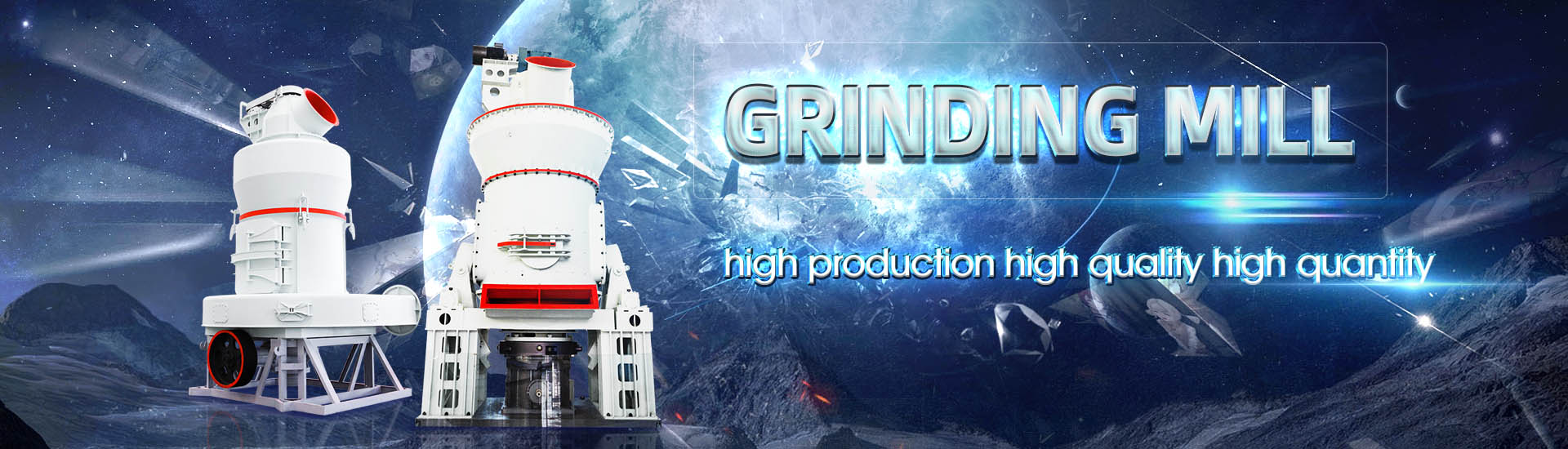
Vertical grinding ore grinding mill particle size
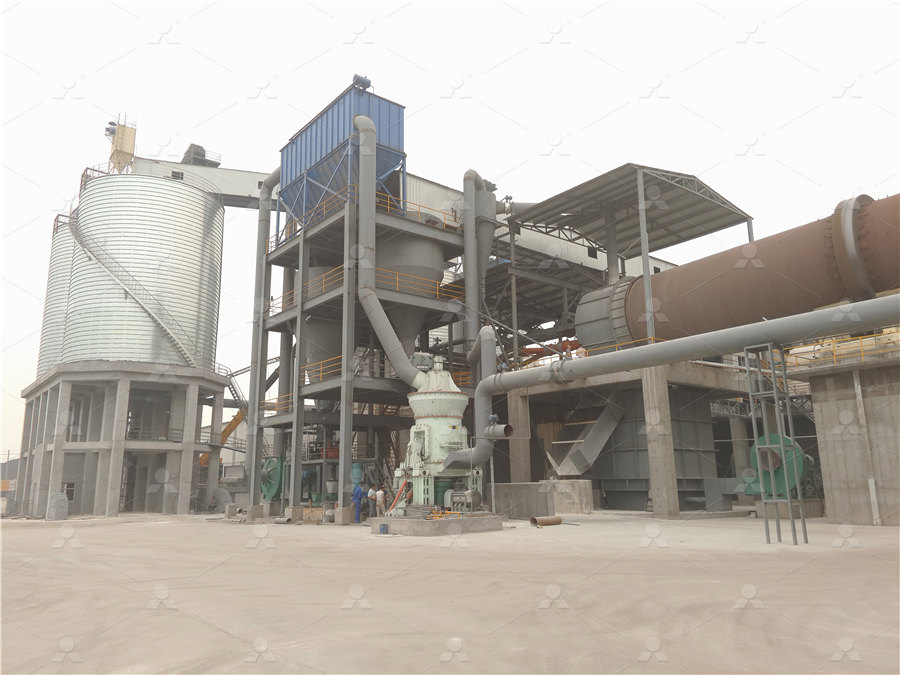
Predicting the grinding energy of vrm depending on material
2021年9月1日 Feed size, product size and energy data from pilot scale grinding tests were evaluated with material characterization tests Based on energysize reduction models 2023年9月21日 STM Minerals introduced the VPMTM (Vertical Power Mill), which is a further development of the industry leading VRMTM technology The VPMTM has a wider grinding RECENT DEVELOPMENTS IN COARSE GRINDING USING particle properties such as size, shape, mineralogy, and texture For instance, the largest and smallest particles in a tumbling mill generally break at lower rates than intermediatesize All About Particles: Modelling Ore Behaviour in Mineral In the present study, size reduction experiments were performed on HighPressure Grinding Rolls (HPGR), ball mill and stirred mill of PGE bearing chromite ore The performance of HPGR wasParticle size distributions of the pilot vertical mill
.jpg)
Stirred media mills in the mining industry: Material
2020年6月1日 Stirred media mills are used by the mining industry for ultrafine grinding to enhance liberation, and to decrease particle sizes of industrial minerals to tailor functional 2017年9月1日 Particle size distribution (PSD) is a key factor in size reduction processes These processes are widely used worldwide and in the Colombian industry However, they represent [PDF] Fine grinding: How mill type affects particle shape 2017年3月4日 Tower mills, often called vertical mills, s tirred mills or regrind mills, are a more efficien t means of grinding material at smaller particle sizes, and can be used after ball mills in a grin(PDF) SIZE REDUCTION BY GRINDING METHODS 2024年8月29日 This study aims to investigate the effect of the stirrer speed, the density and the size of the grinding media on the shape of the PSD and on the grinding rate The results show The effects of processing parameters on the shape of particle size
.jpg)
Predicting the product particle size distribution from a
2018年12月1日 The first stirred vertical mill was developed in Japan by the Japan Tower Mill Company Ltd which was later renamed to Kubota Tower Mill Corporation, KTM The Japanese Tower Mill was the first vertical grinding mill to be used in the mining industry (Stief et al, 1987) The Tower Mill® is now produced by NipponEirich2021年11月8日 Illite ore industrial grinding mill machine can grind illite into powder up to 3000 mesh, including ultrafine mill, vertical mill, Raymond mill, wet mill, etc because of its small particle size, large specific surface area, and Illite Ore Industrial Grinding Mill Machine SBM 2023年9月21日 Figure 3: Relationship between feed size (F80) and Bond efficiency factor (Huang et al, 2019) VERTICAL POWER MILL (VPM) – PRINCIPLE OF OPERATION Declining ore grades and more complex ore bodies, as well as waste management and global net zero initiatives, lead to a clear trend for high tonnage yet energy efficient grindingRECENT DEVELOPMENTS IN COARSE GRINDING USING Grinding tests were conducted using a pearshaped ball mill on an oxidized coppercobalt ore to determine the milling parameters Twelve monosized fractions of the ore sample were prepared and Particle size distributions of the pilot vertical mill circuit feeds
.jpg)
Grinding Mill ultrafine grinding mill, vertical ultrafine mill
4 天之前 LUM ultrafine vertical mill is designed for nonmetallic mineral ultrafine grinding equipment For limestone, calcite, dolomite Mohs hardness of 6 or less nonflammable, nonexplosive brittle material grinding The raw materials of suitable particle size are continuously and evenly sent to main mill by the skirt belt feeder for grinding 2019年4月16日 Vertical roller mills, VRMs, are widely used for grinding raw materials in factories engaged in the extraction and processing of minerals Any machine used for grinding or crushing consumes around (PDF) LEARNING FROM OTHER INDUSTRIES; WHY THE VRM 2015年3月15日 The grinding parts of a Loesche mill (Fig 1) are a rotating table (1) with a horizontal grinding track and rollers (2), which are pressed onto the table by lever arms and a hydro pneumatic spring systemBetween the working surfaces of track and rollers, particle bed comminution takes place A dynamic air separator (3) is located above the grinding chamber, Research of iron ore grinding in a verticalrollermill2020年10月1日 Several comminution laws have been proposed to link the consumed energy to a characteristic particle size of the powder The popular models are those of Rittinger [4], Bond [5] and Kick [6]While the Bond and Kick models are mostly employed for coarse and intermediate size grinding, the Rittinger model is better suited for fine comminution [7]This model assumes Evolution of grinding energy and particle size during dry ball
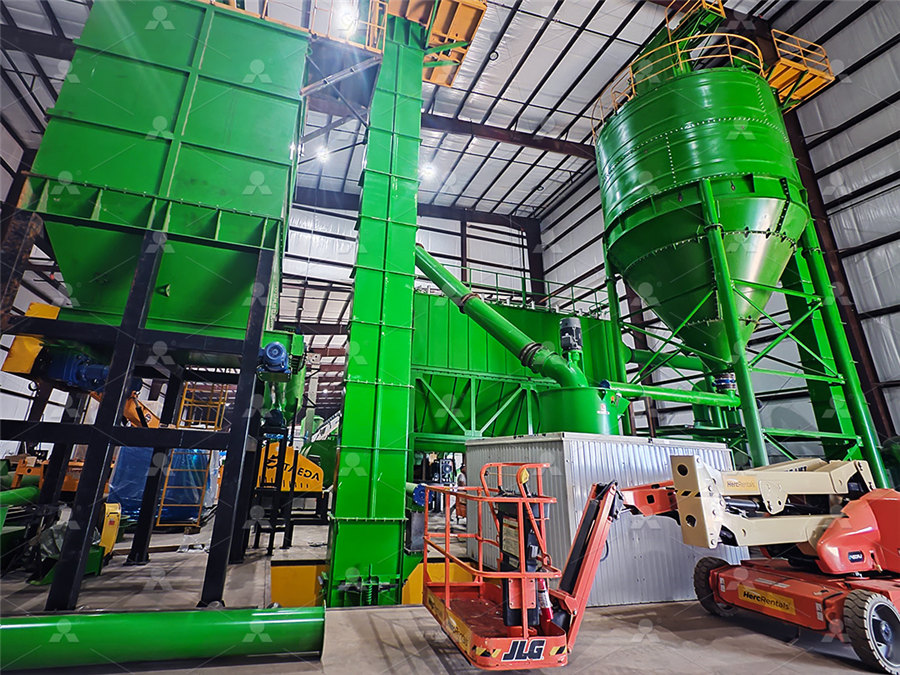
Ore Grinding SpringerLink
2023年7月20日 In the mineral processing industry, ore grinding is the particle size preparation before the separation of the crushed ore Except those that process some placers, almost all mineral processing plants have grinding operations, in which materials are crushed by the impact and abrasive action of grinding medium (steel rod, steel ball, gravel, or 2014年10月1日 Based on final particle size, time consumption, parameters of the grinding process, grinding media, assumed particle size, and type of material used, we identify various types of mills that have Copper Ore Grinding in a Mobile Vertical Roller Mill Pilot PlantDOI: 101016/JMINENG201809016 Corpus ID: ; Predicting the product particle size distribution from a laboratory vertical stirred mill @article{Rocha2018PredictingTP, title={Predicting the product particle size distribution from a laboratory vertical stirred mill}, author={Danielle Campos Rocha and Erik Spiller and Patrick R Taylor and Hugh B Miller}, Predicting the product particle size distribution from a DOI: 101016/JMINENG201705007 Corpus ID: ; Fine grinding: How mill type affects particle shape characteristics and mineral liberation @article{Little2017FineGH, title={Fine grinding: How mill type affects particle shape characteristics and mineral liberation}, author={Lucy Little and Aubrey Njema and Megan Mainza and Jenny Becker and Wiese}, journal={Minerals [PDF] Fine grinding: How mill type affects particle shape
.jpg)
Grinding Mill an overview ScienceDirect Topics
Grinding Mills Barry A Wills, James A Finch FRSC, FCIM, PEng, in Wills' Mineral Processing Technology (Eighth Edition), 2016 71 Introduction Grinding is the last stage in the comminution process where particles are reduced in size by a combination of impact and abrasion, either dry, or more commonly, in suspension in water2020年1月3日 Ball mills are progressively used to grind the ores for particle size reduction and to liberate valuable minerals from the ores The grinding of ore is a highly energyintensive process [1,2,3,4] In this process, the size of the particle obtained depends on the energy consumption of the ball millEstimation of Grinding Time for Desired Particle Size 2015年3月10日 Copper ore grinding in a mobile vertical roller mill pilot plant Author links open overlay panel Deniz Altun a, Carsten Gerold b, Hakan Benzer a, Okay Altun a, Namık Aydogan a Show more It is wellunderstood that grinding for particle size reduction and liberation is the essential step prior to ore concentration [1–4] In mineral Copper ore grinding in a mobile vertical roller mill pilot plant2024年3月21日 The Significance of Grinding in Lithium Ore Processing: Grinding stands as an indispensable process in lithium ore processing, playing a pivotal role in liberating lithiumbearing minerals from the surrounding gangue materialBy reducing the ore particles to a finely ground state, grinding sets the stage for subsequent beneficiation processes, including flotation, Lithium Ore Grinding Mills clirikchina
.jpg)
Industrial Vertical Grinding Mill
Industrial vertical grinding mill is an ideal largescale grinding equipment, integrating crushing, drying, grinding, and grading and conveying It is widely used in cement, electric power, metallurgy, chemical, nonmetallic mining and other industrie The chemical composition of the product is stable, and the particle size is uniform, which 2024年1月3日 For example, using finer particles (with a certain size) in magnetic separation could improve the iron grade The shape of crushed ore affects the product particle size in a ball mill grinding Investigation on the particle size and shape of iron ore 2022年1月1日 Extensive research works (Ohenoja et al, 2013, Kinnarinen et al, 2015, Prziwara et al, 2018a, Prziwara et al, 2018b) were carried out to investigate the operation conditions on energy consumption, particle size distributions, and breakage characteristics of minerals in the laboratory stirred millsThe PBM has been proved to be well successful in simulating the Effect of operating conditions on the particle size 2017年3月4日 Tower mills, often called vertical mills, s tirred mills or regrind mills, are a more efficien t means of grinding material at smaller particle sizes, and can be used after ball mills in a grin (PDF) SIZE REDUCTION BY GRINDING METHODS
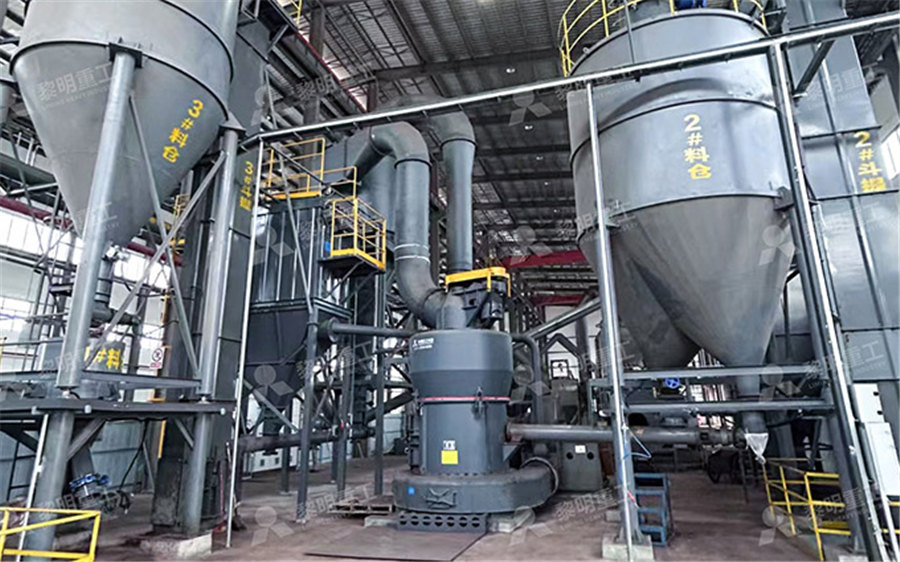
Predicting the effect of operating and design variables in grinding
2021年7月1日 Vertical stirred mills may be classified according to the speed of the stirrer in two groups: gravityinduced or fluidized mills [[1], [2], [3]]In the gravityinduced mills, the stirrer, generally of the screw type, turns so that the grinding charge exhibits an ascending convective motion at the center, descending from the edges of the screw and close to the mill shell, owing 2023年7月10日 The review concludes that stirred mills have significant potential for achieving the energyefficient ultrafine grinding of particles Stirred mills have unique designs and operations, which (PDF) EnergyEfficient Advanced Ultrafine 2024年10月13日 The ore is fed into the mill and as the cylinder rotates, the balls crush and grind the ore, causing the particles to break down in size Rod Mills: Rod mills operate on the same principle as ball mills but use rotating rods instead of balls as the grinding mediaUnderstanding the operation of grinding mills in the mining 2023年12月29日 COMPARISON OF GRINDING EFFICIENCY BETWEEN BALL MILLS AND VERTICAL ROLLER MILLS IN COARSE GRINDING Yakup Umucu 1, Vedat Deniz 2,Osman Mart 1 Abdi Kemal Y!ce 1, Mehmet Fahri Sara" 3 1 S leyman COMPARISON OF GRINDING EFFICIENCY BETWEEN
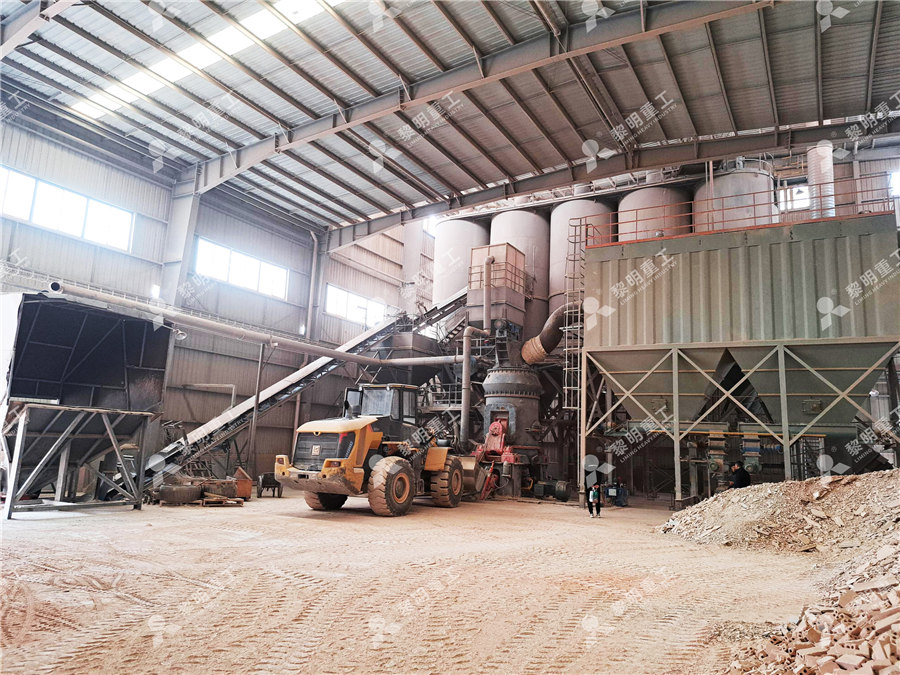
Understanding the SAG Mill in Copper Ore Mining Process
2023年10月10日 The Vertical Shaft Impactor Mill, also known as the VSI Mill, is a unique type of grinding mill that operates on a completely different principle compared to other types of mills This type of mill uses highspeed rotors with wearresistant tips to crush and grind materials into smaller particles2023年12月4日 A vertical roller mill (VRM) is a grinding equipment used for the size reduction of minerals, cement, and ceramics simulated and validated the capability of DEM to estimate the product particle size distribution, suitable rolling resistance can be added to the contact of spherical particles Raw ore from different mines shall have Numerical Investigation of Vertical Roller Mill Operation Ball mills are progressively used to grind the ores for particle size reduction and to liberate valuable minerals from the ores The grinding of ore is a highly energyintensive process [1–4] In this process, the size of the particle obtained depends on the energy consumption of the ball mill The major challenge encountered in theEstimation of Grinding Time for Desired Particle Size 2018年2月1日 In another study to investigate ball size distribution on ball mill efficiency by Hlabangana et al [50] using the attainable region technique on a silica ore by dry milling, a threeball mix of Effect of ball and feed particle size distribution on the milling
.jpg)
Effect of Solid Concentration on Particle Size Distribution and
2024年6月11日 In this study, the evolution behavior of the particle size distribution during the grinding process was examined with fractal theory According to the distribution index k of the Rosin–Rammler–Benne model, the relationship between the fractal dimension D of the fractal theory and the distribution index k is discussed The fractal dimension D was used to evaluate 2013年4月16日 ABSTRACT In this study, ultrafine grinding of a refractory silver ore tailings was studied A laboratory scale pintype vertical stirred mill and ceramic beads were employed for the grinding testsInvestigation of some parameters affecting the Ultrafine grinding 2018年12月1日 The first stirred vertical mill was developed in Japan by the Japan Tower Mill Company Ltd which was later renamed to Kubota Tower Mill Corporation, KTM The Japanese Tower Mill was the first vertical grinding mill to be used in the mining industry (Stief et al, 1987) The Tower Mill® is now produced by NipponEirichPredicting the product particle size distribution from a 2023年9月21日 Figure 3: Relationship between feed size (F80) and Bond efficiency factor (Huang et al, 2019) VERTICAL POWER MILL (VPM) – PRINCIPLE OF OPERATION Declining ore grades and more complex ore bodies, as well as waste management and global net zero initiatives, lead to a clear trend for high tonnage yet energy efficient grindingRECENT DEVELOPMENTS IN COARSE GRINDING USING
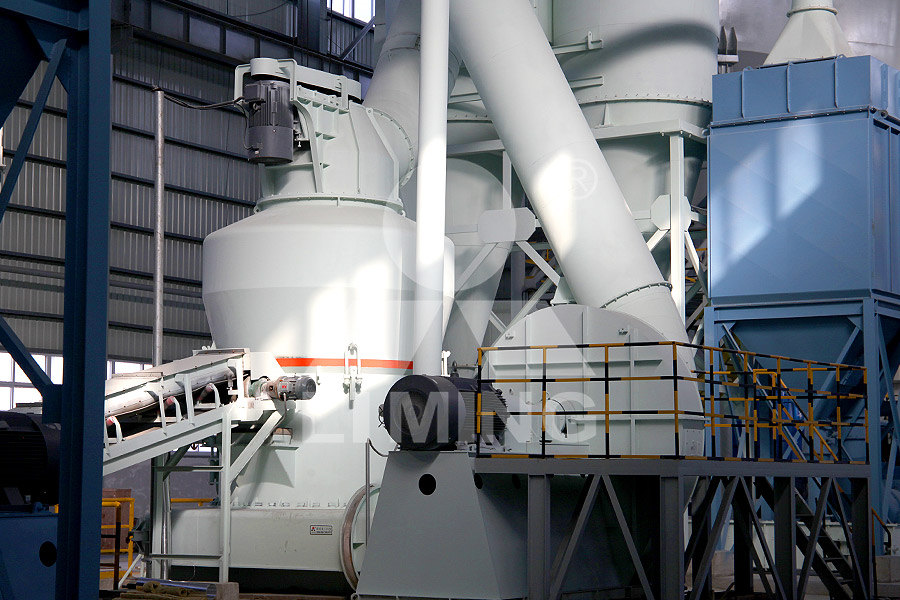
Particle size distributions of the pilot vertical mill
Grinding tests were conducted using a pearshaped ball mill on an oxidized coppercobalt ore to determine the milling parameters Twelve monosized fractions of the ore sample were prepared and 2019年4月16日 Vertical roller mills, VRMs, are widely used for grinding raw materials in factories engaged in the extraction and processing of minerals Any machine used for grinding or crushing consumes around (PDF) LEARNING FROM OTHER INDUSTRIES; WHY THE VRM 2015年3月15日 The grinding parts of a Loesche mill (Fig 1) are a rotating table (1) with a horizontal grinding track and rollers (2), which are pressed onto the table by lever arms and a hydro pneumatic spring systemBetween the working surfaces of track and rollers, particle bed comminution takes place A dynamic air separator (3) is located above the grinding chamber, Research of iron ore grinding in a verticalrollermill2020年10月1日 Several comminution laws have been proposed to link the consumed energy to a characteristic particle size of the powder The popular models are those of Rittinger [4], Bond [5] and Kick [6]While the Bond and Kick models are mostly employed for coarse and intermediate size grinding, the Rittinger model is better suited for fine comminution [7]This model assumes Evolution of grinding energy and particle size during dry ball
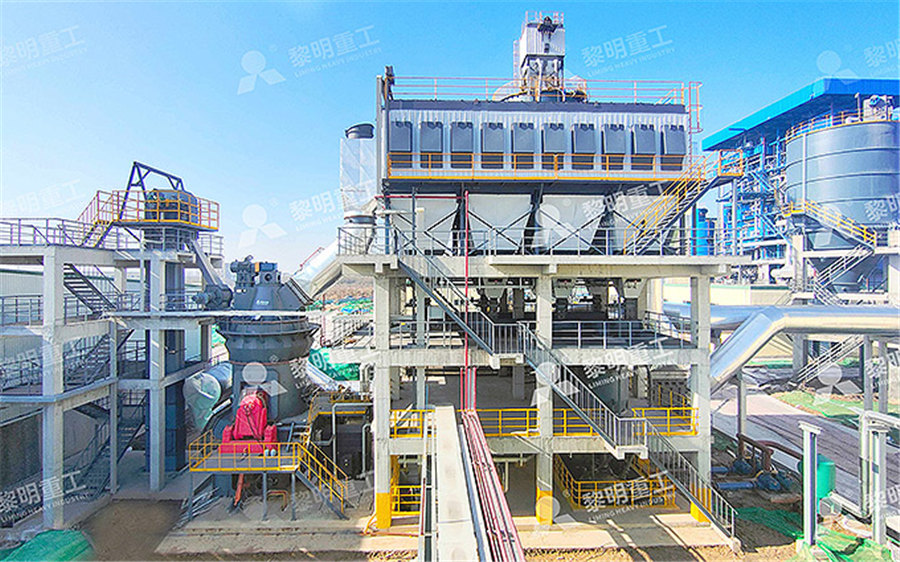
Ore Grinding SpringerLink
2023年7月20日 In the mineral processing industry, ore grinding is the particle size preparation before the separation of the crushed ore Except those that process some placers, almost all mineral processing plants have grinding operations, in which materials are crushed by the impact and abrasive action of grinding medium (steel rod, steel ball, gravel, or 2014年10月1日 Based on final particle size, time consumption, parameters of the grinding process, grinding media, assumed particle size, and type of material used, we identify various types of mills that have Copper Ore Grinding in a Mobile Vertical Roller Mill Pilot PlantOur main products include ultrafine vertical roller mill, ultrafine grinding mill, stone powder production equipment, Welcome to consult +17 [ protected]SBM Ultrafine Powder Technology Industrial Grinding Mill, 2024年4月1日 iii ABSTRACT The mineral processing industry has seen an increased use of vertical stirred mills, owing to the ineficiency of ball mills for fine grind applicationsPREDICTING THE PRODUCT PARTICLE SIZE