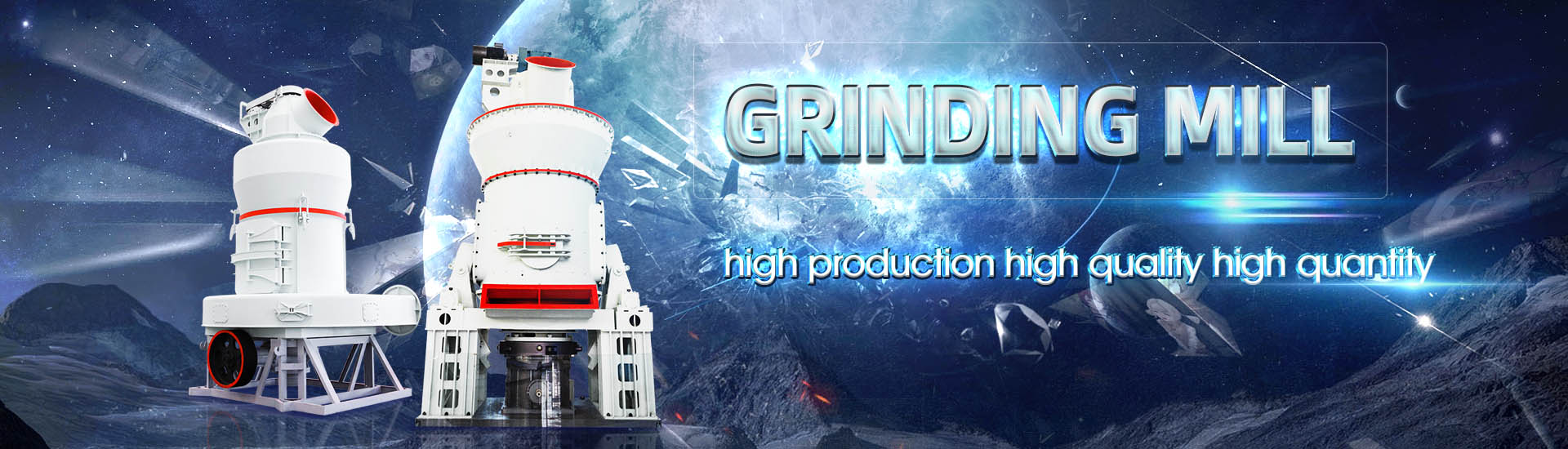
Coal mill limestone loading
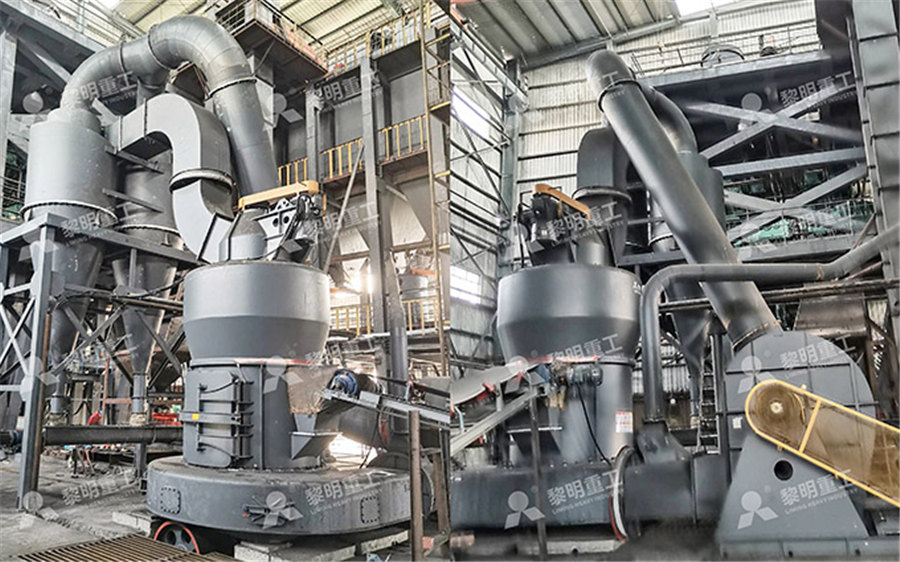
In the Limelight Penta Engineering Corporation
The nature of limestone and the feed size requirements dictates the crushing and screening system Type of fuel Oil and gas firing has optimum handling in a shaft kiln Using pulverised 2021年6月5日 In the coal mining process, the limestone stratum under coal seams would be affected by highpressure water, which has a significant influence on its physical and Mechanical behavior of limestone in natural and forced saturation 2023年9月20日 Conducting singleaxis equalamplitude cyclic loading and unloading tests of watersaturated coal, this paper studied the resistivity response and analyzed the relationship Resistivity and damage of coal under cyclic loading and unloading2023年9月24日 The technological process of the mining operation includes drilling and charging, blasting, coal cutting, using a blasting pressure gun, loading coal with a loose machine, Preventing waterinrush from floor in coal working face with
.jpg)
Mechanical Responses in Rocks with Different Lithologies
2024年7月26日 This study aims to address two issues crucial to the safety of underground mining practices: (1) The disparities in damage and catastrophe mechanisms between coal The Loesche coal grinding mill range is divided into two serial types: Small twin mills constructed to individual specifications (LM 122 D to LM 202 D), with table diameters from 1,200 to 2,000 LOESCHEMILLSpossible, barge or ship delivery of coal and limestone is usually the most practical mode, with the lowest cost per ton mile A typical river barge for coal transportation is an open hopper barge COAL AND LIMESTONE HANDLING2013年1月1日 Continuous miners can cut and load stronger formations like coal, shale, soft sandstone and limestone, gypsum, chalk etc, which cannot be excavated by bucketwheel Rock excavation using surface miners: An overview of some design
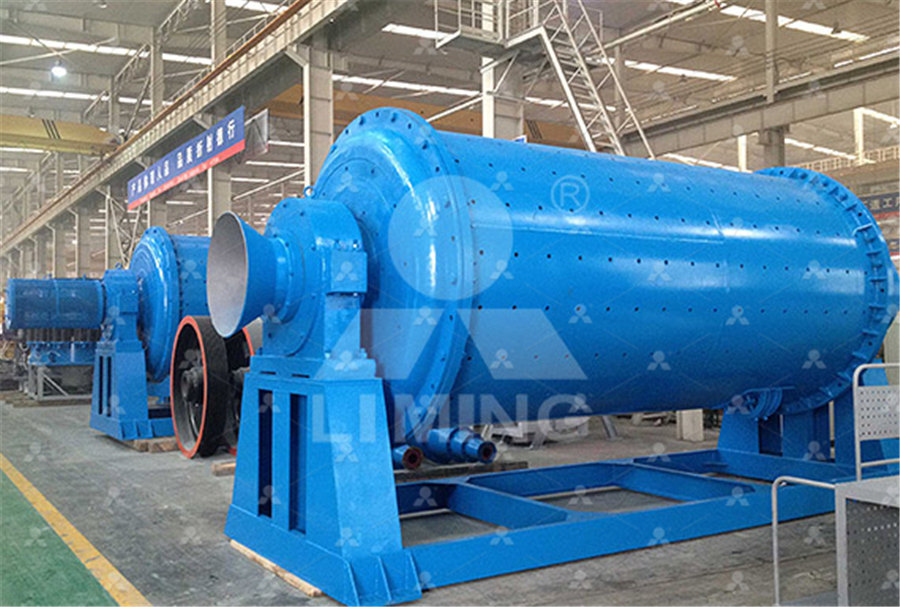
Loesche Mills for industrial minerals
Loesche Mill LM 15200, Slavno, Poland, 2006 Over more than 100 years Loesche has built up a wealth of experience in the grinding of coal, cement raw material, clinker, slag, ores and 1927 First Loesche coal mill delivered for the Klingenberg power station in Berlin 1953 500th coal mill plant sold worldwide 1961 Introduction of hydraulic spring assembly system 1965 Construction of first pressure mill (LM 122 D) 1980 Delivery of first modular coal mill (LM 263 D) 1985 Delivery of first selfinerting coal grinding plant (LM 212 D) for the steel industry (PCI LOESCHEMILLS2021年9月15日 Limestone and coal fuels were all considered typical for industrial applications Table 2 Composition (wt%) of the limestone used in lab experiments This was followed by milling for 2 min to a fine powder in a ball mill the corresponding ash load on the rotary kiln studied would be 565 kg/h If, however, the kiln was Coal ash and limestone interactions in quicklime productionCoal Coal / Limestone Coal BiomassLimestone High Pressure Feeders Low Pressure Feeders Batch Scales Pulverizer To CFB Hourly calibration of load cell circuity is preformed automatically and eliminates system drifts due to time and varying mill inlet centers, rates up to 70 tons/hour and design pressures PASS Stock Coal and Limestone Feed Systems
.jpg)
COAL PREPARATION AND FIRING INFINITY FOR CEMENT EQUIPMENT
Previous Post Next Post Contents1 COAL PREPARATION AND FIRING11 INTRODUCTION12 2COAL RESERVES13 CHARACTERISATION OF COALS BY CHEMICAL131 31 Major components132 32 Minor Components14 4CHARACTERISATION BY PHYSICAL AND MECHANICAL PROPERTIES141 41 Coal Storage142 42 Variation of Physical and carried out on a coal mill, the Lining Coal Mill always experiences wear and tearthis causes the performance of the coal mill to be not optimal Before modifications, the Lining Housing used wearresistant material BS EN 10029 Because it was assessed using wearresistant material BS EN 10029, it often experienced wear and tearWEAR ANALYSIS OF VERTICAL COAL MILL PLATE APS2024年7月17日 They can crush low to medium hardness materials such as limestone and coal, as well as materials with moisture content below 15%, suitable for both dry and wet crushing Hammer crushers have a reduction ratio of up to 50, a feed size of up to 1,000 mm, and a maximum output capacity of 3,000 t/hTypes of Crushers: Choosing the Right One for Each Stage2019年10月1日 Request PDF Wet and dry grinding of coal in a laboratoryscale ball mill: Particlesize distributions In this study, experimental data for wet and dryground coal samples under wet and dry Wet and dry grinding of coal in a laboratoryscale ball mill: Particle
.jpg)
MH Heavy Industry Weigh Belt Feeders Thayer Scale
First designed for coal fired power plants and steel mill service to feed coal, limestone, mill scale, dolomite, iron ore pellets, fluorspar and coke, the Model “MH” has been subjected to extreme environmental conditionssuch as abrasive dusts, corrosive fumes, wide temperature fluctuations and vibrationswithout any detrimental effects on Mill Speed Capacity Desired Coal Properties Feed Size Total Moisture Grindability (HGI) Abrasiveness Prod Fineness thru 200 Mesh Standard Screen Typical Air to Coal Ratio at 100% Mill Load Specific Power @ 100% Mill Load Typical Conditions CrusherDryer Mill PA Fan Total StartUp Time NoiseMill Only Approx Dimensions Mill Dia (D)A Comparison of Three Types of Coal Pulverizers Babcock PowerThe coal vertical mill, also referred to as the vertical roller coal mill, is an advanced equipment developed by our company It combines modern technology with our extensive experience in powder manufacturing This coal pulverizer efficiently integrates coal grinding and drying, providing highperformance and energysaving featuresHighEfficiency Vertical Coal Mill Enhancing Coal PulverizationAir Swept Coal Mill Introduction The airswept coal mill produced by AGICO equipment has reasonable structure, ball loading capacity: maximum 20t: 89: 250KW: ZD60: 63: Φ24X8M air swept coal mill: MFG248000: The Air Swept Coal Mill Cement Plant Machinery
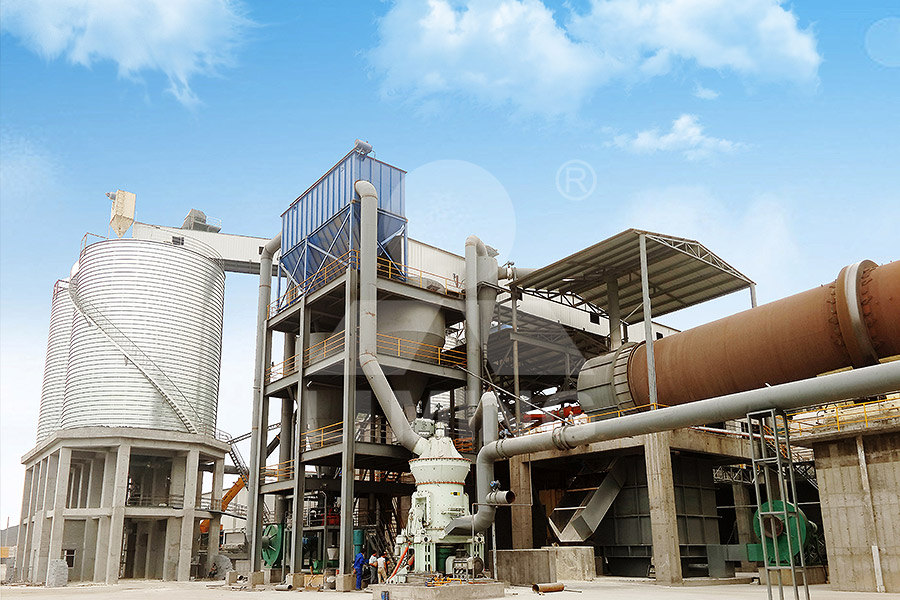
COAL PULVERIZER DESIGN UPGRADES TO MEET THE DEMANDS
For the mill equipped with spring load system, the grinding force is overloaded at reduced mill load This will result in additional wear on roller and table segments and will produce excessive mill vibrationWhile at high mill load operation, the grinding force is insufficient to meet the requirement for mill load increase Figure 6 Mill Closed mill housing pressureshock proof up to 35 bar: 3: Optimized free flow areas: 4: Maintenance door with LiftandSwing System: 5: Design measures preventing pulverized coal deposits: 6: Rollers can be lifted off: 7: Pull rods Coal mill, gypsum mill, clay mill, etc Pfeiffer MPS millsCoal Mill Feeding For coal mill feeding applications all Chain Conveyors come in a shockpressure proof design resistant up to 35 bar as a standard These Chain Conveyors feature a doublestrand chain A variable speed drive with frequency converter ensures a uniform material flow and controlled feeding Armoured Plate Conveyor type PKFChain Conveyors AUMUND Group2023年9月19日 Limestone grinding mill Material: Limestone Finished product particle size: 01730044mm Processing capacity: 8176t/shift Applicable materials: calcium carbonate crushing processing, gypsum powder processing, power plant desulfurization, nonmetallic ore pulverizing, coal powder preparation, etc Main limestone grinding machines Vertical roller Limestone Grinding Mill That You Need To Know Mortar Plant
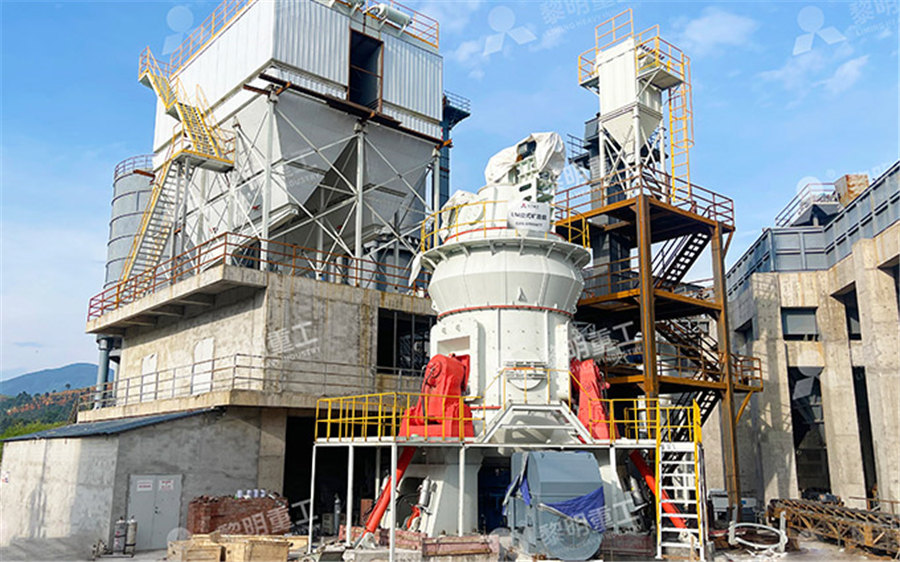
Limestone Grinding Mill MadeinChina
China Limestone Grinding Mill wholesale Kaolin Bentonite Quartz Limestone Zircon Coal Ceramic Cement Powder Ultrafine Calcium Carbonate Powder Gold Ore Copper Pyrite Diesel Grinding Ball Mill US$ 32509200 / Set 1 Set (MOQ) 2023年1月1日 Generally, a value of 55 represents an average grinding coal When switching to lower HGI coal, the capacity of the coal mill system should be assessed A key element in understanding a mill’s ability to handle lower HGI coals is Coal utilization in the cement and concrete industries2022年10月24日 analisa penyebab kenaikan vibrasi pada belt conveyor (42 bc 06) di area coal mill di pabrik ii pt semen baturaja tbk(PDF) ANALISA PENYEBAB KENAIKAN VIBRASI PADA BELT Primarily designed for power stations that burn coal to produce energy, our vertical coal mill wear parts are also good for use with slag, cement, and limestone among other applications For power station operations managers, our innovative Expand + range of wear parts provide significantly better performance than any other Metal Matrix Composite (MMC) products on the market todayVertical Coal Mill Magotteaux
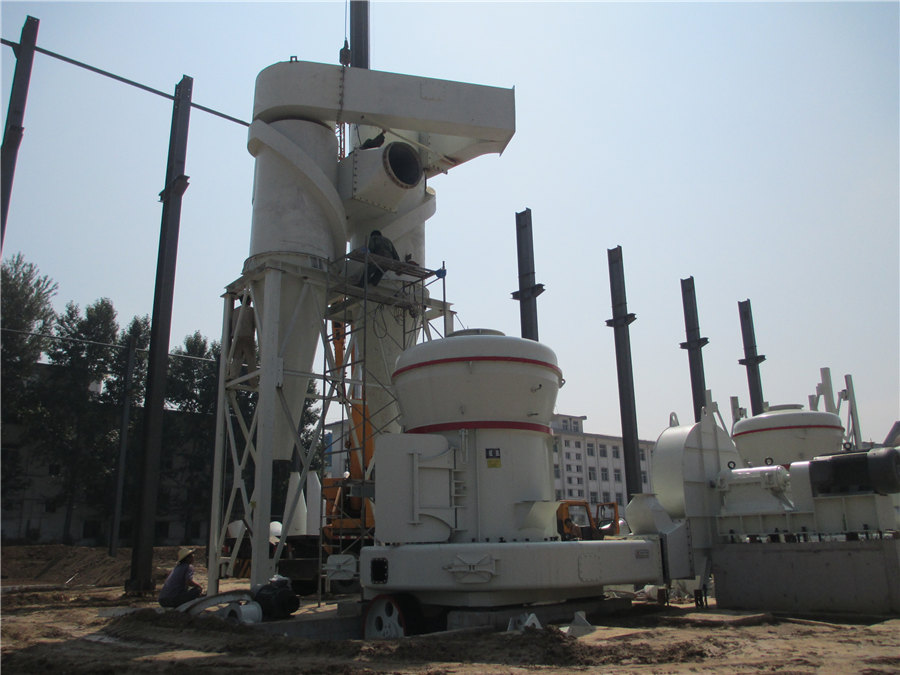
WEAR ANALYSIS OF VERTICAL COAL MILL PLATE ResearchGate
2022年11月1日 PDF Vertical Coal Mill Cement has main ingredients of limestone, clay, silica sand, and iron sand, the test object obtains a friction load from the 2023年10月8日 In addition, the entire coal processing plant must be considered to make the coal crushing plant compatible with the equipment of the screening plant, powder grinding plant, and coal wash plant, such as vibrating screens, 6 Types of Coal Crusher: Which Is Best for Crushing My 2020年8月12日 This study shows the performance of a currently running vertical roller coal mill (VRM) in an existing coalfired power plant In a power plant, the coal mill is the critical equipment, whose An investigation of performance characteristics and Section of coal bowl mill Table 1 Guaranteed coal conditions for mill performance evaluation Coal Moisture % 20 Coal HGI 55 Mill Outlet Temperarure °C 80 Mill Air Flow T/hr 102 Coal Fineness (% passing trough 200 mesh) 70% passing through 200 mesh and 90% passing through 50 mesh Differental Pressure 300 mmwc Coal Output from Mill 609 t/hrA Study on 500 MW Coal Fired Boiler Unit’s Bowl Mill
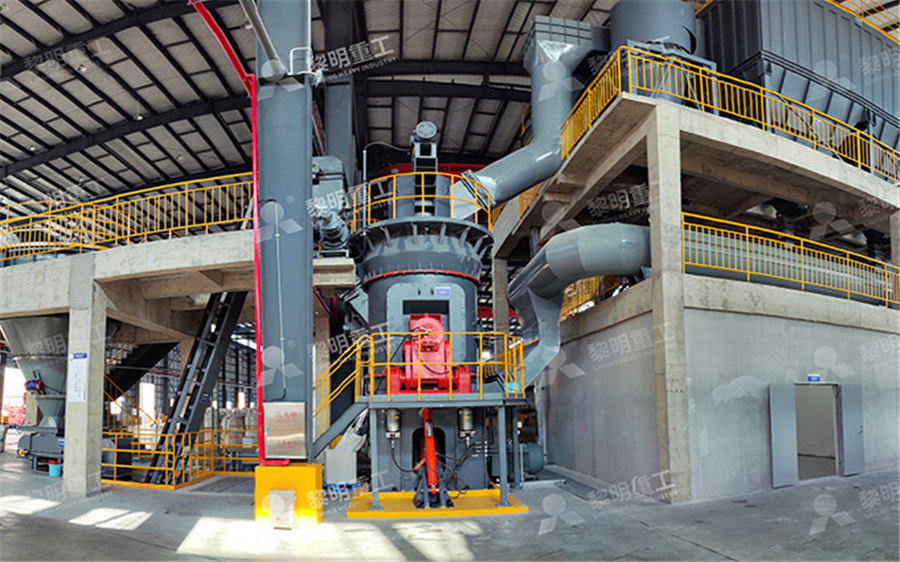
Coal Ball Mill Grinding for Different Kinds of Pulverized Coal
The raw material of coal powder is coal with various hardness, and it drying in the coal mill grinding process to obtain finished coal powder which can be efficiently burned Coal ball mills are widely used in the cement industry and thermal power generation industry, and are also suitable for metallurgical industry, chemical industry, sugar industry and other fieldsmill bottom Journal loading spring loading is available for maximum simplicity or hydraulic loading for flexibility Gear reducer independent heavy duty planetary reducer with external lubrication designed specifically for Vertical Roller Mill application Low pressure drop mill housing and bowl geometryRaymond Bartlett Snow Milling Technologies SpecializedInBuilt Reliability for Cement Plant Application: Raw Material, Cement, Slag, Coal and Minerals In May 2019, AMCL signed an exclusive Licensing Agreement for the design, manufacture, erection, commissioning and after sales service with UBE Machinery Corporation, Ltd (UBE) of VRMs in India, Bangladesh and NepalVRM – AMCL Machinery Limited2024年10月11日 Coal is the most abundant fossil fuel on Earth Its predominant use has always been for producing heat energy It was the basic energy source that fueled the Industrial Revolution of the 18th and 19th centuries, and the industrial growth of that era in turn supported the largescale exploitation of coal deposits Since the mid20th century, coal has yielded its Coal mining Definition, History, Types, Facts Britannica
.jpg)
Lime Quarry Can You Dig It
This plot of land contained a large deposit of Limestone, an integral component of the smelting and steelmaking processes A quarry was established on the property, and a contractor was hired to quarry, crush, and load stone onto railroad cars, which were then shipped to the steel mill and various smelting operations in PuebloUnderground mining is a complex process that involves several steps, including drilling and blasting, loading, and transporting the limestone 20tph Coal Ball Mill For Clean Coal Powder Production Line In Vietnam Read More 85tph Cement Ball Mill Put Into Operation In Indian Cement Plant Read MoreWhat is the Method of Mining Limestone? ball mills supplierIMSBC CODE 2018 EDITION – Errata and Corrigenda – November 2018 5 BROWN COAL BRIQUETTES (appendix, continued) Carriage n paragraph 52, I replace “2000 parts per million (ppm)” and “1000 ppm”, “2,000 parts with per million (ppm)” and “1,000 ppm”, respectively COAL Description Move the paragraph beginning with “Coal shall be classified” and ending with “in International Maritime Solid Bulk Cargoes Code (IMSBC Code)1927 First Loesche coal mill delivered for the Klingenberg power station in Berlin 1953 500th coal mill plant sold worldwide 1961 Introduction of hydraulic spring assembly system 1965 Construction of first pressure mill (LM 122 D) 1980 Delivery of first modular coal mill (LM 263 D) 1985 Delivery of first selfinerting coal grinding plant (LM 212 D) for the steel industry (PCI LOESCHEMILLS
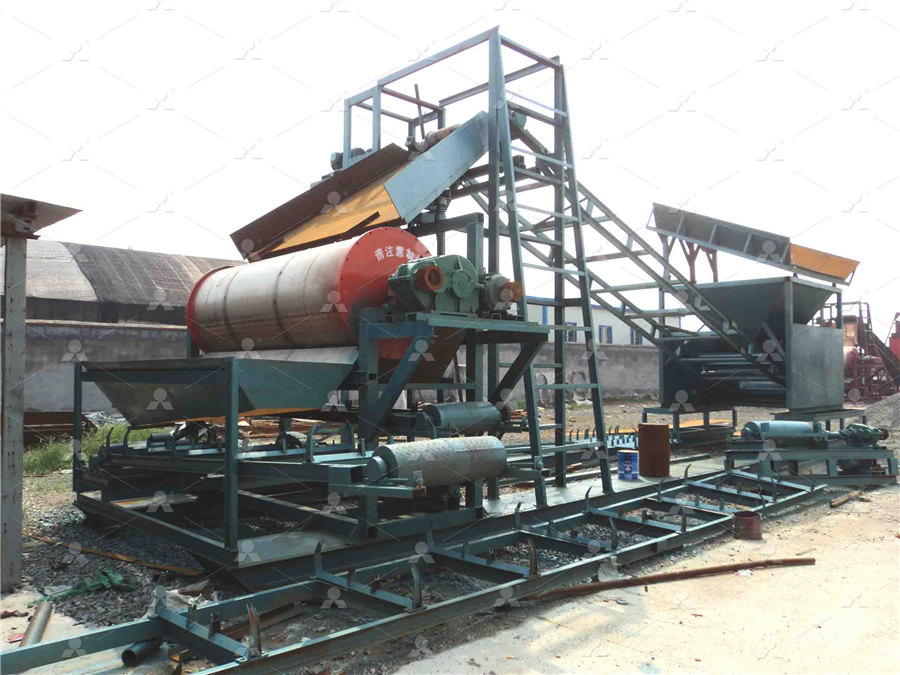
Coal ash and limestone interactions in quicklime production
2021年9月15日 Limestone and coal fuels were all considered typical for industrial applications Table 2 Composition (wt%) of the limestone used in lab experiments This was followed by milling for 2 min to a fine powder in a ball mill the corresponding ash load on the rotary kiln studied would be 565 kg/h If, however, the kiln was Coal Coal / Limestone Coal BiomassLimestone High Pressure Feeders Low Pressure Feeders Batch Scales Pulverizer To CFB Hourly calibration of load cell circuity is preformed automatically and eliminates system drifts due to time and varying mill inlet centers, rates up to 70 tons/hour and design pressures PASS Stock Coal and Limestone Feed SystemsPrevious Post Next Post Contents1 COAL PREPARATION AND FIRING11 INTRODUCTION12 2COAL RESERVES13 CHARACTERISATION OF COALS BY CHEMICAL131 31 Major components132 32 Minor Components14 4CHARACTERISATION BY PHYSICAL AND MECHANICAL PROPERTIES141 41 Coal Storage142 42 Variation of Physical and COAL PREPARATION AND FIRING INFINITY FOR CEMENT EQUIPMENTcarried out on a coal mill, the Lining Coal Mill always experiences wear and tearthis causes the performance of the coal mill to be not optimal Before modifications, the Lining Housing used wearresistant material BS EN 10029 Because it was assessed using wearresistant material BS EN 10029, it often experienced wear and tearWEAR ANALYSIS OF VERTICAL COAL MILL PLATE APS
.jpg)
Types of Crushers: Choosing the Right One for Each Stage
2024年7月17日 They can crush low to medium hardness materials such as limestone and coal, as well as materials with moisture content below 15%, suitable for both dry and wet crushing Hammer crushers have a reduction ratio of up to 50, a feed size of up to 1,000 mm, and a maximum output capacity of 3,000 t/h2019年10月1日 Request PDF Wet and dry grinding of coal in a laboratoryscale ball mill: Particlesize distributions In this study, experimental data for wet and dryground coal samples under wet and dry Wet and dry grinding of coal in a laboratoryscale ball mill: Particle First designed for coal fired power plants and steel mill service to feed coal, limestone, mill scale, dolomite, iron ore pellets, fluorspar and coke, the Model “MH” has been subjected to extreme environmental conditionssuch as abrasive dusts, corrosive fumes, wide temperature fluctuations and vibrationswithout any detrimental effects on MH Heavy Industry Weigh Belt Feeders Thayer ScaleMill Speed Capacity Desired Coal Properties Feed Size Total Moisture Grindability (HGI) Abrasiveness Prod Fineness thru 200 Mesh Standard Screen Typical Air to Coal Ratio at 100% Mill Load Specific Power @ 100% Mill Load Typical Conditions CrusherDryer Mill PA Fan Total StartUp Time NoiseMill Only Approx Dimensions Mill Dia (D)A Comparison of Three Types of Coal Pulverizers Babcock Power
.jpg)
HighEfficiency Vertical Coal Mill Enhancing Coal Pulverization
The coal vertical mill, also referred to as the vertical roller coal mill, is an advanced equipment developed by our company It combines modern technology with our extensive experience in powder manufacturing This coal pulverizer efficiently integrates coal grinding and drying, providing highperformance and energysaving features