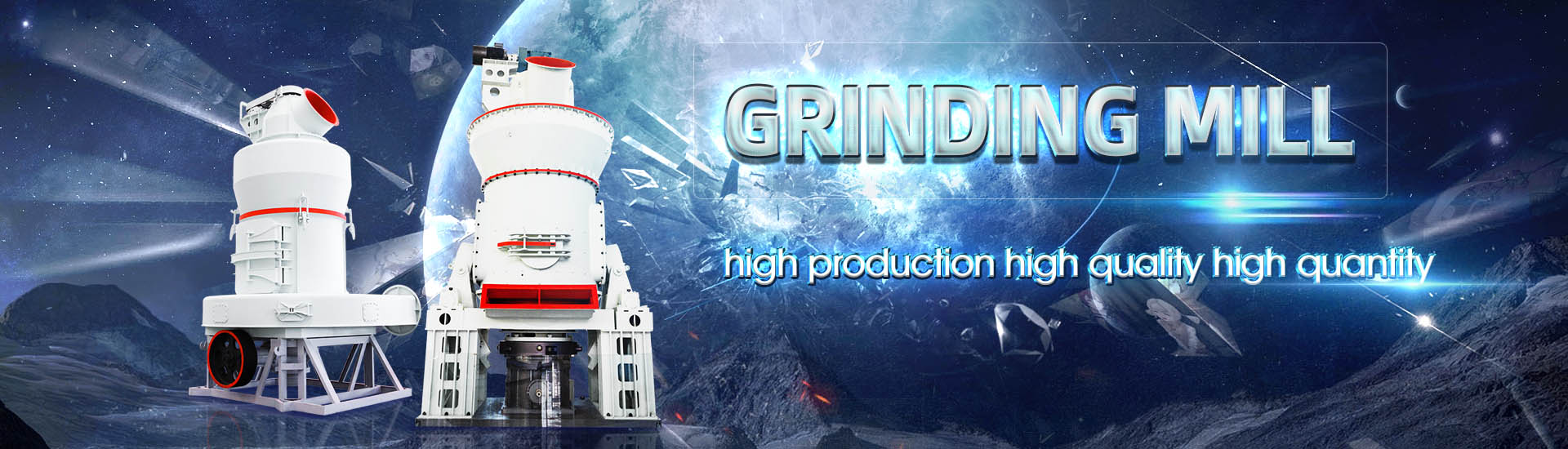
Coal mill shaft temperature is high
.jpg)
A unified thermomechanical model for coal mill operation
2015年11月1日 Coal mills are bottleneck in coal–fired power generation process due to difficulty in developing efficient controls and faults occurring inside the mills In this paper, a dynamic coal mill model is developed using conservation laws and empirical relations2013年11月20日 Coal mill is an important component of the thermal power plant It is used to grind and dry the moisturized raw coal and transport the pulverized coal – air mixture to the Modeling and Control of Coal Mill NTNUCoal Bowl Mill, for guaranteed performance at a 500 MW capacity NTPC thermal power plant The study was conducted to assess the effective performance of the pulverizers of this 500 A Study on 500 MW Coal Fired Boiler Unit’s Bowl Mill 2020年8月12日 Obtained results indicate that grinding pressure, primary air (PA) temperature and mill motor current have a tendency to rise by increasing coal feeding mass flow rates for all used coalAn investigation of performance characteristics
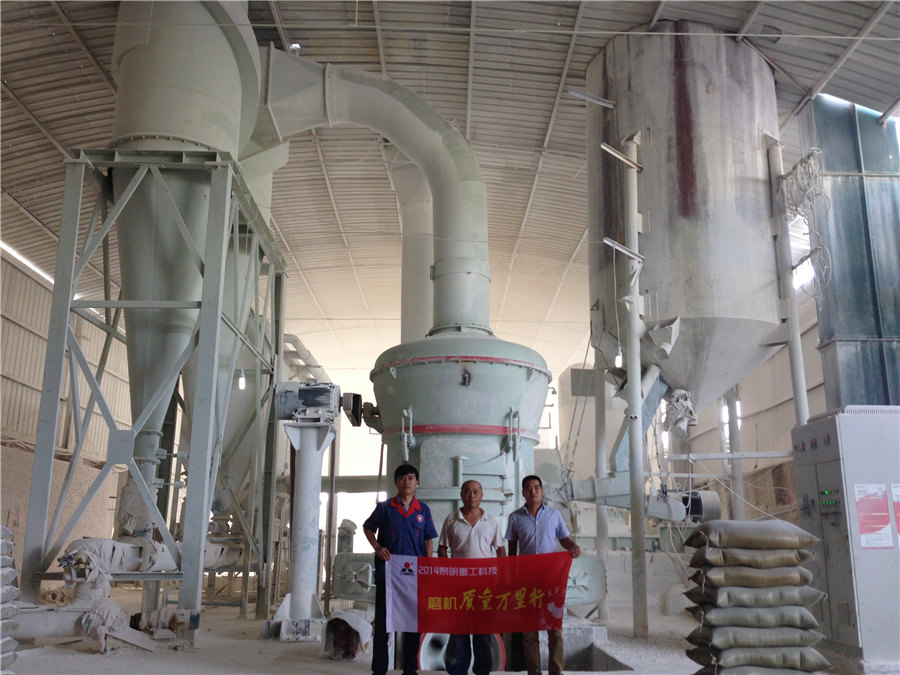
Analysis of the Coal Milling Operations to the Boiler
2021年10月28日 The results show, the highest mill in service not affected to the boiler parameters such as reheater metal temperature, main steam temperature and boiler flue gas 2020年4月2日 The results show, the highest mill in service not affected to the boiler parameters such as reheater metal temperature, main steam temperature and boiler flue gas outlet and others boilerAnalysis of the Coal Milling Operations to the 2012年5月1日 The paper presents development and validation of a coal mill model to be used for improved mill control, which may lead to a better load following capability of power plants Derivation and validation of a coal mill model for control2023年7月18日 We propose an outlet temperature control strategy for coal mills, grounded in the MPC framework, utilizing the ARX for temperature prediction Its lower computational MultiObjective Optimization of Coal Mill Outlet
.jpg)
An investigation of performance characteristics and
2020年8月12日 To understand the performance of a vertical roller coal mill, the real operational tests have been performed considering three different coal sources Obtained results indicate 2021年8月1日 Results show that the mean absolute error of mill differential pressure, mill electric current and outlet primary air temperature are 308%, 305% and 005% on validation Coal mill model considering heat transfer effect on mass 2016年9月30日 fine coal for accelerating the combustion process by exposing large surface area to the action of oxygen The vertical shaft is used in the bowl mill, which is one type of pulverizing mill The diagram of vertical shaft is shown in Figure 2 Figure 2 Coal mill vertical shaft The failure of shaft in the assembly is shown in the Figure 3 It isRoot Cause Failure Analysis of Coal Mill Vertical ShaftSection of coal bowl mill Table 1 Guaranteed coal conditions for mill performance evaluation Coal Moisture % 20 Coal HGI 55 Mill Outlet Temperarure °C 80 Mill Air Flow T/hr 102 Coal Fineness (% passing trough 200 mesh) 70% passing through 200 mesh and 90% passing through 50 mesh Differental Pressure 300 mmwc Coal Output from Mill 609 t/hrA Study on 500 MW Coal Fired Boiler Unit’s Bowl Mill
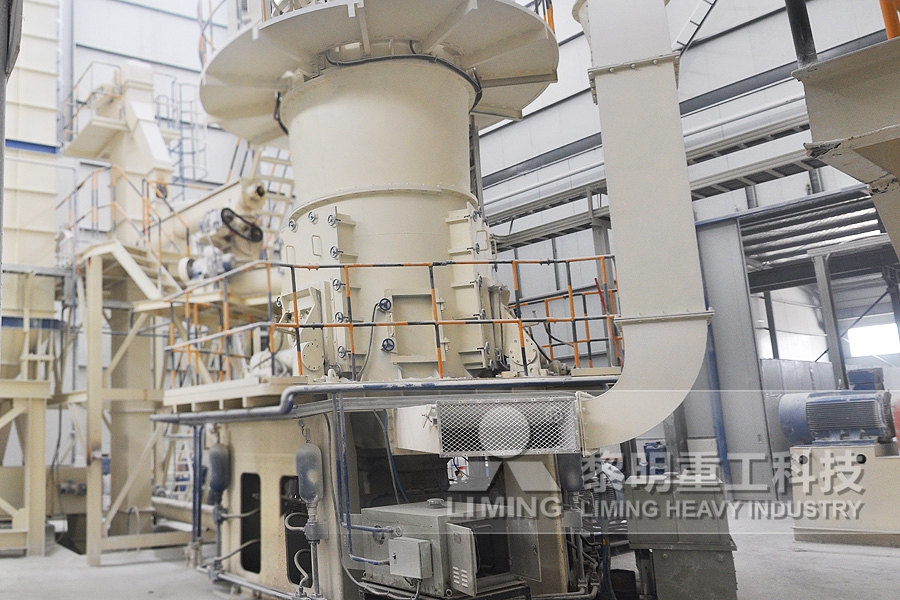
Root cause failure analysis of coal mill vertical shaft
2010年6月22日 The failure analysis results of coal mill vertical shaft used in thermal power plant as carried out in a case study, will be available to the designer and manufacturer, besides the users and the 2015年8月1日 This paper is organized as follows: Section 2 provides an understanding of the mill system together with the control issues and major faults influencing the mill performance Section 3 deals with the review of different control strategies applied to the milling system Control using estimated mill states and advanced control schemes developed for mills such as Review of control and fault diagnosis methods applied to coal millsAs it is observed from Figure 1 1, energetic efficiency decreases when both mill outlet temperature and coal feeding mass flow rate increase In both cases, the heat transfer from the surface of The layout of the coal mill with a rotary classifier2021年10月28日 From the coal yard, the coal is transfer to the mill bunkers through conveyor belt The bunkers are sized for an effective capacity of twelve (12) hours at BMCR with design coal Each mill bunker has one hopper, connected to the feeders Mills operate when the bunker coal gate valves are opened, coal is allowed to flow to the gravimetric feedersAnalysis of the Coal Milling Operations to the Boiler
.jpg)
Root Cause Failure Analysis of Coal Mill Vertical Shaft
section of the shaft under consideration is exposed to high temperature This high temperature will locally alter the material properties of the shaft [2] Duration/history of starting and longer service life and more convenient maintenance Hp1103 coal mill is a kind of HP coal mill Compared with similar coal mills, it has stronger adaptability to raw coal and is more suitable for large unit thermal power plants Taking hp1103 medium speed roller disc coal mill as the carrier, this paper mainly describes theSHPHGLXPVSHHGFRDOPLOO IOPscience2013年11月20日 (2) The temperature of the mill is assumed to be same as the temperature of the classifier (3) Heat emitted from the mill to its environment is negligible (4) The mass change of coal causes insignificant change in the total heat capacity of the mill (5) The ambient temperature (temperature of raw coal entering the mill) , coal moisture and Modeling and Control of Coal Mill NTNU2018年6月7日 – Lower rank coals are generally more easily ignited inside the coal mill – High volatile matter and highly reactive coals encourage preignition inside the mill – Higher moisture content requires temperature extremes inside the mill – High moisture, high volatile matter and highly reactive coals are prone to self heating and canMill Inerting and Pulverizer/Mill Explosion Mitigation

(PDF) Steady state inferential modeling of
Powder Technology 192 (2009) 260–267 Contents lists available at ScienceDirect Powder Technology j o u r n a l h o m e p a g e : w w w e l s ev i e r c o m / l o c a t e / p ow t e c Steady state inferential modeling of temperature and 2021年1月1日 Coal is ground in Coal mill, which is a fuel for use in Kiln firing: 5: High temperature Clinker is cooled to 200 degrees: 7: Clinker Storage: Peter Silo: Storage of Hot clinker and natural cooling: 8: Cement Grinding: Vertical Roller Mills (VRM), High Pressure Grinding Rolls (HPGR), Vertical Shaft Impact Crushers (VSI) Review on vertical roller mill in cement industry its Failure surface of a pulverizer mill shaft showing fatigue beach marks Fig 3 Failure surface of a pulverizer mill shaft, which has been subjected to rubbing during operation 3 Analytical procedure adopted In order to understand the genesis of failure of the coal pulverizer mill shafts, the following tests/ examinations were conducted: 1Failure analysis of coal pulverizer mill shaft Academia2016年9月7日 if any running Coal Mill pipe temperature goes low, below 60 C it will flash an alarm called “Any coal mill pipe temperature low” Thus we were able to execute the project and established automation for remote monitoring and measurement of coal pipe temperature of coal mill of PF boiler Fig 4Measurement and Control of Coal Pipe Temperature of
.jpg)
Techflow
2023年12月23日 The coal mill fan is usually installed on the top of the coal mill, and its inlet is connected to the coal mill discharge port, and its outlet is connected to the furnace The coal mill fan is driven by a motor, and the motor drives the fan impeller to rotate, which generates centrifugal force to suck in air from the inlet and blow it out from 2016年8月1日 It can be seen that the outlet temperature of mill A is around 75 When the load was decreased from 750 MW to 670 MW, mill A was placed out of service to ensure high operating efficiency, and the coalfeeding rates of the mills remaining in service were slightly increased At relatively low loads, mills B and F were supplied with 43 A powersaving control strategy for reducing the total MILL FIRE The usual causes of pulveriser fires are: i)Excessive Mill Outlet temperatures ii)Foreign material such as paper, bags, belt etc iii)Excessive accumulation of pyrites or coal at the mill bottom or air inlet to the mill iv)Improper or unusual operation INDICATIONS: The two most common indications of a fire in a milling system are: a Coal Mills In Thermal Power Plant [ylyxo7868qnm]2016年9月7日 if any running Coal Mill pipe temperature goes low, below 60 C it will flash an alarm called “Any coal mill pipe temperature low” Thus we were able to execute the project and established automation for remote monitoring and measurement of coal pipe temperature of coal mill of PF boiler Fig 4Measurement and Control of Coal Pipe Temperature of
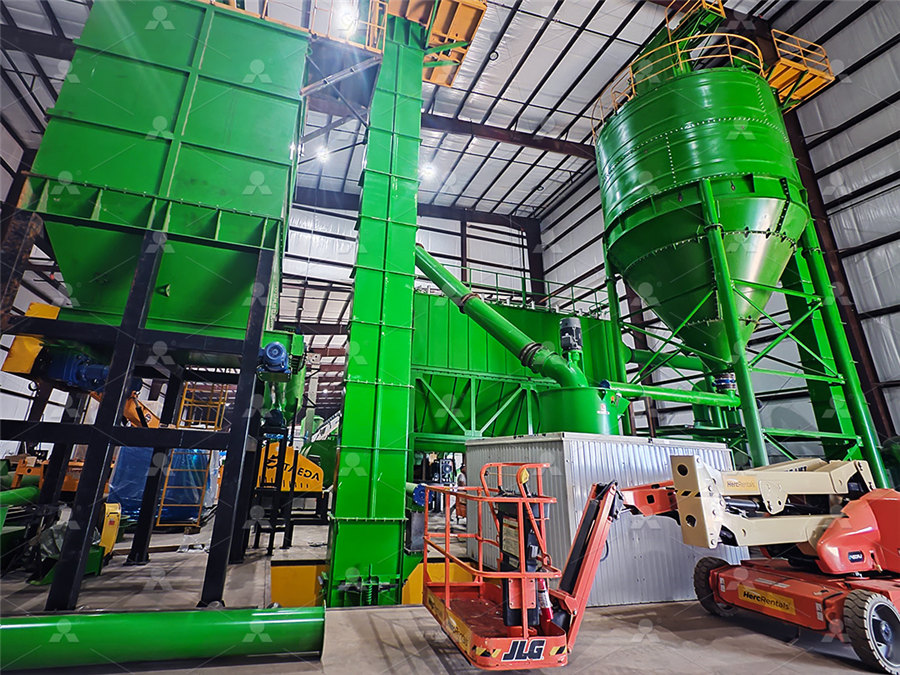
Failure analysis of coal pulverizer mill shaft Request PDF
2003年12月1日 Failure of a ball and race type coal pulverizer mill shaft has been analysed It was found that the shaft, made of EN 25 steel, failed by fatigue2024年8月22日 with increasing mill size As described earlier, it is a highspeed mill that pulverizes coal by the combination of crushing, attrition and impact The BTM System should be equipped with a crusher/ dryer for high moisture coals, or coals with a top size greater than 3/4 inches The primary crushing and drying is performed in the crusher/ dryerA Comparison of Three Types of Coal Pulverizers2023年7月18日 Multiobjective Optimization of Coal Mill Outlet Temperature Control Using MPC Zengji Zhang1, Yicheng Zhang2, Wei Shen2, BOE Xukang Lyu3,∗ 1Sinoma International Engineering Co, Ltd, Nanjing, Jiangsu, China 2College of Computer Science and Technology, Zhejiang SciTech University, Hangzhou, Zhejiang, China 3Zhejiang New Rise Digital MultiObjective Optimization of Coal Mill Outlet 2020年8月12日 Moreover, coal volatile matter and moisture content are improved by increasing the mill outlet temperature for each coal type Additionally, effect of enhancement of the classifier speed has been found favorable on the combustion performance indicators CMC coal shows relatively better performance since it has lower moisture content and higher An investigation of performance characteristics and
.jpg)
The Effect of Surface Finish and Fillet Design on Tie Rod
2023年11月30日 Shaft Lifetime at Coal Mill Plant Operation Alif Burhanuddin Yusuf Habibie1*, Andrian Sagisky Januartha1, Fatahul Arifin2, Bayumi Setiawan1 3mm 004mm 13mm 228 Still HighThe ball mill is a traditional coal pulverizer machine, which has been widely used since it was invented In the cement plant, the new dry process cement manufacturing requires the moisture content of coal powder to be 05% ~ 15%, while that of raw coal is 15% ~ 40%Coal Mill in Cement Plant Vertical Roller Mill AirSwept Ball MillThe coal mill grinding system is an important part of the dry process cement manufacturing In cement plants, we usually adopt the air swept coal mill system or vertical mill system as the pulverized coal preparation system, which is arranged at the cement kiln head or kiln tail to provide fuel for clinker calcination However, due to the flammable and explosive Coal Mill – Coal Mill In Cement Plant AGICO Cement As one of the three major forces of coal mills, the grinding force exerts a significant impact on the working process of coal mills and parameters like mill current and outlet temperatureTechnical specifications of vertical roller coal mill
.jpg)
The temperature of Britain's coalfields Quarterly Journal of
Following the closure of the majority of the British underground coal mines during the 1980s–1990s, the requirement to dewater ceased and many collieries were left to progressively flood ()The resulting mine water often has undesirable water chemistry and may be aggressive or acidic, with high iron and sulphate arising from oxidation of pyrite and associated precipitation 2013年12月6日 NomenclatureBowl Mills 583 XRS / 803 XRP Bowl mills 58,80 stands for bowl diameter in inches If the number is even then its shallow bowl mill If the number is odd then its deep bowl mill 3 number of rollers three nos X frequency of power supply 50 cyclesIn USA ’x’ means 60 cycles R Raymond, name of the inventorPulverizer Plant OM Aspects eecpowerindia2024年9月24日 A coal mining area is more susceptible to the danger of coal spontaneous combustion due to elevated ground temperature and high stress from deep mining To investigate the heat generation behavior and the evolution of critical groups of unloaded bulk coal under high primary temperature in a deep mine, the thermogravimetric and heat release characteristics of Thermal Generation Behavior, Key Groups and Disaster The improper hot working process of the coal mill shaft resulted in the abnormal metallographic structure of the shaft, and the existence of serious reticulated ferrite and brittle widmanstatten Mechanical Properties of Failed Axial shaft and AISI 304
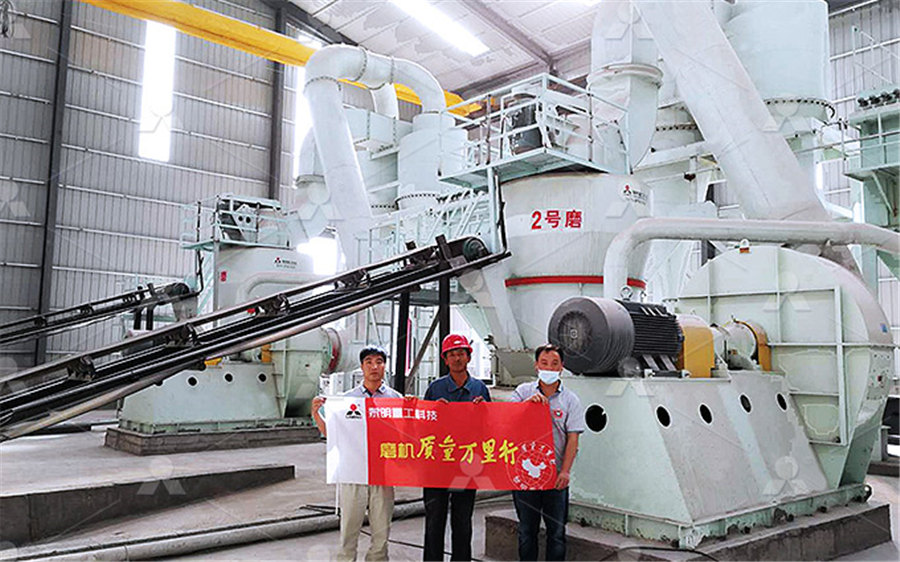
Root Cause Failure Analysis of Coal Mill Vertical Shaft
2016年9月30日 fine coal for accelerating the combustion process by exposing large surface area to the action of oxygen The vertical shaft is used in the bowl mill, which is one type of pulverizing mill The diagram of vertical shaft is shown in Figure 2 Figure 2 Coal mill vertical shaft The failure of shaft in the assembly is shown in the Figure 3 It isSection of coal bowl mill Table 1 Guaranteed coal conditions for mill performance evaluation Coal Moisture % 20 Coal HGI 55 Mill Outlet Temperarure °C 80 Mill Air Flow T/hr 102 Coal Fineness (% passing trough 200 mesh) 70% passing through 200 mesh and 90% passing through 50 mesh Differental Pressure 300 mmwc Coal Output from Mill 609 t/hrA Study on 500 MW Coal Fired Boiler Unit’s Bowl Mill 2010年6月22日 The failure analysis results of coal mill vertical shaft used in thermal power plant as carried out in a case study, will be available to the designer and manufacturer, besides the users and the Root cause failure analysis of coal mill vertical shaft2015年8月1日 This paper is organized as follows: Section 2 provides an understanding of the mill system together with the control issues and major faults influencing the mill performance Section 3 deals with the review of different control strategies applied to the milling system Control using estimated mill states and advanced control schemes developed for mills such as Review of control and fault diagnosis methods applied to coal mills
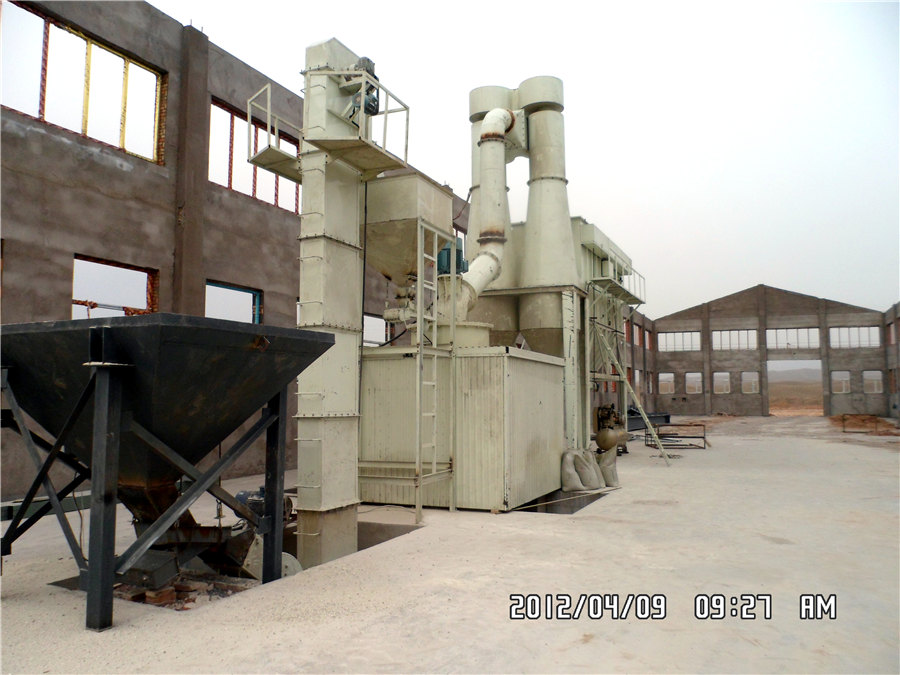
The layout of the coal mill with a rotary classifier
As it is observed from Figure 1 1, energetic efficiency decreases when both mill outlet temperature and coal feeding mass flow rate increase In both cases, the heat transfer from the surface of 2021年10月28日 From the coal yard, the coal is transfer to the mill bunkers through conveyor belt The bunkers are sized for an effective capacity of twelve (12) hours at BMCR with design coal Each mill bunker has one hopper, connected to the feeders Mills operate when the bunker coal gate valves are opened, coal is allowed to flow to the gravimetric feedersAnalysis of the Coal Milling Operations to the Boiler section of the shaft under consideration is exposed to high temperature This high temperature will locally alter the material properties of the shaft [2] Duration/history of starting and Root Cause Failure Analysis of Coal Mill Vertical Shaftlonger service life and more convenient maintenance Hp1103 coal mill is a kind of HP coal mill Compared with similar coal mills, it has stronger adaptability to raw coal and is more suitable for large unit thermal power plants Taking hp1103 medium speed roller disc coal mill as the carrier, this paper mainly describes theSHPHGLXPVSHHGFRDOPLOO IOPscience
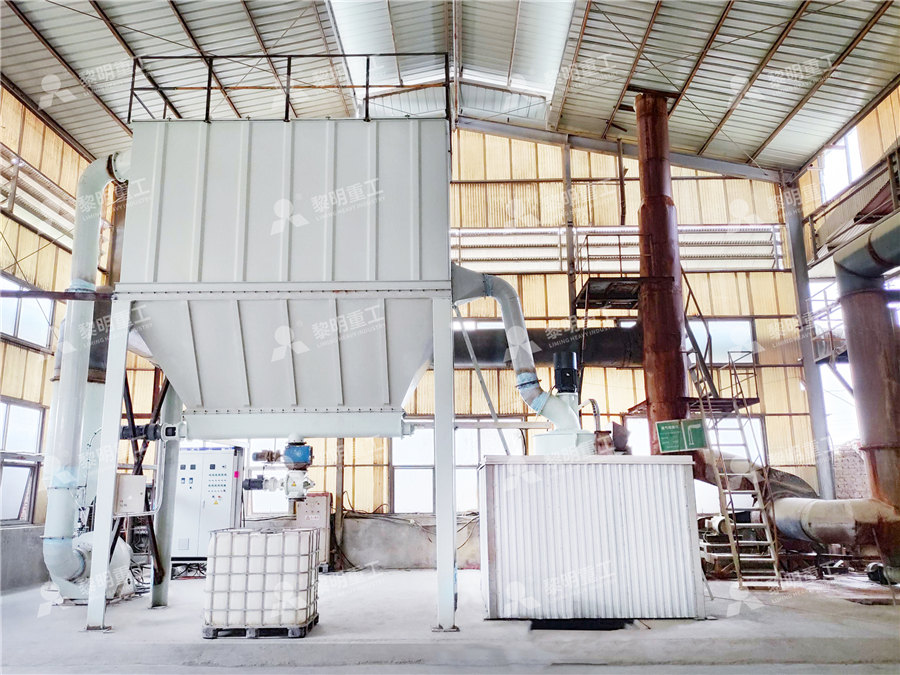
Modeling and Control of Coal Mill NTNU
2013年11月20日 (2) The temperature of the mill is assumed to be same as the temperature of the classifier (3) Heat emitted from the mill to its environment is negligible (4) The mass change of coal causes insignificant change in the total heat capacity of the mill (5) The ambient temperature (temperature of raw coal entering the mill) , coal moisture and 2018年6月7日 – Lower rank coals are generally more easily ignited inside the coal mill – High volatile matter and highly reactive coals encourage preignition inside the mill – Higher moisture content requires temperature extremes inside the mill – High moisture, high volatile matter and highly reactive coals are prone to self heating and canMill Inerting and Pulverizer/Mill Explosion Mitigation