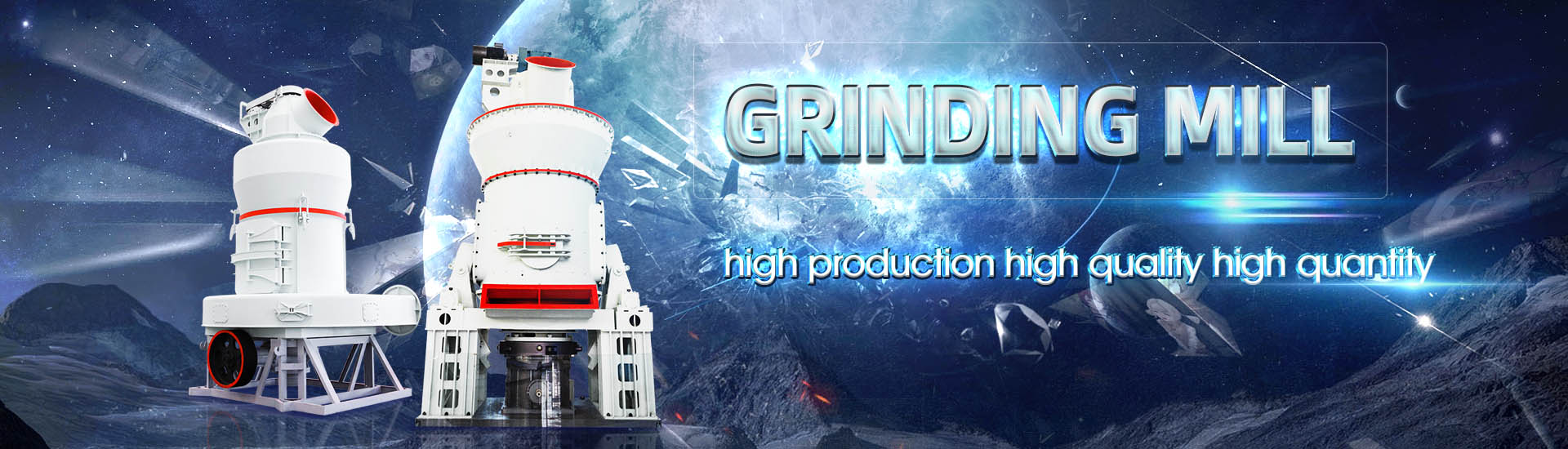
Ore grinding mill processing capacity
.jpg)
Ore Grinding SpringerLink
2023年7月20日 In order to improve the processing capacity of the autogenous mill (especially the wet autogenous mill) and reduce power consumption, a small amount of steel balls (accounting for 2–12% of the autogenous mill volume) can be loaded to the autogenous mill to 2023年7月31日 In order to improve the processing capacity of the autogenous mill (especially the wet autogenous mill) and reduce power consumption, a small amount of steel balls Ore Grinding Methods and Process of Ore Grinding2020年5月1日 The problem of lowgrade ore cost and a low utilization rate can be effectively solved by employing a largescale ball mill Therefore, effectively improving the grinding Enhancing the capacity of largescale ball mill through process 2023年9月1日 Based on the machine learning method, this study analyzed the full process parameters (ie, ball mill power, fresh ore feed rate, hydrocyclone feed pump power, Analyzing process parameters for industrial grinding circuit
.jpg)
MultiObjective Optimization for an Industrial Grinding and
2023年9月28日 In order to stabilize the grinding index and improve grinding capacity in the process, a process model based on population balance model (PBM) is calibrated in this study2022年6月6日 The present work aims to assess additional capacity scenarios for processing the Cristalino ore in the Sossego industrial grinding circuit by adjusting the SAG mill fresh feed size distribution, as resulting from the PreProcessing to Increase the Capacity of SAG 2023年10月17日 Production capacity: Determine the required processing capacity of the ore powder grinding mill according to production needs to ensure production efficiency and capacity 3 Grinding accuracy: Select the grinding How to choose a suitable ore powder grinding With the improvement of mining efficiency and the merger of surrounding mineral rights, the underground ore lifting capacity is further improved The existing mineral processing Feasibility Test Study on Increasing Ore Processing Capacity
.jpg)
Research on Grinding Law and Grinding
2022年10月13日 The factors affecting the grinding process mainly include ore properties and operating conditions The hardness, density, brittleness, mud content, distribution characteristics, particle size, grinding fineness and other 2019年4月25日 How closely the optimum grind actually approaches the maximumrecovery grind depends on the following factors: In any plant, considerable fluctuation normally occurs Optimizing Grinding and Regrinding Capacity in Mill Design2024年10月13日 Autogenous mills use the ore itself as the grinding media, while semiautogenous mills use a combination of ore and steel balls These mills operate by rotating a large drum filled with the ore, which impacts and grinds the particles against the mill walls Autogenous and semiautogenous mills are more energyefficient and are suitable for fine Understanding the operation of grinding mills in the mining 2024年10月17日 The processing capacity of the ball mill is closely related to its rotation speed and the volume of the cylinderIt can usually be calculated by the following formula: processing capacity = π × cylinder volume × ore bulk weight × grinding load factor ÷ grinding cycleAmong them, π is the pi (314), and the volume of the cylinder can be What is the processing capacity of the ball mill?How to
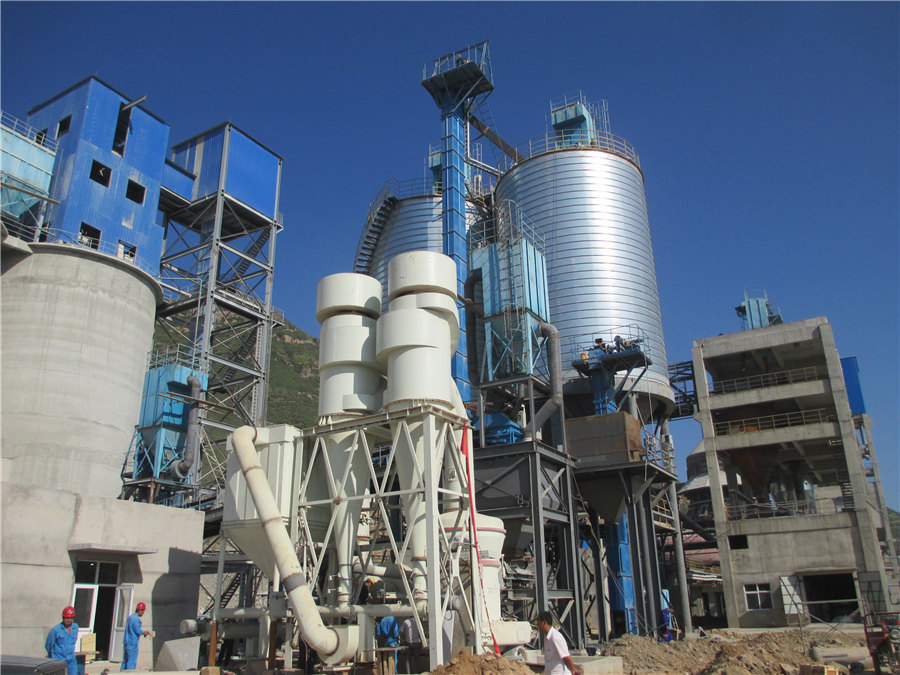
High Pressure Grinding Roll and Magnetic Separation for
2024年6月20日 after the thirdstage ne crushing operation to reduce the particle size of ball mill feed and improve the processing capacity of grinding operation The optimal process parameters of high pressure grinding roll and magnetic separation were determined the yield of coarse tailings was 3616%, which signicantly reduced the amount of ore Grinding Mills Barry A Wills, James A Finch FRSC, FCIM, PEng, in Wills' Mineral Processing Technology (Eighth Edition), 2016 71 Introduction Grinding is the last stage in the comminution process where particles are reduced in size by a combination of impact and abrasion, either dry, or more commonly, in suspension in waterGrinding Mill an overview ScienceDirect Topics2024年8月15日 Ideal for coarse ore grinding, preventing overgrinding Low Autogenous mill: Very hard, highly abrasive large ores Uses the ore's impact for grinding, reducing wear on equipment and grinding media The ROI period depends on the type and value of the ore, processing capacity, equipment investment, and operating costs While large plants Mineral Processing Plants: What You Need to Know2016年6月6日 Based on experience, millliner designs have moved toward more openshell lifter spacing, increased pulp lifter volumetric capacity, and a grate design to facilitate maximizing both pebblecrushing circuit utilization and SAG mill capacity As a guideline, mill throughput is maximized with shell lifters between ratios of 25:1 and 50:1SAG Mill Grinding Circuit Design 911Metallurgist
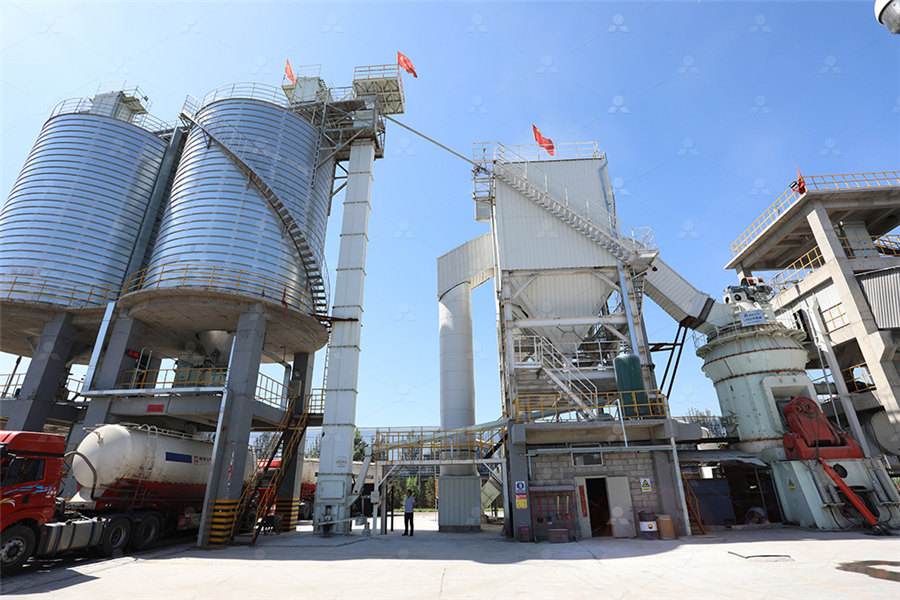
Comminution and classification technologies of iron ore
2022年1月1日 High pressure grinding rolls (HPGR) technology was introduced to the minerals processing industry in the mid 1980s and has rapidly (for the mining industry) established itself as the convention in the comminution of cement, clinker, slag, iron ore, iron ore 2016年2月14日 Do you need a quick estimation of a ball mill's capacity or a simple method to estimate how much can a ball mill of a given size (diameter/lenght) grind for 911 Metallurgist is a trusted resource for practical insights, solutions, and support in mineral processing engineering, helping industry professionals succeed with proven expertise Small Ball Mill Capacity Sizing Table 911Metallurgist2024年9月22日 Improved Grind Quality: The larger volume of ore processed per unit of time in high capacity ball mills allows for a more consistent and uniform grind This results in a higher quality of the final product, with smaller particle sizes and better liberation, which is essential for efficient iron ore beneficiation and pelletizationEnhancing iron ore grinding efficiency with high capacity ball mills2023年9月1日 After threestage crushing and onestage closedcircuit screening process, the ore particle size d80 is maintained at 10 mm The grinding circuit process comprises a ball mill (d = 55 m), a pump sump, a hydrocyclone cluster consists of six hydrocyclones (d = 660 mm), and related pumps and belt conveyorsAnalyzing process parameters for industrial grinding circuit
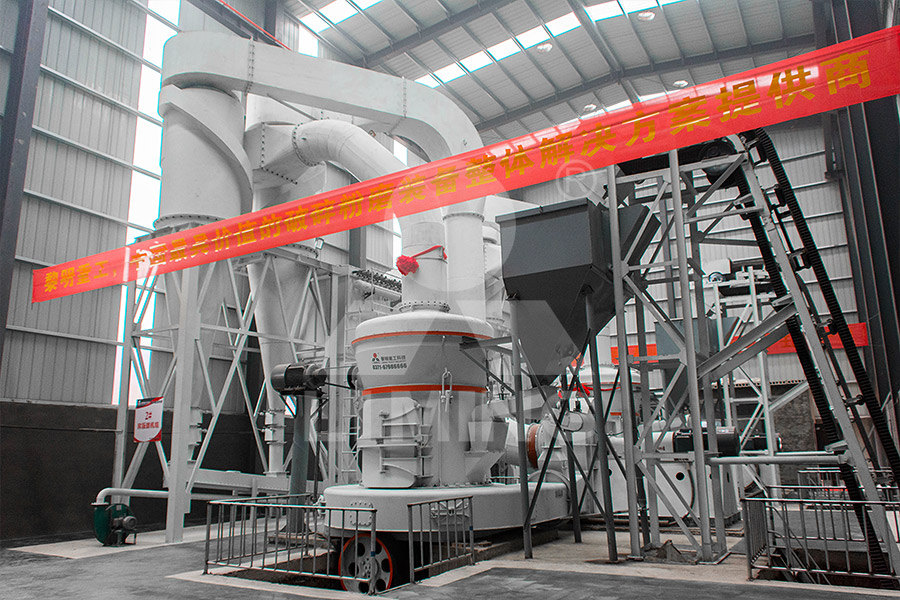
Calculate Ball Mill Grinding Capacity
2015年10月15日 A) Total Apparent Volumetric Charge Filling – including balls and excess slurry on top of the ball charge, plus the interstitial voids in between the balls – expressed as a percentage of the net internal mill volume (inside 2024年7月8日 Durable construction, high capacity, and efficient reduction of ore size: Used in the initial stage to break down large chunks of ore into manageable sizes for further processing Ball Mill: Efficient grinding, adjustable particle Mastering Oxidized Gold Ore Processing 2016年11月7日 In Fig 13 is shown a large ball mill, designed for the dry grinding of limestone, dolomite, quartz, refractory and similar materials; this type of mill being made in a series of sizes having diameters ranging from about 26 in to 108 in, with the corresponding lengths of drum ranging from about 15 in to 55 inGrinding Mills Common Types 911MetallurgistIn the quicklime grinding plant case, the customer using our HGM grinding mill as a stone dust making machine to process quicklime (calcium oxide) and calcium carbonate into a fine, 325 mesh powder 2024 1029SBM Ultrafine Powder Technology Industrial Grinding Mill,
.jpg)
How Ball Mill Ore Feed Size Affects Tonnage Capacity
2017年7月26日 Crushing and milling circuit control systems that balance the crushing plant output to the grinding mill capacity will maximize plant capacity at the lowest production cost Properly applied, the technology described will reduce the magnitude of the overdesign parameters used in most comminution plant design calculations2023年7月19日 Ore grindability is mainly used to calculate and select the specifications, models, processing capacity, and number of grinding mills, and to determine whether the grinding mills work in proper conditions It is important raw data in the concentrator design and productionOre Grindability SpringerLink2023年11月1日 Grinding operation is the last preparation stage before beneficiation In this stage, the material undergoes the combined action of impact and grinding, so that the ore particle size is diminished and the qualified materials is provided for succeeding beneficiation operations [1, 2]Generally, the quality of the grinding product is also an important factor to determine the Energy conservation and consumption reduction in grinding 2018年8月17日 SemiAutogenous Mills/ SAG Mills (primary grinding mill) — these mills use grinding balls with forces of attrition, impact, and abrasion between grinding balls and ore particles that result in Grinding Mills — Types, Working Principle Applications
.jpg)
Ore Crushing, Sand Making, Grinding Machinery Bellian
1 天前 At Bellian Mining Machinery, we specialize in crafting advanced solutions for ore crushing, sand making, and grinding processes Whether it's efficiently crushing ores, creating highquality sand for construction, or precision grinding for various applications, Choose Bellian Mining Machinery for all your mining and processing needs, where technology and excellence 2023年10月9日 The ball mill works on the principle of impact and attrition: size reduction is done by impact as the balls drop from near the top of the shell You can apply our ball mill in ore beneficiation plant to grind iron ore, copper ore, Ball Mill Ball Grinding Mill SKE2020年5月1日 The problem of lowgrade ore cost and a low utilization rate can be effectively solved by employing a largescale ball mill Therefore, effectively improving the grinding efficiency and processing capacity of largescale mills is a crucial research topic for concentrators [7], [8]Enhancing the capacity of largescale ball mill through process It can be judged from process mineralogy data that the ore belongs to easytoselect ore The crushing process of the concentrator adopts a threestage closedcircuit crushing process of conventional coarse crushing open circuit + medium fine crushing closedcircuit screening (Chang 2017); grinding using a ball mill + cyclone classification Feasibility Test Study on Increasing Ore Processing Capacity
.jpg)
A Review of the Grinding Media in Ball Mills for Mineral Processing
2023年10月27日 The ball mill is a rotating cylindrical vessel with grinding media inside, which is responsible for breaking the ore particles Grinding media play an important role in the comminution of mineral ores in these mills This work reviews the application of balls in mineral processing as a function of the materials used to manufacture them and the mass loss, as 2019年4月25日 However, since grinding is usually by far the most expensive unit operation in a concentrator, the grinding capacity is normally designed for average rather than extreme conditions, with provisions for varying the feed rate and fineness of grind to utilize the capacity of the grinding circuit as fully as possible as the ore variesOptimizing Grinding and Regrinding Capacity in Mill Design2023年4月23日 Grinding media are the main components of the grinding process involving a ba ll mill Research has been done to Research has been done to select the most su itable ma terials to manufacture (PDF) Grinding Media in Ball MillsA Review ResearchGate2018年10月17日 The ball mill (BALL grinding) is 834 m in diameter and 1326 m in length Its capacity 78206 cubic meters The operating load is 1,272 tons The mill is fed 80mm steel grinding balls The mill grinding performance might be up to 3,100 tons of ore per hour The grinding balls charged to these mills are characterized with a greater impact GRINDING MILLS CHAMPIONS World's biggest Grinding mills
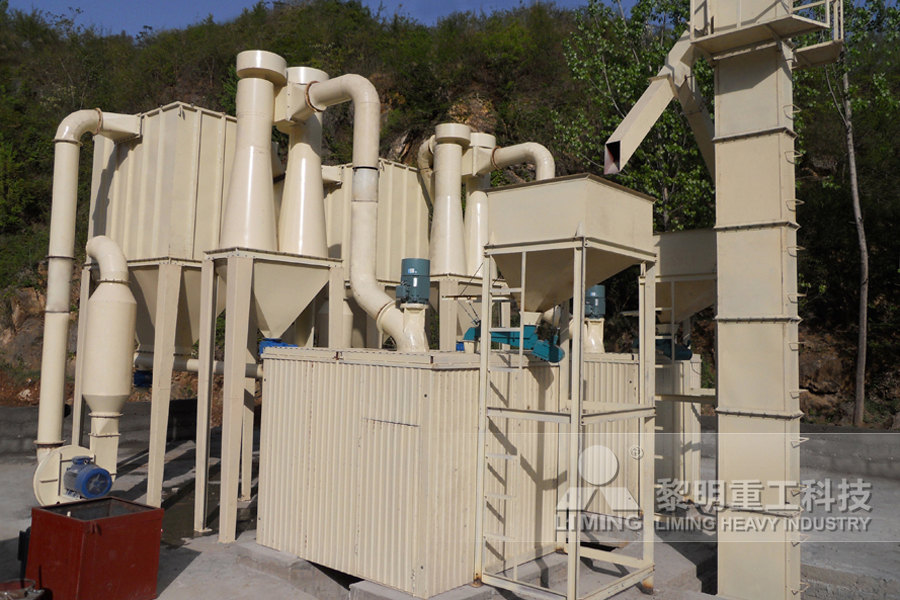
Ball Mill Design/Power Calculation 911Metallurgist
2015年6月19日 The basic parameters used in ball mill design (power calculations), rod mill or any tumbling mill sizing are; material to be ground, characteristics, Bond Work Index, bulk density, specific density, desired mill tonnage capacity DTPH, operating % solids or pulp density, feed size as F80 and maximum ‘chunk size’, product size as P80 and maximum and finally the type of 2021年11月8日 Illite ore industrial grinding mill machine can grind illite into powder up to 3000 mesh, including ultrafine mill, vertical mill, Raymond mill, wet mill, etc The equipment has the characteristics of a small footprint, simple operation, convenient maintenance, large processing capacity, energysaving, and consumption reduction Illite Ore Industrial Grinding Mill Machine SBM Ultrafine 2023年11月24日 Grinding media are the main components of the grinding process involving a ball mill For sulfide ore, inert grinding media such as ceramic ball or pebbles have shown a superior performance to steel pebbles This is due to the sulfide mineral surface being covered by the iron hydroxides produced by oxidation, Grinding Media in Ball Mills for Mineral Processing2024年10月13日 Autogenous mills use the ore itself as the grinding media, while semiautogenous mills use a combination of ore and steel balls These mills operate by rotating a large drum filled with the ore, which impacts and grinds the particles against the mill walls Autogenous and semiautogenous mills are more energyefficient and are suitable for fine Understanding the operation of grinding mills in the mining
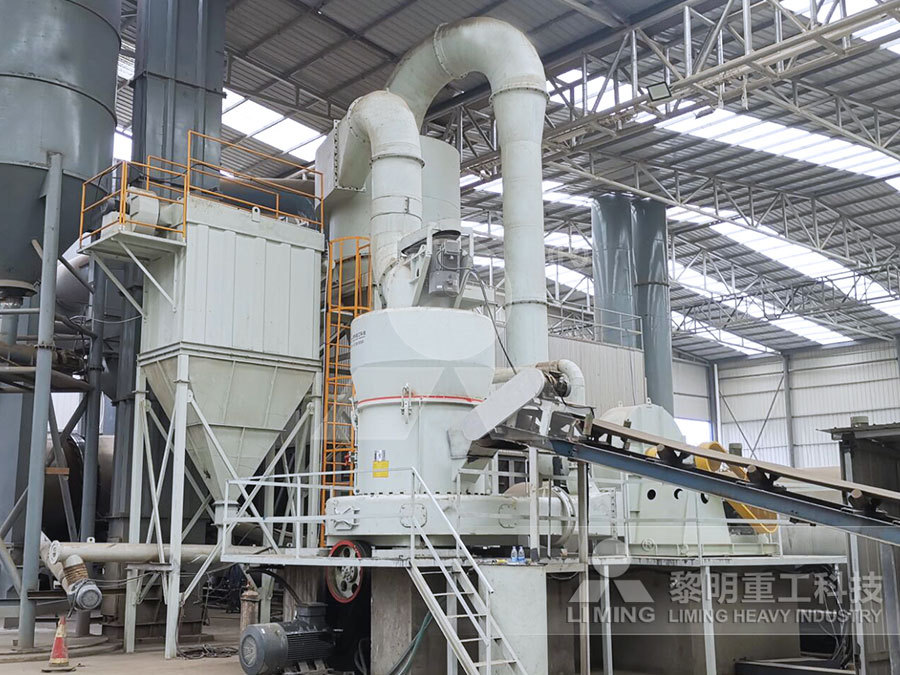
What is the processing capacity of the ball mill?How to
2024年10月17日 The processing capacity of the ball mill is closely related to its rotation speed and the volume of the cylinderIt can usually be calculated by the following formula: processing capacity = π × cylinder volume × ore bulk weight × grinding load factor ÷ grinding cycleAmong them, π is the pi (314), and the volume of the cylinder can be 2024年6月20日 after the thirdstage ne crushing operation to reduce the particle size of ball mill feed and improve the processing capacity of grinding operation The optimal process parameters of high pressure grinding roll and magnetic separation were determined the yield of coarse tailings was 3616%, which signicantly reduced the amount of ore High Pressure Grinding Roll and Magnetic Separation for Grinding Mills Barry A Wills, James A Finch FRSC, FCIM, PEng, in Wills' Mineral Processing Technology (Eighth Edition), 2016 71 Introduction Grinding is the last stage in the comminution process where particles are reduced in size by a combination of impact and abrasion, either dry, or more commonly, in suspension in waterGrinding Mill an overview ScienceDirect Topics2024年8月15日 Ideal for coarse ore grinding, preventing overgrinding Low Autogenous mill: Very hard, highly abrasive large ores Uses the ore's impact for grinding, reducing wear on equipment and grinding media The ROI period depends on the type and value of the ore, processing capacity, equipment investment, and operating costs While large plants Mineral Processing Plants: What You Need to Know
.jpg)
SAG Mill Grinding Circuit Design 911Metallurgist
2016年6月6日 Based on experience, millliner designs have moved toward more openshell lifter spacing, increased pulp lifter volumetric capacity, and a grate design to facilitate maximizing both pebblecrushing circuit utilization and SAG mill capacity As a guideline, mill throughput is maximized with shell lifters between ratios of 25:1 and 50:12022年1月1日 High pressure grinding rolls (HPGR) technology was introduced to the minerals processing industry in the mid 1980s and has rapidly (for the mining industry) established itself as the convention in the comminution of cement, clinker, slag, iron ore, iron ore Comminution and classification technologies of iron ore2016年2月14日 Do you need a quick estimation of a ball mill's capacity or a simple method to estimate how much can a ball mill of a given size (diameter/lenght) grind for 911 Metallurgist is a trusted resource for practical insights, solutions, and support in mineral processing engineering, helping industry professionals succeed with proven expertise Small Ball Mill Capacity Sizing Table 911Metallurgist2024年9月22日 Improved Grind Quality: The larger volume of ore processed per unit of time in high capacity ball mills allows for a more consistent and uniform grind This results in a higher quality of the final product, with smaller particle sizes and better liberation, which is essential for efficient iron ore beneficiation and pelletizationEnhancing iron ore grinding efficiency with high capacity ball mills