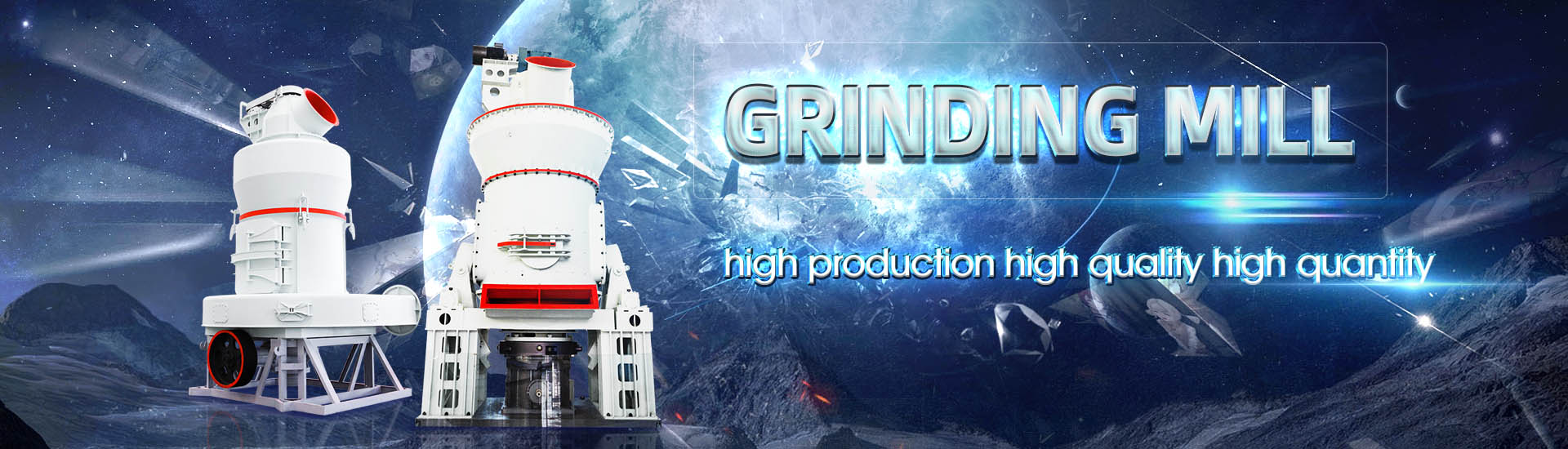
Ore powder making plant mining backfill
.jpg)
Cemented paste backfill for mineral tailings management: Review
2019年12月1日 To dispose mineral tailings in a technical, environmental and economical way, the cemented paste backfill (CPB) technology is proposed and widely adopted Here we 2023年12月25日 Capable mining methods with diverse fill types such as cementitious tail/paste backfill (CTB/CPB) in metal mines and cementitious gangue/ash backfill in coal mines can Innovative mine backfill materials and structures Taylor Francis 2021年11月22日 Critical review on utilising mill tailings, fly ash and slag in mine paste backfilling Explains strength prediction using statistical and artificial intelligence techniques Utilization of mill tailings, fly ash and slag as mine paste backfill 2015年5月13日 The backfilling provides ground support and regional stability, thus facilitating ore removal from nearby regions The large underground voids created by the ore removal are backfilled with the waste tailings in the form of Underground Mine Backfilling in Australia Using Paste
.jpg)
Optimized tailings paste backfill combined with ore
With combined design of concentration plant and backfill plant, the tailings with desired particle sizes and proportions during the mineral processing are chosen to produce CPB without 2022年1月21日 Backfilling of minedout areas is a fundamental component of many underground mining operations The backfill material supports the surrounding rock mass, reduces wasteful dilution, enables a safe working area Backfilling Materials for Underground Mining, Volume 2022年8月13日 Mining with backfill has been used extensively in underground metal mines which is an important way to conduct the green and lowcarbon mining operation Backfill technologies can(PDF) Research Progress on Mining with Backfill 2023年4月13日 In this paper, steel slag (SS), vanadiumtitanium slag (VTS) and vanadiumtitanium iron ore tailings (VTIOTs) were used as the main raw materials to make the mine cemented paste backfill material (CPBM) Through the Properties and microstructure of total tailings
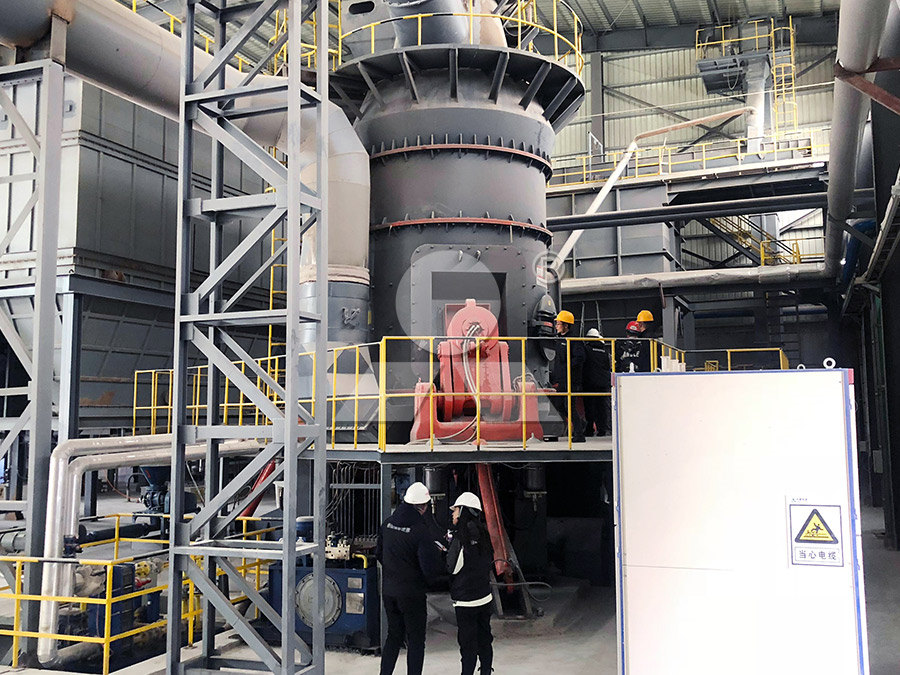
Design of highstrength backfill for a driftandfill mining method
By developing a suit of mix recipes incorporating superplasticiser admixtures, it was possible to achieve the strength demands and the workability of the backfill This paper presents the mines in Montana, Stillwater Mining Company, owns and operates underground mines for PGM ore and a Concentrator plant The process involves mining, transporting the muck (ore and waste) to the surface, milling ore into powder and backfilling the mined out cavities in the underground with tailings from milling operationSIMULATING BACKFILL OPERATIONS FOR UNDERGROUND MINING We Pineer has experience with complete flowsheet development to recover highgrade lithium concentrate powder from hard rock lithium minerals Experienced mining and mineral processing engineers make sure the technology right We Lithium Ore Flotation Plant Pineer Mining Machinerymines in Montana, Stillwater Mining Company, owns and operates underground mines for PGM ore and a Concentrator plant The process involves mining, transporting the muck (ore and waste) to the surface, milling ore into powder and backfilling the mined out cavities in the underground with tailings from milling operationSIMULATING BACKFILL OPERATIONS FOR UNDERGROUND MINING
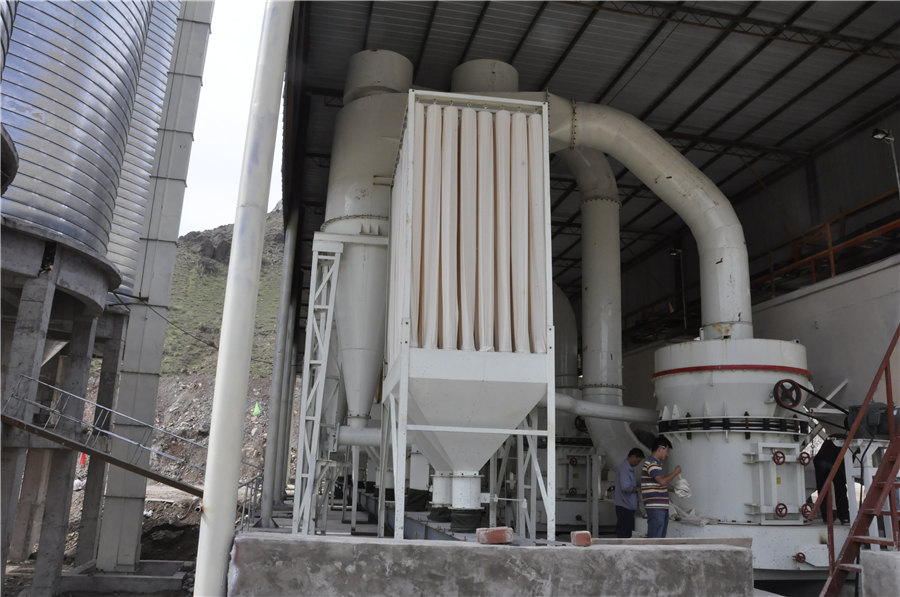
Ore and Backfill Dilution in Underground Hard Rock Mining
Keywords: Ore dilution, backfill, hard rock mining, stoping, measurement, control measures DOI: 101134/S60120 INTRODUCTION Mining is considered as one of the industry among others towards achieving healthy economy of the any developed as well as developing country It is the mainly mining industry which supports the2015年5月13日 Underground mine backfilling is a form of ground improvement that has to be carried out in the mine sites The backfilling provides ground support and regional stability, thus facilitating ore removal from nearby regions The large underground voids created by the ore removal are backfilled with the waste tailings in the form of paste fills, hydraulic fills, and Underground Mine Backfilling in Australia Using Paste Fills and The cylinders cause the powder to roll into marblesized balls (This is like rolling wet, sticky snow into balls to make a snowman) The balls are then dried and heated until they are white hot The balls become hard as they cool The finished product is taconite pellets Steel The taconite pellets are loaded into ore shipsIron Mining Process2022年3月15日 Abstract The ore dilution is generally defined as the degradation of economical and valuable ore with the addition of the unwanted host rock, failed backfilled material and or ore material considered below the cutoff the grade The importance of ore dilution on the profitability of a mining operation is very well known and also well documented, since, it adds to the cost Ore and Backfill Dilution in Underground Hard Rock Mining

Simulating Backfill Operations for Underground Mining
The company’s processes involve mining, transporting ore and waste to the surface, milling ore into powder, and backfilling minedout cavities with tailings from milling operations The circular dependency between mining and backfilling operations, along with variability for each task, makes it difficult to develop a realistic shortterm schedules and efficiently deploy equipment and 2007年5月1日 The mining industry worldwide has typically not conducted the development of mines with the overall design objective of a safe, environmentally sound and aesthetically satisfactory post (PDF) Underground Mining with Backfills ResearchGate2022年4月7日 The company’s processes involve mining, transporting ore and waste to the surface, milling ore into powder, and backfilling minedout cavities with tailings from milling operations The circular dependency between mining and backfilling operations, along with variability for each task, makes it difficult to develop a realistic shortterm schedules and Simulating Backfill Operations for Underground Mining2017年3月4日 In: 10th international symposium on mining with backfill, South Africa, p 205–212 Google Scholar Moghaddam AS, Hassani FP (2007) Yield stress measurement of cemented paste backfill with the vane method and Design and Characterization of Underground Paste
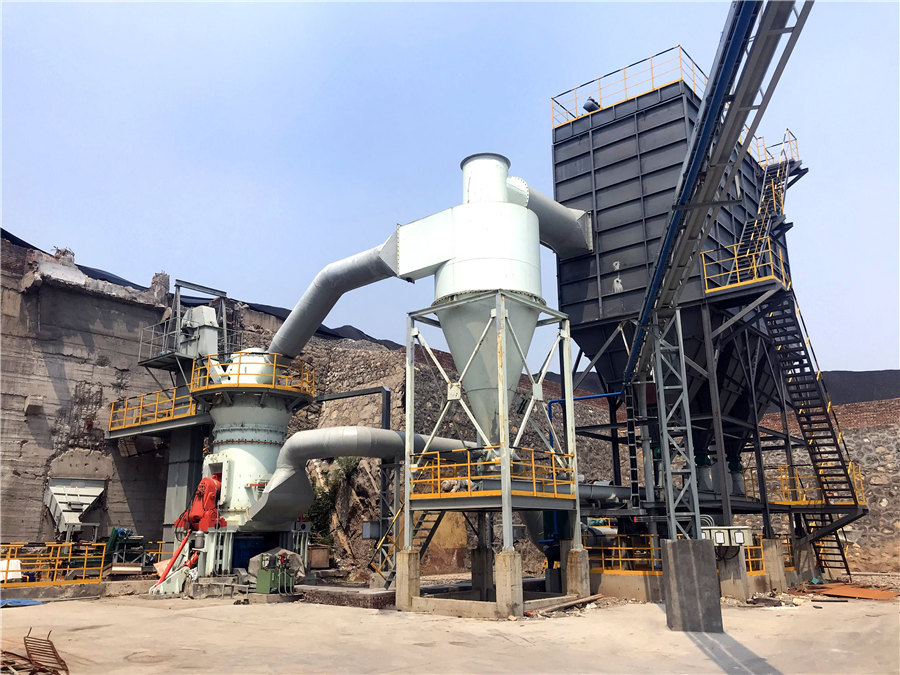
Paste Backfill Plant CMQ Engineering USA
A paste backfill plant is an important piece of industrial equipment that is generally used to help construct ground supports in underground cutandfill mining The mine tailing is one of the waste products of mining, which is mixed 2020年5月14日 The concentration of lowgrade iron ores is vital to the continued availability of iron and steel in our everyday lives (Eisele and Kawatra, 2003;Kawatra and Claremboux, 2021a;Zhang et al, 2021)THE GROWING IMPORTANCE OF PELLETIZING FOR 2023年4月26日 Mining is the foundation of modern industrial development In the context of the “carbon peaking and carbon neutrality” era, countries have put forward the development strategy of “adhering to the harmonious coexistence of humans and nature” The ongoing progress and improvement of filling mining technology have provided significant advantages, such as “green Progress and prospects of mining with backfill in metal mines in 2019年11月28日 The new product is expected to produce cost efficient, high quality paste backfill at a lower unit cost than with modified concrete plants and larger, older model paste backfill plants The modular paste plant features a combined paste mixer and hopper with a reduced plant size and lower cleaning and maintenance requirementsBACKFILL: Outotec introduces modular paste backfill plant
.jpg)
Planning an Iron Ore Mine: From Exploration Data to Informed Mining
PDF On Jan 1, 2013, Jim Everett published Planning an Iron Ore Mine: From Exploration Data to Informed Mining Decisions Find, read and cite all the research you need on ResearchGate2024年8月15日 4 Screening equipment Screening equipment is used in a mineral processing plant to classify ore particles at different processing stages, ensuring that the size of the ore being handled is suitable for each stage, which improves processing efficiency and product qualityMineral Processing Plants: What You Need to KnowDasen provides gold ore CIP CIL processing plant and also equipment manufacturing solution with benefits of ultra low power consumption, Zinc Powder Replacement Plant; Gold Amalgamation Dressing Plant; Copper Ore Processing Xi’an Dasen Mining Machinery Equipment Co, LTD Tel: +86 29 8113 7393 Whatsapp: Gold CIP/CIL Processing Plant Solution Dasen MiningRequest PDF On Nov 1, 2021, M N Bagde published Ore and Backfill Dilution in Underground Hard Rock Mining Find, read and cite all the research you need on ResearchGateOre and Backfill Dilution in Underground Hard Rock Mining
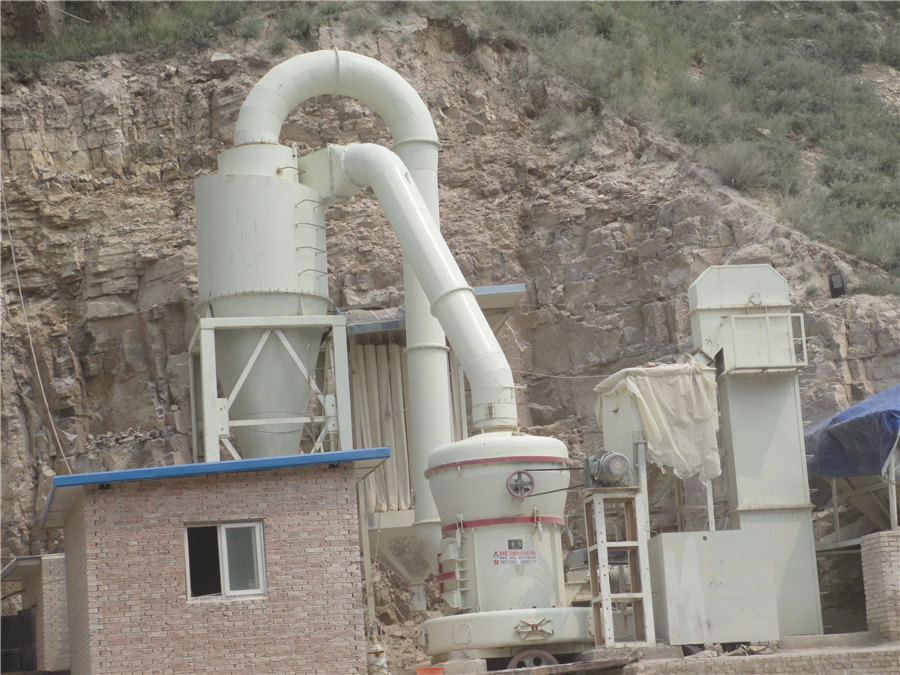
Utilization of mill tailings, fly ash and slag as mine paste backfill
2021年11月22日 In mining, the development of the ore deposits generates waste rock The first paste backfill plant in Brazil came in 1998 and later followed in Turkey, Tanzania, Argentina, and Peru in the 2000 s India witnessed its first paste fill plant in 2015 in Limestone powder usage also improves the strength and stability of paste 2019年6月11日 The remaining 2% of domestic iron ore was produced for nonsteel end uses Seven openpit iron ore mines (each with associated concentration and pelletizing plants), and three iron metallic plants—one direct Sintering: A Step Between Mining Iron Ore and 2024年1月1日 Ore mining is the engineering discipline of using relevant technologies, equipment, and mining methods according to the conditions of mineral resources, ie, whether they are on the surface, underground, or underwater, to obtain useful minerals The mining industry is a major raw material mining industryOre Mining, An Introduction on SpringerLinkThe company’s processes involve mining, transporting ore and waste to the surface, milling ore into powder, and backfilling minedout cavities with tailings from milling operations The circular dependency between mining and backfilling operations, along with variability for each task, makes it difficult to develop a realistic shortterm schedules and efficiently deploy equipment and Simulating Backfill Operations for Underground Mining
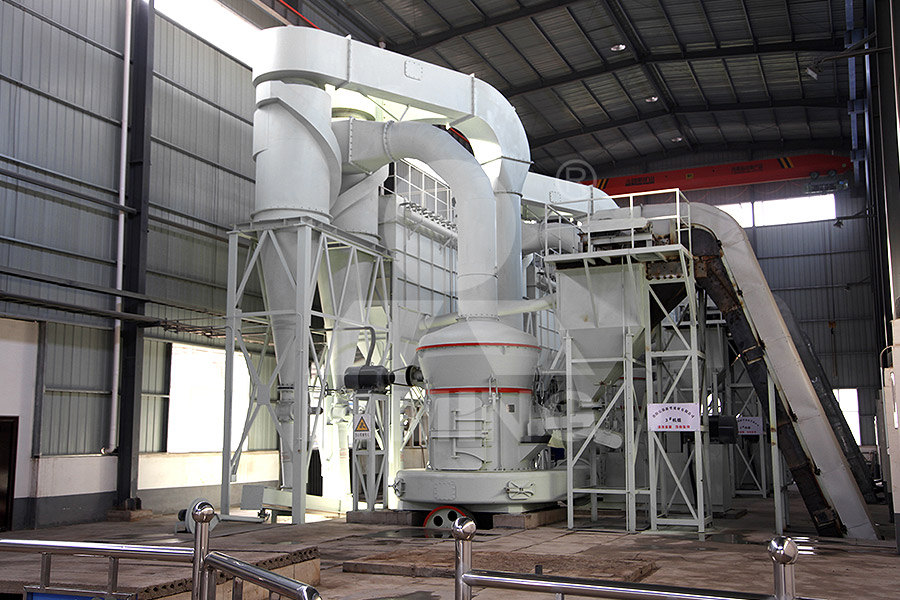
Ivanhoe Mines: KamoaKakula Phase 1 Junior Mining Network
First copper concentrates shipped to nearby Lualaba Copper Smelter; Mining crews deliver 406,000 tonnes of ore grading 577% copper in May, including 103,000 tonnes grading 858% copper from the 2022年3月1日 The general copper flotation plant flowsheet is as below: ORE MINING —CRUSHING —MILLING — CHEMICALS MIX WITH SLURRY —FROTH FLOTATION —COLLECT CONCENTRATE —THICKENING —FILTER PRESS —DRY ORE POWDER Previously Project Show Main Machinery Introduce Jaw crusher Feature: COPPER FLOTATION PLANT Pineer Mining Machinery2020年1月1日 The use of backfill in underground mining is increased due to a need for systematic backfilling the mine openings and workings Backfilling is applied in order to prevent fires and explosions Paste backfill materials for underground mining: Some experiences 2020年7月2日 Hybrid method of ground control with caving and backfill: mthickness of ore body; h r height of caving zone (arch); B ck and B cp width of ore pillar at the roof and floor, respectively; В (PDF) Ground control with backfill and caving in deeplevel mining
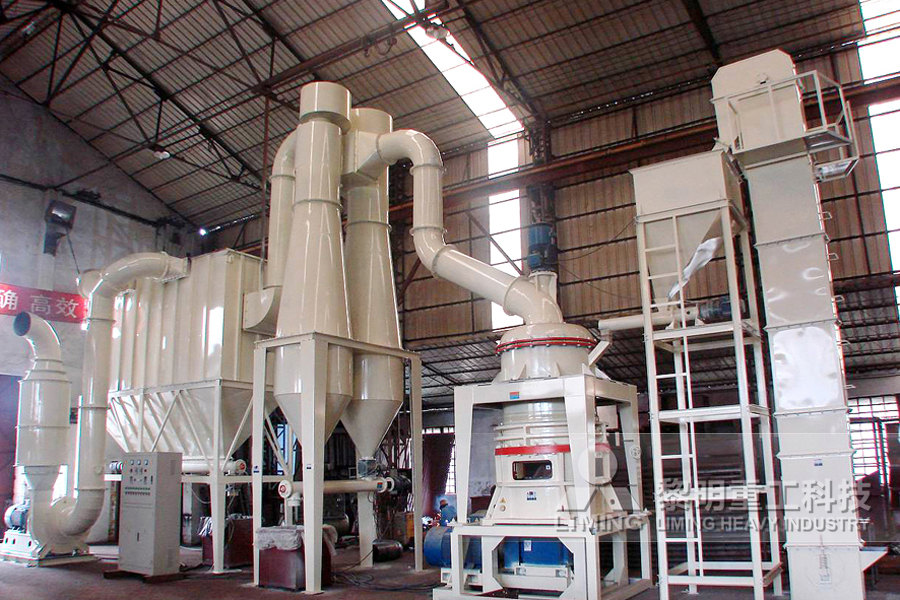
Outotec provides modular paste backfill solution International Mining
2019年11月28日 “With a dedicated paste backfill plant, costeffective plant solution for underground nonferrous mining applications with lowrange backfill throughput requirements The wet tailings solution uses 80 m2 of vacuum disc filtration and is geared towards mines with an ore production capacity of between 700,000 t/y and 1 Mt/y2023年9月4日 It is an 80100 tph iron ore processing plant The complete plant consists of the below machines: vibrating feeder, jaw crusher, belt conveyor, cone crusher, double roller crusher, vibrating screen, dry magnetic separators, and ball mill Raw ore information as below: Iron rock ore, magnetite Fe3 O4Iron Ore Beneficiation Plant Equipment For Mining ProcessPDF On Jan 1, 2019, Milena Kostović published Paste backfill materials for underground mining: Some experiences in Serbia: Part I Find, read and cite all the research you need on ResearchGatePaste backfill materials for underground mining: Some experiences mines in Montana, Stillwater Mining Company, owns and operates underground mines for PGM ore and a Concentrator plant The process involves mining, transporting the muck (ore and waste) to the surface, milling ore into powder and backfilling the mined out cavities in the underground with tailings from milling operationSIMULATING BACKFILL OPERATIONS FOR UNDERGROUND MINING
.jpg)
Lithium Ore Flotation Plant Pineer Mining Machinery
We Pineer has experience with complete flowsheet development to recover highgrade lithium concentrate powder from hard rock lithium minerals Experienced mining and mineral processing engineers make sure the technology right We mines in Montana, Stillwater Mining Company, owns and operates underground mines for PGM ore and a Concentrator plant The process involves mining, transporting the muck (ore and waste) to the surface, milling ore into powder and backfilling the mined out cavities in the underground with tailings from milling operationSIMULATING BACKFILL OPERATIONS FOR UNDERGROUND MININGKeywords: Ore dilution, backfill, hard rock mining, stoping, measurement, control measures DOI: 101134/S60120 INTRODUCTION Mining is considered as one of the industry among others towards achieving healthy economy of the any developed as well as developing country It is the mainly mining industry which supports theOre and Backfill Dilution in Underground Hard Rock Mining2015年5月13日 Underground mine backfilling is a form of ground improvement that has to be carried out in the mine sites The backfilling provides ground support and regional stability, thus facilitating ore removal from nearby regions The large underground voids created by the ore removal are backfilled with the waste tailings in the form of paste fills, hydraulic fills, and Underground Mine Backfilling in Australia Using Paste Fills and
.jpg)
Iron Mining Process
The cylinders cause the powder to roll into marblesized balls (This is like rolling wet, sticky snow into balls to make a snowman) The balls are then dried and heated until they are white hot The balls become hard as they cool The finished product is taconite pellets Steel The taconite pellets are loaded into ore ships2022年3月15日 Abstract The ore dilution is generally defined as the degradation of economical and valuable ore with the addition of the unwanted host rock, failed backfilled material and or ore material considered below the cutoff the grade The importance of ore dilution on the profitability of a mining operation is very well known and also well documented, since, it adds to the cost Ore and Backfill Dilution in Underground Hard Rock MiningThe company’s processes involve mining, transporting ore and waste to the surface, milling ore into powder, and backfilling minedout cavities with tailings from milling operations The circular dependency between mining and backfilling operations, along with variability for each task, makes it difficult to develop a realistic shortterm schedules and efficiently deploy equipment and Simulating Backfill Operations for Underground Mining2007年5月1日 The mining industry worldwide has typically not conducted the development of mines with the overall design objective of a safe, environmentally sound and aesthetically satisfactory post (PDF) Underground Mining with Backfills ResearchGate
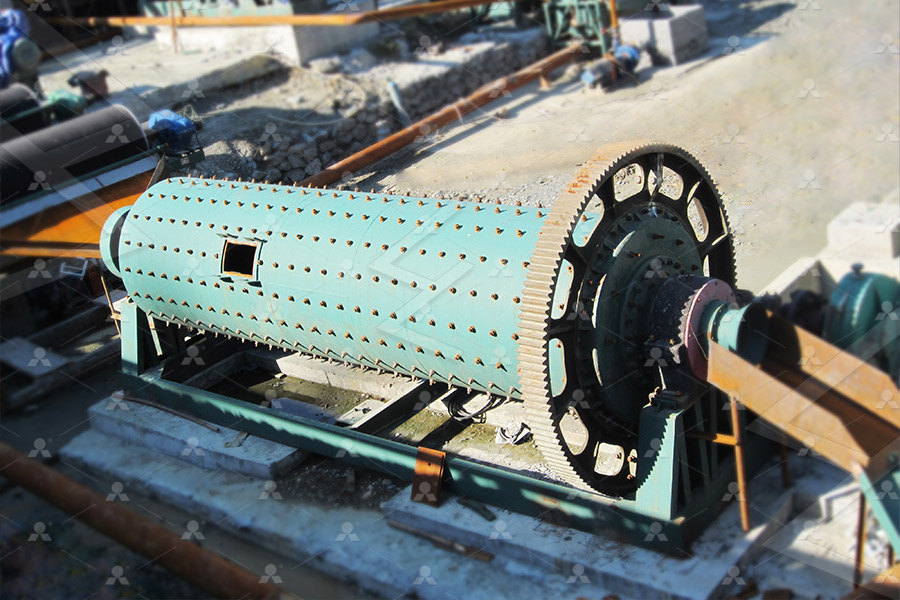
Simulating Backfill Operations for Underground Mining
2022年4月7日 The company’s processes involve mining, transporting ore and waste to the surface, milling ore into powder, and backfilling minedout cavities with tailings from milling operations The circular dependency between mining and backfilling operations, along with variability for each task, makes it difficult to develop a realistic shortterm schedules and