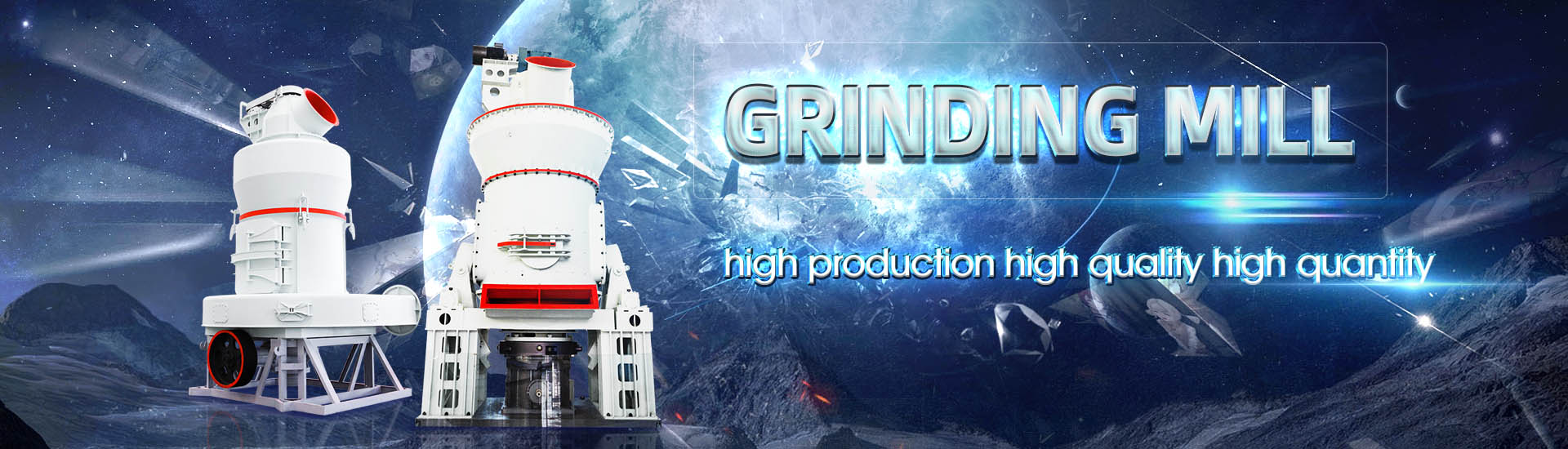
Principle of chemical raw material grinding machine
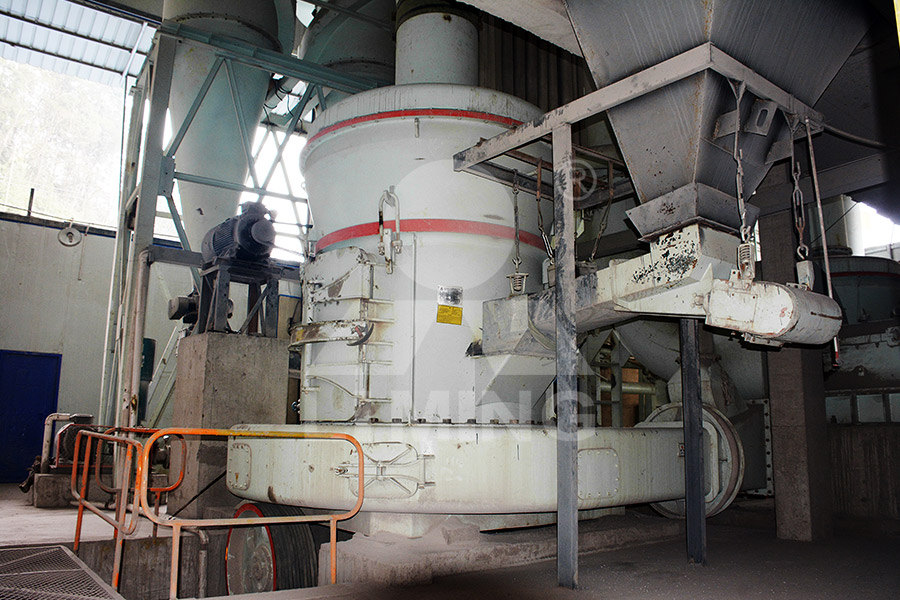
Grinding Machine: Definition, Parts, Working Principle,
2021年5月5日 A grinding machine is a production machine tool used in the manufacturing industry in which the grinding wheel is attached in the tool post and the workpiece is fixed to the work table and when the operation starts it Initial considerations include types of inaccuracy, principles of machine design to achieve high machine stiffness and low deflections levels due to grinding forces, temperature rise or Principles of Modern Grinding Technology ScienceDirect2022年6月24日 Grinding is a manufacturing process which significantly contributes in producing high precision and durable components required in numerous applications such as aerospace, (PDF) A comprehensive review on the grinding process: Roller mill is a type of grinding equipment for crushing materials by pressure between two or more rolling surfaces or between rolling grinding bodies (balls, rollers) and a track (plane, ring, and Roller Mill Springer
.jpg)
Electrochemical Grinding: Definition, Parts or
2021年8月27日 The working principle of electrochemical grinding is When a metal surface is acted upon with an electrolyte under a high current, the metal surface gets oxidized to form an oxide layer (corrosive layer) This layer is This chapter illustrates the different centerless processes and then gives detailed insights into external plunge grinding and the effects of machine design Centerless grinding is a fast and Principles of Modern Grinding Technology ScienceDirectGrinding is the process of removing metal by the application of abrasives which are bonded to form a rotating wheel When the moving abrasive particles contact the workpiece, they act as GRINDING MACHINES Carnegie Mellon UniversityThe article discusses prediction and assessment of environmental impacts (effects) on the design and interdisciplinary arts cotton textile environment for industry 30 cotton roller ginning processWORKING PRINCIPLE OF THE COTTON ROLLER
.jpg)
Ball mill Wikipedia
A section cutthrough of ball mills A ball mill is a type of grinder filled with grinding balls, used to grind or blend materials for use in mineral dressing processes, paints, pyrotechnics, ceramics, and selective laser sinteringIt works on the 2020年6月15日 Industrial hammer mills are employed in particle reduction applications for processing material Though machine designs vary, the basic hammer mill working principle remains the same—uniform size reduction of Understanding the Working Principle of Hammer Mills Cylindrical Grinding Machine: Types, Process Working Principle What is Cylindrical Grinder? Cylindrical Grinding Machine: Types, Process Working Principle :Cylindrical grinders are employed to slice or cut very precise and subtle finishes on materials such as aluminum, carbide, steel or other metalsThey are especially used to work on cylindrical surfaces, rods or other Cylindrical Grinding Machine: Types, Process Working Principle2023年2月22日 All nonconducting materials cannot be machined Tools material and workpiece material should be chemically stable with the electrolyte solution Designing and marking of the tool is difficult, but its life is long, so recommended only for mass production The accurate feed rate of tools is required Application of Electrochemical MachiningElectrochemical Machining (ECM): Process, Working Diagram
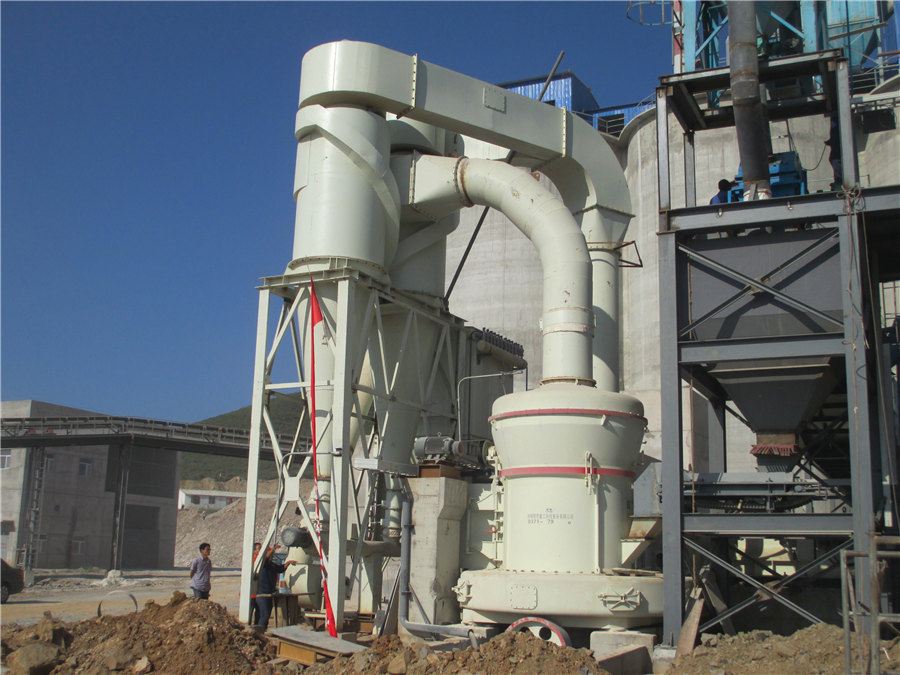
A Comprehensive Guide to the Cement Manufacturing Process
2024年9月5日 Huge machines called excavators dig the limestone out of the earth The extracted limestone is then taken through a crushing plant, which reduces the size to smaller pieces of about 5 inches in size This is important because small pieces are easier to handle and process during subsequent stages 2 Raw material grinding After crushing, the (Horst 1985, p 3A5) Average grinding sizes for the ore can be brought down to 1015 microns at the very most, if using long grinding periods on a product which has already passed a 200 mesh sieve Some specific mills are reported to be available, which are capable of grinding the ore down to sizes of 5 microns or lessCHAPTER 5 GENERAL PRINCIPLES OF MINERAL PROCESSING 2017年6月2日 Autogenous grinding (AG) and semiautogenous grinding (SAG) mills use the material to be ground as the grinding media Autogenous grinding mills use larger rocks to impact and break smaller rocks as the mill rotates Semiautogenous mills are basically the same autogenous mills, but with the addition of balls, similar to those in ball millsHow it Works: Crushers, Grinding Mills and PulverizersJune 2022; ARCHIVE Proceedings of the Institution of Mechanical Engineers Part C Journal of Mechanical Engineering Science 19891996 (vols 203210) 236(2):1107(PDF) A comprehensive review on the grinding process:

Chemical Machining: Definition, Working Principle, Types,
2022年1月12日 This machining process is not magic, but scientifically practical This process uses a strongly acidic or alkaline chemical reagent to remove material from the workpiece This is an ageold process prior to 400 BCE when organic chemicals such as citric acids and lactic acids were used to etch metals to manufacture the desired shape of armors2018年8月17日 As is quite evident (Marty knows that you know!), the ultimate objective of processing a mineral is to extract the maximum value from a raw material There are two end results that one is trying toGrinding Mills — Types, Working Principle For example, grinding media type, size, and amount; different machine speeds; variable loading or feed rate of raw material In addition to reducing particle size, Attritors also can create the highest intensity intimate blending of dissimilar materials Specific chemicals or additives canWe will discuss the principle of the Attritor and its applicationsTypes of Extruders: Application and Working Principle : Extruders are one of the most important component which is used in the manufacturing process Whenever these are combined with feeding, cutting, deairing or other form of Types of Extruders: Application Working Principle
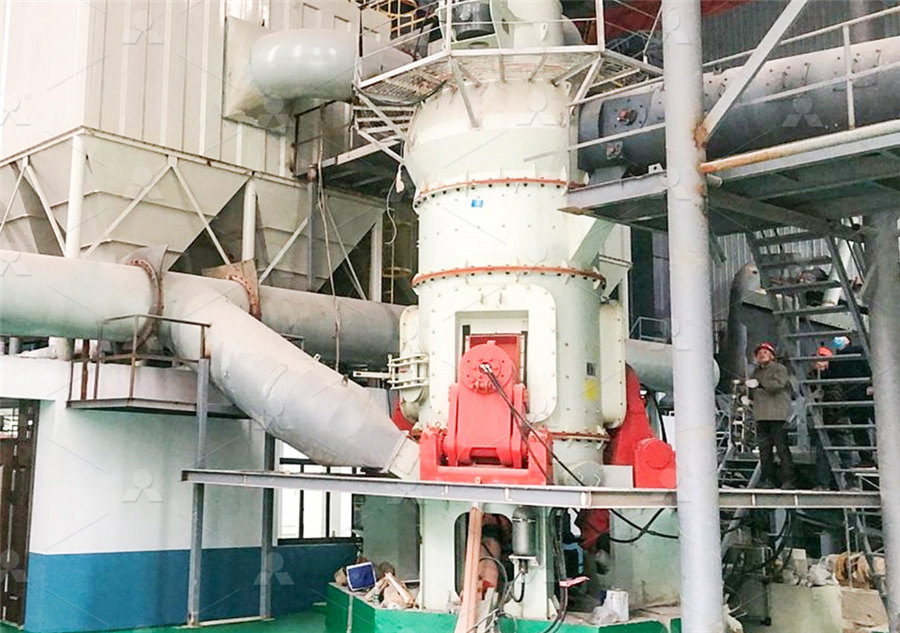
Grinding SpringerLink
2022年2月28日 Generally, grinding process efficiency can mainly be improved by either improving the grinding behavior of the material being ground or enhancing the grinding machines Recently, the use of additives socalled grinding aids, which is applied in a small amount of 001–025 wt% related to the mass of product, has reduced these problems and been 2024年8月11日 Material costs are influenced by multiple factors: Raw material costs: Fluctuations in global commodity markets can significantly impact prices Material utilization rate: Efficient nesting and scrap reduction techniques can improve costeffectiveness Forming costs: Expenses associated with processes like casting, forging, or extrusionMetal Material Selection Principles Methods MachineMFG2023年7月13日 The process of pulping, which turns raw materials like wood chips or recycled paper into pulp slurry, is a basic one in the production of paper Mechanical and chemical pulping are the two main types While mechanical pulping separates fibers from raw materials by grinding them, it may not be appropriate for all types of paperPaper Making Process: From Raw Materials to Finished Products2012年6月1日 The feed material is typically composed of the BFRs and the catalyst, both in powder form As the cylinder starts to rotate, the grinding balls inside the cylinder crush and grind the feed Grinding in Ball Mills: Modeling and Process Control
.jpg)
Ultrafine Powder Grinder Machine Eversun,Sieving machine
The Working Principle of Ultrafine Powder Grinder Machine The raw material enters the crushing chamber through the feed valve and is impacted by the impact hammer, causing the strong collision, friction, and shearing to achieve ultrafine crushing The pulverized material enters the classification chamber with the rising of the airflow2020年9月22日 Grinding machine has been widely used in gold mines in South Africa since 1905 At that time, the grinding machine used river pebble as the grinding medium, which was essentially a gravel mill Later, in order to improve the production capacity of the mill, cast iron balls were used as the medium, so normal gravel mills were evolved into ball mills and rod millsGrinding Machines: Types and Selection Principles Mining Raw mill is also called cement raw mill, similar to cement ball mill, it is an important cement milling equipment used in the cement production process Raw mill is mainly used for grinding cement raw meal in the cement factory production process It is also suitable for metallurgical, chemical, electric power and other industrial mining enterprises to grind various ores and other grindable Cement Raw Mill in Cement Plant for Cement Raw Meal GrindingAcknowledged for high quality, functionality, high efficiency, low power consumption, and cost effectiveness, our range is broadly categorized as Grinding Machines, Food Processing Machines, Mixer Machines, Industrial Pulverizer Machines, Industrial Grinding Machines,
.jpg)
International Journal of ChemTech Research
The principle of attrition and impact is mainly used here appropriate solvent and mechanical process involves subjugation to mechanical forces using grinding machines The former is used mainly for the production of bulk drugs or inorganic raw materials and chemicals like magnesium carbonate or calcium carbonate [4]Publisher Summary Dressing is performed on a grinding wheel in preparation for grinding The aspects of dressing include truing to eliminate deviations from specified form or straightness; dressing to achieve a sharp cutting surface and a uniform random distribution of cutting edges; conditioning to remove the bonds surrounding the abrasive grains and create a more open Principles of Modern Grinding Technology ScienceDirectwidely applied in chemical raw materials, nonmetallic processing, refractory materials, and other industries, and is suitable for dry fine grinding of mineral raw materials with Mohs hardness below 6 (such as talc, causticburned magnesia powder, kaolin, wollastonite, gypsum, lime, bentonite, etc), and the particle size can be adjustedRoller Mill SpringerWorking Principle Of Animal Feed Grinding Machine The working principle of the animal feed grinding machine The raw material falls into the inlet of the animal feed grinding machine by gravity from the top of the crusher, and the falling speed is about 164~328m/s The raw material is hit by the hammer for the first time on the top of the Animal Feed Grinding Machine pelletrichi
.jpg)
From raw materials Extracting raw materials Raw material
Raw material preparation I: Storage and homogenisation Raw material preparation II: Drying and raw grinding Burning The burning of the raw meal at approx 1,450°C is carried out in Lepol or preheater kilns that work by varying methods, the main difference being in the preparation and preheating of the kiln feed By chemical conversion, a 2021年9月28日 What Is the Working Principle of Grinding Machines? During the grinding process, the grinding surface of the grinder tool is evenly coated with abrasive If the material hardness of the grinding tool is lower than that of the workpiece, when the grinding tool and the workpiece move relative to each other under pressure, the abrasive has sharp edges and What Is Grinding and Its Working Principle and Type?Grinding is the common collective name for machining processes that utilize hard, abrasive particles as the cutting medium The grinding process of shaping materials is probably the oldest in existence, dating from the time prehistoric humans found that they could sharpen their tools by rubbing them against gritty rocksGrinding Processes SpringerLinkThe vertical cement mill is largescale cement grinding machine With advantages of energyefficient and stable quality, vertical roller mill is widely applied to many industries, such as cement, power, metallurgy, chemical and nonmetallic mining industry and etc As a typical type of Cement Mill, vertical cement mill set crushing, drying, grinding, grading transportation in one, it grind Vertical Cement Mill, Vertical Roller Mill Buy Cement Mill From
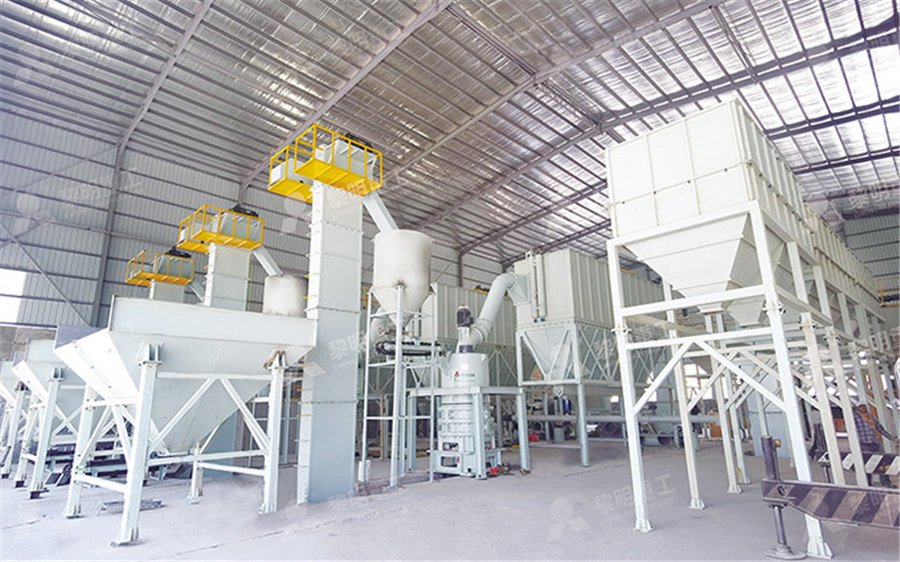
Electrochemical Grinding: Learn Components, Working Principle
2023年8月12日 Disadvantages of Electrochemical Grinding Electrochemical Grinding comes with some drawbacks or disadvantages These include: Low Metal Removal Rate: The rate at which material is removed during the process is relatively slow, typically around 15mm/s, which can impact productivity for highvolume production requirements; High Power Consumption: The article discusses prediction and assessment of environmental impacts (effects) on the design and interdisciplinary arts cotton textile environment for industry 30 cotton roller ginning processWORKING PRINCIPLE OF THE COTTON ROLLER A section cutthrough of ball mills A ball mill is a type of grinder filled with grinding balls, used to grind or blend materials for use in mineral dressing processes, paints, pyrotechnics, ceramics, and selective laser sinteringIt works on the Ball mill Wikipedia2020年6月15日 Industrial hammer mills are employed in particle reduction applications for processing material Though machine designs vary, the basic hammer mill working principle remains the same—uniform size reduction of Understanding the Working Principle of Hammer Mills
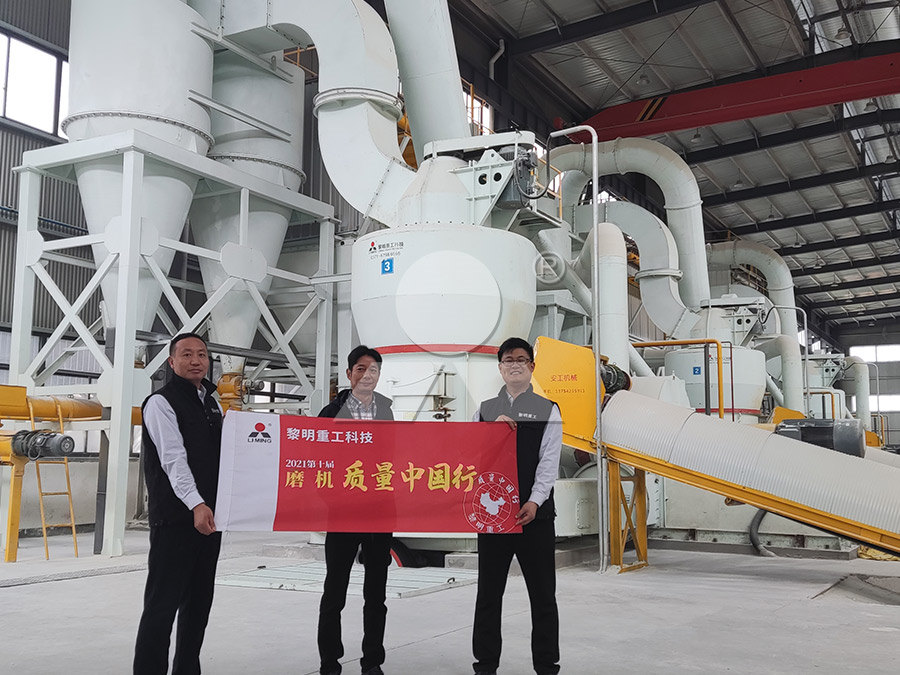
Cylindrical Grinding Machine: Types, Process Working Principle
Cylindrical Grinding Machine: Types, Process Working Principle What is Cylindrical Grinder? Cylindrical Grinding Machine: Types, Process Working Principle :Cylindrical grinders are employed to slice or cut very precise and subtle finishes on materials such as aluminum, carbide, steel or other metalsThey are especially used to work on cylindrical surfaces, rods or other 2023年2月22日 All nonconducting materials cannot be machined Tools material and workpiece material should be chemically stable with the electrolyte solution Designing and marking of the tool is difficult, but its life is long, so recommended only for mass production The accurate feed rate of tools is required Application of Electrochemical MachiningElectrochemical Machining (ECM): Process, Working Diagram2024年9月5日 Huge machines called excavators dig the limestone out of the earth The extracted limestone is then taken through a crushing plant, which reduces the size to smaller pieces of about 5 inches in size This is important because small pieces are easier to handle and process during subsequent stages 2 Raw material grinding After crushing, the A Comprehensive Guide to the Cement Manufacturing Process(Horst 1985, p 3A5) Average grinding sizes for the ore can be brought down to 1015 microns at the very most, if using long grinding periods on a product which has already passed a 200 mesh sieve Some specific mills are reported to be available, which are capable of grinding the ore down to sizes of 5 microns or lessCHAPTER 5 GENERAL PRINCIPLES OF MINERAL PROCESSING
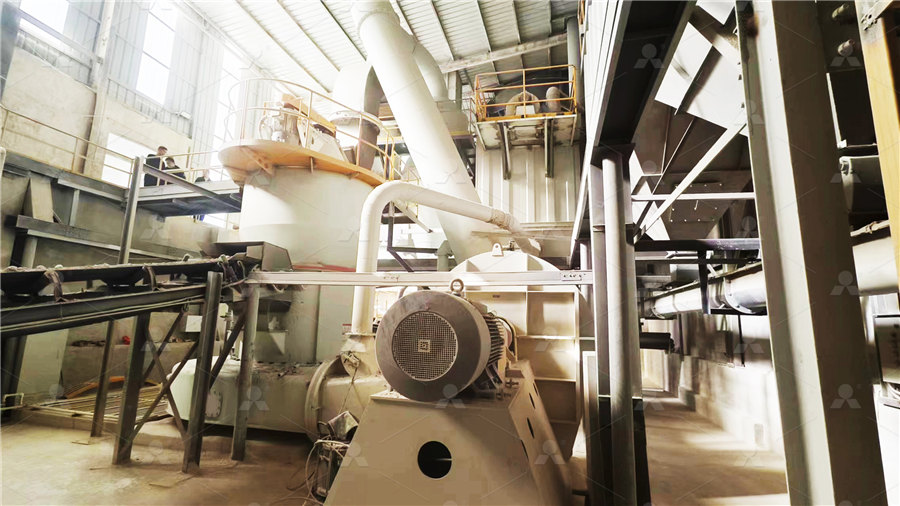
How it Works: Crushers, Grinding Mills and Pulverizers
2017年6月2日 Autogenous grinding (AG) and semiautogenous grinding (SAG) mills use the material to be ground as the grinding media Autogenous grinding mills use larger rocks to impact and break smaller rocks as the mill rotates Semiautogenous mills are basically the same autogenous mills, but with the addition of balls, similar to those in ball millsJune 2022; ARCHIVE Proceedings of the Institution of Mechanical Engineers Part C Journal of Mechanical Engineering Science 19891996 (vols 203210) 236(2):1107(PDF) A comprehensive review on the grinding process: 2022年1月12日 This machining process is not magic, but scientifically practical This process uses a strongly acidic or alkaline chemical reagent to remove material from the workpiece This is an ageold process prior to 400 BCE when organic chemicals such as citric acids and lactic acids were used to etch metals to manufacture the desired shape of armorsChemical Machining: Definition, Working Principle, Types,