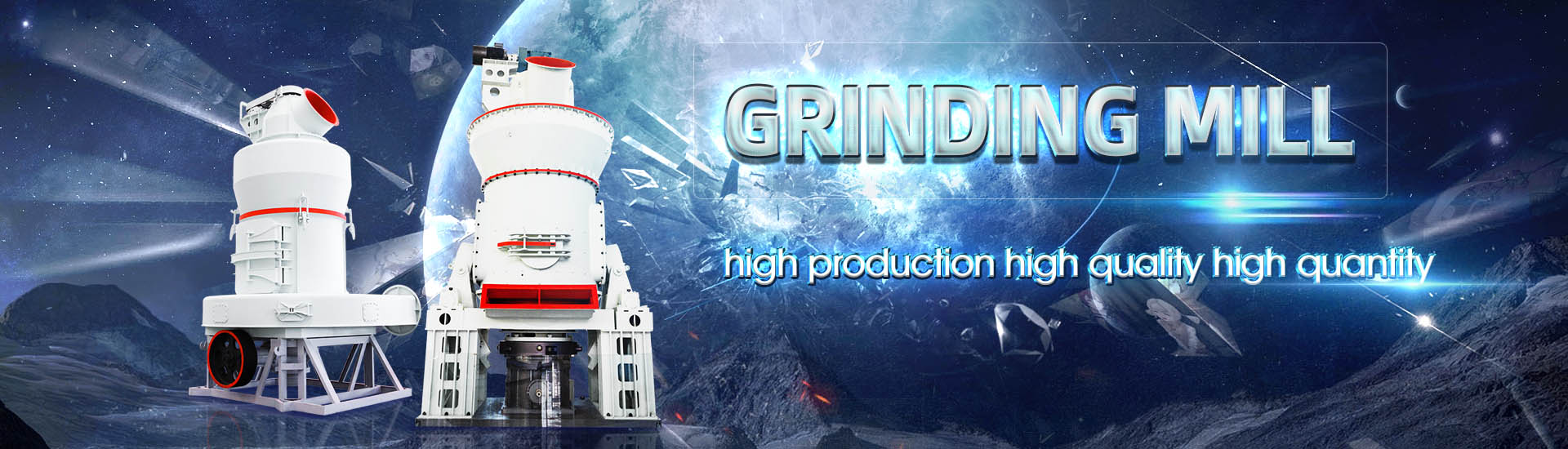
Traditional method to refine calcite ore powder into pig iron
.jpg)
From Ore to Iron with Smelting and Direct Iron Reduction
2017年10月17日 The Hismelt process employs a single smelt reduction vessel (SRV) where iron oxide fines are injected deep into hot metal melt, which instantly reduces the ore to produce iron and carbon monoxide Flux and coal are also injected into the bath near the bottom, which Following three distinct operations are involved in the manufacturing process of pigiron: (1) Dressing (2) Calcination and roasting (3) Smelting (1) Dressing: The iron ores as obtained How to Manufacture Pig Iron: How Pig Iron is made?The whole process consists of four steps, ie, heating, reduction of iron ore, carburization and melting of pig iron The solutionloss of carbon and the reduction of iron ore are coupled and Mechanisms of Pigiron Making from Magnetite Ore Pellets Sponge iron powder The Höganäs process is a direct reduction method for production of sponge iron powder using magnetite ore (Fe3O4) and carbon as raw materials The reduction process Iron Manufacturing process related to the specified manufacture(s)
.jpg)
Iron Making: Exploring Traditional and Innovative Techniques for
limestone reacts with impurities in the iron ore to form slag, which is removed from the furnace The iron produced in the blast furnace is called pig iron and contains 45% carbon, along with To obtain pig iron from iron ore there are two main reactions; one is reduction by carbon and the other carburization Both of them are endothermic reactions and therefore to make pig iron Production of Pig Iron from Magnetite Ore–Coal Composite 2023年8月23日 Three groups of materials are needed to smelt ore into iron: Iron carriers such as iron ores or scrap metal Fuels and reducing agents such as coke, coal, oil and gas From Ore to Steel SpringerLinkDivided into seven chapters, it discusses the following topics: raw materials for steel production (coking coal, iron ore, slagforming agents and fluxes, scrap, ferroalloys and prereduced Operations and Basic Processes in Ironmaking SpringerLink

(PDF) Determination of Total Iron Content in Iron
2016年1月15日 Total iron and ferrous iron contents were determined with the standard titrimetric method using potassium dichromate as titrant after reduction of the iron (III) by tin (II) chloride and/or 2020年8月19日 Throat: zone for charging the burden [ferric charge + reductant (coke)]The blast furnace gases circulate through the throat of the furnace toward the dry and wet cleaning systems The temperature in the throat is 200–250 °C, the pressure is around 15 atm (there are blast furnaces in Russia and other countries that operate with bigger excesses of pressure), Production of Iron in the Blast Furnace SpringerLink2024年4月7日 What is iron ore Iron ore is a mineral aggregate that contains iron element or iron compound and can be used economically It can be used for refining elemental pig iron, steelmaking and many other purposes About 98% Iron ore uses – types of iron ores and the specific 2017年10月10日 Roasting or calcination of the ore oxidizes some of the sulfur, phosphorus and arsenic impurities Sulfur oxide is volatile and evaporates off or is washed out Iron is mainly extracted from hematite (Fe 2 O 3) and magnetite ores Natural or direct shipping iron ores contain between 5070% iron and can be fed directly into the blast furnaceIronmaking 101 – From Ore to Iron with Blast Furnaces
.jpg)
How to Extract Iron from Hematite: Methods and Plants
2023年2月15日 If it is difficult to recover fine ore particles smaller than 10μm by other methods, the flotation separation method can be adopted At present, froth flotation is commonly used Its principle is to grind the hematite ore into a slurry by adding water to the flotation machine, and then stir and aerate to produce a large number of dispersed bubbles2023年10月6日 The blast furnace can also produce ferromanganese and ferrosilicon needed for steelmaking The main product of blast furnace ironmaking is pig iron, and its byproducts are blast furnace slag and blast furnace gas Pig iron can be divided into steelmaking pig iron, casting pig iron, and special pig iron according to its composition and useBlast Furnace Ironmaking SpringerLinkGuide for manufacturing and making Pig Iron Following three distinct operations are involved in the manufacturing process of pigiron: (1) Dressing (2) Calcination and roasting (3) Smelting (1) Dressing: The iron ores as obtained from mines are crushed into pieces of size of 25 mm diameter This is achieved in the rock crushers of ordinary type The crushing of ores helps in How to Manufacture Pig Iron: How Pig Iron is made?2024年3月17日 Steel making is a sophisticated process that turns iron ore into steel, involving methods like the Blast Furnace and Electric Arc Furnace to produce various grades of steel The industry emphasizes sustainability by using additives and recycled materials while ensuring quality through rigorous testing for diverse applicationsA Visual Guide: Steel Making Process Chart Cabaro Group
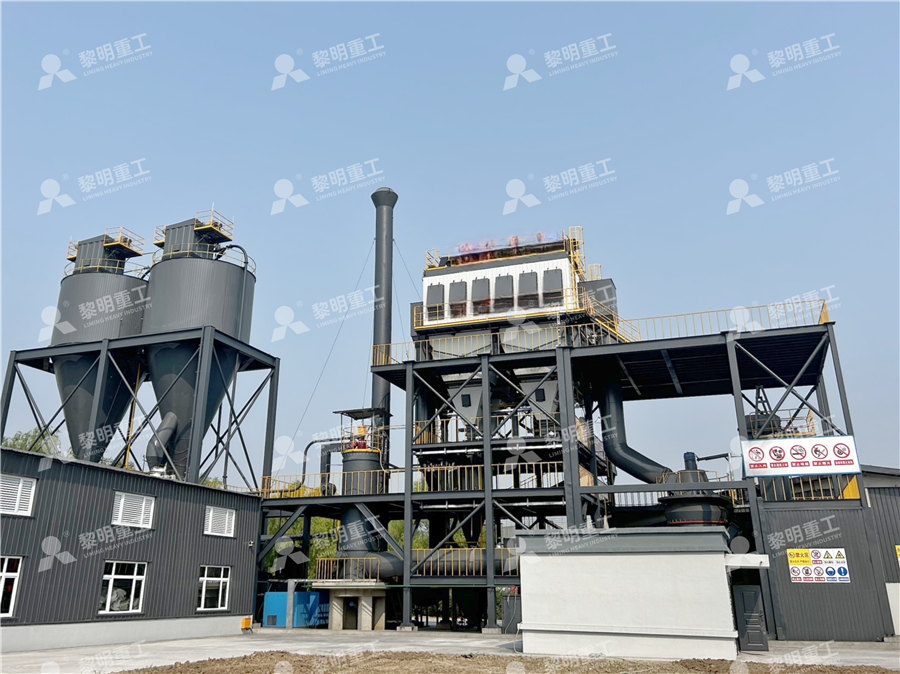
Iron Ore Processing, General SpringerLink
2022年10月20日 Iron ore handling, which may account for 20–50% of the total delivered cost of raw materials, covers the processes of transportation, storage, feeding, and washing of the ore en route to or during its various stages of treatment in the mill Since the physical state of iron ores in situ may range from friable, or even sandy materials, to monolithic deposits with hardness of limestone reacts with impurities in the iron ore to form slag, which is removed from the furnace The iron produced in the blast furnace is called pig iron and contains 45% carbon, along with other impurities Direct reduction iron making: This method involves the reduction of iron ore into metallic iron without melting itIron Making: Exploring Traditional and Innovative Techniques for 2024年8月18日 The term “pig iron” originates from the traditional casting method where molten iron was poured into molds arranged in sand beds, resembling suckling pigs In addition to carbon, pig iron contains several other elements Pig Iron vs Wrought Iron: The Differences Explained2016年11月1日 The pig iron produced from this process contained of 9362%Fe, 35%C, 155%Si, 087%Mn, 005%P, and 0087%SWith this result, the pig iron produced already fulfill the metallurgical specification (PDF) The production of pig iron from crushing plant
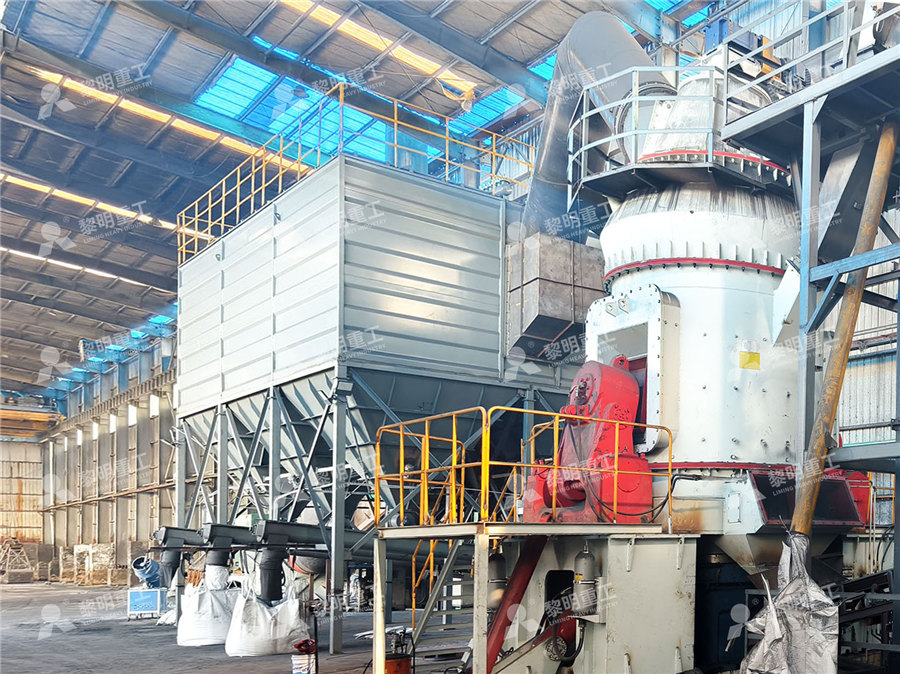
Pig Iron International Iron Metallics Association
Pig iron is the product of smelting iron ore (also ilmenite) with a highcarbon fuel and reductant such as coke, usually with limestone as a flux Merchant pig iron is cold pig iron, cast into ingots and sold to third parties as feedstock for the Pig iron used to manufacture ductile iron Pig iron, also known as crude iron, is an intermediate good used by the iron industry in the production of steelIt is developed by smelting iron ore in a blast furnacePig iron has a high carbon content, typically 38–47 %, [1] along with silica and other dross, which makes it brittle and not useful directly as a material except for limited Pig iron Wikipedia2017年2月16日 PDF Sintering is a thermal agglomeration process that is applied to a mixture of iron ore fines, recycled ironmaking products, fluxes, slagforming Find, read and cite all the research you (PDF) Iron Ore Sintering: Process ResearchGate2006年10月20日 Download Citation Production of Pig Iron from Magnetite Ore–Coal Composite Pellets by Microwave Heating Magnetite orecoal composite pellets with about 10, 15 and 20 mm diameter were rapidly Production of Pig Iron from Magnetite Ore–Coal ResearchGate
.jpg)
Iron Ore Smelting Process Bright Hub Engineering
The ore is loaded into a blast furnace along with measured quantities of coke and limestone Hot combustion air is supplied to the furnace and some form of fuel used to raise the temperature The iron is reduced from the ore by carbon in the coke, the limestone aiding slag separation from the molten iron The slag and molten iron are tapped off from the bottom of the furnace, the A method of onestep reducing melted iron ore concentrate to obtain low sulfur/phosphor pig iron is disclosed The method comprises the following steps: grinding a carbon reducing agent into particles, mixing the particles with iron ore concentrate and additives to obtain a mixed mineral material; adding the mixed mineral material into a molten pool furnace from the feed opening Method of onestep reducing melted iron ore concentrate to 2004年2月1日 The optimum conditions for the demanganisation process have been attained by injection of an oxygen gas–manganese ore mixture at the injection rate of 68 L min1kg1 into molten high manganese (PDF) Demanganisation of high manganese pig iron to produce Steel is primarily produced using one of two methods: iron ore and limestone to produce pig iron Coal traditionally has been a key part of the cokemaking process The coal is crushed and ground into a powder and then charged into an oven where it is heated to approximately 1800°F in the absence of oxygenSteel Production American Iron and Steel Institute
.jpg)
Pig Iron Production – Interstahl
Grey pigiron is produced when the pigiron is cooled slowly and the carbon settles out as graphite on the raw material This type of carbon deposition needs specific amounts of silicon (more than 2%) and manganese (less than 02 2022年8月23日 Preliminary studies have revealed that there are tendencies to achieve more than a 90 % metallization degree from the direct reduction of iron ore/oxides using noncoking coal or charcoal as a (PDF) An Overview of the ReductionSmelting Process 2020年5月26日 Iron ore consists of various oxides of iron (occurring as ironcontaining minerals) mixed with oxides of other metals (such as Al and Si) In the traditional route to produce steel, the ore is first ground and most of the non Overview of the Steel Production Process SpringerIron ore is converted into pig iron in the blast furnace 2 The pig iron is made into steel Strong magnets pull the iron ore particles away from the rest of the powder as the separator Getting the iron out was too expensive at the time Today, due to improvements in processing methods, taconite is one of the most popular ores About us6: Manufacture of Iron and Steel Flashcards Quizlet

233: Metallurgy of Iron and Steel Chemistry LibreTexts
The first step in the metallurgy of iron is usually roasting the ore (heating the ore in air) to remove water, decomposing carbonates into oxides, and converting sulfides into oxides The oxides are then reduced in a blast furnace that is 80–100 feet high and about 25 feet in diameter (Figure \(\PageIndex{2}\)) in which the roasted ore, coke, and limestone (impure CaCO 3 ) are Quality requirements of iron ore for iron production L Lu, D Zhu, in Iron Ore, 2015 164 Summary The BF ironmaking process is currently the dominant process for providing steelmaking raw materials worldwide However, the BF process relies heavily on metallurgical coke and involves cokemaking and sintering operations, which often attract serious environmental Ironmaking Process an overview ScienceDirect TopicsIron ores [1] are rocks and minerals from which metallic iron can be economically extracted The ores are usually rich in iron oxides and vary in color from dark grey, bright yellow, or deep purple to rusty red The iron is usually found in the form of magnetite (Fe 3 O 4, 724% Fe), hematite (Fe 2 O 3, 699% Fe), goethite (FeO(OH), 629% Fe), limonite (FeO(OH)n(H 2 O), 55% Fe), or Iron ore Wikiwand2022年12月7日 Back to Pig Iron: 10,000 Blood Ore with 390 Coke using the Furnace yields: 4000 Pig Iron Congrats you are finished with the extraction process now we are going to start the ‘refining’ process: First we are going to make Grain Steel in the refining oven with Coke and Calx Powder (2:1:1 Ratio): 10,000 Pig Iron with 5000 Coke and 5000 Calx Powder in the refining Mining to metal Guide Mortal Online 2 Forums
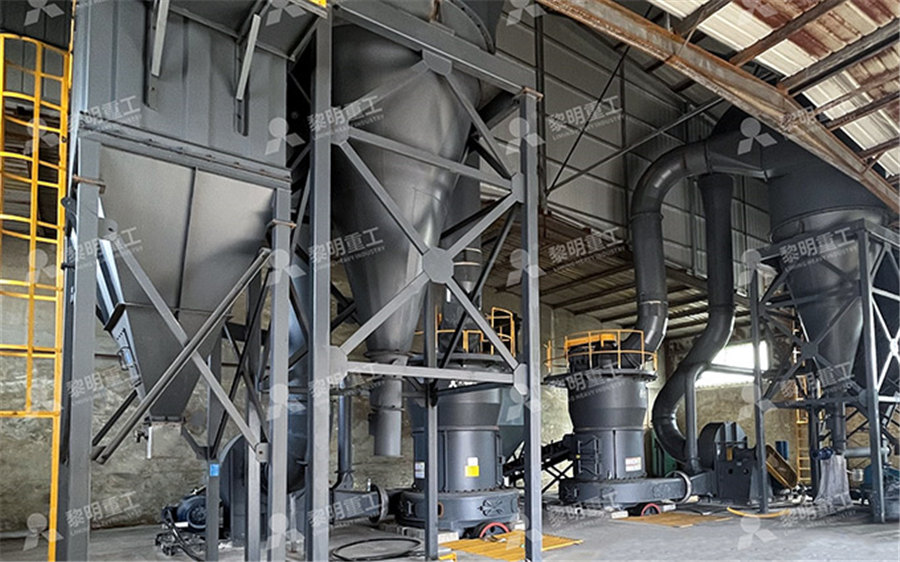
Lowcarbon production of iron and steel: Technology options, economic
2021年4月21日 These processes operate with different feedstocks The BFBOF pathway converts raw iron ore to pig iron and then to steel HM, whereas EAF converts both steel scrap and sponge iron to steel HM DRI converts raw iron ore to sponge iron, a porous, permeable, and highly reactive product that requires treatment with EAF before selling to marketSmelting Pig Iron You can smelt pig iron into Grain Steel at the Refining Oven You can obtain pig iron from extracting Blood Ore at the Extraction Furnace with one of the following catalysts: Coke; Sulfur; Rock Oil; Nitre; 6 catalyst for every 100 Pig Iron Mortal Online 2 Wiki Poggregate2016年1月15日 Total iron and ferrous iron contents were determined with the standard titrimetric method using potassium dichromate as titrant after reduction of the iron (III) by tin (II) chloride and/or (PDF) Determination of Total Iron Content in Iron 2020年8月19日 Throat: zone for charging the burden [ferric charge + reductant (coke)]The blast furnace gases circulate through the throat of the furnace toward the dry and wet cleaning systems The temperature in the throat is 200–250 °C, the pressure is around 15 atm (there are blast furnaces in Russia and other countries that operate with bigger excesses of pressure), Production of Iron in the Blast Furnace SpringerLink
.jpg)
Iron ore uses – types of iron ores and the specific
2024年4月7日 What is iron ore Iron ore is a mineral aggregate that contains iron element or iron compound and can be used economically It can be used for refining elemental pig iron, steelmaking and many other purposes About 98% 2017年10月10日 Roasting or calcination of the ore oxidizes some of the sulfur, phosphorus and arsenic impurities Sulfur oxide is volatile and evaporates off or is washed out Iron is mainly extracted from hematite (Fe 2 O 3) and magnetite ores Natural or direct shipping iron ores contain between 5070% iron and can be fed directly into the blast furnaceIronmaking 101 – From Ore to Iron with Blast Furnaces2023年2月15日 If it is difficult to recover fine ore particles smaller than 10μm by other methods, the flotation separation method can be adopted At present, froth flotation is commonly used Its principle is to grind the hematite ore into a slurry by adding water to the flotation machine, and then stir and aerate to produce a large number of dispersed bubblesHow to Extract Iron from Hematite: Methods and Plants2023年10月6日 The blast furnace can also produce ferromanganese and ferrosilicon needed for steelmaking The main product of blast furnace ironmaking is pig iron, and its byproducts are blast furnace slag and blast furnace gas Pig iron can be divided into steelmaking pig iron, casting pig iron, and special pig iron according to its composition and useBlast Furnace Ironmaking SpringerLink
.jpg)
How to Manufacture Pig Iron: How Pig Iron is made?
Guide for manufacturing and making Pig Iron Following three distinct operations are involved in the manufacturing process of pigiron: (1) Dressing (2) Calcination and roasting (3) Smelting (1) Dressing: The iron ores as obtained from mines are crushed into pieces of size of 25 mm diameter This is achieved in the rock crushers of ordinary type The crushing of ores helps in 2024年3月17日 Steel making is a sophisticated process that turns iron ore into steel, involving methods like the Blast Furnace and Electric Arc Furnace to produce various grades of steel The industry emphasizes sustainability by using additives and recycled materials while ensuring quality through rigorous testing for diverse applicationsA Visual Guide: Steel Making Process Chart Cabaro Group2022年10月20日 Iron ore handling, which may account for 20–50% of the total delivered cost of raw materials, covers the processes of transportation, storage, feeding, and washing of the ore en route to or during its various stages of treatment in the mill Since the physical state of iron ores in situ may range from friable, or even sandy materials, to monolithic deposits with hardness of Iron Ore Processing, General SpringerLinklimestone reacts with impurities in the iron ore to form slag, which is removed from the furnace The iron produced in the blast furnace is called pig iron and contains 45% carbon, along with other impurities Direct reduction iron making: This method involves the reduction of iron ore into metallic iron without melting itIron Making: Exploring Traditional and Innovative Techniques for