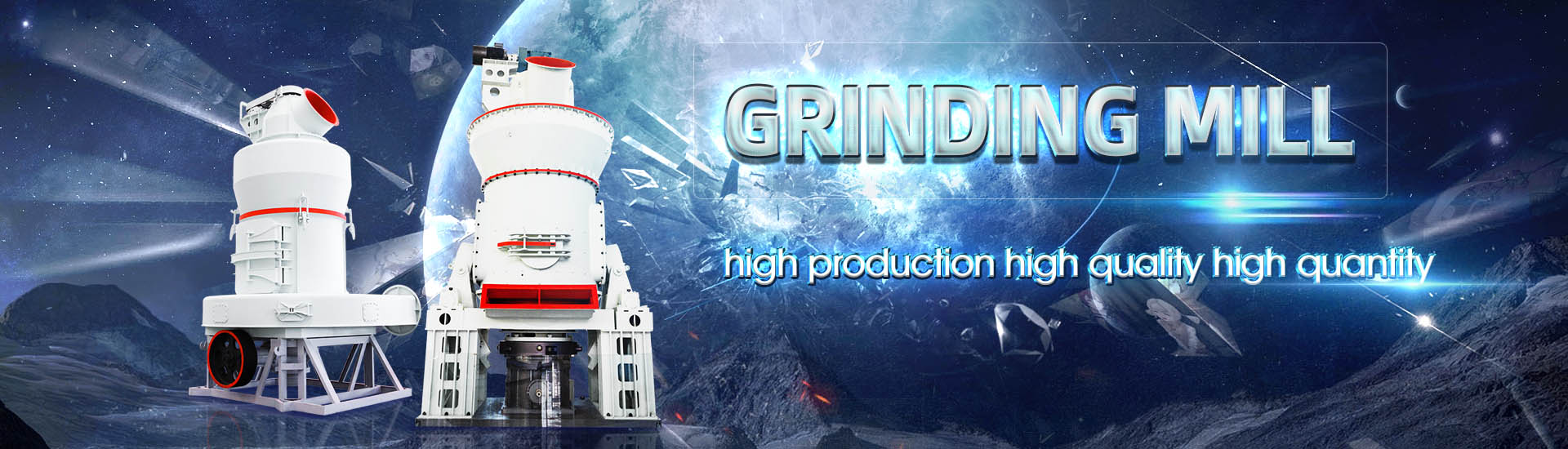
Cement product processing technology
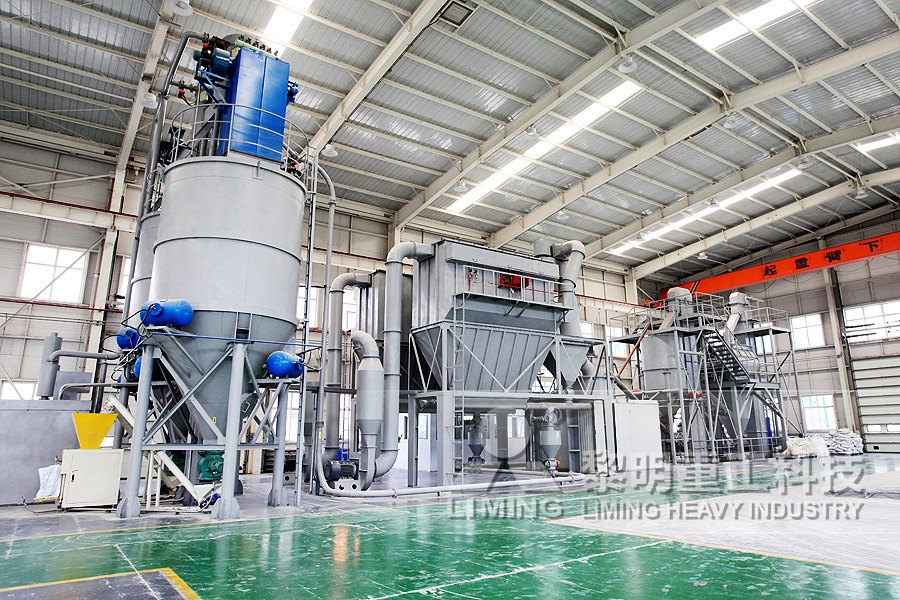
Process technology for efficient and sustainable cement production
2015年12月1日 In recent years the cement industry's NO x emissions have been significantly reduced by optimising existing and proven technologies as well as introducing technologies 2024年6月17日 In the US, EPIXC – Electrified Processes for Industry without Carbon – is aiming to develop the technologies and workforce required to replace fossil fuelbased heating with electric heating in industry, including cement Electric Cement Production: The Technologies2024年6月1日 By setting specific requirements for emissions from the entire cement production process, including raw material extraction, fuel combustion and clinker production, Decarbonising cement and concrete production: Strategies, 2015年12月1日 The objective of this paper is to review the current status of the cleaner cement manufacturing, the cement industry's shifting to alternative raw materials and alternative Process technology for efficient and sustainable cement production
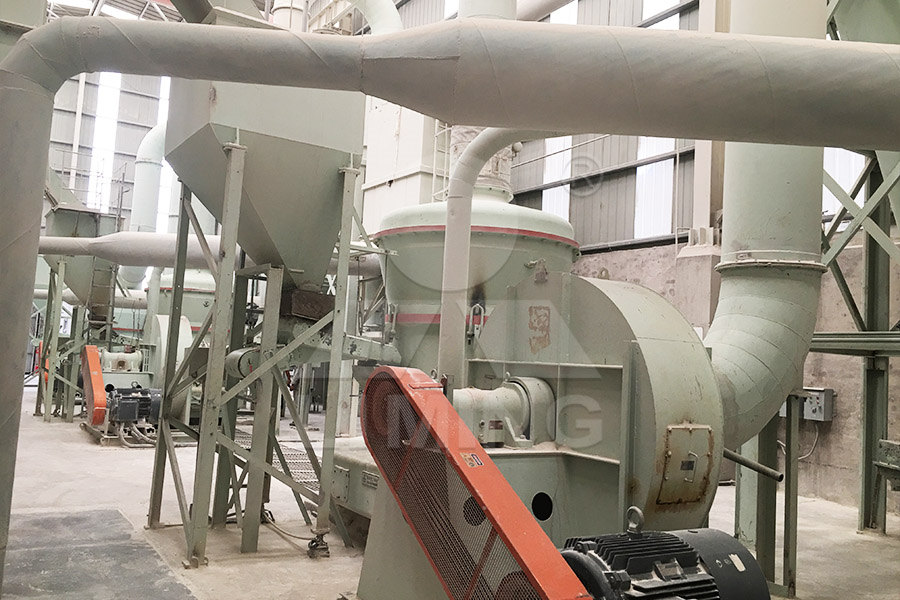
Modernizing cement manufacturing in China leads to substantial
2022年11月17日 The cement manufacturing process mainly includes four steps: resource extraction, raw material preparation, clinker calcination, cement grinding 17,18, and fossil fuel 1 天前 “All Industry 40 systems require data; the higher the data quality, the better the Industry 40 outcomes will be Alongside the production process, the cement laboratory is one of the The Cement Lab and Industry 40 – Cement ProductsThere are four main types of processes used in cement manufacture: Dry Process, Semidry Process, Semiwet Process, and the Wet process In all these processes, the following steps Cement Manufacturing—Technology, Practice, and Development2018年5月9日 This multidisciplinary title on cement production technology covers the entire process spectrum of cement production, starting from extraction and winning of natural raw materials to the finished products including the Cement Production Technology Principles and
.jpg)
Cement and Clay Products Technology SpringerLink
2021年8月10日 The techniques used to manufacture refractory materials have been presented in this chapter, namely the mold and burn process, electric fusion process and ceramic fiber With our marketleading MULTICOR cement processing solutions, we help you meet the defining challenges in today’s marketplace, by dramatically reducing your CO2 emissions in line with new regulations – and ensuring the quality Cement processing equipment Qlar2 Cement manufacturing technology and coprocessing of materials derived from waste 6 21 What is cement? 6 22 Thermal characteristics of a cement kiln 7 23 Cement kiln suitability for processing waste 7 24 Turning waste into a source of raw material and fuel 8 25 Feeding points for waste materials into the cement manufacturing process 9Guidelines for CoProcessing Fuels and Raw Materials in Cement 2019年1月3日 Clinker grinding technology is the most energyintensive process in cement manufacturing Traditionally, it was treated as "low on technology" and "high on energy" as grinding circuits use more than 60 per cent of total energy Clinker grinding technology in cement manufacturing
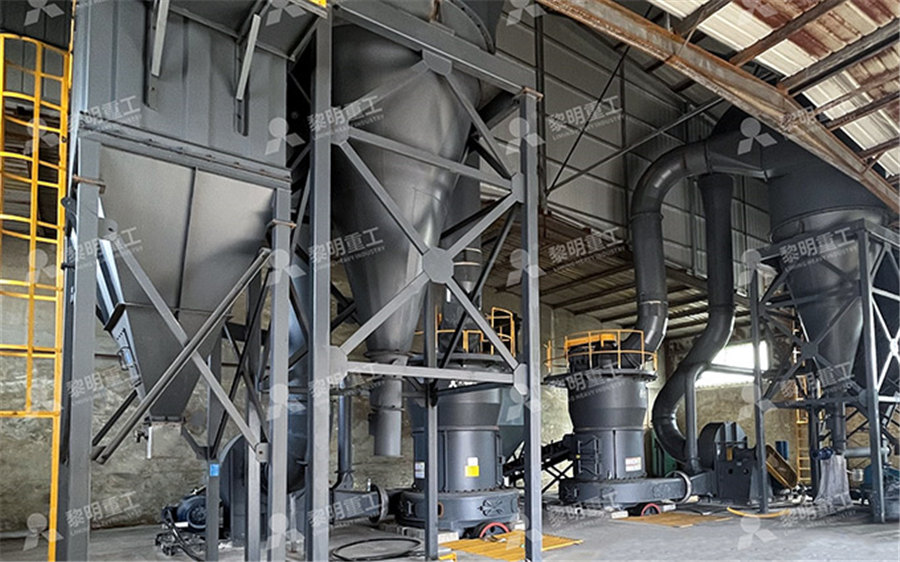
Cement Technology
Adding a bypass ventilation system is an effective way to solve the problem of cement product quality deterioration caused by the use of solid waste raw materials in cement kilns Application of Intelligent Rebar Processing Technology in Cement Engineering EPC Project Construction: ZHANG Pengdi, LI Junyan, SUN Yachao:2021年11月17日 AFR Coprocessing technology consists of different steps that are explained in detail below 111 Receipt of Waste/AFR Material At the cement plant undertaking coprocessing, depending upon the coprocessing rate, either waste or AFR will be receivedCoprocessing of Wastes as AFRs in Cement KilnsStage 2: Grinding, Proportioning, and Blending The crushed raw ingredients are made ready for the cementmaking process in the kiln by combining them with additives and grinding them to ensure a fine homogenous mixture The composition of cement is proportioned here depending on the desired properties of the cement Generally, limestone is 80%, and the remaining 20% How Cement is Made Cement Manufacturing ProcessCement is a global commodity, manufactured at thousands of plants The industry is consolidating globally, but large international firms account for only 30% of the worldwide market The principal and most visible market for cement is the construction industry in a multitude of applications where it is combined with water to make concrete Most modern civil engineering projects, Cement production Climate Technology Centre Network
2FD{P}PC]854]XQ.jpg)
The benefits of coprocessing World Cement
2023年11月27日 According to the technical report ‘Evaluation of the energy performance of cement kilns in the context of coprocessing’ by the European Cement Research Academy, energy efficiency in cement kilns varies between 70 – 80%, depending on the raw materials’ moisture content Overview and achievements of alternative fuels in cement industryM HEAVY TECHNOLOGY carries out fulldesign of process pipeline systems Cement terminal Design of automobile and railway terminals of various capacities Cement Plant Modernization Instrumentation and process control of a cement plant Design of stateoftheart instrumentation and process control loopsCement Plant Design Engineering Consultants M HEAVY TECHNOLOGY2024年2月1日 As a major greenhouse gas, large emissions of CO 2 contribute to the global greenhouse effect In 2019, CO 2 emissions from cement industry reached 24 Gt, accounting for 26% of the total industrial emissions (IEA, 2020a), and the lowcarbon development for the cement industry is extremely urgentOver 90% of countries and regions worldwide produce A review of lowcarbon technologies and projects for the global cement 2024年3月1日 Eliminating the tower also reduces construction and maintenance costs and downtime from tower issues PGNAA data can be combined with XRF lab results for improved process optimization Read the story of a cement Everything about Cement Production Thermo
.jpg)
Cement Production Process Cement Manufacturing
2020年8月25日 Before you send inquiry Please provide us with project information as much as possible: For a complete project: the material availability, the required output capacity, the process technology, your budgetary and Uses of alternative fuels and raw materials in the cement industry as sustainable waste management options Alfonso Aranda UsónAna M LópezSabirónGermán FerreiraEva Llera Sastresa, in Renewable and Sustainable Energy Reviews, 2013 21 Worldwide production One of the wellknown characteristics of cement production is that cement plants are not uniformly Cement Production an overview ScienceDirect Topics2022年4月15日 Cement kiln coprocessing technology has a strong disposal efficiency for the pollutants caused by these pollution sources Land pollution is an inescapable byproduct of social and economic development Overcoming it requires broad socialpolitical concern and Cement kiln coprocessing promotes the redevelopment of 2024年1月12日 Optimising technology Cement manufacturers should strategically incorporate key technologies to enhance operational efficiency and product quality to meet sustainability goals The application of Industry 40 in cement plants represents a transformative shift towards intelligent, interconnected, and datadriven manufacturing [12]Technology: A Transformative Force Indian Cement Review
.jpg)
Coprocessing of Wastes as AFRs in Cement Kilns
without impacting the quality of the clinker Clinker is an intermediate product in the manufacture of cement 102 Coprocessing of Wastes as AFRs in the Cement Kilns Cement kiln coprocessing technology provides opportunities for the sustainable management of wastes from Municipal, Industrial, and Agricultural sectors ThesePDF On Jul 1, 2016, T Belhaj and others published Improvement of Productivity Using Tromp Curve Measurement for Cement Separator Processing Technology Find, read and cite all the research you Improvement of Productivity Using Tromp Curve Measurement for Cement 5 CEMENT –HISTORY In India, Portland cement was first manufactured in 1904 near Madras, by the South India Industrial LtdBut this venture failed Between 1912 and 1913, the Indian Cement Co Ltd, was established at Porbander (Gujarat) and by 1914 this Company was able to deliver about1000 tons of Portland cement By 1918 three factories were established1 Manufacturing Process of Cement Indus UniversityCement is a binder used in production to bond, harden and glue other substances together Cement is rarely used alone, but to bond sand and gravel cement technology, Kothanar Supply Inc is a privately owned company that supplies hydraulic cement and patch mixtures to businesses throughout North America, including the United States(PDF) THE CEMENT MANUFACTURING PROCESS Academia
.jpg)
Improvement of Productivity Using Tromp Curve Measurement for Cement
DOI: 1021608/SJOU201631761 Corpus ID: ; Improvement of Productivity Using Tromp Curve Measurement for Cement Separator Processing Technology @inproceedings{Belhaj2016ImprovementOP, title={Improvement of Productivity Using Tromp Curve Measurement for Cement Separator Processing Technology}, author={Tamim Belhaj 2024年5月23日 Overview of Belt Conveyor Roles within a Cement Processing Plant The conveyor belt for cement industry plays a pivotal role in the smooth and efficient operation of a cement processing plant These belts are integral Conveyor Belt for Cement Industry: Technology CEMTEC manages every project it works on from start to finish, from planning to commissioning The company's product spectrum includes tube mills for grinding a wide range of bulk materials and minerals, as well as rotating drums for thermal treatment (calcination, drying, cooling) and mechanical processing (mixing, washing, conditioning, etc) of different bulk materialsCEMTEC Manages Worldwide Projects for the Cement and Processing 2020年1月28日 Detection and Segmentation of Cement Concrete Pavement Pothole Based on Image Processing Technology January 2020 Mathematical Problems in Engineering 2020(6):113(PDF) Detection and Segmentation of Cement
.jpg)
(PDF) An Insight into the Chemistry of Cement—A Review
2022年12月23日 Even if the technology of cement seems quite well established, the operating parameters of processing, Additionally, a secondary product, calcium hydroxide or port2022年9月6日 Cement, is a grey mineral powder, is fine and milled It contains limestone, clay, and marl as its important proportions [1] The principal application of cement is in the construction industryCement Production Technology Medium2022年11月10日 Cumulative amount and fitted line of the cement kiln coprocessing (CKC) adoption The cumulative (a) number of cases and (b) volume of treated contaminated soil are presented(PDF) Diffusion of Cement Kiln CoProcessing of Contaminated This multidisciplinary title on cement production technology covers the entire process spectrum 43 FEASIBILITY OF AN AFR PROJECT 44 INVENTORY AND MATERIAL CHARACTERISTICS 45 SYSTEMATIC QUALITY ASSESSMENT 46 COPROCESSING OF ALTERNATIVE FUELS 47 SYSTEMIC REQUIREMENTS FOR USING ALERNATIVE FUELS 48 GASIFICATION Cement Production Technology: Principles and Practice PDF
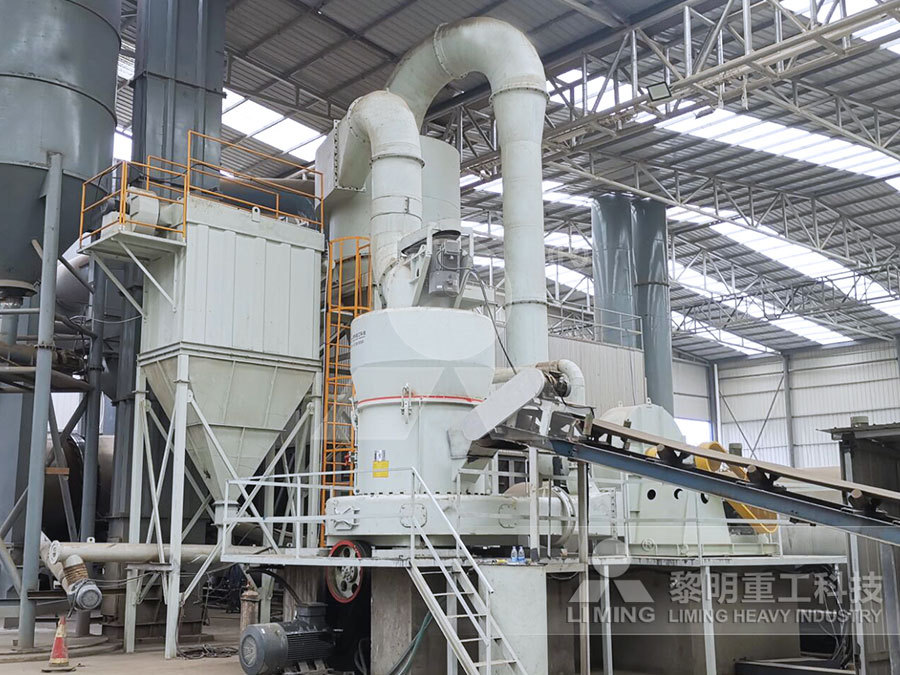
Technology can definitely make cement plants safer
2022年2月1日 ICR engages ChunChun Kumar, Head (VP)OHS, Corporate, JK Cement, in a conversation about safety norms at cement plants, and he sheds light on some important aspects such as use of technology and automation to make the environment at cement processing plants safer for all the employees How do you define a safe plant? A plant []1 basics of mineral resources for cement production 2 raw mix proportioning, processing and burnability assessment 3 fuels commonly in use for clinker production 4 alternative fuels and raw materials 5 pyroprocessing and clinker cooling 6 clinker grinding and cement making 7 composition and properties of portland cements 8Cement Production Technology Principles and Practice2010年2月2日 Request PDF Cement production technology improvement compared to factor 4 objectives In this study, the effects of potential technological improvements in cement industry are compared to Cement production technology improvement compared to With our marketleading MULTICOR cement processing solutions, we help you meet the defining challenges in today’s marketplace, by dramatically reducing your CO2 emissions in line with new regulations – and ensuring the quality Cement processing equipment Qlar
.jpg)
Guidelines for CoProcessing Fuels and Raw Materials in Cement
2 Cement manufacturing technology and coprocessing of materials derived from waste 6 21 What is cement? 6 22 Thermal characteristics of a cement kiln 7 23 Cement kiln suitability for processing waste 7 24 Turning waste into a source of raw material and fuel 8 25 Feeding points for waste materials into the cement manufacturing process 92019年1月3日 Clinker grinding technology is the most energyintensive process in cement manufacturing Traditionally, it was treated as "low on technology" and "high on energy" as grinding circuits use more than 60 per cent of total energy Clinker grinding technology in cement manufacturingAdding a bypass ventilation system is an effective way to solve the problem of cement product quality deterioration caused by the use of solid waste raw materials in cement kilns Application of Intelligent Rebar Processing Technology in Cement Engineering EPC Project Construction: ZHANG Pengdi, LI Junyan, SUN Yachao:Cement Technology2021年11月17日 AFR Coprocessing technology consists of different steps that are explained in detail below 111 Receipt of Waste/AFR Material At the cement plant undertaking coprocessing, depending upon the coprocessing rate, either waste or AFR will be receivedCoprocessing of Wastes as AFRs in Cement Kilns
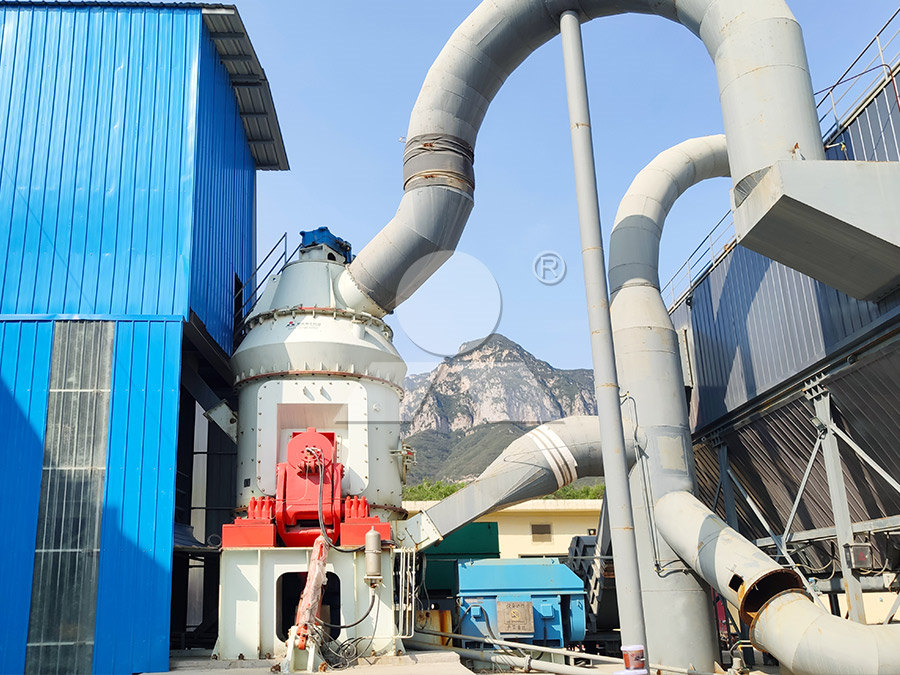
How Cement is Made Cement Manufacturing Process
Stage 2: Grinding, Proportioning, and Blending The crushed raw ingredients are made ready for the cementmaking process in the kiln by combining them with additives and grinding them to ensure a fine homogenous mixture The composition of cement is proportioned here depending on the desired properties of the cement Generally, limestone is 80%, and the remaining 20% Cement is a global commodity, manufactured at thousands of plants The industry is consolidating globally, but large international firms account for only 30% of the worldwide market The principal and most visible market for cement is the construction industry in a multitude of applications where it is combined with water to make concrete Most modern civil engineering projects, Cement production Climate Technology Centre Network2023年11月27日 According to the technical report ‘Evaluation of the energy performance of cement kilns in the context of coprocessing’ by the European Cement Research Academy, energy efficiency in cement kilns varies between 70 – 80%, depending on the raw materials’ moisture content Overview and achievements of alternative fuels in cement industryThe benefits of coprocessing World CementM HEAVY TECHNOLOGY carries out fulldesign of process pipeline systems Cement terminal Design of automobile and railway terminals of various capacities Cement Plant Modernization Instrumentation and process control of a cement plant Design of stateoftheart instrumentation and process control loopsCement Plant Design Engineering Consultants M HEAVY TECHNOLOGY
7TOCS.jpg)
A review of lowcarbon technologies and projects for the global cement
2024年2月1日 As a major greenhouse gas, large emissions of CO 2 contribute to the global greenhouse effect In 2019, CO 2 emissions from cement industry reached 24 Gt, accounting for 26% of the total industrial emissions (IEA, 2020a), and the lowcarbon development for the cement industry is extremely urgentOver 90% of countries and regions worldwide produce