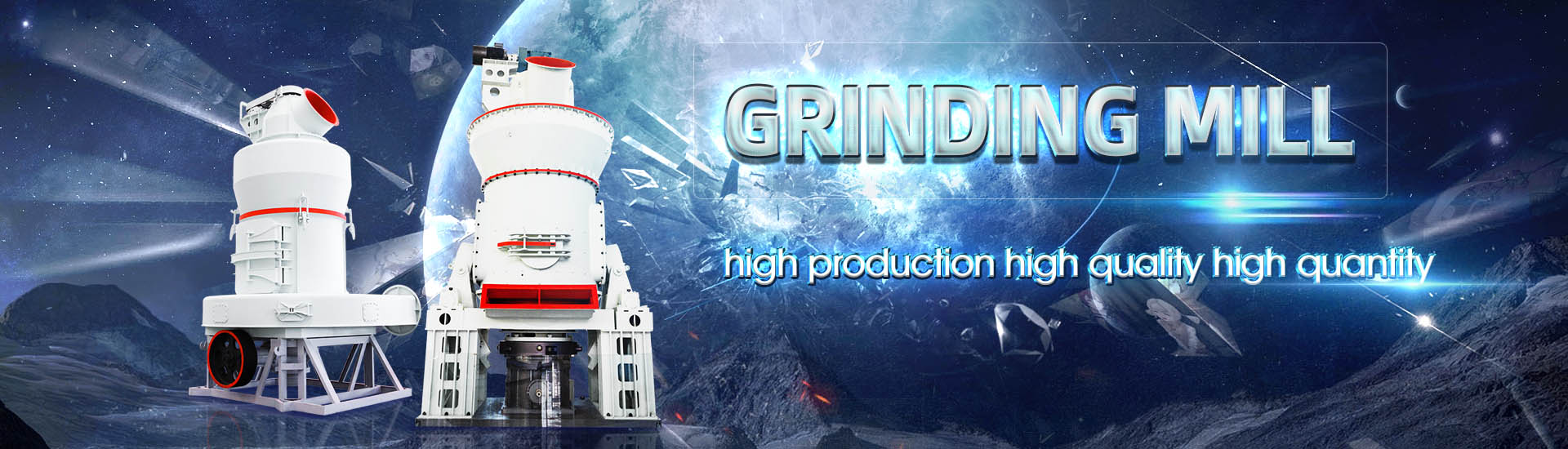
HOME→Air flow grinding particle size of air flow grinding particle size of air flow grinding particle size
Air flow grinding particle size of air flow grinding particle size of air flow grinding particle size
46.jpg)
Grinding in an air classifier mill — Part II: Characterisation of
2011年7月25日 The particle motion in the size range between 29 and 573 μm is investigated using Particle Image Velocimetry (PIV) The mathematical model for the fluid flow is extended to a fully coupled twophase flow numerical calculation The particle motion in the grinding zone is The present study deals with the grinding of ammonium perchlorate (AP) using an air classifier mill Numerous trials were carried out producing a diverse range of particle size distribution OPTIMIZATION OF GRINDING PARAMETERS AND PRODUCT PARTICLE SIZE 2011年7月25日 Starting from the air flow visualisation measurements by Particle Image Velocimetry (PIV), the influence of the operating conditions on the flow pattern within the mill is Grinding in an air classifier mill — Part I: Characterisation of 2007年1月1日 Air jet mills have mainly been developed for producing fine particles of below 50 mm Most models are available in many sizes from labsize versions (as low as to 1 gram/h) Chapter 8 Air Jet Milling ScienceDirect

Model and simulator of inlet air flow in grinding installation
2023年5月22日 Maximum particle size of the feed material is about 1–2 mm, depending on the diameter of the mill’s working chamber After grinding, the product particles are sized about It contains 13 parameters describing the particle stressing, the particle size and shape and bulk material properties The single parameters of influence are combined to ten dimensionless Modelling of Grinding in an Air Classifier Mill Based on a 2021年9月26日 The airflow ultrafinegrinding resulted in marked differences in particle size (from 100 to 10 μm) The UMFs were all brighter in appearance (higher L*) than Tartary buckwheat Effects of Airflow UltrafineGrinding on the Physicochemical 2011年7月1日 First, the investigation of the air flow using a Particle Image Velocimetry (PIV) system showed significant differences to the assumed ideal flow field, then particle sphericity Grinding in an air classifier mill Part I: Characterisation of
.jpg)
Effect of Nozzle Quantity on the Flow Field
2024年7月17日 During the experiments, identical feed particle size distributions are used for the fly ash, with d 50 = 2829 μm and d 90 = 7785 μm, and the target particle sizes after grinding are set to d 50 = 10–12 μm and d 90 = 45 2021年7月11日 particle size, the air classifier mill has an internal classifier wheel that can be easily adjusted during operation to rotate at higher or lower speed, controlling the particles’ How to operate an air classifier mill to meet your fine 2023年10月4日 In the paint and pigment industries particle size influences appearance properties including gloss and tinctorial strength Particle size of the cocoa powder used in chocolate affects color and flavor The size and shape of the glass beads used in highway paint impacts reflectivity Cement particle size influences hydration rate strengthA GUIDEBOOK TO PARTICLE SIZE ANALYSIS University 2023年5月22日 The transport air plays a key role in the operation of this grinding circuit 22,23Most of all, appropriate air flow suspends the raw material in the working chamber of the millModel and simulator of inlet air flow in grinding installation
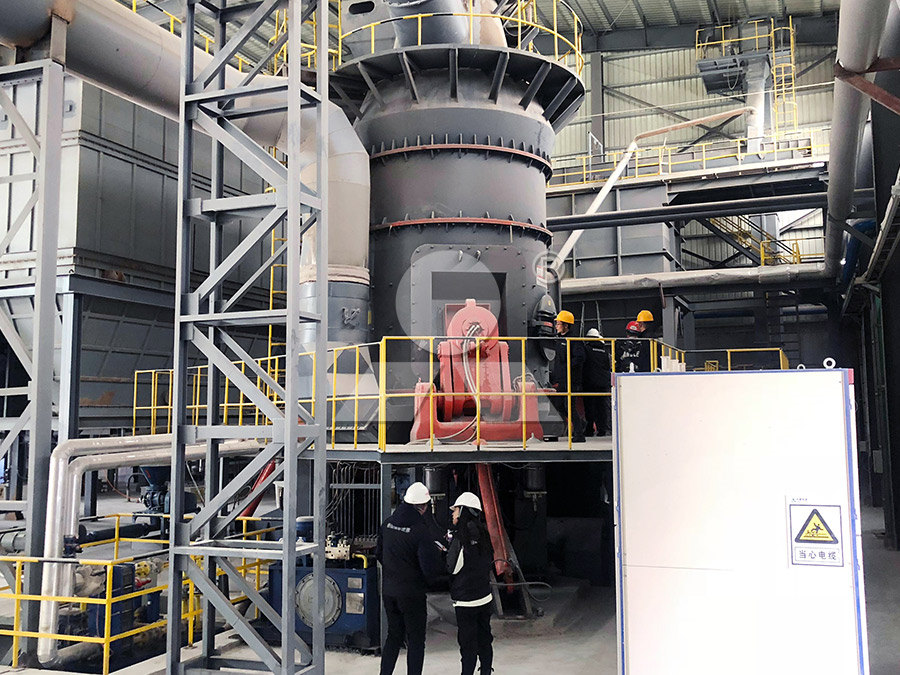
Improvement of pulverization efficiency for microsized particles
2019年11月2日 Improvement of pulverization efficiency for microsized particles grinding by uncooled hightemperature air jet mill using a computational simulation and appeared classification by the particle size The particles larger than 25 μm at 5,000 rpm, a relatively low rotational speed, is confirmed remaining inside the chamber while smaller one 2022年5月20日 Spiral jet or pancake mills have jets of air tangentially located around the center of the equipment in order to create a vortex of air Particlesize reduction is a result of particle–particle and particle–wall collisions upon feeding of solids into the air stream (Fig 46) Normally, gas velocities are such that a sonic flow is achieved Mechanical ParticleSize Reduction Techniques SpringerLink2018年7月23日 Critical check point in Grinding Particle Size and Distribution; Both particle size and particle size distribution are important for animal performance and feed mill productivity The research data recommend to have particle size of 600 to 900 for cornbased broiler diet to achieve the optimum animal performanceArt of GrindingParticle size reduction Benison Media2018年6月6日 ABSTRACT Electrostatic sampling is a promising method for the collection of bioaerosol particles Although the underlying physics responsible for particle collection are well understood, the collection efficiency of simple passive electrostatic samplers is difficult to predict Under these conditions, the collection efficiency becomes very sensitive to ambient air current The Influence of Air Flow Velocity and Particle Size on the
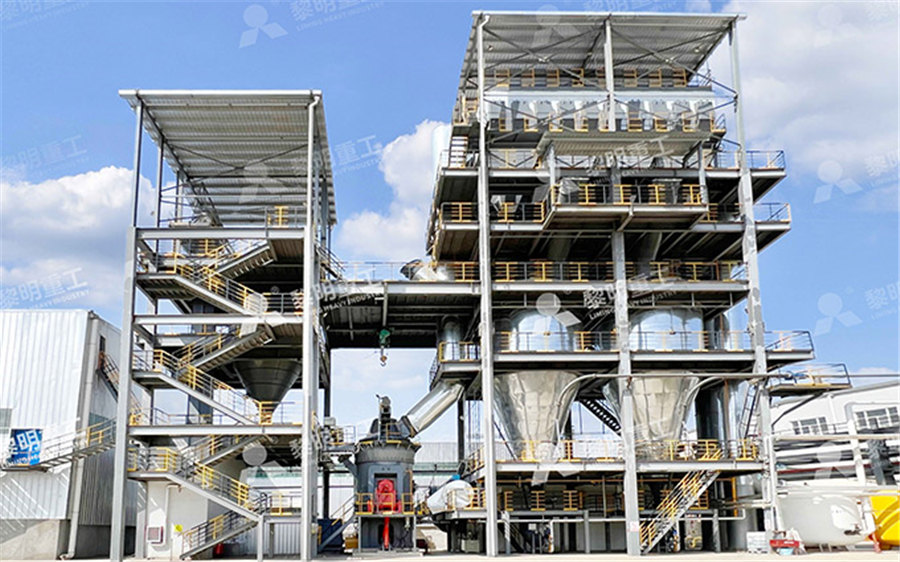
(PDF) Particle size distribution of cement and concrete
2021年7月9日 Particle size distribution (PSD) is an essential property of cement The only standard method to measure the PSD of cement, namely ASTM C115 is limited in scope; this standard describes a method 2023年7月10日 The present literature review explores the energyefficient ultrafine grinding of particles using stirred mills The review provides an overview of the different techniques for size reduction and the impact of energy requirements on the choice of stirred mills It also discusses the factors, including the design, operating parameters, and feed material properties, EnergyEfficient Advanced Ultrafine Grinding of Particles 2021年12月1日 The mesh size was based on the largest particle size (240 μm) and a maximum particletofluid cell volume ratio of 40% was selected, as recommended by Norouzi et al [18] The particle parameters such as the coefficient of restitution and friction are listed in Table 2, along with the time steps used for both the fluid and particle systemsEffect of grinding nozzles pressure on particle and fluid flow Onsize particles pass through the rotor and are pneumatically conveyed to the next stage in the process while offspec particles are rejected to second stage grinding The air classifier rotor is independently controlled, allowing for precise control of particle size simply by adjusting the RPM using a Variable Frequency Drive, VFDAir Classifying Mill for Particle Size Reduction Prater
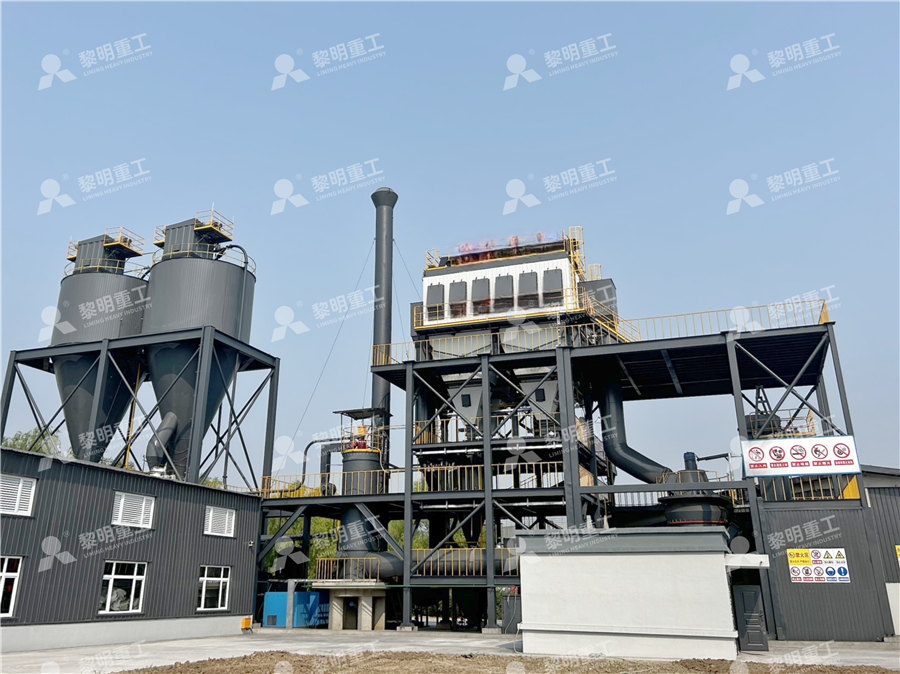
Fine Grinders, Hammer Mills, and More for
Air Classifying Mills The air classifying mills combines twostaged, closed circuit grinding with internal air classification for ultrafine micronization The distinctive capabilities of the Prater Air Classifying Mill outperform singlestage mills 2011年10月31日 Spiral jet or pancake mills have jets of air tangentially located around the center of the equipment in order to create a vortex of air Particlesize reduction is a result of particle–particle and particle–wall collisions upon feeding of solids into the air stream (Fig 46) Normally, gas velocities are such that a sonic flow is achieved Mechanical ParticleSize Reduction Techniques SpringerLink2023年7月28日 Brewing espresso coffee (EC) is considered a craft and, by some, even an art Therefore, in this study, we systematically investigated the influence of coffee grinding, water flow rate, and temperature on the extraction Influence of Flow Rate, Particle Size, and 2019年3月12日 Particles with a size between 01 and 1 μm have the lowest depositionrateinthehuman respiratory systemwith lessthan 25% of the inhaled particles depositing in the human respiratory system Smaller particles with a size between 001 and 01 μm mainly deposit in the tracheobronchial and alveolar region, the deepest point in the human Cutting fluid emissions in grinding processes: influence
.jpg)
Effect of Particle Size and Grinding Time on Gold Dissolution
2016年7月7日 The recovery of gold by ore leaching is influenced by the size of the particles and the chemical environment The effect of particle size on the dissolution of gold is usually studied using mono 2016年10月14日 Particle size reduction, screening and size analysis Objective This laboratory examines the particle size reduction of silica sand using manual and automatic grinding methods and the subsequent separation and size analysis of the obtained polydisperse powders The particle size of the powder samples will be determined using sedimentation and imageParticle size reduction, screening and size analysis 2016年4月5日 In PFboilers, coal is pulverised in a mill (or pulveriser) before being entrained by primary combustion air to burners, to form a high temperature flame in the furnace of the boiler (1000–1600 °C) [2]The fineness of the coal powder, as well as the uniformity of the coal flow sent to each burner fed by the same mill, are crucial parameters to achieve an effective combustion Online monitoring of coal particle size and flow distribution 2018年5月10日 With many grinding mills—including roller mills, rotor mills, hammer mills, airclassifier mills, and fluidizedbed opposedjet mills—successfully achieving the desired production throughput depends on help from a vacuum pneumatic conveying system The system not only helps draw the material through the mill, but in some cases assists the mill in achieving the Particle Size Reduction: How to Get Better Grinding
.jpg)
Experimental study on specific grinding energy and particle size
PDF On Aug 7, 2020, Jun Fu and others published Experimental study on specific grinding energy and particle size distribution of maize grain, stover and cob Find, read and cite all the 2024年6月24日 Air classifying mill: Combining air classification with a dualstage grinding mill, Prater’s air classifying mill provides a singleunit design that uses space and energy more efficiently GSeries fullscreen hammer mill : Able to provide markedly uniform particle size reduction, Prater’s Gseries hammer mills bring energy efficiency to Particle Size Reduction: A Comprehensive Guide Prater2013年3月10日 Consumer acceptance depends on taste and mouth feeling Processing can generate varying particle size distributions (PSD), which again influence flow parameters Chocolate can be produced by roller refining and conching or alternatively by ball milling Fat content during milling is an important parameter of both processes The aim of this project was Impact of fat content during grinding on particle size In previous research, the Tartary buckwheat bran and Tartary buckwheat flour were treated by the traditional ultrafine powder process (shear crushing, air flow crushing, and wet grinding) to Particle size distribution of different Tartary
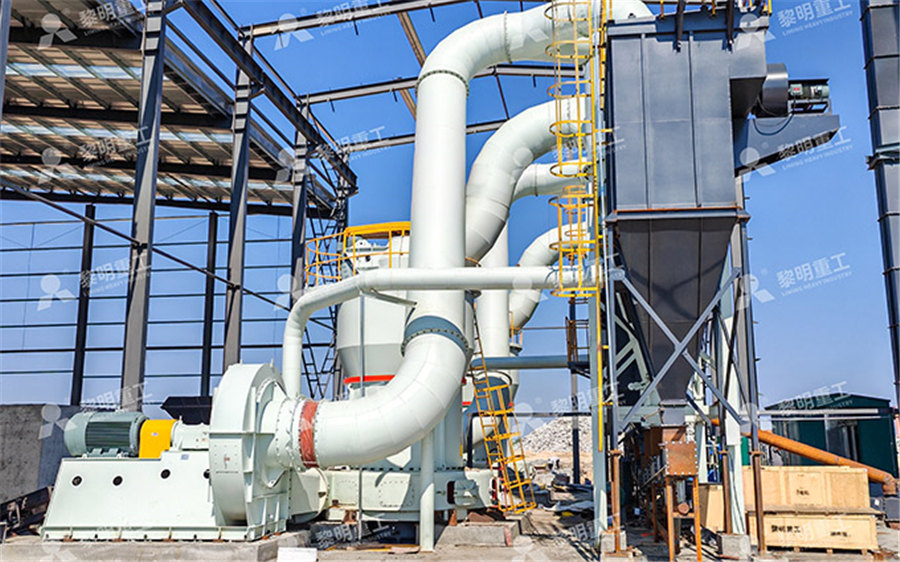
Effect of Solid Concentration on Particle Size
2024年6月11日 In this study, the evolution behavior of the particle size distribution during the grinding process was examined with fractal theory According to the distribution index k of the Rosin–Rammler–Benne model, the As shown in Figure 3 a, the particle size of the conductive carbon particles in the ink is within 35 μm after ball milling for 20 min, and the median diameter D50 (the cumulative distribution of (a) Relationship between grinding time and particle size 2019年11月30日 An experimental investigation of hydrodynamics of gassolid flow is carried out by engaging different designs of air distributor plates An analysis of three different plates, ie, perforated, 45 Effect of particle size on flow behavior in fluidized beds2024年11月1日 Benefits of Size Reduction Size reduction carries several benefits For example, smaller particles tend to exhibit more trait uniformity, whether it be color or grain texture, that can positively contribute to product perception Particle size uniformity also prevents segregation of individual ingredients within a blendHow Fine Grinders Achieve Particle Size Reduction Prater
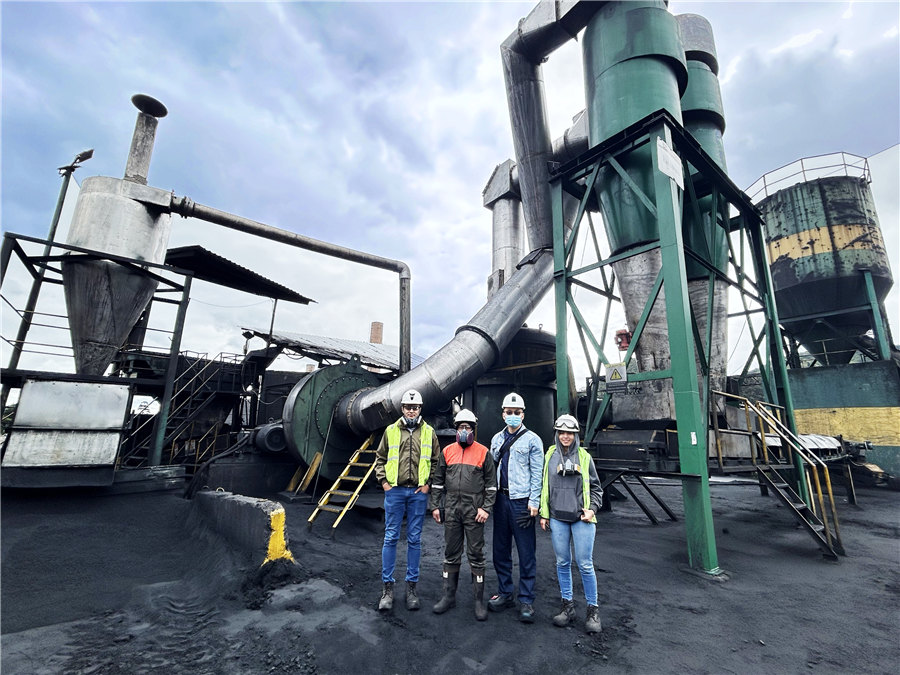
Chapter 8 Air Jet Milling ScienceDirect
2007年1月1日 Air jet mills have mainly been developed for producing fine particles of below 50 μm and have the following common features: There are no moving parts in the grinding chamber and energy for size reduction is brought by the carrier gasThe main grinding action is by particles hitting other particles making for little or no product contamination2019年11月19日 The grinding rate and consequently the grinding efficiency increases when the particle size increases, but drops sharply near zero after prolonged grinding periodsGrinding Kinetics of Slag and Effect of Final Particle Size on 2023年12月4日 The air classifying mill is a versatile machine widely used for particle size reduction in various industries It is an essential equipment in manufacturing many products, including Understanding the Working Principle of Air Classifying Mill 2017年12月12日 In this study, the grinding kinetics and the flowability of balloon flowers (BFs) with various moisture contents (8, 12, and 20%) were determined Three semiempirical grinding models (Bond, Kick, and Rittinger) were applied to describe the BFs’ grinding process A lower moisture content resulted in a decreased grinding constant value (Bond’s index) Based on the Effect of moisture content and particle size on grinding
.jpg)
A GUIDEBOOK TO PARTICLE SIZE ANALYSIS University
2023年10月4日 In the paint and pigment industries particle size influences appearance properties including gloss and tinctorial strength Particle size of the cocoa powder used in chocolate affects color and flavor The size and shape of the glass beads used in highway paint impacts reflectivity Cement particle size influences hydration rate strength2023年5月22日 The transport air plays a key role in the operation of this grinding circuit 22,23Most of all, appropriate air flow suspends the raw material in the working chamber of the millModel and simulator of inlet air flow in grinding installation 2019年11月2日 Improvement of pulverization efficiency for microsized particles grinding by uncooled hightemperature air jet mill using a computational simulation and appeared classification by the particle size The particles larger than 25 μm at 5,000 rpm, a relatively low rotational speed, is confirmed remaining inside the chamber while smaller one Improvement of pulverization efficiency for microsized particles 2022年5月20日 Spiral jet or pancake mills have jets of air tangentially located around the center of the equipment in order to create a vortex of air Particlesize reduction is a result of particle–particle and particle–wall collisions upon feeding of solids into the air stream (Fig 46) Normally, gas velocities are such that a sonic flow is achieved Mechanical ParticleSize Reduction Techniques SpringerLink
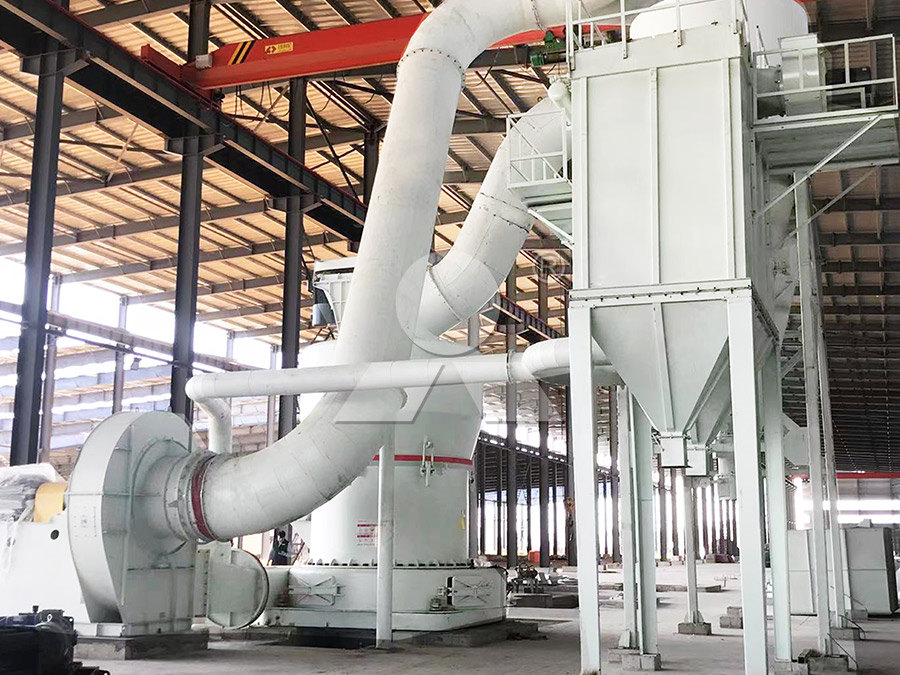
Art of GrindingParticle size reduction Benison Media
2018年7月23日 Critical check point in Grinding Particle Size and Distribution; Both particle size and particle size distribution are important for animal performance and feed mill productivity The research data recommend to have particle size of 600 to 900 for cornbased broiler diet to achieve the optimum animal performance2018年6月6日 ABSTRACT Electrostatic sampling is a promising method for the collection of bioaerosol particles Although the underlying physics responsible for particle collection are well understood, the collection efficiency of simple passive electrostatic samplers is difficult to predict Under these conditions, the collection efficiency becomes very sensitive to ambient air current The Influence of Air Flow Velocity and Particle Size on the 2021年7月9日 Particle size distribution (PSD) is an essential property of cement The only standard method to measure the PSD of cement, namely ASTM C115 is limited in scope; this standard describes a method (PDF) Particle size distribution of cement and concrete2023年7月10日 The present literature review explores the energyefficient ultrafine grinding of particles using stirred mills The review provides an overview of the different techniques for size reduction and the impact of energy requirements on the choice of stirred mills It also discusses the factors, including the design, operating parameters, and feed material properties, EnergyEfficient Advanced Ultrafine Grinding of Particles
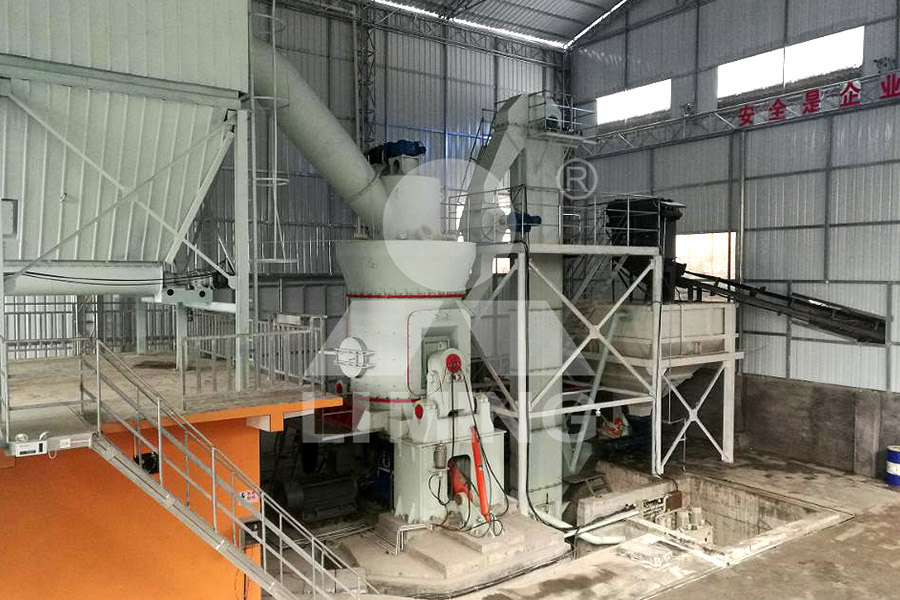
Effect of grinding nozzles pressure on particle and fluid flow
2021年12月1日 The mesh size was based on the largest particle size (240 μm) and a maximum particletofluid cell volume ratio of 40% was selected, as recommended by Norouzi et al [18] The particle parameters such as the coefficient of restitution and friction are listed in Table 2, along with the time steps used for both the fluid and particle systemsOnsize particles pass through the rotor and are pneumatically conveyed to the next stage in the process while offspec particles are rejected to second stage grinding The air classifier rotor is independently controlled, allowing for precise control of particle size simply by adjusting the RPM using a Variable Frequency Drive, VFDAir Classifying Mill for Particle Size Reduction Prater