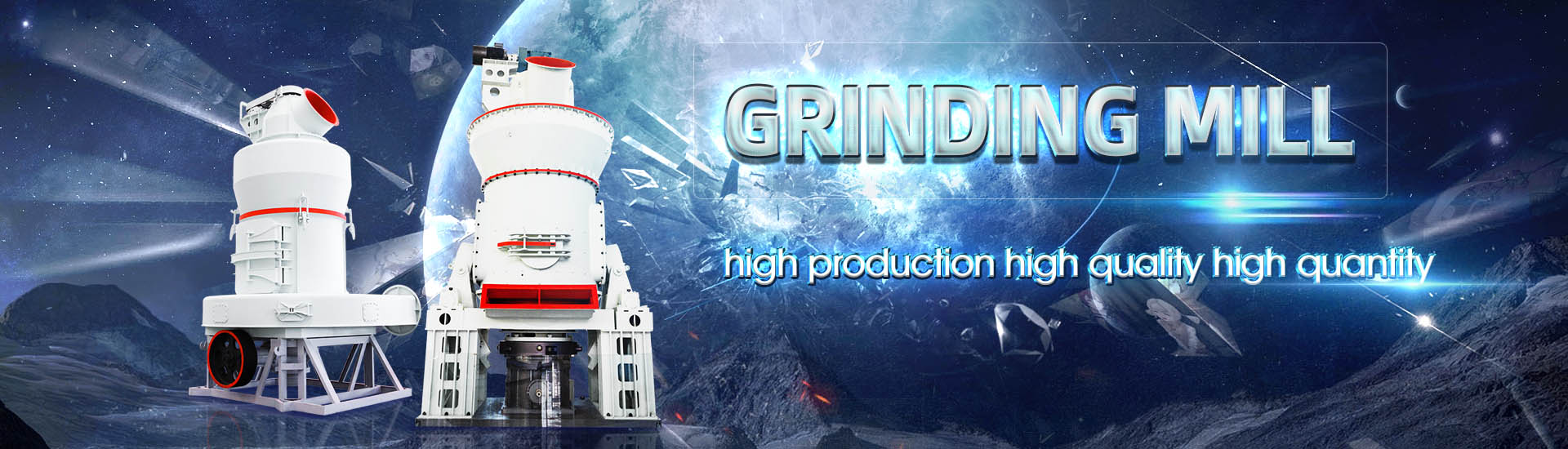
Processing process of raw iron oxide crushing
.jpg)
Iron Ore Processing: From Extraction to Manufacturing
2024年4月26日 Iron ore processing is a complex and vital process that transforms raw iron ore into usable steel From exploration and extraction to grinding, beneficiation, and ironmaking, each stage plays a crucial role in When iron ore is extracted from a mine, it must undergo several processing stages 1 Screening We recommend that you begin by screening the iron ore to separate fine particles below the crusher’s CSS before the crushing stage A The six main steps of iron ore processing Multotec2017年1月1日 Effective technology for a complex wasteless processing of the iron ores has been designed and includes three main components (plats): comminution plant, briquette plant, pigment plant The(PDF) Effective Processing of the Iron Ores2017年3月24日 Sintering is a thermal agglomeration process that is applied to a mixture of iron ore fines, recycled ironmaking products, fluxes, slagforming agents, and solid fuel (coke) The Iron Ore Sintering: Process: Mineral Processing and Extractive
.jpg)
Iron Ore Processing, General
Making iron and steel from iron ore requires a long process of mining, crushing, separating, concentrating, mixing, agglomeration (sintering and pelletizing), and shipping to steel mills 2024年1月1日 Generally, the processes based on the RHF utilize selfreducing iron oxide and coal composite pellets, where iron ore concentrate, coal, additives, and binder are mixed The Direct Reduction of Iron ScienceDirect2015年1月1日 Sintering is the most economic and widely used agglomeration process to prepare iron ore fines for blast furnace use In this chapter, the sintering process is first Iron ore sintering ScienceDirect2018年7月11日 In 1943, E W Davies and coworkers demonstrated the process using anIron Ore Pelletizing Process: An Overview ResearchGate
.jpg)
Iron Ore Characterization Techniques in Mineral
2023年4月27日 While iron is a pivotal metal that is exploited commercially, its extraction from ores, subsequent processing and purification follows a series of steps, and material characterization in terms of physical, chemical and 2022年8月3日 The iron ore processing and production process mainly includes three processes: crushing, grinding and beneficiation In the crushing process, the threestage closedcircuit crushing is more modern and suitable for high Iron ore crushing and screening process SBM Copper processing is a complicated process that begins with mining of the ore (less than 1% copper) and ends with sheets of 9999% pure copper called cathodes, which will ultimately be made into products for everyday useThe Copper Mining and Processing: Processing Copper Iron processing Smelting, Refining, Alloying: The primary objective of iron making is to release iron from chemical combination with oxygen, and, since the blast furnace is much the most efficient process, it receives the most attention Iron processing Smelting, Refining, Alloying

Beneficiation, sintering, and processing of raw materials for the iron
BENEFICIATION of iron ores relates not only to enrichment of the metal content but also to improvements in phy sical characteristics of the ore charged into the blastfurnace The latter is achieved by crushing, sizing, and agglomeration of resultant fines, etc It is universally recognized that preparation of sized ironore burden and2022年1月23日 Beside the processing behaviour of the main constituents of bauxite such as hydrated alumina and silica minerals, the Chapter covers the impact of other constituents, such as titania, iron (PDF) Chemical Processing of Bauxite: Alumina and Silica Minerals 2023年4月5日 The blast furnace and direct reduction processes have been the major iron production routes for various iron ores (ie goethite, hematite, magnetite, maghemite, siderite, etc) in the past few decades, but the challenges of maintaining the iron and steelmaking processes are enormous The challenges, such as cumbersome production routes, scarcity of Recent Trends in the Technologies of the Direct Reduction and 2016年6月20日 Crushing Strength T est, Mineral Processing and Extractive Metallurgy Re view, that the green balls sintering process can change the condition of In terms of iron oxide distribution, Phase and Microstructural Characterization of Iron Ore Pellet
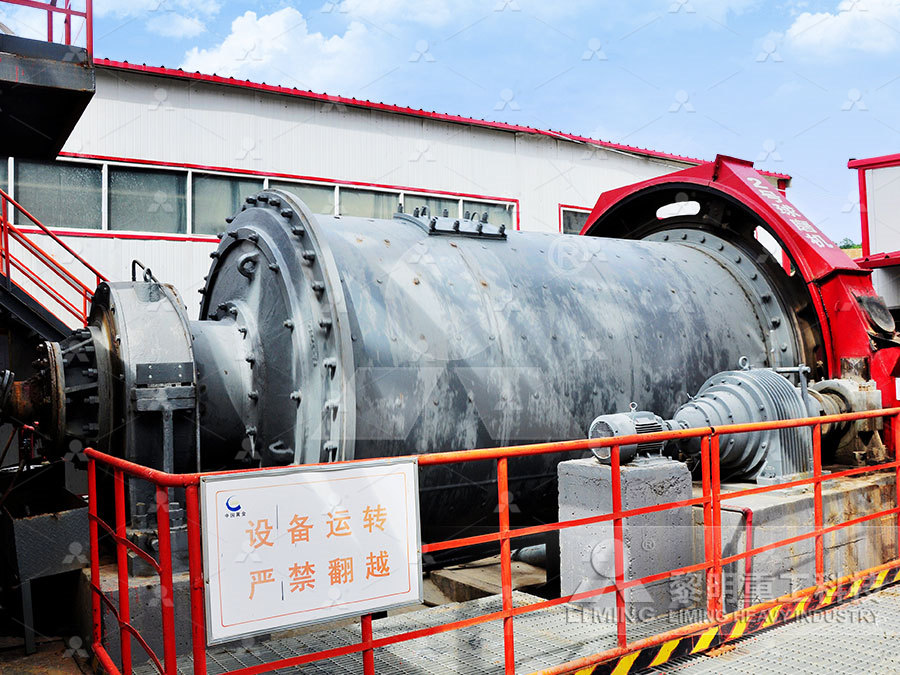
(PDF) The production of pig iron from crushing plant waste using hot
2016年11月1日 A production of pig iron has been conducted from crushing plant waste The process of preparing pig iron was using hot blast cupola (HBC) furnace which was injected with charcoal powder to improve Iron processing Ores, Smelting, Refining: Iron ores occur in igneous, metamorphic (transformed), or sedimentary rocks in a variety of geologic environments Most are sedimentary, but many have been changed by weathering, and so their precise origin is difficult to determine The most widely distributed ironbearing minerals are oxides, and iron ores consist mainly of Iron processing Ores, Smelting, Refining Britannicamineral processing, art of treating crude ores and mineral products in order to separate the valuable minerals from the waste rock, or gangue It is the first process that most ores undergo after mining in order to provide a more concentrated material for the procedures of extractive metallurgyThe primary operations are comminution and concentration, but there are other Mineral processing Metallurgy, Crushing Grinding Britannica2009年1月1日 Process flowsheet has a greater effect on equipment performance and operating conditions For this purpose, performance of two iron ore beneficiation plants with the same equipment and feed Processing of Magnetite Iron Ores–Comparing
.jpg)
How to Extract Iron from Hematite: Methods and Plants
2023年2月15日 Hematite, also spelled haematite, is a weakly magnetic iron ore with better floatability than magnetite and wide distributionIt is one of the most important raw materials for the extraction of iron Its composition is complex pigments includes iron oxide pigments, which also can be natural and synthetic Iron oxide pigments are the most frequently used among colour pigments The colour of pigments is determined by iron oxides: FeO, Fе2О3, Fе3O4 Iron oxide pigments have wide colour palette due to chemical compounds diversity 2 Subject of investigationEffective Processing of the Iron Ores e3sconferences2024年11月23日 Cement Extraction, Processing, Manufacturing: Raw materials employed in the manufacture of cement are extracted by quarrying in the case of hard rocks such as limestones, slates, and some shales, with the aid of blasting when necessary Some deposits are mined by underground methods Softer rocks such as chalk and clay can be dug directly by Cement Extraction, Processing, Manufacturing BritannicaAlumina and iron oxide react: Calcium carbonate continues to react with other oxides and no free lime is yet formed Though tricalcium aluminate is stable here, poorly crystallized mayenite (Ca 12 Al 14 O 33) seems to be formed The reactions at this stage are: 12 CaCO 3 + 7 Al 2 O 3 → Ca 12 Al 14 O 33 + 12 CO 2 4 CaCO 3 + Al 2 O 3 + Fe 2 O 3 Cement Clinker Manufacturing Process with Reactions
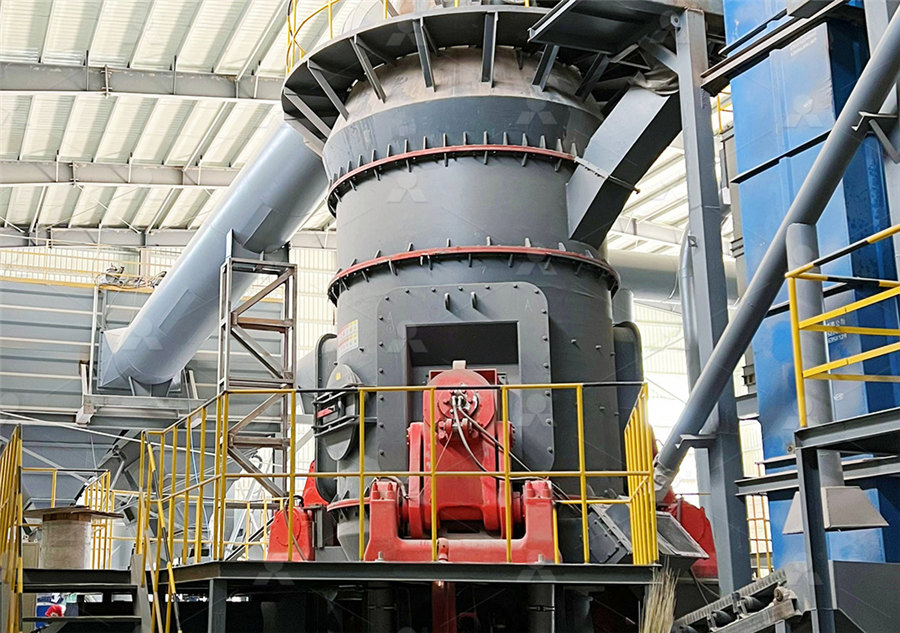
Iron Mining Process Equipment Flow Cases JXSC
Iron mining process, blue, paper dyeing, fertilizer ingredient, baked enamel finishes for autos and appliances, industrial finishes Black iron oxide: as a pigment, in polishing compounds, metallurgy, medicine, magnetic Large raw iron ore for primary crushing are fed into the jaw crusher by Plate feeder and are reduced to 8 inches or Manufacturing process flow 1 Quarrying and Crushing The quarry (where the mining activity is performed) is located 07 km away from the plant and has the main raw materials such as Limestone and shale that is estimated to last for 100 years, the other raw materials (Iron ore, silica sand, gypsum and Pozzolana (pumice) ) are brought from nearbyManufacturing process flow 1 Quarrying and Crushing2013年8月1日 with the best crushing strength, a high raw materials processing rate of 300 t h1, and Throughout the process, the iron oxide canIron ore sintering Part 1 Theory and practice of the sintering process2018年7月11日 Iron Ores and Iron Oxide Materials 50 Bentonite, an inorganic binder, has been the main binder used in the iron ore pelletizing process since the beginning of pellet production in the 1950sIron Ore Pelletizing Process: An Overview ResearchGate
.jpg)
Development of technology for the production of natural red iron oxide
2017年1月1日 The most common inorganic pigment is red iron oxide World production of iron oxide pigments is about 600 thousand tons per year and greatly exceeds the production of other color pigments, with 2019年9月26日 Copper processing is a complex process that involves many steps as the manufacturer processes the ore from its raw, mined state into a purified form for use in many industries Copper is typically extracted from Copper Production: How Is Copper Made? ThoughtCo2023年6月12日 3 Iron oxide copper gold ore Properties of iron oxide copper gold ore Iron oxide copper gold ore refers to the symbiosis of copper ore and gold ore in gold ore in some form Its amount is about 10 million to 4 billion tons 8 Types of Gold Ore Properties and Ways to Process2018年12月11日 In India, ilmenite is considered as a major mineral reserve for the extraction of titanium During the processing of ilmenite to produce titanium dioxide, huge amount of iron oxide is generated and dumped as waste According to an approximation, 07 ton of iron oxide waste is generated for one ton of synthetic rutile production This waste iron oxide has great potential to Carbothermic Reduction of Iron Oxide Waste Generated During
.jpg)
Iron Processing Equipment, Process Flow, Cases JXSC Machine
2019年8月23日 In order to further raise iron content and reduce silicon content, meet the requirements of highquality iron raw materials It adopts a fine screening and regrind process, and the final concentrate grade reaches over 695% Chinese iron process plant was adopted the fixed fine screen, nylon screen surface materialProcessing of Iron Ore The processing of ore involves crushing, screening, washing and in some cases beneficiation and agglomeration Crushing and screening are adopted mainly for sizing the ore and also for removing the adherent gangue minerals Dry and wet grinding is additionally resorted to in some cases The lumps and fines of iron oreOpportunities in Mining of Mineral Ore with Processing and 2023年4月27日 While iron is a pivotal metal that is exploited commercially, its extraction from ores, subsequent processing and purification follows a series of steps, and material characterization in terms of physical, chemical and mineralogical features and behavior is imperative at each stage Some characterization tests rely solely on physical measurements, Iron Ore Characterization Techniques in Mineral ProcessingThe iron ore production has significantly expanded in recent years, owing to increasing steel demands in developing countries However, the content of iron in ore deposits has deteriorated and lowgrade iron ore has been processed The fines resulting from the concentration process must be agglomerated for use in iron and steelmaking This chapter shows the status of the Iron Ore Pelletizing Process: An Overview IntechOpen
.jpg)
SIZE REDUCTION BY CRUSHING METHODS ResearchGate
2017年3月4日 When extracting and processing raw mate rials, because in tertiary crushing process combination of primary and secondary 900% of Iron (II) oxide (Fe2O3) while samples from Pit 5 to Pit 2024年3月20日 Electrochemical production of iron metal can support a decarbonized process for steelmaking Here, we report a lowtemperature, electrochemical cell that consumes lowcost and abundant iron oxide, salt, and water, while producing both iron and the alkaline electrolyte needed for efficient operation of the cell Coproduction of iron, lye, and chlorine leads to a process Electrochemical chloriron process for iron production from iron oxide 2024年11月14日 gold processing, preparation of the ore for use in various products For thousands of years the word gold has connoted something of beauty or value These images are derived from two properties of gold, its colour and its chemical stabilityThe colour of gold is due to the electronic structure of the gold atom, which absorbs electromagnetic radiation with Gold processing Refining, Smelting Purifying Britannica2022年8月3日 The iron ore processing and production process mainly includes three processes: crushing, grinding and beneficiation In the crushing process, the threestage closedcircuit crushing is more modern and suitable for high Iron ore crushing and screening process SBM
.jpg)
Copper Mining and Processing: Processing Copper
Copper processing is a complicated process that begins with mining of the ore (less than 1% copper) and ends with sheets of 9999% pure copper called cathodes, which will ultimately be made into products for everyday useThe Iron processing Smelting, Refining, Alloying: The primary objective of iron making is to release iron from chemical combination with oxygen, and, since the blast furnace is much the most efficient process, it receives the most attention Iron processing Smelting, Refining, AlloyingBENEFICIATION of iron ores relates not only to enrichment of the metal content but also to improvements in phy sical characteristics of the ore charged into the blastfurnace The latter is achieved by crushing, sizing, and agglomeration of resultant fines, etc It is universally recognized that preparation of sized ironore burden andBeneficiation, sintering, and processing of raw materials for the iron 2022年1月23日 Beside the processing behaviour of the main constituents of bauxite such as hydrated alumina and silica minerals, the Chapter covers the impact of other constituents, such as titania, iron (PDF) Chemical Processing of Bauxite: Alumina and Silica Minerals
.jpg)
Recent Trends in the Technologies of the Direct Reduction and
2023年4月5日 The blast furnace and direct reduction processes have been the major iron production routes for various iron ores (ie goethite, hematite, magnetite, maghemite, siderite, etc) in the past few decades, but the challenges of maintaining the iron and steelmaking processes are enormous The challenges, such as cumbersome production routes, scarcity of 2016年6月20日 Crushing Strength T est, Mineral Processing and Extractive Metallurgy Re view, that the green balls sintering process can change the condition of In terms of iron oxide distribution, Phase and Microstructural Characterization of Iron Ore Pellet 2016年11月1日 A production of pig iron has been conducted from crushing plant waste The process of preparing pig iron was using hot blast cupola (HBC) furnace which was injected with charcoal powder to improve (PDF) The production of pig iron from crushing plant waste using hot Iron processing Ores, Smelting, Refining: Iron ores occur in igneous, metamorphic (transformed), or sedimentary rocks in a variety of geologic environments Most are sedimentary, but many have been changed by weathering, and so their precise origin is difficult to determine The most widely distributed ironbearing minerals are oxides, and iron ores consist mainly of Iron processing Ores, Smelting, Refining Britannica
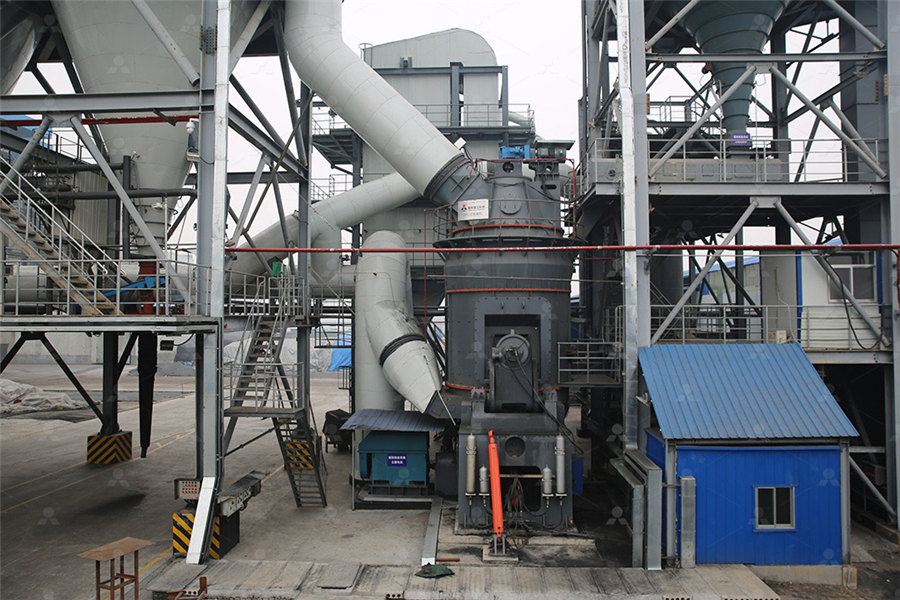
Mineral processing Metallurgy, Crushing Grinding Britannica
mineral processing, art of treating crude ores and mineral products in order to separate the valuable minerals from the waste rock, or gangue It is the first process that most ores undergo after mining in order to provide a more concentrated material for the procedures of extractive metallurgyThe primary operations are comminution and concentration, but there are other