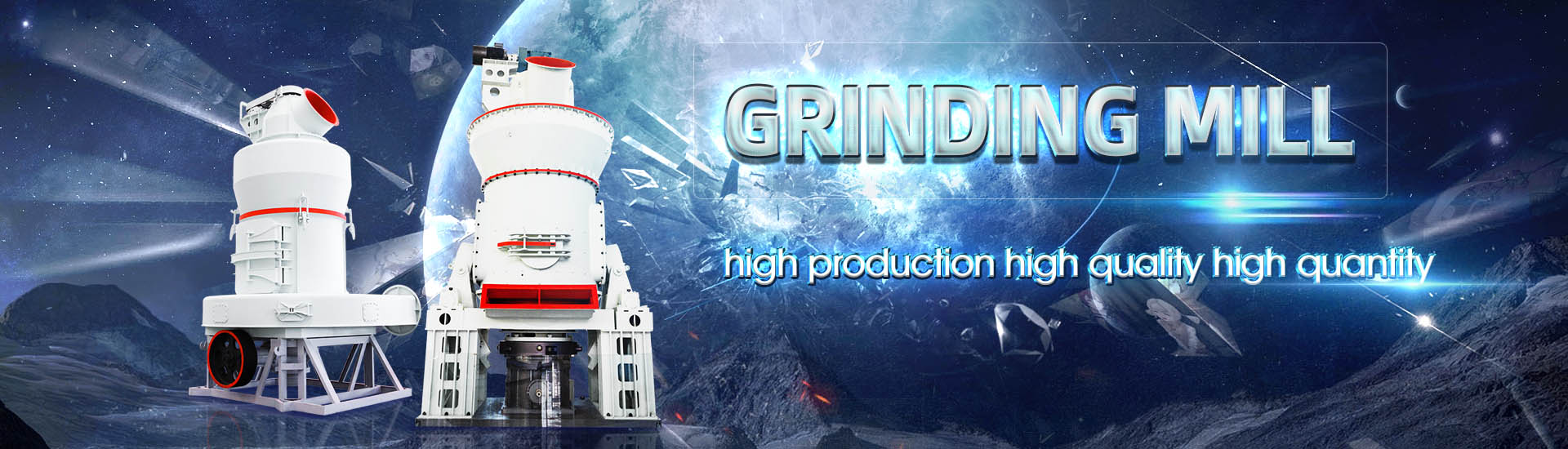
What is the Capacity of 3213m Cement Mill
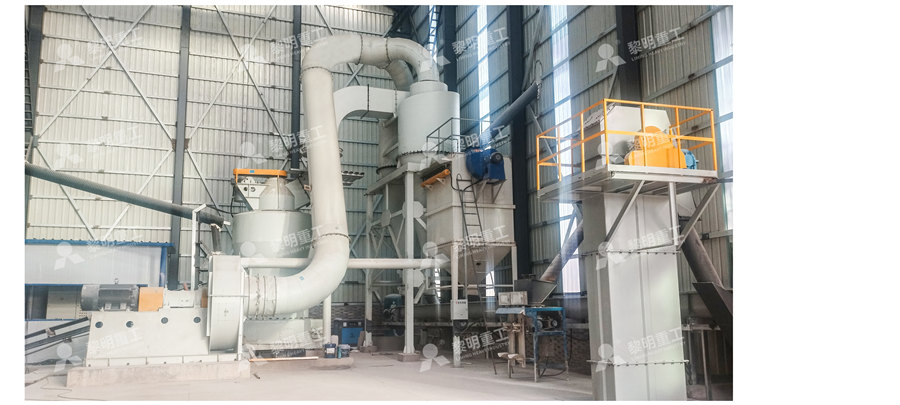
The Cement Plant Operations Handbook International
3 天之前 In combination with cement storage, there should be adequate storage capacity for clinker and other cement components to maintain deliveries during maintenance shutdowns and, if the market is cyclical, to bridge low and high shipping periods Total clinker capacity should 6 Cement Mill The cement mill grinds the clinker to a fine powder, which is then mixed with gypsum to form cement Equipment: Ball mills, vertical roller mills Technical Specifications: Ball Mills: 1030 tons/hour capacity, 5001500 kW The Comprehensive Guide to Cement Plant The cement mill capacity (in machine hours) for 12 periods of year 2015 as can be seen in Table 3 below The machine hours capacity in each month were different due to dayoff scheduleCement Mill Capacity (2015) Download TableDrill depth: max 25m Drill diameter: 80165mm Blasting is the most widely used method to excavate limestone for cement production as the rock is usually too hard to be ripped or dozed After blast holes are drilled, they will be charged Cement Manufacturing Process INFINITY FOR
.jpg)
Review on vertical roller mill in cement industry its
2021年1月1日 There are 210 large cement plants having total capacity of 410 MT cement production, with 350 small plants account for the rest Out of 210 large units, 77 are situated in Cement milling is usually carried out using ball mills with two or more separate chambers containing different sizes of grinding media (steel balls) Grinding clinker requires a lot of energy How easy a particular clinker is to grind Cement Milling Understanding CementUp to now, the company has three cement production lines, one of which is a new dry process clinker production line with a daily production capacity of 2,500 tons, which has the 42 13m large cement mill has been successfully fitted2021年12月21日 Almost 409Mt/yr of new cement capacity and 270Mt/yr of new clinker capacity is provided by these projects 272% of the new cement capacity comes from new separate Global Projects: Cement capacity expansion to 2025 Global Cement
.jpg)
What is the Importance of Cement Milling ball mills supplier
However, with the advancement of technology, modern cement mills are designed to be more energyefficient By using highpressure roller mills, vertical roller mills, or ball mills with highefficiency separators, manufacturers can reduce their energy consumption while still producing highquality cement 4 Cost SavingsCALCULATED VALUE OF DF, % Maximum ball size (MBS) Please Enter / Stepto Input Values Mill Feed Material Size F, mmball mill calculations, grinding media filling degree, ball size, mill 2024年11月19日 If you’re trying to make a profit off other production buildings, you might be interested in our cement factory guide Placing and Purchasing The Grain Mill Starting off, you’ll need to get your hands on the grain mill There Farming Simulator 25: Grain Mill Guide Item 2015年6月19日 The basic parameters used in ball mill design (power calculations), rod mill or any tumbling mill sizing are; material to be ground, characteristics, Bond Work Index, bulk density, specific density, desired mill tonnage capacity DTPH, operating % solids or pulp density, feed size as F80 and maximum ‘chunk size’, product size as P80 and maximum and finally the type of Ball Mill Design/Power Calculation 911Metallurgist
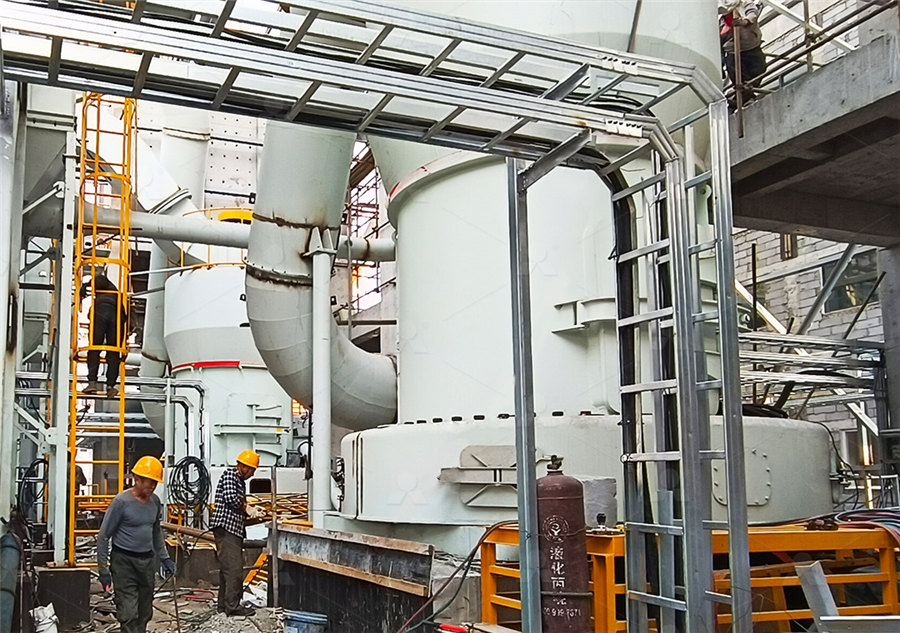
Review on vertical roller mill in cement industry its
2021年1月1日 India is the world's second largest producer of cement and produces more than 8 per cent of global capacity Due to the rapidly growing demand in various sectors such as defense, housing, commercial and industrial construction, government initiative such as smart cities PMAY, cement production in India is expected to touch 550–600 million tones per 6 Cement Mill The cement mill grinds the clinker to a fine powder, which is then mixed with gypsum to form cement Equipment: Ball mills, vertical roller mills Technical Specifications: Ball Mills: 1030 tons/hour capacity, 5001500 kW motor power Vertical Roller Mills: 2050 tons/hour capacity, 10003000 kW motor power Example Brands:The Comprehensive Guide to Cement Plant Costs: An In The differences between raw mill and cement mill in the cement manufacturing process Learn about the unique functions and applications of each type of mill and how they contribute to producing highquality cement products The production capacity of a raw mill is generally lower than that of a cement mill This is because the raw materials Understanding the Difference Between Raw Mill and Cement MillProcess Training Ball Mill To Download this post + all manuals and books and Excel sheets and all notes I collected over my 23 years of experience in Cement industry click here now INTRODUCTION Comminution is a major unit operation in a cement plant, accounting for about 50 75 % of the total plant energy consumptionProcess Training Ball Mill INFINITY FOR CEMENT EQUIPMENT
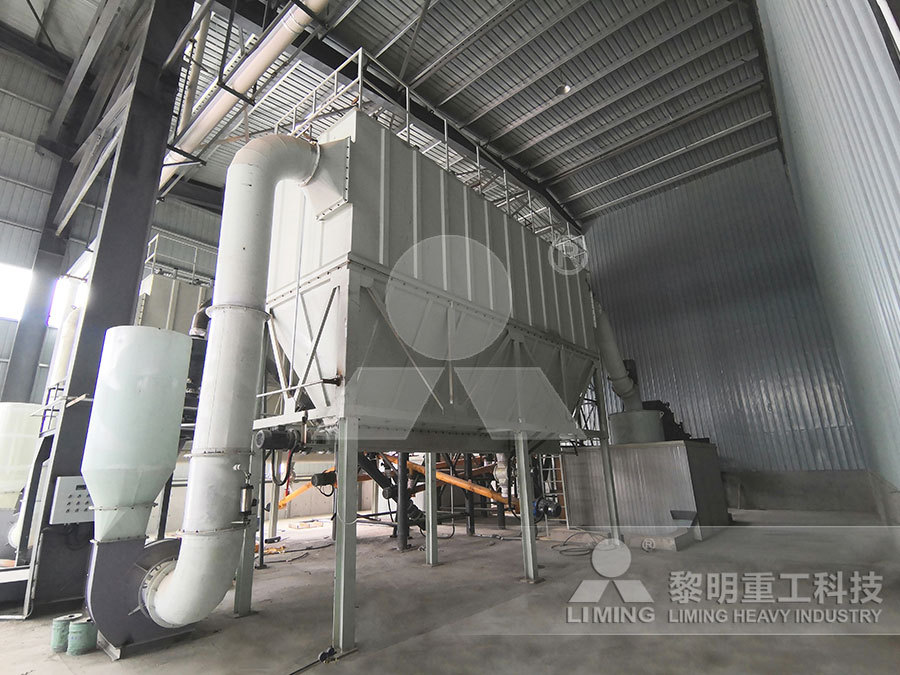
Raw Mill, Cement Raw Mill, Raw Mill In Cement Plant Cement
Raw mill is also known as cement raw mill, AGICO CEMENT supplies raw mill in cement plant,and other cement equipment with high quality and competitive price, welcome to ask! Skip to content +86 Why AGICO CEMENT is popular? Large production capacity: AGICO has a large area of the workshop of 30,000 square meters, also has 2024年11月22日 Production Efficiency Rate Definition The Production Efficiency Rate is a key performance indicator that measures the effectiveness of a cement manufacturing plant in utilizing its resources to produce finished products It is defined as the ratio of the actual output to the potential output, expressed as a percentage This metric is crucial for assessing how well the What to Achieve with Cement Manufacturing FinModelsLabConcrete milling is the process of removing the top layers of a concrete surface It’s carried out using scarifying machines equipped with diamondtipped blades Milling operations are effective at creating level, smooth surfaces that provide Concrete Milling 101 What is the concrete 3 天之前 Clinker – 11 Finish mill – 12 Cement – 13 Quality control – 14 Packing and distribution – 15 Emission abatement (dust, NO x, SO 2, etc) – 16 Maintenance – 17 Process – 18 Materials analysis –19 Plant capacity summary – 20 Storage capacity 15 Cement plant construction and valuation 244 1 New plant construction The Cement Plant Operations Handbook International

What Role Does Cement Mill Play In Production?
2024年10月14日 In today's construction industry, the demand for cement as a basic material continues to grow, and cement mills, as key equipment in the cement production process, play a vital role The production process of cement mills involves a variety of technical links, from the grinding of raw materials to the manufacture of finished cement, and each step affects the Premier Cement Mills PLC is growing at a pace faster than all its competitors Our commercial production started back on 12th March 2004 with its 1st Unit having a production capacity of only 06 million tons per annum and then added its 3rd and 4th Units on November 2012 having a combined annual capacity of 12 millionHome Premier CementThe vertical roller mill (VRM) is a type of grinding machine for raw material processing and cement grinding in the cement manufacturing processIn recent years, the VRM cement mill has been equipped in more and more cement plants around the world because of its features like high energy efficiency, low pollutant generation, small floor area, etc The VRM cement mill has a Vertical Roller Mill Operation in Cement Plant2021年1月29日 Cement sector in india is enjoyign success and capacity enhancement due to the rapidly growing demand in various sectors but at the same time a threat is approaching to cement industry that its Increase productivity of vertical roller mill using seven QC tools
.jpg)
OK™ CEMENT MILL
2024年9月1日 hardest materials The OK™ cement mills are available in all sizes 0 100 200 300 400 500 600 700 800 OK 776 OK 434 OK 484 OK 404 OK 524 OK 716 OK 816 OK 666 OK 614 OK 564 OK ™ cement mill production and slag grinding production (t/h) OK 283 OK 373 OK ™ cement mill and slag grinding Actual capacity depends on product fineness 2016年10月5日 In this chapter an introduction of widely applied energyefficient grinding technologies in cement grinding and description of the operating principles of the related equipments and comparisons over each other in terms of grinding efficiency, specific energy consumption, production capacity and cement quality are given A case study performed on a EnergyEfficient Technologies in Cement GrindingThe process involves feeding the raw materials into a cement ball mill or vertical roller mill, where they are ground into a fine powder The Purpose of Cement Milling Cement milling plays a crucial role in the production of cement The primary purpose of cement milling is to reduce the size of the clinker and other raw materials that have What is Cement Milling? ball mills supplier2013年6月25日 Even if the cement is not lowalkali cement (below 060%), the amount is important for three reasons: Airentraining agents generally produce more air as the alkali content goes up Where the alkali occurs in the cement can affect this, but to get a first approximation, we need to track the equivalent alkali contentHow to Read a Cement Mill Certificate: Part 1 NPCA
.jpg)
(PDF) Capacity of roller mill for cement grinding
2020年12月15日 In a cement manufacturing plant the electric power consumption for carminution processes usually amounts to about 70% of the total plant power consumption A roller mill has been recently Mill performance test Steps 1 Recording of related operational data 2 Air flow measurement 3 Crash stop and visual inspection in mill 4 Sampling in mill 5 Evaluation of test 1 Recording of related operational dataTube Mill Feed Cement Separator Ball Mill OptimizationThe vertical cement mill is largescale cement grinding machine With advantages of energyefficient and stable quality, vertical roller mill is widely applied to many industries, such as cement, power, metallurgy, chemical and nonmetallic mining industry and etc As a typical type of Cement Mill, vertical cement mill set crushing, drying, grinding, grading transportation in one, it grind Vertical Cement Mill, Vertical Roller Mill Buy Cement Cement The aim of Deshbandhu Cement Mills Ltd is to establish its brand as a rising contender in the construction sector of the Real Estate Industry Fineness, Strength, and Standard Blending Proportion are the three Raw materials from which the quality is marked The client is ensured to have both product satisfaction and service delightfulness of Deshbandhu Cement Mills Ltd Deshbandhu Group
.jpg)
Cement Milling Understanding Cement
This is done by a mixture of both aircooling and watercooling, including spraying water inside the mill Cement milling and gypsum dehydration Because the cement gets hot due to the heat generated by grinding, gypsum can be partly dehydrated, forming hemihydrate, or plaster of Paris 2CaSO 4H 2 O2020年6月14日 The function of the slide shoe bearing is to keep the mill aligned to the mechanical process while allowing for mill rotation The advantages provided by the slide shoe bearing includes: Lighter mill weight (less energy to operate) More compact mill while maintaining capacity; Reduced mechanical stress; Design and LubricationImproving Mill Shoe Bearing Reliability and ProductivityA cement mill is a machine used to grind the clinker into fine powder The clinker is a hard nodular material produced by sintering of limestone and clay How many types of cement mills are there? There are several types of cement mills that are used in the milling process The most common types of cement mills include ball mills, vertical How many types of cement mills are there? ball mills supplier2021年3月12日 and cement Roller presses are used mainly in combination with a ball mill for cement grinding applications and as finished product grinding units, as well as raw ingredient grinding equipment in mineral applications This paper will focus on the ball mill grinding process, its tools and optimisation possibilities (see Figure 1) The ball millBALL MILLS Ball mill optimisation Holzinger Consulting
.jpg)
(PDF) Grinding Media in Ball MillsA Review ResearchGate
2023年4月23日 Comminution is a very important and resultdetermining step in mineral processing This is because further downstream processes in the beneficiation chain depend entirely on itHowever, with the advancement of technology, modern cement mills are designed to be more energyefficient By using highpressure roller mills, vertical roller mills, or ball mills with highefficiency separators, manufacturers can reduce their energy consumption while still producing highquality cement 4 Cost SavingsWhat is the Importance of Cement Milling ball mills supplierCALCULATED VALUE OF DF, % Maximum ball size (MBS) Please Enter / Stepto Input Values Mill Feed Material Size F, mmball mill calculations, grinding media filling degree, ball size, mill 2024年11月19日 If you’re trying to make a profit off other production buildings, you might be interested in our cement factory guide Placing and Purchasing The Grain Mill Starting off, you’ll need to get your hands on the grain mill There Farming Simulator 25: Grain Mill Guide Item
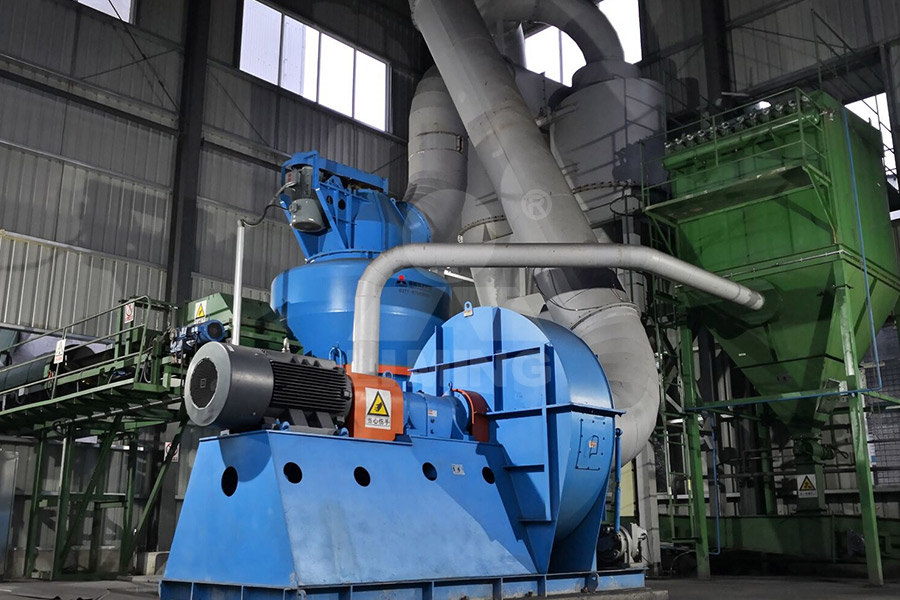
Ball Mill Design/Power Calculation 911Metallurgist
2015年6月19日 The basic parameters used in ball mill design (power calculations), rod mill or any tumbling mill sizing are; material to be ground, characteristics, Bond Work Index, bulk density, specific density, desired mill tonnage capacity DTPH, operating % solids or pulp density, feed size as F80 and maximum ‘chunk size’, product size as P80 and maximum and finally the type of 2021年1月1日 India is the world's second largest producer of cement and produces more than 8 per cent of global capacity Due to the rapidly growing demand in various sectors such as defense, housing, commercial and industrial construction, government initiative such as smart cities PMAY, cement production in India is expected to touch 550–600 million tones per Review on vertical roller mill in cement industry its 6 Cement Mill The cement mill grinds the clinker to a fine powder, which is then mixed with gypsum to form cement Equipment: Ball mills, vertical roller mills Technical Specifications: Ball Mills: 1030 tons/hour capacity, 5001500 kW motor power Vertical Roller Mills: 2050 tons/hour capacity, 10003000 kW motor power Example Brands:The Comprehensive Guide to Cement Plant Costs: An In The differences between raw mill and cement mill in the cement manufacturing process Learn about the unique functions and applications of each type of mill and how they contribute to producing highquality cement products The production capacity of a raw mill is generally lower than that of a cement mill This is because the raw materials Understanding the Difference Between Raw Mill and Cement Mill
.jpg)
Process Training Ball Mill INFINITY FOR CEMENT EQUIPMENT
Process Training Ball Mill To Download this post + all manuals and books and Excel sheets and all notes I collected over my 23 years of experience in Cement industry click here now INTRODUCTION Comminution is a major unit operation in a cement plant, accounting for about 50 75 % of the total plant energy consumptionRaw mill is also known as cement raw mill, AGICO CEMENT supplies raw mill in cement plant,and other cement equipment with high quality and competitive price, welcome to ask! Skip to content +86 Why AGICO CEMENT is popular? Large production capacity: AGICO has a large area of the workshop of 30,000 square meters, also has Raw Mill, Cement Raw Mill, Raw Mill In Cement Plant Cement 2024年11月22日 Production Efficiency Rate Definition The Production Efficiency Rate is a key performance indicator that measures the effectiveness of a cement manufacturing plant in utilizing its resources to produce finished products It is defined as the ratio of the actual output to the potential output, expressed as a percentage This metric is crucial for assessing how well the What to Achieve with Cement Manufacturing FinModelsLab