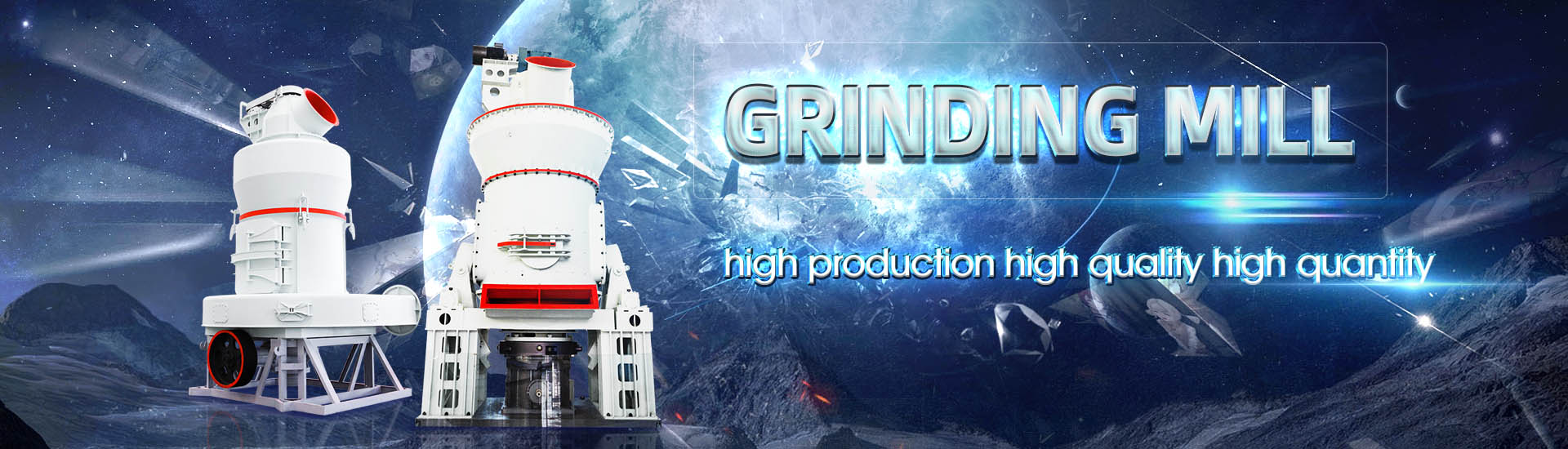
Working and studying process flow chart in cement plant
.jpg)
The Cement Plant Operations Handbook International
2 天之前 The Cement Plant Operations Handbook is a concise, practical guide to cement manufacturing and is the standard reference used by plant operations personnel worldwide 2024年7月29日 According to [39], Figure 4 provides a process flow diagram of the general cement production process and the associated inputs, during various steps of the production process consumptionProcess flow diagram for the cement Download scientific diagram Cement Manufacturing Process Flowsheet (Flow Chart) from publication: Cement Manufacturing – Process Modeling and TechnoEconomic Assessment (TEA) usingCement Manufacturing Process Flowsheet (Flow 2019年10月23日 Cement Plant: The Manufacturing Process worldcementassociation 1 Limestone (CaCO3) is taken from a quarry 2 4 3 The limestone is fed into a crusher and then Cement Plant: The Manufacturing Process 4 5 World
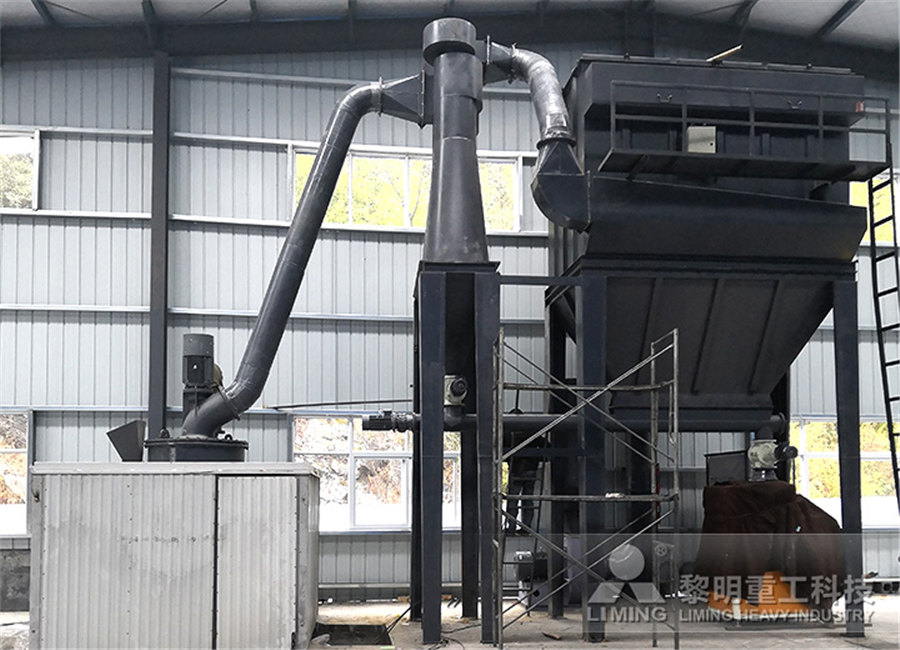
Process Flow Diagram of the Cement Plant
Figure 1 shows the detailed process flow diagram of the cement plant The consistency of the measured data is proved much better, and the balance shows clearly where the heat is consumed2018年8月28日 CEMENT MANUFACTURING PROCESS FLOW CHART After explaining the complete process of cement making, flow chart would be like that flow chart present the summary of whole process as shown belowCement Manufacturing Process The 2019年8月26日 To design the Refractory for the lining of different equipments in a cement plant, it is necessary to understand the total operational process of a cement plant in depth It is Chapter 4 Cement Manufacturing and Process Control2019年7月20日 The whole process of cement manufacturing in Messebo Cement plant which consists of two separate Cement Production lines can be summarized into the following CEMENT PRODUCTION AND QUALITY CONTROL A
.jpg)
The Cement Manufacturing Process Thermo
2023年12月20日 The Cement Manufacturing Process flow chart sums up where in the process each type of technology is making a difference Cement operators also use these analysis systems to analyze and adjust the coal mix instream, Fully revised and updated with improved content, the new Sixth Edition of the Cement Plant Operations Handbook is now available Covering some 300 pages, the cement industry’s favourite technical reference book offers indepth The Cement Plant Operations Handbook 6th 2017年5月25日 Before we understand the working or operation of a concrete batch plantIt is important to understand the basic components and structure of a batching plantWe have mobile concrete plants installations in Philippines’s Concrete Batch Plant Work Components2020年10月6日 SAXUM scope of work: Complete basic and detailed mechanical and structural engineering, drawing sign off and stamping, for the new Process ByPass Duct, to be installed in the St Mary’s Cement plant as part of the plant upgrade project Votorantim North America St Mary´s CementPROCESS ENGINEERING FOR THE CEMENT LIME
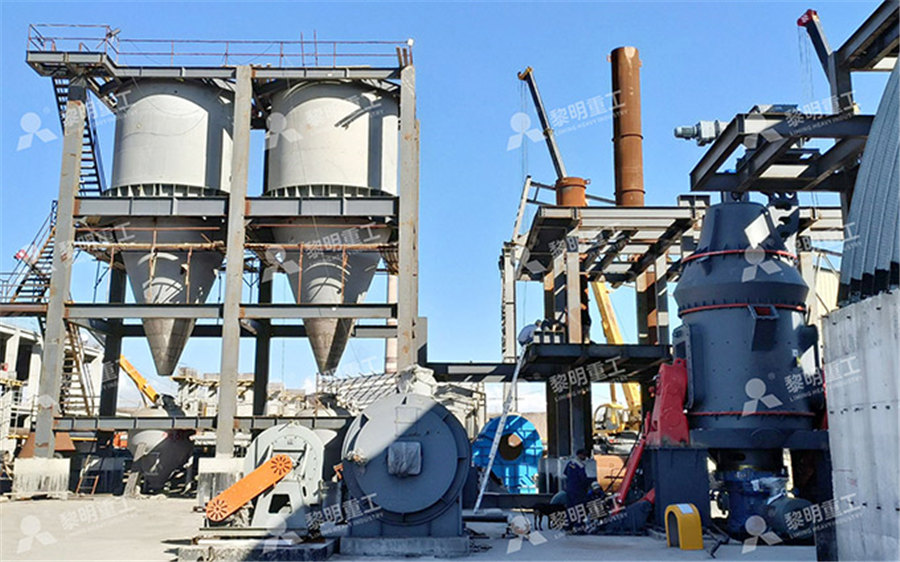
Cement Plant: The Manufacturing Process 4 5 World
2019年10月23日 Cement Plant: The Manufacturing Process worldcementassociation 1 Limestone (CaCO3) is taken from a quarry 2 4 3 The limestone is fed into a crusher and then stored until needed The clinker is mixed with additives, such as gypsum, and then ground in a cement mill, which creates cement The cement is then packed and distributed to consumersChoose an optimal location for the cement plant Design the layout of the cement factory Acquire the necessary equipment Construct the factory and install the equipment Recruit and train staff to operate the plant What is the process for making concrete? The concrete manufacturing process includes: Batching, where all required ingredients StepbyStep Guide to the Manufacturing of CementThis reduces the capital costs of a new cement plant A dry process kiln might be only 70m long and 6m wide but produce a similar quantity of clinker (usually measured in tonnes per day) as a wet process kiln of the same diameter but 200m in length For the same output, a dry process kiln without a precalciner would be shorter than a wet The cement kiln Understanding Cement2024年5月14日 1 READY MEXED CONCRETE PROCESS RMC Ready mixed concrete process (RMC) is the fresh concrete mix, which is produced by weighbatching ready mix concrete manufacturing plant under complete quality control and delivered duly mixed to the site of placement by truckmounted agitators or dumpersREADY MIXED CONCRETE PROCESS TYPES, PLANT, ADVANTAGES, RMC
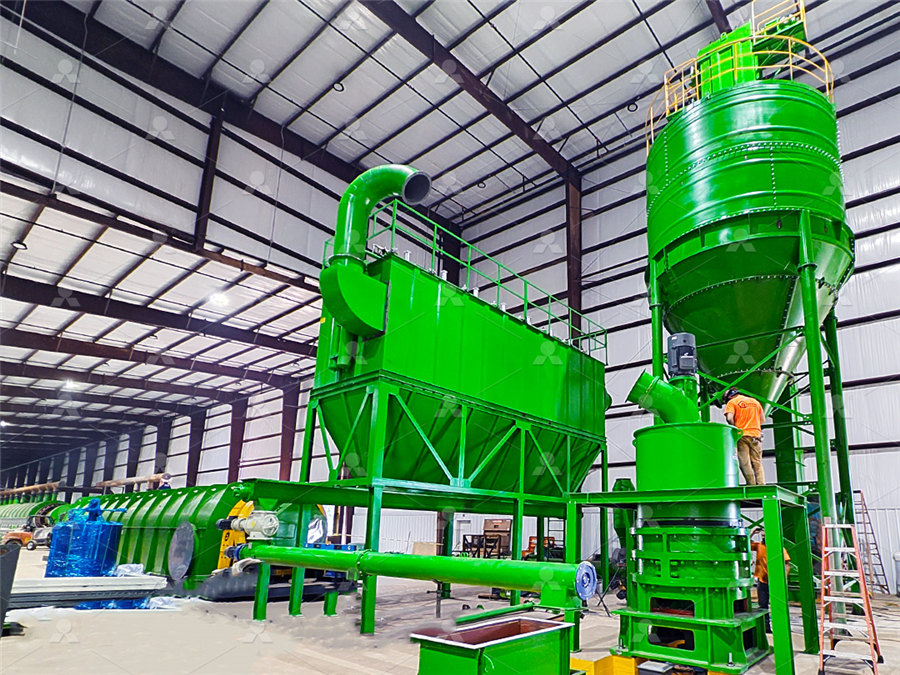
Cement Manufacturing Process and Its Environmental Impact
2023年7月10日 Cement manufacturing is a significant industrial activity that plays a vital role in the construction sector However, the process of cement production is associated with various environmental Cement manufacturing: components of a cement plant This page and the linked pages below summarize the cement manufacturing process from the perspective of the individual components of a cement plant the kiln, the cement mill etc For information on materials, including reactions in the kiln, see the ' Clinker ' pagesCement manufacturing components of a cement plant Understanding CementDownload scientific diagram The Flowchart of stationary batching plant from publication: Quality Management to continuous improvements in process of Ready Mix Concrete production The key The Flowchart of stationary batching plant ResearchGate2024年7月29日 According to [39], Figure 4 provides a process flow diagram of the general cement production process and the associated inputs, during various steps of the production process consumption of Process flow diagram for the cement manufacturing process,
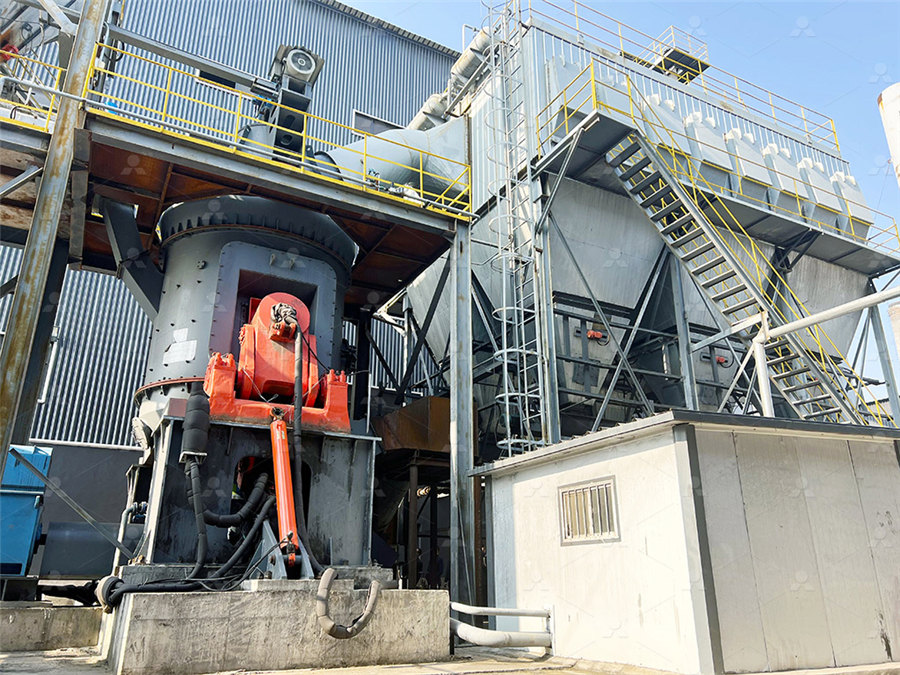
Cement Production Process PPT SlideShare
2015年9月17日 6 00 Limestone Quarry and Crushing plant The major raw material for cement production is limestone The limestone most suitable for cement production must have some ingredients in specified quantities ie, 1 天前 In summary, the control system in a batching plant significantly enhances the precision, consistency, and efficiency of concrete production Its ability to automate operations, monitor in realtime, prevent errors, and adapt to variations contributes to the production of highquality concrete for construction projectsUnderstanding the Working Flow of Concrete Batching Plants2022年6月25日 1 Introduction Cement industry is one of the most energy intensive in industrial sector around the World In fact, the energy consumption in cement plant represents about 40% to 60% of cement production cost [1]Cement production is ranked second after the steel industry regarding energy consumption [2]Typically, 75% of the total consumed energy in cement Development of a new technique of waste heat recovery in cement plants 2021年3月24日 Cement manufacturing requires cooling down of hot clinker at temperature of about 1350o C to temperature lower than 100 o C in a cooling system known as clinker coolerModelling of clinker cooler and evaluation of its
.jpg)
CONTINUOUS PROCESS IMPROVEMENT IN READY MIX
2023年2月7日 improve the quality of the concrete produced the system in the RMC plants should be standardized The quality control should be ensured in the production process through the continuous process improvement Such process improvement can be achieved using the statistical process control (SPC) toolsDownload scientific diagram Process flow chart of cement plant from publication: Design and Implementation of Reduced Fuel Consumption in Cement Kiln with Efficient Cooling Technology Using PLC Process flow chart of cement plant Download Scientific 2019年7月15日 The key benefits from Ready Mix Concrete (RMC) are good quality, lower Life cycle cost, the speed of work and friendliness of environment more than the site mixed concrete, but when the quality of Quality Management to continuous improvements in process 2023年12月20日 The Cement Manufacturing Process flow chart sums up where in the process each type of technology is making a difference Cement operators also use these analysis systems to analyze and adjust the coal mix instream, which enables the plant to reduce energy consumption by using exactly the amount of coal fuel required to meet the specific The Cement Manufacturing Process Thermo Fisher Scientific
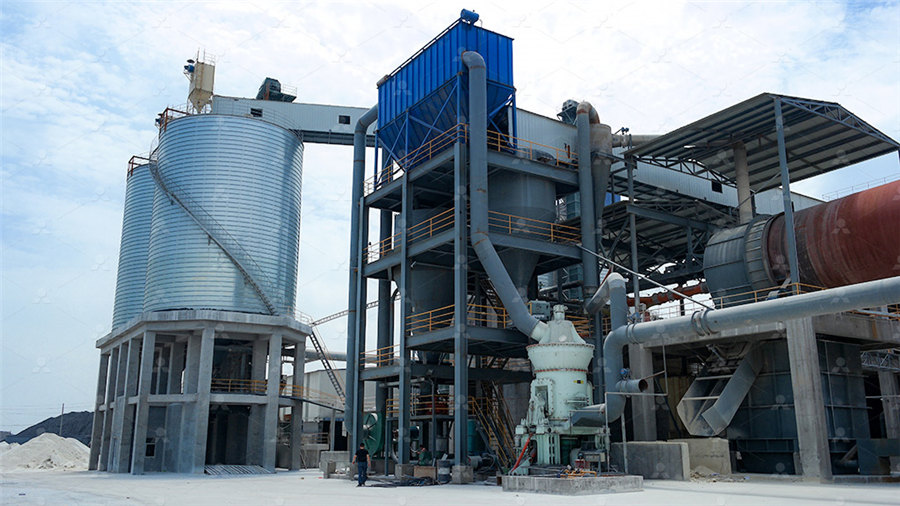
Cement manufacturing process PPT Free Download
2014年6月10日 Evolution of the cement Process • Wet process easiest to control chemistry better for moist raw materials • Wet process high fuel requirements fuel needed to evaporate 30+% slurry water • Dry process kilns less fuel requirements • Preheater/Precalciner further enhance fuel efficiency allow for high production rates2012年6月1日 As the cylinder starts to rotate, the grinding balls inside the cylinder crush and grind the feed material, generating mechanical energy that aids in breaking bonds, activating the catalyst, and (PDF) Grinding in Ball Mills: Modeling and Process ControlThe aim of this work was to evaluate the effect of different inorganic compounds as electron donors for the capture of CO2 from a model cement flue gas CO2/O2/N2 (42:135:823 % v/v) using a non Cement plant flue gas characteristicsDownload scientific diagram Concrete production process flow chart from publication: Assessment tools for the environmental evaluation of concrete, plaster and brick elements production Concrete production process flow chart
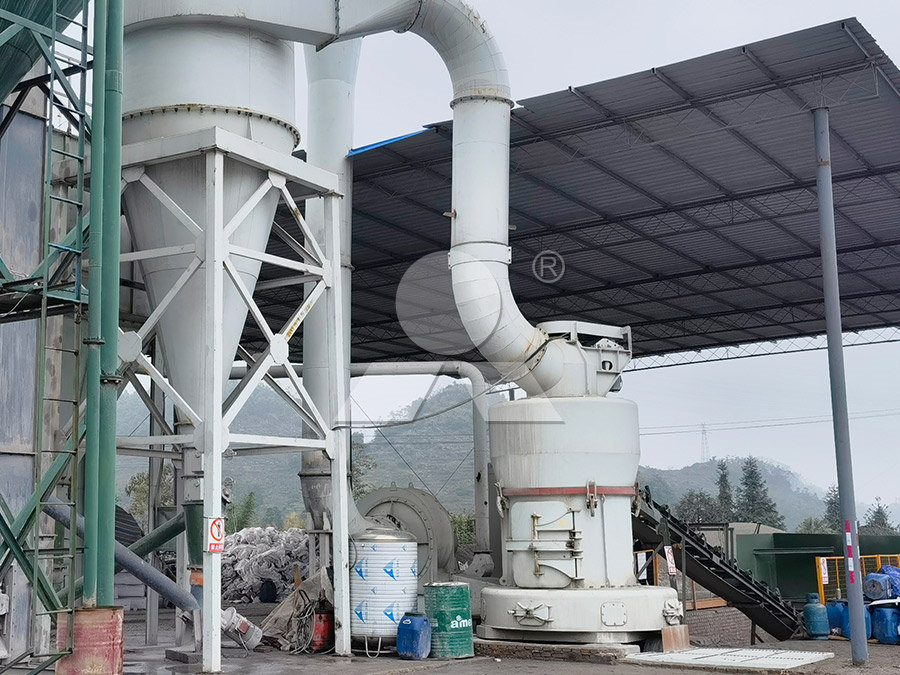
Stages in cement production flow chart [43] ResearchGate
The main impact on the energy consumption of cement production is the burning process of cement clinker in a rotary kiln, and the energy costs associated with burning cement clinker constitute 50 Download scientific diagram Cement Manufacturing Process Flowsheet (Flow Chart) from publication: Cement Manufacturing – Process Modeling and TechnoEconomic Assessment (TEA) using SuperPro Cement Manufacturing Process Flowsheet (Flow Chart)2024年1月18日 The use of fossil fuels such as coal, natural gas, and oil is common in cement production, both as a fuel for the kiln and as a source of heat for other parts of the process which leads to CO2 emitted by combustionHowever chemical reactions happening in the kiln (calcination) are also responsible for up to 60% of the total of emissions of the Cement Production Demystified: StepbyStep Process and 2023年9月5日 Process control instrumentation is a complex system of sensors, transmitters, controllers, and other devices designed to measure and control physical quantities such as temperature, pressure, flow, and level in an industrial process In the realm of cement plants, process control instrumentation is the key to achieving highquality cement and Mastering Process Control Instrumentation in Cement Plants:
.jpg)
(PDF) Dust Emission Monitoring in Cement Plant Mills: A
2021年8月28日 Additionally, the Portland cement mill technological process (its component parts), as well as the solutions regarding the reduction of the air emissions level, following the emission limit values 2019年7月20日 The whole process of cement manufacturing in Messebo Cement plant which consists of two separate Cement Production lines can be summarized into the following processes ;as can be seen in the process and Quality flow diagram below; 1 Quarrying and Crushing 2 Raw material Storage and TransportationCEMENT PRODUCTION AND QUALITY CONTROL A 2018年12月31日 Energy recovery and exergy recovery in a clinker cooler was a major factor in optimizing clinker production and cement grinding process, the running clinker cooler has an energy recovery was 4831 Energy and Exergy Analysis of Clinker Cooler in the Cement To address a decarbonized cement production process (DCPP), a calcium looping process is connected to an industrial cement production process (CPP) for capturing CO2 by 935~96%Process flow sheet of a CAP process integrated in a cement plant
.jpg)
Concrete Batch Plant Work Components
2017年5月25日 Before we understand the working or operation of a concrete batch plantIt is important to understand the basic components and structure of a batching plantWe have mobile concrete plants installations in Philippines’s 2020年10月6日 SAXUM scope of work: Complete basic and detailed mechanical and structural engineering, drawing sign off and stamping, for the new Process ByPass Duct, to be installed in the St Mary’s Cement plant as part of the plant upgrade project Votorantim North America St Mary´s CementPROCESS ENGINEERING FOR THE CEMENT LIME 2019年10月23日 Cement Plant: The Manufacturing Process worldcementassociation 1 Limestone (CaCO3) is taken from a quarry 2 4 3 The limestone is fed into a crusher and then stored until needed The clinker is mixed with additives, such as gypsum, and then ground in a cement mill, which creates cement The cement is then packed and distributed to consumersCement Plant: The Manufacturing Process 4 5 World Choose an optimal location for the cement plant Design the layout of the cement factory Acquire the necessary equipment Construct the factory and install the equipment Recruit and train staff to operate the plant What is the process for making concrete? The concrete manufacturing process includes: Batching, where all required ingredients StepbyStep Guide to the Manufacturing of Cement
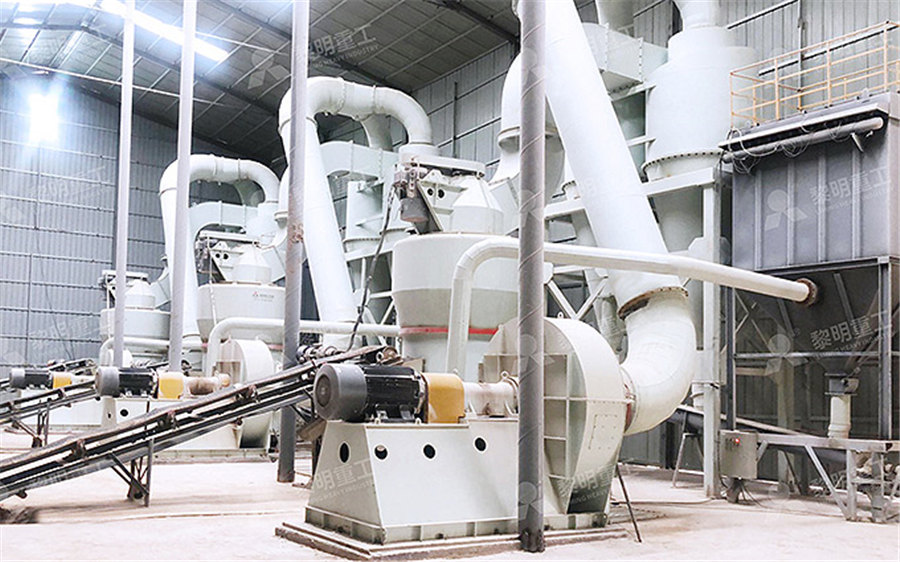
The cement kiln Understanding Cement
This reduces the capital costs of a new cement plant A dry process kiln might be only 70m long and 6m wide but produce a similar quantity of clinker (usually measured in tonnes per day) as a wet process kiln of the same diameter but 200m in length For the same output, a dry process kiln without a precalciner would be shorter than a wet 2024年5月14日 1 READY MEXED CONCRETE PROCESS RMC Ready mixed concrete process (RMC) is the fresh concrete mix, which is produced by weighbatching ready mix concrete manufacturing plant under complete quality control and delivered duly mixed to the site of placement by truckmounted agitators or dumpersREADY MIXED CONCRETE PROCESS TYPES, PLANT, ADVANTAGES, RMC 2023年7月10日 Cement manufacturing is a significant industrial activity that plays a vital role in the construction sector However, the process of cement production is associated with various environmental Cement Manufacturing Process and Its Environmental ImpactCement manufacturing: components of a cement plant This page and the linked pages below summarize the cement manufacturing process from the perspective of the individual components of a cement plant the kiln, the cement mill etc For information on materials, including reactions in the kiln, see the ' Clinker ' pagesCement manufacturing components of a cement plant Understanding Cement
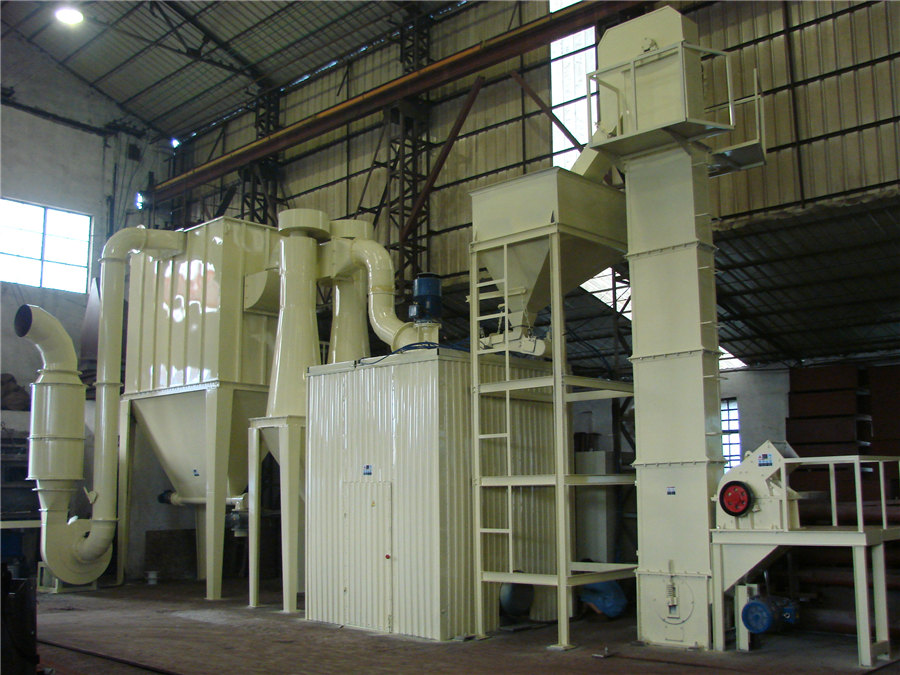
The Flowchart of stationary batching plant ResearchGate
Download scientific diagram The Flowchart of stationary batching plant from publication: Quality Management to continuous improvements in process of Ready Mix Concrete production The key 2024年7月29日 According to [39], Figure 4 provides a process flow diagram of the general cement production process and the associated inputs, during various steps of the production process consumption of Process flow diagram for the cement manufacturing process,