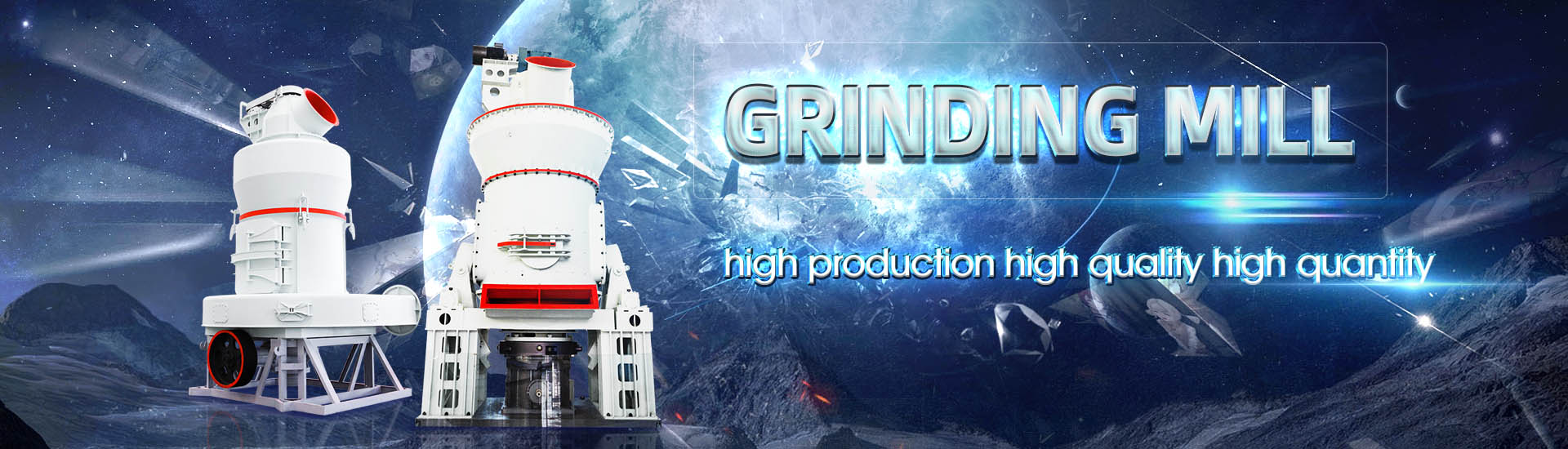
Vertical raw material mill
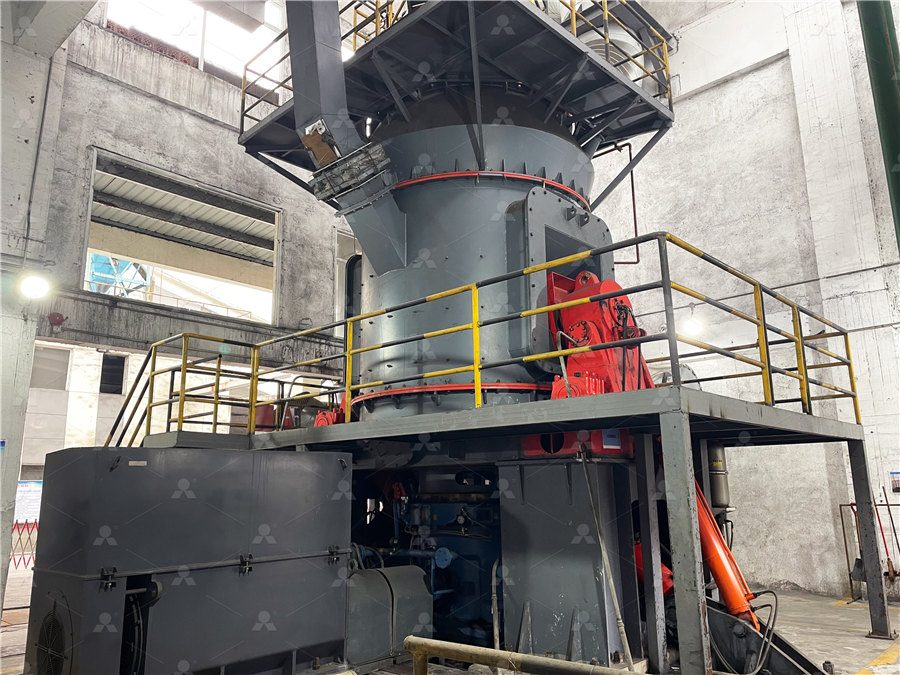
Vertical roller mill for raw Application p rocess materials
2016年1月4日 Vertical roller mills are adopted in 20 cement plants (44 mills) in Japan In the vertical roller mill which is widely used in the raw material grinding process, raw materials input Our bestinclass OK™ Mill is a globally successful vertical roller mill solution for grinding raw material, cement and slag Its cuttingedge design features consistently deliver the highest quality products with the greatest efficiency It Vertical roller mills FLSmidth CementOur bestinclass OK™ Mill is a globally successful vertical roller mill solution for grinding raw material, cement and slag Its cuttingedge design features consistently deliver the highest quality products with the greatest efficiency It OK™ Raw and Cement Mill FLSmidth Cement2024年11月22日 The vertical mill of raw material is used for grinding cement raw material or cement clinker and other industrial materials such as construction, chemical and ceramic It has a series of advantages, such as small volume, Vertical Raw Material Mill
.jpg)
UBE Vertical Mill UBE Machinery Corporation, Ltd
2024年1月31日 UBE Vertical Mill is used for grinding of cement raw materials, coal, cement clinker, blast furnace slag and other material Restoring your equipment to its original performance Maximizing your equipment 2022年5月31日 The vertical roller mill (VRM) is commonly used for secondary and tertiary crushing processes in numerous industries In this study, the discrete element method (DEM) Analysis of vertical roller mill performance with changes in material 2017年9月11日 For grinding cement, two types of mills are used ball and roller Recent decades have proven the great effectiveness of a vertical roller mill for grinding raw materials(PDF) Performance Evaluation of Vertical Roller No matter what type of material has to be ground – cement raw material, cement clinker or granulated blastfurnace slag – and how different their grindability and abrasiveness may be, the MVR mill ensures throughput rates of a different Cement mills and raw mills for high throughput
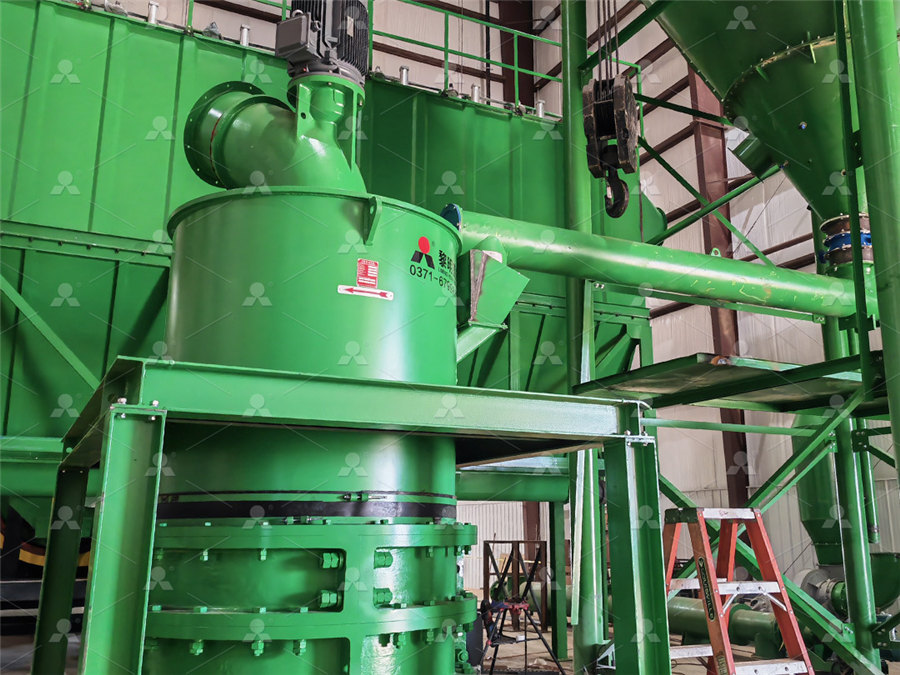
OK RAW AND CEMENT MILL FLSmidth Cement
2024年11月14日 available for raw grinding, ensure the ability to meet all possible capacity requirements in a single mill even for the hardest materials The wellknown reputation of the OK mill as a reliable machine that is easy to operate and maintain continues with the OK raw mill In addition to the roller design features, the OK mill retains the ability2024年6月21日 Roller; Roller pada Vertical Raw Mill berfungsi sebagai media penggilingan material ke meja Roller Vertical Raw Mill berjumlah empat buah dengan diameter 2,5 mANALISA KINERJA ALAT VERTICAL RAW MILL PABRIK II For raw materials and cement clinker, the vertical roller mill is an excellent grinding solution because of the relatively lower cost of installation, ease of operation and maintenance, energy efficiency and product quality Further, our Vertical roller mills FLSmidth Cement2024年11月20日 The power consumption of raw material vertical mill system is 97Kwh/t lower than ball mill, that is to say: in one year, a 5000TPD cement plant can save energy in clinker grinding system: 97kWh/t * 5000t/d * 300d=14,550,000 kWh, that means the cement plant clinker grinding system can save 14,550,000 kWh electricity one year Vertical Raw Mill CHAENG
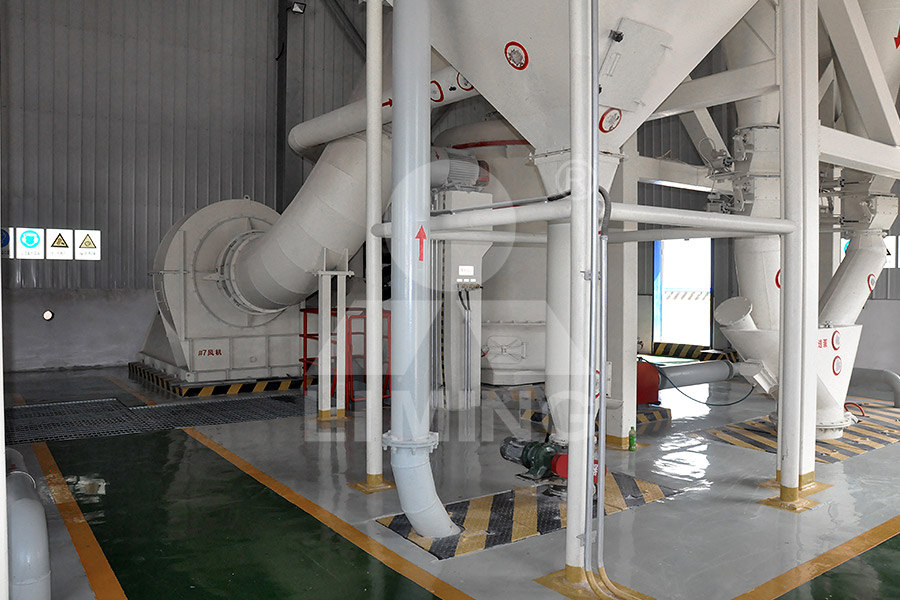
PROCESS OPTIMISATION FOR LOESCHE GRINDING
2017年8月12日 • Material grindability • Material temperature • Material moisture • Mixture composition • Composition of raw material • Grinding roller wear • Fineness (Blaine) or residue (VOA) • Mill motor speed • Mill air flow/mill differential pressure • Temperature after the mill • Pressure before the mill • Grinding stock feedFor raw material grinding a quadropol® vertical roller mills QMR² 45/23 was contracted to serve the kiln line, while for cement grinding two identical QMC² 45/23 were considered for grinding different cement types The request for interchangeable parts for the three mills was fulfilled and represents still a holistic approachquadropol® thyssenkrupp Polysius Grinding TechnologiesMPS vertical mill from Pfeiffer is the ideal allrounder Grinding of coal, petcoke, clay, limestone, quicklime, gypsum, and many other materials and remote control of grinding pressure and classifier rotor speed ensure a fully automatic operation of the MPS mill even with varying raw material characteristics Design principle and technical Coal mill, gypsum mill, clay mill, etc Pfeiffer MPS mills2024年11月26日 The roller grinding mill technology, patented in 1928 and continuously developed since then, has become synonymous with Loesche‘s pioneering engineering knowhow CEMENT BLAST FURNACE SLAG CEMENT RAW MATERIALCement Industry Loesche
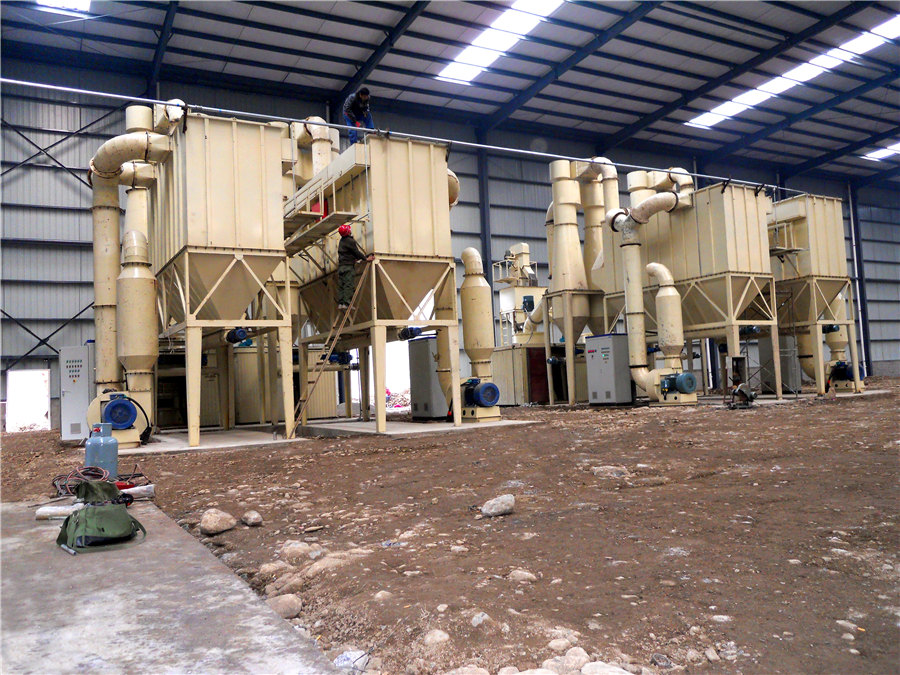
OPTIMIZATION OF INTERLOCKING MAIN MOTOR
Vertical Raw Mill is equipment for producing raw meal (the basic product for making clinkers) with a production capacity of 420 tons / hour As for the Vertical Raw Mill, the milling process of raw material has been arranged to become a material with a size of 90µ2024年11月13日 Vertical Roller SINOMALY produces cement raw material grinding mills in various specifications These machines are suitable for grinding mill production lines with an output of 2500t/d, 3200t/d, 4000t/d, 5000t/d, 6000t/d and 8000t/d The vertical grinding mill is utilized for the grinding of raw materials, mixed cement, and slag powderVertical Roller Mill for Cement Raw Material SINOMALY2017年9月11日 Due to the compact design and material transportation system of vertical roller mills (VRM), some important streams (total mill feed and discharge, dynamic separator feed and reject) remain in the (PDF) Performance Evaluation of Vertical Roller Vertical raw mill is important equipment widely used in the cement raw meal (cement raw materials) grinding section of the cement production process in cement plantBecause the vertical raw mill is the use of roller grinding principle Vertical Raw Mill for Cement Raw Meal Grinding
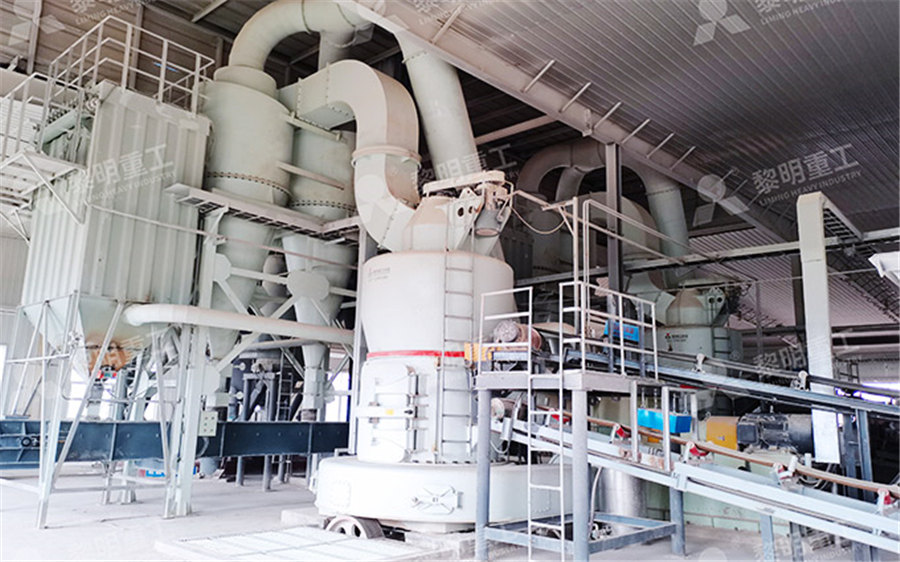
Analysis and Optimization of Grinding
2022年1月23日 This work concentrates on the energy consumption and grinding energy efficiency of a laboratory vertical roller mill (VRM) under various operating parameters For design of experiments (DOE), the response surface method 2024年1月31日 The mill motor is rotating the table via a gear reducer Raw materials are supplied onto the table through the chute and spead to the outer table by the centrifugal force STEP2 At the outer of table, the materials are ground by roller which pressed by hydraulic pressure Ground material drying by hot air are blown up to separator STEP3UBE Vertical Mill UBE Machinery Corporation, Ltd2021年7月27日 Raw materials grinding process is a first step of cement production which is has an important role in the first grinding step Vertical Raw Mill is a main equipment that is used in grinding or Evaluasi Kinerja alat Vertical Raw Mill Melalui Perhitungan Also the temperature at mill outlet influences the efficiency of the grinding process, with some raw materials more with others less In case the grindability of the raw material is bad and/or the efficiency of the grinding process is poor the internal recirculation of the material in the mill is high The material is crushed and ground between PROCESS TRAINING for operators of Vertical RAW Mills
.jpg)
MENGHITUNG EFISIENSI THERMAL PADA ALAT
2024年4月23日 Alfiansyah MR, dkk Menghitung Efisiensi ThermalPada Alat Vertical Raw Mill 550 Jurnal Multidisipliner Bharasumba (548559) langsung jatuh ke centre table yang berputar dan bergerak ke arah luar centre table karena gaya sentrifugal table Pada saat itu Type of mill: Ball and tube mills Vertical Roller Mills (VRM) Horizontal roller mill (Roll Press) Roller press with Ball mill Ball Mill Ball mills with high efficiency separators have been used for raw material and cement grinding in cement plants all these years Ball mill is a cylinder rotating at about 7080% of critical speed on two Raw Material DryingGrinding Cement Plant OptimizationTable 10 shows both the inlet and outlet streams of the vertical raw mill process and their mass and energy balances According to Table 3, the cement vertical raw mill system has an energy efficiency of 673 percent Energy efficiency percentages in this study followed a similar pattern, with estimated values between 60 and 70%Assessment of the thermodynamics efficiency of a cement vertical raw 2023年12月4日 A vertical roller mill (VRM) is a grinding equipment used for the size reduction of minerals, cement, and ceramics In processing plants, size reduction of raw materials is an energyintensive operation A vertical roller mill is a grinding equipment for many industries such as minerals, cement, and ceramics It is also used to grind slag Numerical Investigation of Vertical Roller Mill Operation
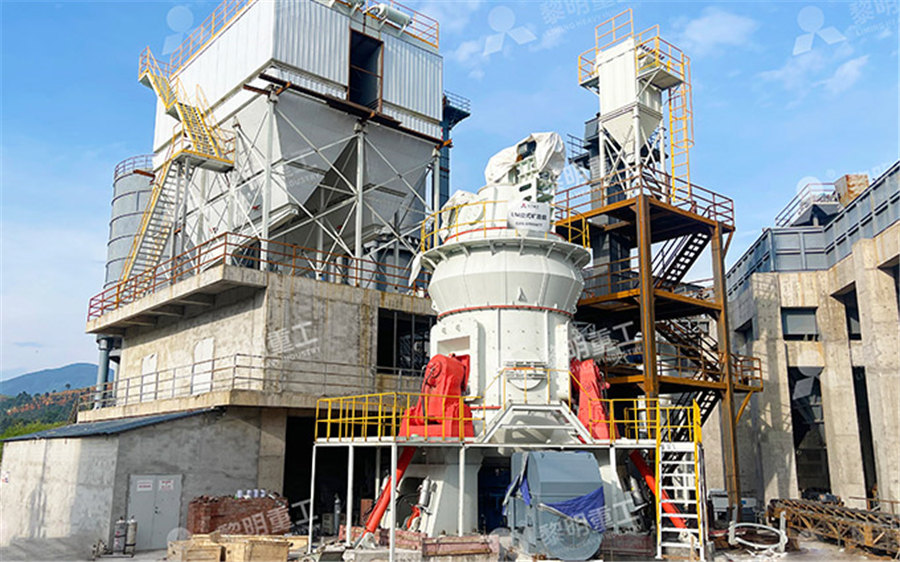
PFEIFFER MILLS FOR THE CEMENT INDUSTRY
2022年5月18日 7 // Almost any plant for the grinding of cement raw material is a combination of machines specially adapted to the particular physical properties of the material to be ground As a result, our plants work efficiently without any trouble » Highly efficient grinding, drying, and separating in one unit » Outstanding production capacities exceeding 1,400 t/h in one single mill2016年9月1日 Vertical roller mills, VRMs, are widely used for grinding raw materials in factories engaged in the extraction and processing of minerals Any machine used for grinding or crushing consumes around Operational parameters affecting the vertical roller mill Vertical Raw Mill: A vertical raw mill is mainly used in cement plants for raw material grinding Simple process flow, providing for drying, grinding and classifying all in one equipment; Minimum floor space requirement, compact layout and low investment in civil works; High grinding efficiency, low energy consumption and low wear on metal partsVertical Roller Mills LNV TECHNOLOGY2023年7月4日 3 Raw material grinding: The crushed raw materials are ground into a fine powder, called raw meal, using grinding equipment like ball mills or vertical roller mills 4 Pyroprocessing: The raw meal is heated in a rotary kiln at high temperatures (around 1450°C) to form clinker, a semifinished product consisting of small, nodular lumps 5Vertical Roller Mill in Cement Manufacturing Plant
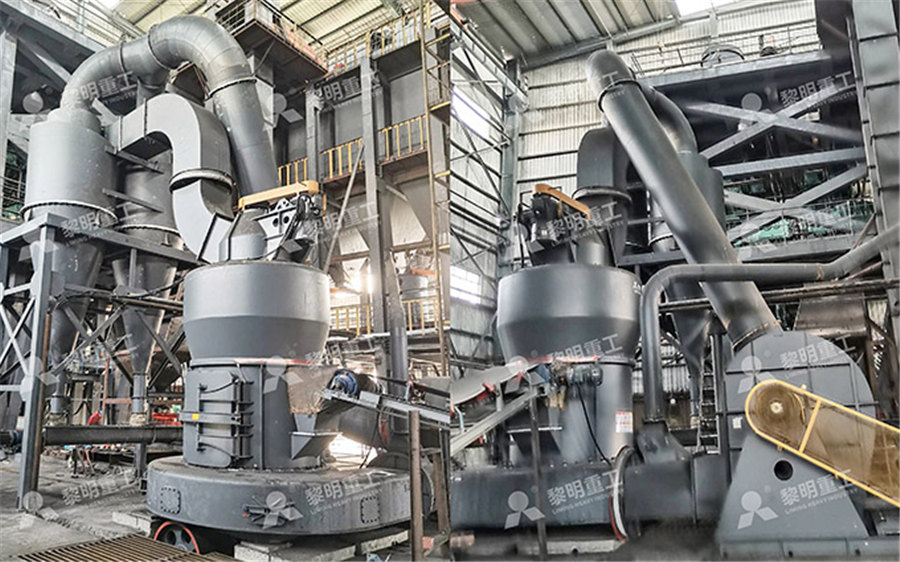
Cement mills and raw mills for small to medium throughput
MVR vertical roller mill with conventional planetary gearbox is the optimum solution from Pfeiffer in terms of economy for small to medium throughput rates For the preparation of cement raw material, cement, and granulated blastfurnace slag with small to medium output rates, the MVR mill with conventional drive is the right choice We can design and manufacture vertical roller mills of diversified specifications and models for raw meal, cement, and slag comminuation systems in cement clinker production lines with capacity up to 10,000t/d To continuously meet the needs of grinding various materials, we have developed a variety of VRMs for handling materials such as Vertical Roller Mill (VRM)SinomaLiyang Heavy Machinery 2022年1月11日 pembuatan artikel yaitu pengertian vertical raw mill, bagianbagian vertical raw mill, data instrument pada vertical raw mill, serta bahan baku pada pembuatan semen B Pengamatan Langsung (Observasi)(PDF) ANALISIS PENGGILINGAN DAN PENCAMPURAN 2024年10月13日 2 Raw Material Preparation: Before being fed into the kiln, raw materials must be ground to a specific particle size The vertical raw mill ensures that the raw materials are finely ground, which is crucial for the subsequent chemical reactions in the kiln 3 Energy Savings: Vertical raw mills are more energyefficient than traditional ball The vertical raw mill: A key component in cement production
.jpg)
Vertical Raw Material Mill
2024年11月22日 The vertical mill of raw material is used for grinding cement raw material or cement clinker and other industrial materials such as construction, chemical and ceramic It has a series of advantages, such as small volume, light weight, less land occupation, low electricity consumption, long life and so onAGICO Cement Vertical Mill AGICO Cement Ball Mill Cement Vertical Mill Grinding System Cement vertical mill, also called roller mill, is another raw mill commonly used in cement pared with the cement ball mill, it has a great difference in structure, grinding principle, process layout, automatic control, and energy consumption, which play an important role in the Raw Mill – Raw Mill In Cement Plant AGICO Cement Raw Mill2024年11月14日 available for raw grinding, ensure the ability to meet all possible capacity requirements in a single mill even for the hardest materials The wellknown reputation of the OK mill as a reliable machine that is easy to operate and maintain continues with the OK raw mill In addition to the roller design features, the OK mill retains the abilityOK RAW AND CEMENT MILL FLSmidth Cement2024年6月21日 Roller; Roller pada Vertical Raw Mill berfungsi sebagai media penggilingan material ke meja Roller Vertical Raw Mill berjumlah empat buah dengan diameter 2,5 mANALISA KINERJA ALAT VERTICAL RAW MILL PABRIK II
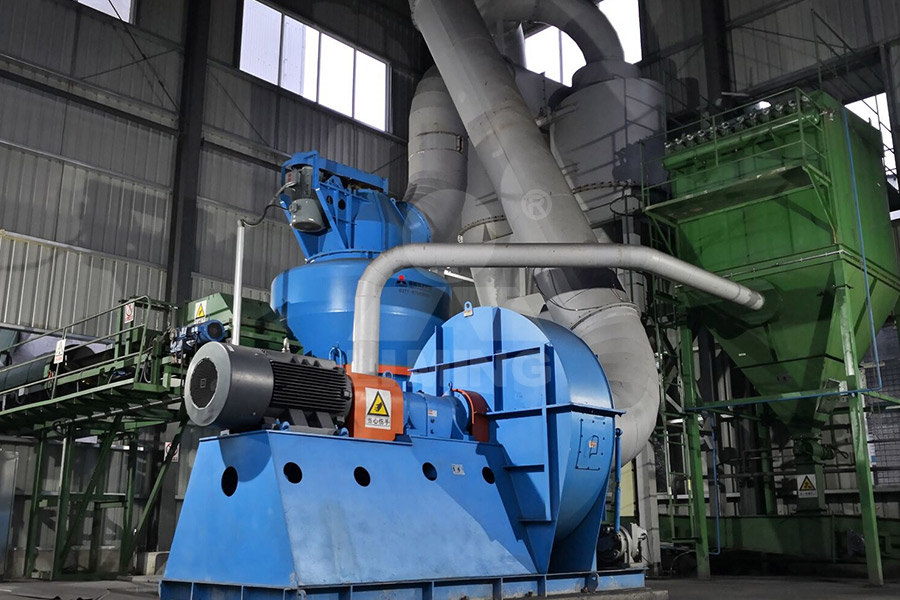
Vertical roller mills FLSmidth Cement
For raw materials and cement clinker, the vertical roller mill is an excellent grinding solution because of the relatively lower cost of installation, ease of operation and maintenance, energy efficiency and product quality Further, our 2024年11月20日 The power consumption of raw material vertical mill system is 97Kwh/t lower than ball mill, that is to say: in one year, a 5000TPD cement plant can save energy in clinker grinding system: 97kWh/t * 5000t/d * 300d=14,550,000 kWh, that means the cement plant clinker grinding system can save 14,550,000 kWh electricity one year Vertical Raw Mill CHAENG2017年8月12日 • Material grindability • Material temperature • Material moisture • Mixture composition • Composition of raw material • Grinding roller wear • Fineness (Blaine) or residue (VOA) • Mill motor speed • Mill air flow/mill differential pressure • Temperature after the mill • Pressure before the mill • Grinding stock feedPROCESS OPTIMISATION FOR LOESCHE GRINDING For raw material grinding a quadropol® vertical roller mills QMR² 45/23 was contracted to serve the kiln line, while for cement grinding two identical QMC² 45/23 were considered for grinding different cement types The request for interchangeable parts for the three mills was fulfilled and represents still a holistic approachquadropol® thyssenkrupp Polysius Grinding Technologies
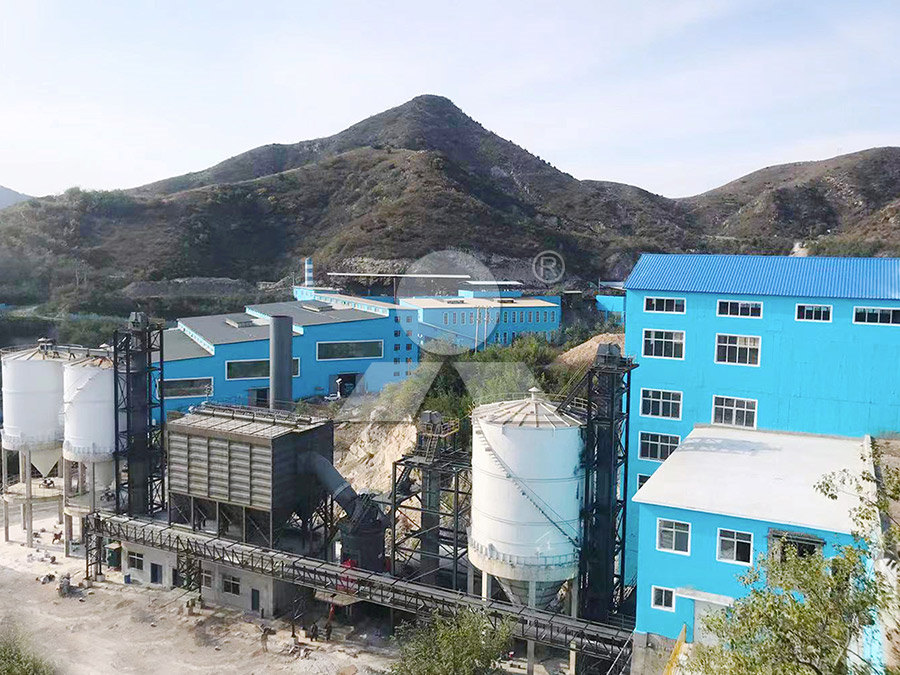
Coal mill, gypsum mill, clay mill, etc Pfeiffer MPS mills
MPS vertical mill from Pfeiffer is the ideal allrounder Grinding of coal, petcoke, clay, limestone, quicklime, gypsum, and many other materials and remote control of grinding pressure and classifier rotor speed ensure a fully automatic operation of the MPS mill even with varying raw material characteristics Design principle and technical 2024年11月26日 The roller grinding mill technology, patented in 1928 and continuously developed since then, has become synonymous with Loesche‘s pioneering engineering knowhow CEMENT BLAST FURNACE SLAG CEMENT RAW MATERIALCement Industry LoescheVertical Raw Mill is equipment for producing raw meal (the basic product for making clinkers) with a production capacity of 420 tons / hour As for the Vertical Raw Mill, the milling process of raw material has been arranged to become a material with a size of 90µOPTIMIZATION OF INTERLOCKING MAIN MOTOR 2024年11月13日 Vertical Roller SINOMALY produces cement raw material grinding mills in various specifications These machines are suitable for grinding mill production lines with an output of 2500t/d, 3200t/d, 4000t/d, 5000t/d, 6000t/d and 8000t/d The vertical grinding mill is utilized for the grinding of raw materials, mixed cement, and slag powderVertical Roller Mill for Cement Raw Material SINOMALY