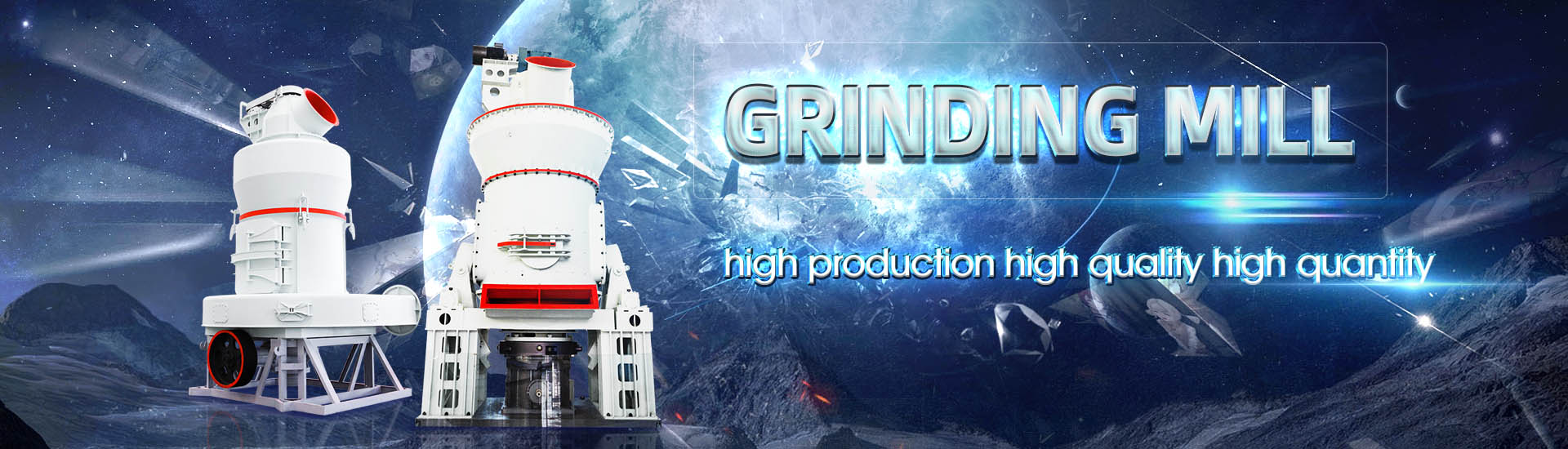
Cement industry energy saving grinding advanced control technology
.jpg)
Energy and cement quality optimization of a cement grinding circuit
2018年7月1日 Energy utilization of the cement grinding circuit was improved by 43% This study aimed at optimizing both the energy efficiency and the quality of the end product by modifying Automation and advanced process control (APC) have become increasingly influential forces within the modern cement industry Underpinning the development of intelligent plants, these Building an intelligent cement plant Advanced Process Control 2019年7月26日 Over many years, a variety of strategies for control and optimization of key industrial processes have been developed and implemented in EO, with particular focus on Advanced Control for the Cement Industry IEEE Control 2023年6月19日 Association of Portland Cement (ABCP), the International Energy Agency (IEA), the Cement Sustainability Initiative (CSI) of the World Business Council for Sustainable IMPROVING THERMAL AND ELECTRIC ENERGY
.jpg)
Towards Leveraging Artificial Intelligence for
2024年6月5日 By embracing the integration of relatively costeffective intelligent digital technologies into production processes and decisionmaking, cement manufacturers can harness the power of data analytics and artificial 2015年2月1日 In recent years, China's cement industry has taken several measures to reduce its energy consumption and CO 2 emissions, primarily through: increasing production Evaluation of energy saving potential in China's cement industry 2013年3月1日 In this paper, energy saving measures in the cement industry, such as energyefficiency measures for the preparation of raw materials, production of clinker, and the An overview of energy savings measures for cement industries2016年10月5日 In this chapter an introduction of widely applied energyefficient grinding technologies in cement grinding and description of the operating principles of the related equip‐ ments and comparisons over each other in EnergyEfficient Technologies in Cement Grinding

Estimation of energy efficiency improvement
It is therefore essential to understand the energy efficiency improvement opportunities in Taiwan’s cement industry A bottomup model is adopted for scenario analysis related to the availability 2015年2月1日 The cement industry, as a pillar of Chinese economic development, has grown rapidly alongside the national economy Cement production has increased dramatically from 6524 million tons in 1978 to 2099 million tons in 2011, with an average annual growth rate of 1108% (NBSC, 2013)Up to 2011, China has been the largest cementproducer in the world Evaluation of energy saving potential in China's cement industry 2021年2月8日 during the cement grinding process (gkg1); grind,fugitive: removal efficiency of fugitive PM control technology during the cement grinding process; EF clinker,gas : emission factor of gaseous species (SO 2 , NO x , and CO) per ton of clinker produced (gkg 1 ); : removal efficiency of control technology for gaseousCarbon and air pollutant emissions from China’s cement 2018年4月1日 Cement, as a very basic raw material for infrastructure, consumes high energy during its production process [1][2][3] Note that a large amount of energy was consumed in order to grind cement into Energy and cement quality optimization of a cement grinding
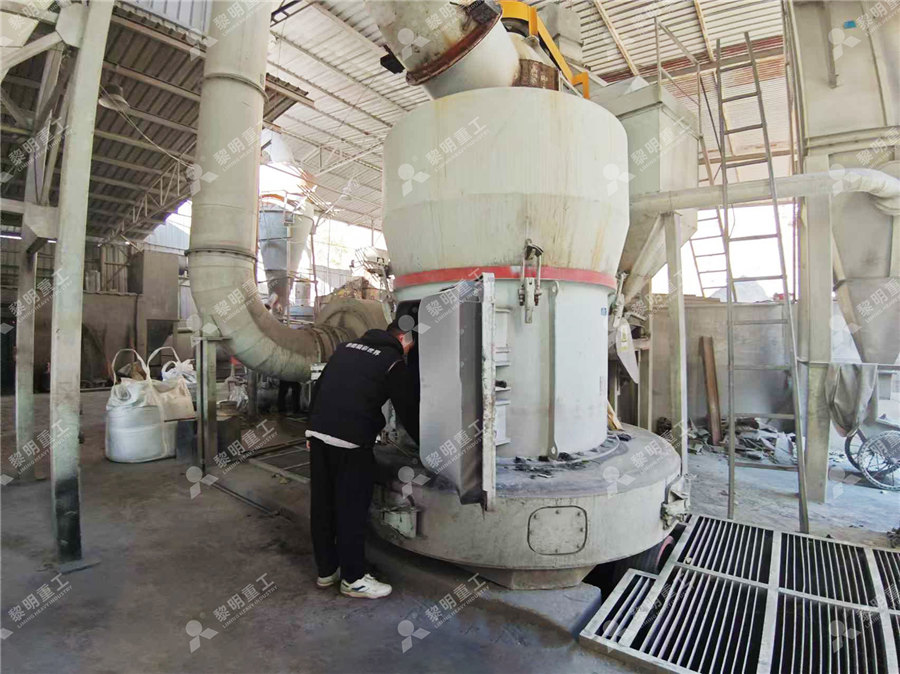
Air Pollution Control in Cement: Solutions Impact
2023年9月22日 By addressing key environmental concerns and utilizing advanced technologies, we aim to transform cement plants into ecofriendly and sustainable operations Understanding the Cement Industry's Air Pollution Challenges Before we dive into the solutions, it's crucial to see the need for air pollution control in cement industry Cement 2024年4月26日 An important benefit of enhancing energy efficiency in the cement industry would be the reduction in energy costs Broadly speaking, in the EU cement industry the energy bill represents about 40% of total production costs, while European cement production techniques are amongst the most energy efficient in the worldEnergy Efficiency and Saving in the Cement Industry2024年6月5日 Cement manufacturing is known for its significant energy consumption and environmental footprint As the world strives for sustainability, optimizing electrical energy consumption (EEC) in cement manufacturing is essential for reducing operational costs and minimizing the industry’s environmental impact This systematic review aims to synthesize and Towards Leveraging Artificial Intelligence for Sustainable Cement 2021年2月8日 67 (GB 49152013) promoted more advanced emission control technologies in the cement industry These timedependent 68 transitions should be implemented when constructing the historical trend of cement emissions in China 69 Based on the background above, the aim of this study is to quantify the decadal changes of carbon dioxide and air pollutantCarbon and air pollutant emissions from China's cement
.jpg)
Advanced grinding in the cement industry Request PDF
2003年1月1日 The use of highpressure grinding rolls (HPGR) prior to ball mills has become a common practice in cement clinker grinding due to significant energy savings in comparison to ball milling alone2018 In this chapter an introduction of widely applied energyefficient grinding technologies in cement grinding and description of the operating principles of the related equip‐ ments and comparisons over each other in terms of grinding efficiency, specific energy consumption, production capacity and cement quality are givenEnergyEfficient Technologies in Cement Grinding10 Most Effective EnergySaving Techniques in the Cement Industry The cement industry is one of the most energyintensive sectors globally Implementing energysaving techniques can significantly reduce operational costs and carbon emissions Advanced Kiln Control Systems Implementing advanced control systems for kiln operations can 10 Most Effective EnergySaving Techniques in the Cement Industry2019年3月8日 Savings in the Cement Industries,” Renewable and Sustainable Energy Reviews 15, no 4 (2011): 2,042–60 Figure 2 : Rotary Cement Kiln (Dry Process with Cyclonic Preheaters)IMPROVING THERMAL AND ELECTRIC ENERGY
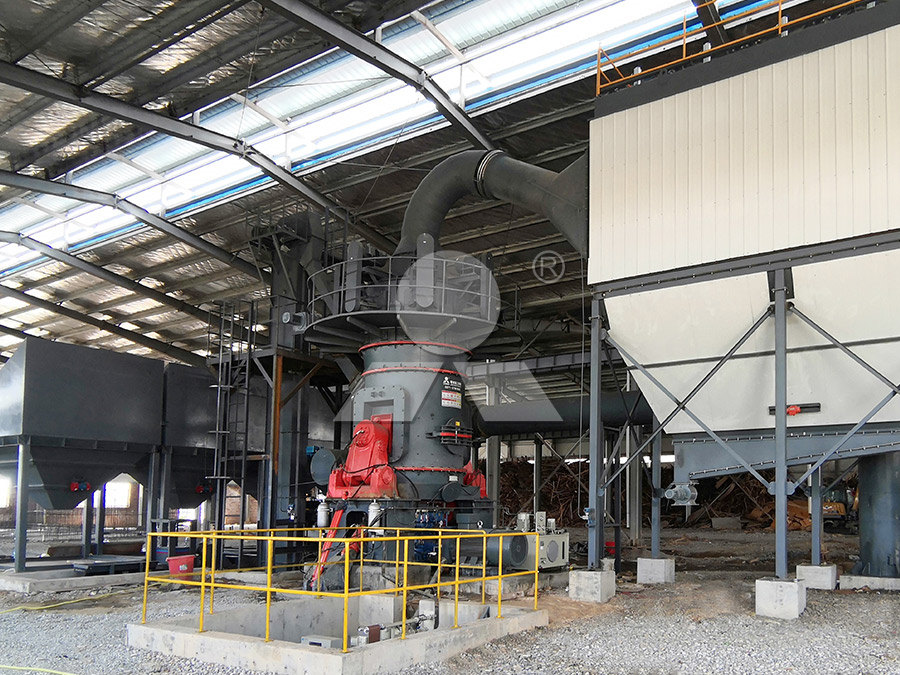
Energy Efficiency Improvement Opportunities for the
2024年8月23日 each technology or measure, costs and energy savings per tonne of cement produced are estimated and then carbon dioxide emissions reductions are calculated based on the fuels used at the process step to which the technology or measure is applied The analysis of cement kiln energyefficiency opportunities is divided into technologies and measuresInnovations in Portland cement manufacturing [81] Buzzi, S, Sassone, G, 1993 Optimization of clinker cooler operation [82] Birch E Energy savings in cement kiln systems energy efficiency in the cement industry Elsevier Applied An overview of energy savings measures for 2018年7月1日 Among the industries, the nonmetallic industry was reported as the third largest energy user and accounted for about 12% of the global energy use [1]Within this portion, cement industry had the majority of the utilization with 85–12% [1], [2]US Energy Information Administration (EIA) [7] named cement industry as the most energy intensive among the Energy and cement quality optimization of a cement grinding circuit2023年8月21日 ICR looks at the inner workings of grinding mills in the cement industry to understand the technological advancements that are reshaping the landscape against the foreground of sustainability Innovations to enhance the grinding processes are aimed at minimising their environmental footprint while increasing efficiency and performance In CuttingEdge Grinding Solutions Indian Cement Review
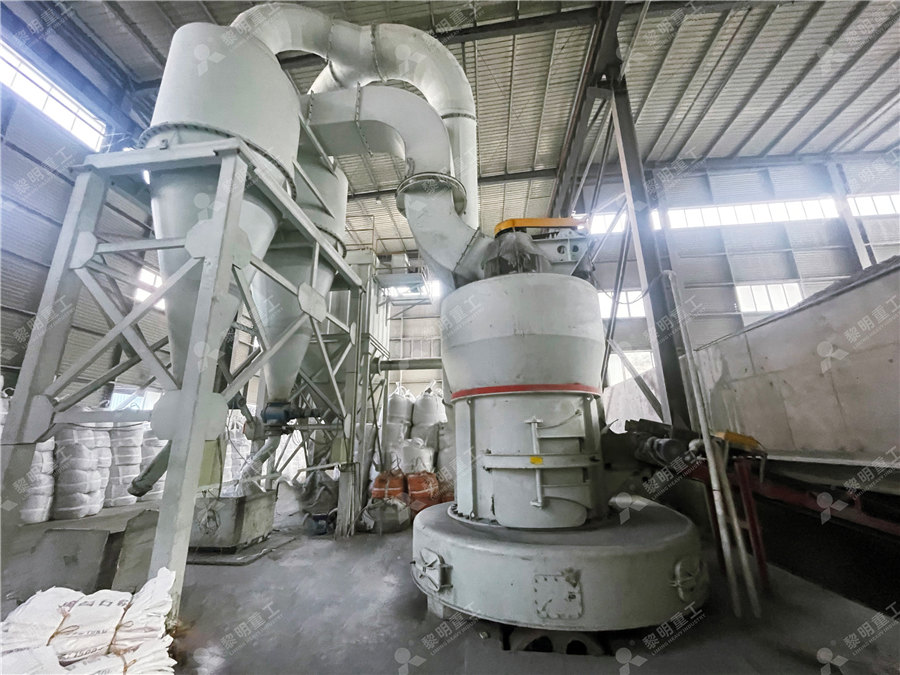
Applications of Efficient EnergySaving Cement Grinding Technology
2010年10月1日 Joint grinding system is the preferred cement grinding system of current cement process design, the advantages are high productivity, low energy consumption of system and low noise, etc2021年2月8日 China is the largest cement producer and consumer in the world Cement manufacturing is highly energyintensive and is one of the major contributors to carbon dioxide (CO2) and air pollutant Carbon and air pollutant emissions from China's cement industry 2024年3月28日 Additional elements being tackled include mining, raw meal grinding, cement grinding, electricity usage and cement mixingThe future of advanced process control will be Artificial Intelligence Augmented Plants (AIAP) across these process stages: combining human expertise with AI to orchestrate complex plant operations and maximise process The future of advanced process control in cement production2021年3月30日 The cement industry is highly energyintensive, consuming approximately 7% of global industrial energy consumption each year Improving production technology is a good strategy to reduce the energy needs of a cement plant The market offers a wide variety of alternative solutions; besides, the literature already provides reviews of opportunities to Technological Energy Efficiency Improvements in Cement Industries
.jpg)
Advanced Process Control for Clinker Rotary Kiln and Grate
2023年3月3日 The cement industry includes energyintensive processes, eg, clinker rotary kilns and clinker grate coolers Clinker is obtained through chemical and physical reactions in a rotary kiln from raw meal; these reactions also involve combustion processes The grate cooler is located downstream of the clinker rotary kiln with the purpose of suitably cooling the clinker 2020年5月11日 In this analysis, the cement industry (Standard Industrial Classification 3241) includes establishments engaged in manufacturing hydraulic cements, including portland, natural, masonry, and pozzolana cements The production of cement is an energyintensive process Annually the cement industry spends over $1 billion energy purchasesEnergy Efficiency Improvement and Cost Saving 2013年3月1日 Processes like grinding, transport of materials and crushing utilize machine drives and account for the majority of electricity consumption, as is evident in the result of the Manufacturing Energy Consumption Survey (MECS) in 1998 presented in Fig 3Process heating, by which clinker is made in large kilns, accounts for about 90% of the natural gas consumption An overview of energy savings measures for cement industries2022年12月1日 In the cement industry, the total energy consumption accounts for 50–60% of the overall manufacturing cost, while thermal energy accounts for 20–25% (Wang et al, 2009; Singhi and Bhargava, 2010)The modern cement industry requires 110–120 kWh of electrical power to produce one ton of cement (Mejeoumov, 2007)Thermal energy is used mainly during Review on energy conservation and emission reduction
.jpg)
Carbon emissions mitigation methods for cement industry
2024年1月9日 Cement production contributes significantly to anthropogenic greenhouse gas emissions (GHG), a major contributor to global carbon emissions The environmental impacts of cement production have grown in recent years and it is urgent to reduce its carbon footprint Systems dynamics (SD) is a simulation method used to understand the nonlinear behavior of 2011年5月1日 New technologies can be developed to reduce its energy consumption as sizeable energy is consumed in grinding operation of a cement manufacturing process In another study [16] , it was found that cement mill, raw mill, crusher and heater consume approximately 38%, 35%, 3% and 24% of total energy, respectivelyA critical review on energy use and savings in the cement industries2022年9月19日 The cost of cement production is governed by so many factors like availability of raw material, quality of raw material and off course fuel for thermal energy and electrical energy As we know, the cement industry is highly energy intensive The cost of energy as a part of the total production in the cement industry is significantCement industry is giving a major thrust to energysaving 2020年10月13日 Separate grinding and subsequent blending is a commonly used practice in the cement industry, enabling the lowering of the specific electric energy demand by using highly efficient comminution techniquesEnergy saving with separate fine grinding International Cement
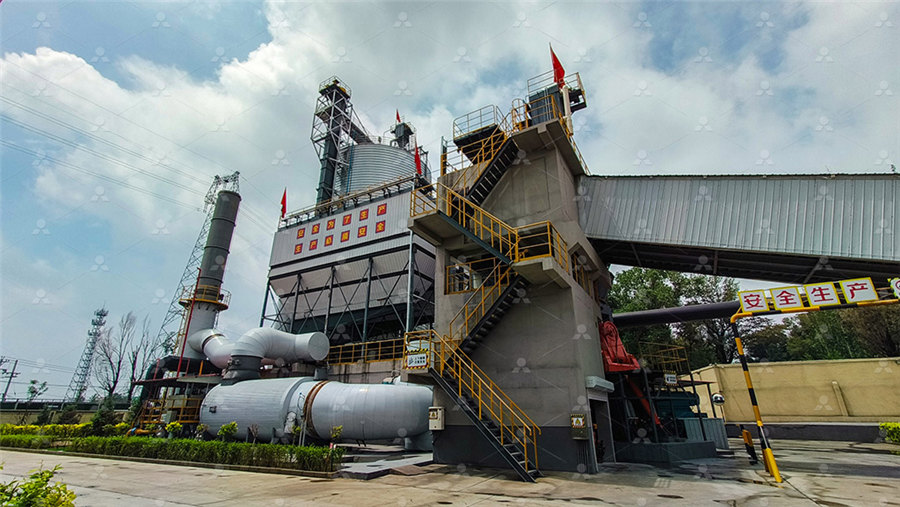
ACP Carbon and air pollutant emissions from China's cement industry
2021年2月8日 Abstract China is the largest cement producer and consumer in the world Cement manufacturing is highly energyintensive and is one of the major contributors to carbon dioxide (CO2) and air pollutant emissions, which threatens climate mitigation and air quality improvement In this study, we investigated the decadal changes in carbon dioxide and air 2018年7月1日 A critical review on energy use savings in the cement industries Renew Sustain Energy Rev (2011) saving a maximum of 430 GJ/t of thermal energy Furthermore, the use of advanced roller mills, Waste gas from rotary kiln and Upgradation of mill for finish grinding can save a maximum of 119 kWh/t, 1784 kWh/t, and 2593 kWh/t electrical Energy and cement quality optimization of a cement grinding circuit 2015年2月1日 The cement industry, as a pillar of Chinese economic development, has grown rapidly alongside the national economy Cement production has increased dramatically from 6524 million tons in 1978 to 2099 million tons in 2011, with an average annual growth rate of 1108% (NBSC, 2013)Up to 2011, China has been the largest cementproducer in the world Evaluation of energy saving potential in China's cement industry 2021年2月8日 during the cement grinding process (gkg1); grind,fugitive: removal efficiency of fugitive PM control technology during the cement grinding process; EF clinker,gas : emission factor of gaseous species (SO 2 , NO x , and CO) per ton of clinker produced (gkg 1 ); : removal efficiency of control technology for gaseousCarbon and air pollutant emissions from China’s cement
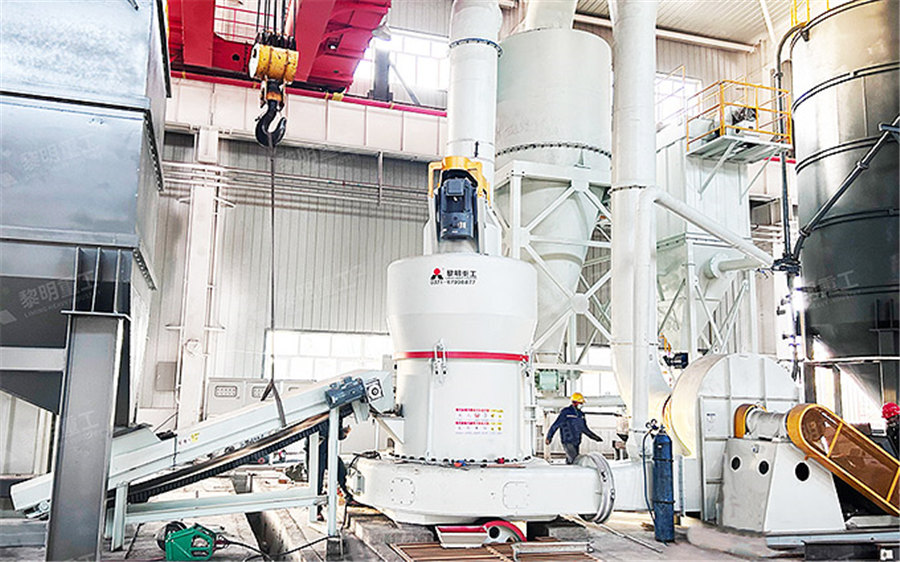
Energy and cement quality optimization of a cement grinding
2018年4月1日 Cement, as a very basic raw material for infrastructure, consumes high energy during its production process [1][2][3] Note that a large amount of energy was consumed in order to grind cement into 2023年9月22日 By addressing key environmental concerns and utilizing advanced technologies, we aim to transform cement plants into ecofriendly and sustainable operations Understanding the Cement Industry's Air Pollution Challenges Before we dive into the solutions, it's crucial to see the need for air pollution control in cement industry Cement Air Pollution Control in Cement: Solutions Impact2024年4月26日 An important benefit of enhancing energy efficiency in the cement industry would be the reduction in energy costs Broadly speaking, in the EU cement industry the energy bill represents about 40% of total production costs, while European cement production techniques are amongst the most energy efficient in the worldEnergy Efficiency and Saving in the Cement Industry2024年6月5日 Cement manufacturing is known for its significant energy consumption and environmental footprint As the world strives for sustainability, optimizing electrical energy consumption (EEC) in cement manufacturing is essential for reducing operational costs and minimizing the industry’s environmental impact This systematic review aims to synthesize and Towards Leveraging Artificial Intelligence for Sustainable Cement
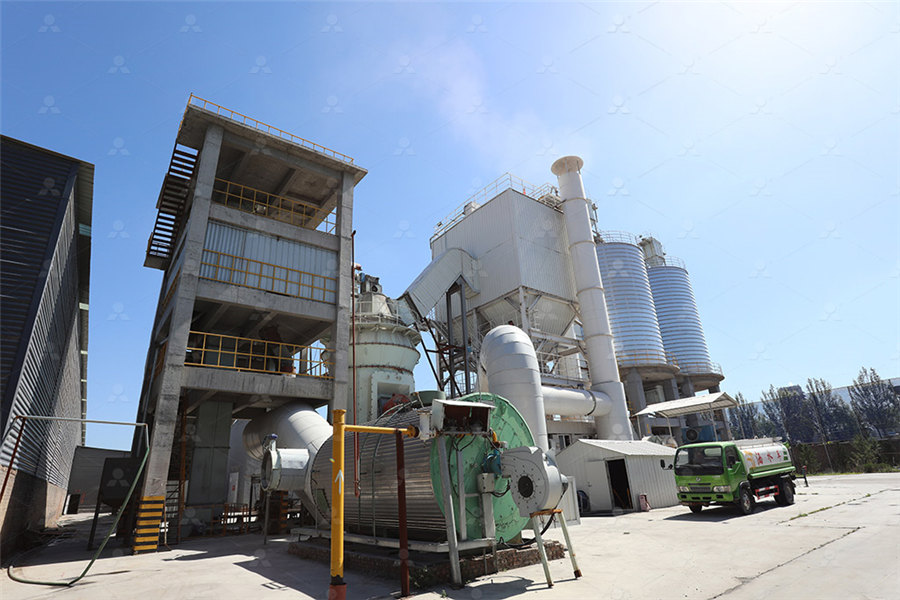
Carbon and air pollutant emissions from China's cement
2021年2月8日 67 (GB 49152013) promoted more advanced emission control technologies in the cement industry These timedependent 68 transitions should be implemented when constructing the historical trend of cement emissions in China 69 Based on the background above, the aim of this study is to quantify the decadal changes of carbon dioxide and air pollutant2003年1月1日 The use of highpressure grinding rolls (HPGR) prior to ball mills has become a common practice in cement clinker grinding due to significant energy savings in comparison to ball milling aloneAdvanced grinding in the cement industry Request PDF2018 In this chapter an introduction of widely applied energyefficient grinding technologies in cement grinding and description of the operating principles of the related equip‐ ments and comparisons over each other in terms of grinding efficiency, specific energy consumption, production capacity and cement quality are givenEnergyEfficient Technologies in Cement Grinding10 Most Effective EnergySaving Techniques in the Cement Industry The cement industry is one of the most energyintensive sectors globally Implementing energysaving techniques can significantly reduce operational costs and carbon emissions Advanced Kiln Control Systems Implementing advanced control systems for kiln operations can 10 Most Effective EnergySaving Techniques in the Cement Industry