore that is mined has to be crushed, and if the particles are of suitable size are directly charged to a blast furnace; however, if the particles are too fine, then they are During the steelmaking process, various slags are produced as byproducts (Shen and Forssberg, 2003) The first stage of steel production is blast furnace steelmaking, in which raw iron ore is Steelmaking Process an overview ScienceDirect TopicsMaking steel doesn’t begin in the furnace or mold; it starts with extracting raw materials Notably, the first step would be extracting and processing the iron ore, the naturally occurring mineral from which Iron is extracted Iron ore makes up Exploring the Steelmaking Process: From Ore to 2024年3月20日 The steel making process involves several key stages: preparation of raw materials such as iron ore, coke, and limestone; smelting and reduction to produce molten iron; primary steelmaking which converts molten Unlock the Secrets of Steel: An InDepth Flow
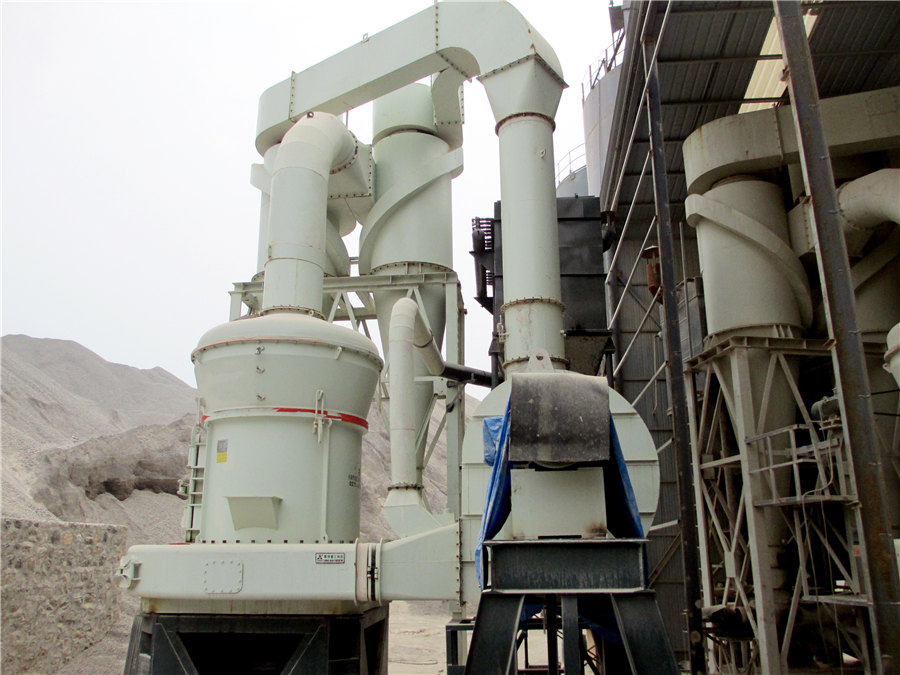
Raw Materials for Steelmaking SpringerLink
2020年3月3日 Main raw material for pneumatic or autogenous steelmaking processes is hot metal and pig iron and/or scrap/sponge iron is for nonautogenous steelmaking processes 2023年1月4日 After a long period of random discoveries, people also mastered the metallurgical processing of found ores For this they had to gain the technical ability to generate very high Steelmaking SpringerLink2014年8月9日 Inline continuous processing of highgrade hematite ore (crushed ore or fines) with a pure hydrogen reductant is assessed An appraisal is made of the rate controlling mechanisms involved in the reduction of a pure layer of molten wustite being transported by floating on a molten carrier iron carbonfree medium at temperatures just in excess of the iron Towards Zero CO2 Continuous Steelmaking Directly from Ore 2020年3月3日 Lime is generally added during steelmaking to make the slag basic enough to retain phosphorus and sulphur in the slag phase The pretreatment of hot metal is carried out for improving costeffectiveness in steelmaking by reducing the volume of slag Steel scrap acts as cooling material in steelmaking Iron ore also acts as cooling material Raw Materials for Steelmaking SpringerLink
.jpg)
Guide to Modern Smelting Processes CED Engineering
2024年4月21日 Guide to Modern Smelting Processes – T09002 3 • Environmental Impact: Smelting processes can have environmental consequences, including emissions of greenhouse gases and other pollutants Modern smelting endeavors to mitigate these impacts through cleaner technologies and sustainableDuring the steelmaking process, various slags are produced as byproducts (Shen and Forssberg, 2003) The first stage of steel production is blast furnace steelmaking, in which raw iron ore is converted into pig iron, which contains various amounts of Steelmaking Process an overview ScienceDirect Topics2022年5月1日 Basic oxygen furnace (BOF) slag is the main coproduct in the steelmaking process, its recycling within the iron and steel enterprises is crucial for the industry to ensure greater sustainabilitySeparation of Iron and Calcium from a BSSF Steelmaking 2024年1月4日 Steel manufacturing is a complex process that transforms iron ore into steel, involving precise heating and mixing to create different grades for various applications The journey includes primary methods like Basic Oxygen Steelmaking BOS and Electric Arc Furnace EAF, followed by secondary refining to meet specific quality standardsExploring Steel Manufacturing: A StepbyStep Insider Guide
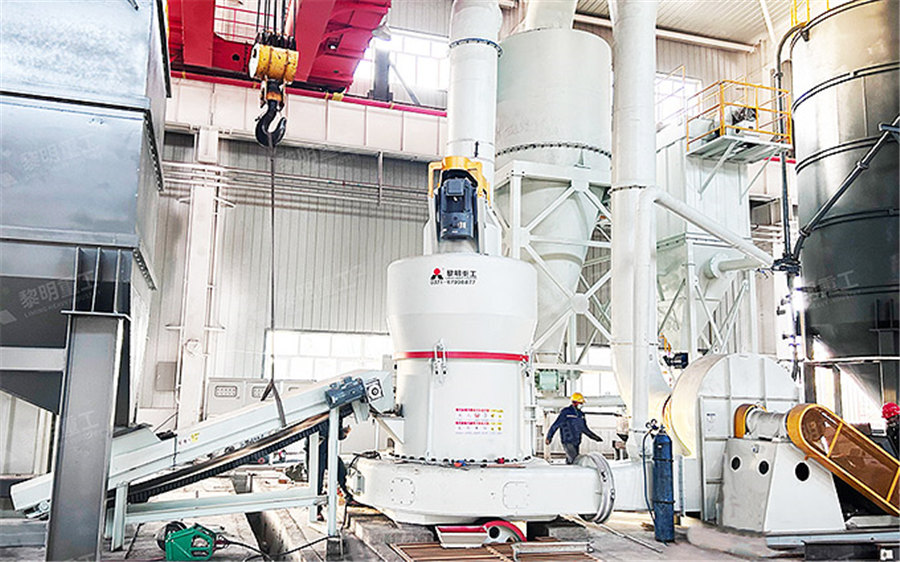
Can industry decarbonize steelmaking? Chemical
2021年6月13日 The process should lower carbon dioxide emissions in all stages of steelmaking, including pelletizing iron ore, reducing iron oxides to iron, and producing crude steel Source: Adapted from HYBRIT2024年10月21日 The particle size of lump ore was large, so it needed to be crushed by a jaw crusher, and it also was screened using roundhole after crushing, and the lump ore’s diameter ranging was 10–16 mm ZG, Zhao ZC, Liu PJ, Yan RJ (2022) Quantifying the energy saving potential and environmental benefit of hydrogenbased steelmaking process Reduction Behavior of Lump Ore and Its Applicability During 2017年3月22日 Sulphur removal in the ironmaking and oxygen steelmaking process is reviewed A sulphur balance is made for the steelmaking process of Tata Steel IJmuiden, the Netherlands(PDF) Sulphur removal in ironmaking and oxygen steelmaking 2024年11月19日 Steel Smelting, Alloying, Refining: In principle, steelmaking is a melting, purifying, and alloying process carried out at approximately 1,600° C (2,900° F) in molten conditions Various chemical reactions are initiated, either in sequence or simultaneously, in order to arrive at specified chemical compositions and temperatures Indeed, many of the reactions Steel Smelting, Alloying, Refining Britannica
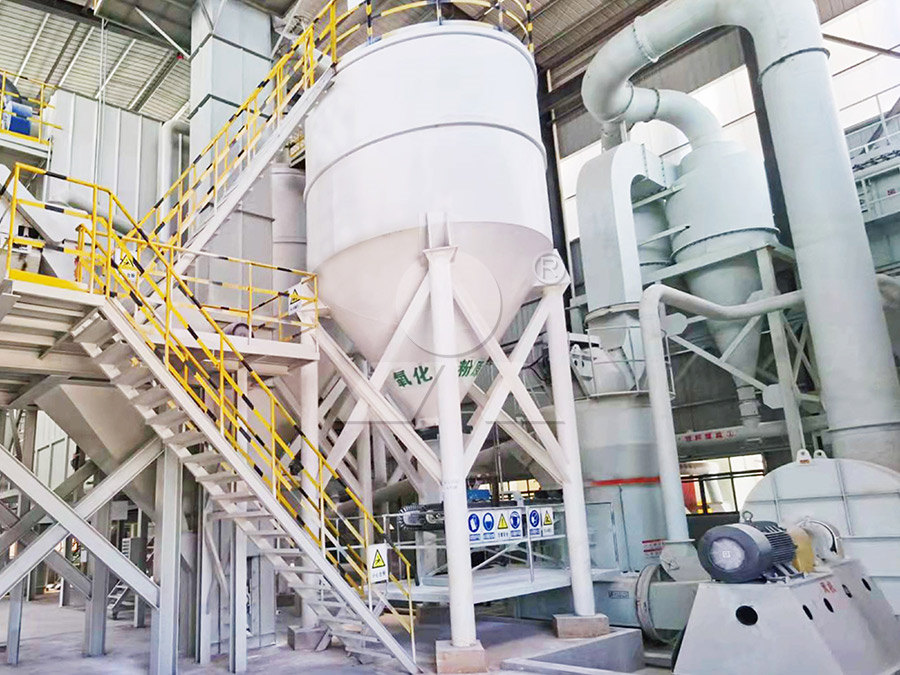
(PDF) Iron Ore Sintering: Process ResearchGate
2017年2月16日 Sintering is a thermal agglomeration process that is applied to a mixture of iron ore fines, recycled ironmaking products, fluxes, slagforming agents and solid fuel (coke)2023年4月16日 The extracted iron ore is then transported to processing plants, where it is crushed and turned into small pellets These pellets are then transported to steel mills for further processing The quality of iron ore is The Fascinating Journey of Steel Manufacturing2023年4月1日 To deal with the increasingly serious resource depletion and environmental problems [8, 9], the electric arc furnace (EAF) steelmaking process, in line with the highquality development concept and the two major themes of the green and intelligent innovation of the future ISI, served as an effective way to achieve the carbon neutral goal before 2060 during Life cycle carbon footprint of electric arc furnace steelmaking 2022年7月1日 1 Primary Steelmaking In primary steelmaking, raw iron from a blast furnace is used as the primary feedstock Basic oxygen steelmaking is a common method, where oxygen is blown through molten pig iron to reduce the carbon content, producing lowcarbon steel 2 Secondary Steelmaking Secondary steelmaking typically uses scrap steel as theThe Metallurgy Process Australian General Engineering
.jpg)
Exploring the Steelmaking Process: From Ore to Alloy
Iron ore makes up 5% of the Earth’s crust, which is why steel is humanity’s most famous building material Then, the iron ore is “smelted,” which includes melting the Iron in a blast furnace or electric arc furnace2024年7月30日 average of 125% slag is formed during steelmaking, the amount of steelmaking slag produced is 17491 million tons The estimation of total iron and steelmaking slags inIRON AND STEELMAKING SLAGS: ARE THEY 2024年8月2日 The beneficiation of lowgrade iron ores is a key research and development topic in the mineral processing industry The gradual exhaustion of highgrade iron ore reserves, and rising consumer iron and steel demand globally necessitate efficient lowquality iron ore beneficiation to meet steelmaking quality requirements This comprehensive review explores Exploring LowGrade Iron Ore Beneficiation Techniques: A2024年3月13日 When combined with other materials like iron ore and coke, it undergoes a series of chemical reactions in the blast furnace, resulting in the production of molten iron limestone also contributes to the steelmaking process by adjusting the composition of the steel About 12% of the total production of limestone during 2020–21 was of Limestone—A Review with Special Reference to the Iron and
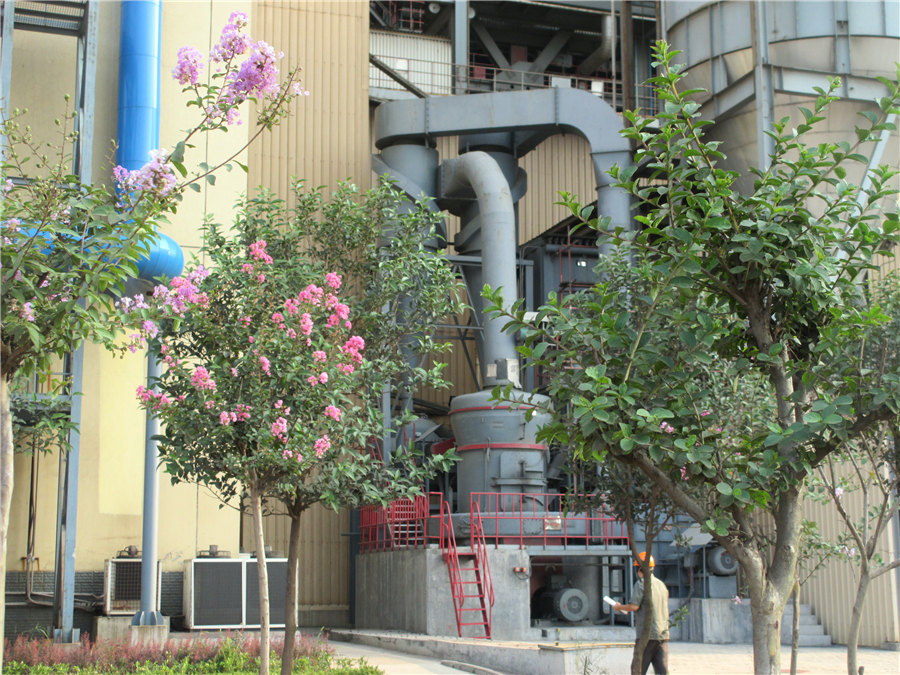
Why is manganese used in steelmaking? Steel Standart
2023年2月5日 The most common method is to add manganese ore to the steel during the manufacturing process This is done by adding the ore to the molten steel before it is poured into molds brittle, graywhite metal that is found in nature as an ore Manganese is used in steelmaking as an alloying agent, which helps to improve the strength, hardness 2020年6月10日 The major charge materials in blast furnace are sinter or pellets iron ore and limestone, and the ascending gas CO is a product of combustion of carbon (coke) in tuyere region Iron ore (Fe 2 O 3, Fe 3 O 4) is reduced to FeO in lower stack and bosh area All the raw materials are charged from furnace throat and hot air is purged through the Iron and SteelMaking Process SpringerLink2015年1月1日 Like other sintering processes, iron ore sintering converts iron ore fines of often − 8 mm sizing into larger agglomerates, namely, sinter, between 5 and 50 mm particle size, which possess the physical and metallurgical characteristics and gas permeability required for efficient blast furnace operationAs shown in Figure 141, iron ore sintering is carried out in three Iron ore sintering ScienceDirect2019年6月11日 The remaining 2% of domestic iron ore was produced for nonsteel end uses Seven openpit iron ore mines (each with associated concentration and pelletizing plants), and three iron metallic plants—one direct Sintering: A Step Between Mining Iron Ore and
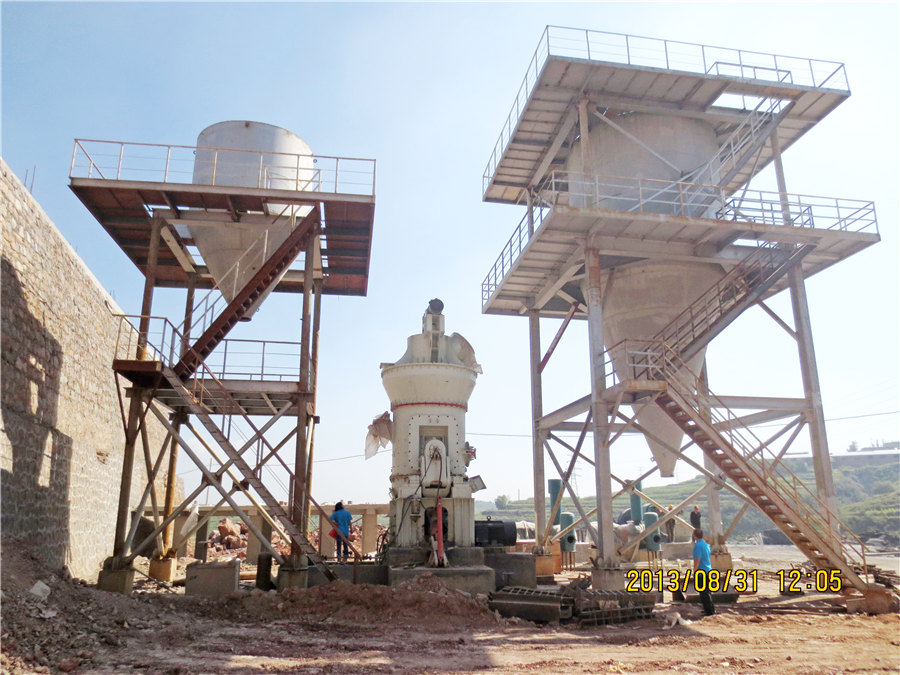
Steelmaking Slag an overview ScienceDirect Topics
Steelmaking slag, or steel slag, is a byproduct from the production of steel during the conversion of hot metal to crude steel in a basic oxygen furnace, or during the melting of scrap in an EAFThe slag is generated as a melt and is a complex solution of silicates and oxides that solidify upon cooling 11 Depending on the specific steel production process, three different types of steel Basic oxygen steelmaking (BOS) slag, a product of hot metal element (eg, Si, Mn, Fe, P) oxidation and flux (eg lime, dolomite) dissolution, plays a critical role in the production of highquality crude steel, although its behavior inside the BOS vessel (formation and reaction with metal droplets and gas) is still not clear and its recycling has always been challengingBasic Oxygen Steelmaking Slag: Formation, Reaction, and 2022年10月20日 Iron ore handling, which may account for 20–50% of the total delivered cost of raw materials, covers the processes of transportation, storage, feeding, and washing of the ore en route to or during its various stages of treatment in the mill Since the physical state of iron ores in situ may range from friable, or even sandy materials, to monolithic deposits with hardness of Iron Ore Processing, General SpringerLink2022年1月1日 The sintering process begins with preparation of a sinter mixture consisting of iron ore fines, fluxes, solid fuel (called bonding agents in Japan) such as coke breeze, and return fines from the sinter plant as well as recycled ferruginous materials from downstream iron and steelmaking processesIron ore sintering ScienceDirect
.jpg)
The Steelmaking Flow Chart: A Roadmap to Efficient
2024年6月9日 The article explains the importance of understanding a steelmaking flow chart, which outlines each step from raw material preparation to final products, aiding in efficiency and productivity It details key components like raw materials iron ore, limestone, coal, primary steps raw material prep, ironmaking, steelmaking, and methods such as Basic Oxygen Furnace BOF 2024年1月1日 The history of electric steelmaking is quite short—only a little over 100 years from the first trials to melt steel by utilizing electric powerDuring that period, great advancements have been attained both in furnace equipment and technology, Electric Furnace Steelmaking ScienceDirect2024年3月20日 The steel making process involves several key stages: preparation of raw materials such as iron ore, coke, and limestone; smelting and reduction to produce molten iron; primary steelmaking which converts molten iron to steel using methods like the Basic Oxygen Furnace (BOF) or Electric Arc Furnace (EAF); casting where steel is formed into semifinished Unlock the Secrets of Steel: An InDepth Flow Diagram 2014年8月9日 Inline continuous processing of highgrade hematite ore (crushed ore or fines) with a pure hydrogen reductant is assessed An appraisal is made of the rate controlling mechanisms involved in the reduction of a pure layer of molten wustite being transported by floating on a molten carrier iron carbonfree medium at temperatures just in excess of the iron Towards Zero CO2 Continuous Steelmaking Directly from Ore
.jpg)
Raw Materials for Steelmaking SpringerLink
2020年3月3日 Lime is generally added during steelmaking to make the slag basic enough to retain phosphorus and sulphur in the slag phase The pretreatment of hot metal is carried out for improving costeffectiveness in steelmaking by reducing the volume of slag Steel scrap acts as cooling material in steelmaking Iron ore also acts as cooling material 2024年4月21日 Guide to Modern Smelting Processes – T09002 3 • Environmental Impact: Smelting processes can have environmental consequences, including emissions of greenhouse gases and other pollutants Modern smelting endeavors to mitigate these impacts through cleaner technologies and sustainableGuide to Modern Smelting Processes CED EngineeringDuring the steelmaking process, various slags are produced as byproducts (Shen and Forssberg, 2003) The first stage of steel production is blast furnace steelmaking, in which raw iron ore is converted into pig iron, which contains various amounts of Steelmaking Process an overview ScienceDirect Topics2022年5月1日 Basic oxygen furnace (BOF) slag is the main coproduct in the steelmaking process, its recycling within the iron and steel enterprises is crucial for the industry to ensure greater sustainabilitySeparation of Iron and Calcium from a BSSF Steelmaking

Exploring Steel Manufacturing: A StepbyStep Insider Guide
2024年1月4日 Steel manufacturing is a complex process that transforms iron ore into steel, involving precise heating and mixing to create different grades for various applications The journey includes primary methods like Basic Oxygen Steelmaking BOS and Electric Arc Furnace EAF, followed by secondary refining to meet specific quality standards2021年6月13日 The process should lower carbon dioxide emissions in all stages of steelmaking, including pelletizing iron ore, reducing iron oxides to iron, and producing crude steel Source: Adapted from HYBRITCan industry decarbonize steelmaking? Chemical2024年10月21日 The particle size of lump ore was large, so it needed to be crushed by a jaw crusher, and it also was screened using roundhole after crushing, and the lump ore’s diameter ranging was 10–16 mm ZG, Zhao ZC, Liu PJ, Yan RJ (2022) Quantifying the energy saving potential and environmental benefit of hydrogenbased steelmaking process Reduction Behavior of Lump Ore and Its Applicability During 2017年3月22日 Sulphur removal in the ironmaking and oxygen steelmaking process is reviewed A sulphur balance is made for the steelmaking process of Tata Steel IJmuiden, the Netherlands(PDF) Sulphur removal in ironmaking and oxygen steelmaking