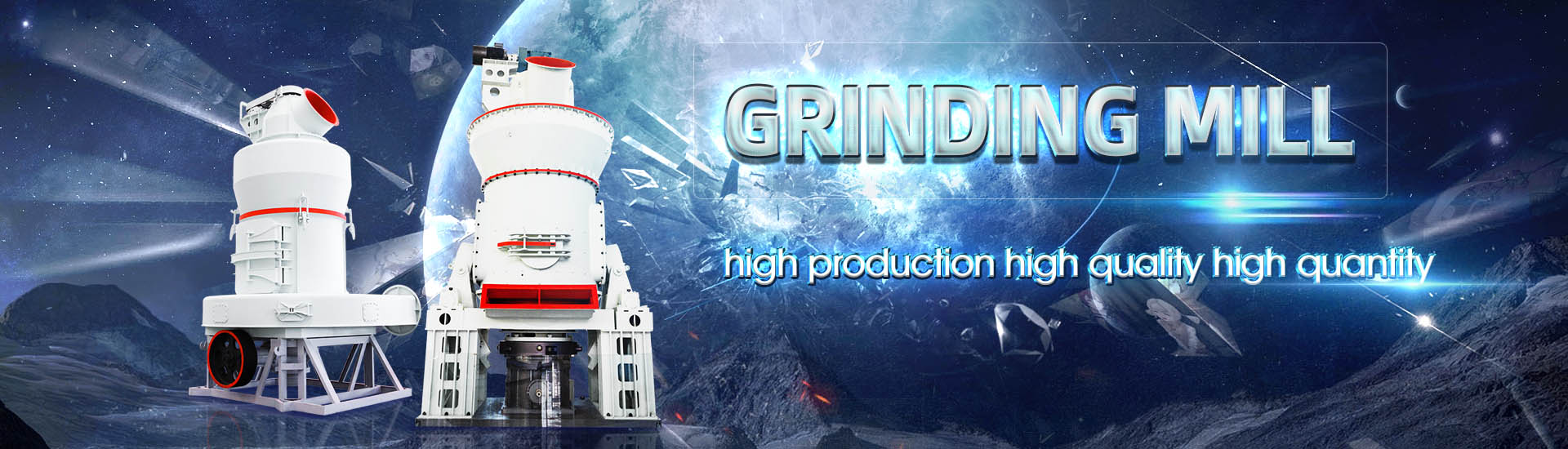
Several measures to improve the quality of cement mill production

Process technology for efficient and sustainable cement
2015年12月1日 Taking into account all processintegrated measures, thermal process efficiency reaches values above 80% of the theoretical maximum The grinding of raw materials and cement has been in the focus of better energy utilisation, but product quality is also of the highest 2024年3月1日 To further improve the sustainability of cement production, optimization of the clinkering process is a key factor This optimization not only leads to improved manufacturing Cement and Concrete Composites ScienceDirect2014年9月23日 Several studies focus on the evaluation of environmental performance in cement industry with life cycle inventory (LCI) and life cycle assessment (LCA) approaches Data The LCA of portland cement production in China1987年8月1日 Cement manufacturing process is now operated with the aid of various control systems, such as raw meal composition control, kiln control and mill control Those systems Optimization of Cement Manufacturing Process ScienceDirect
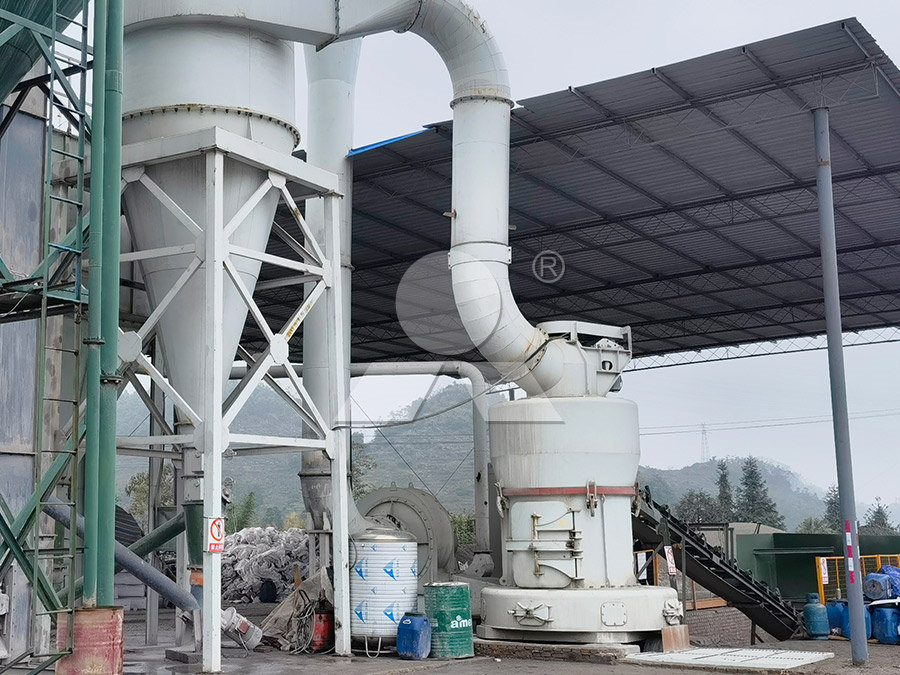
BALL MILLS Ball mill optimisation Holzinger Consulting
2021年3月12日 As grinding accounts for a sizeable share in a cement plant’s power consumption, optimisation of grinding equipment such as ball mills can provide significant cost 2024年5月22日 Market leaders are measuring key information and using the data to drive efficient bulk materials handling and blending via responsive automated controls Integration, Costefficient strategies for sustainable cement production2020年10月30日 In total six cement mills, four of them centre discharge mills, received an individual software package and parametrisation to reach the challenging optimisation guarantees of between 5% and 8% of production Highlevel control in cement production World 2024年5月22日 There are 4 stages of cement production that help maintain consistent raw material quality with minimal chemistry deviation, from quarry to silo to customer The Quarry: A practical guide to improving cement manufacturing
.jpg)
Modernizing cement manufacturing in China leads to
2022年11月17日 We find that novel suspension preheater rotary kilns account for approximately 99% of cement production in China in 2021 Climate change and fossil depletion are identified 2021年4月27日 Optimization of the Cement Ball Mill Operation Optimization addresses the grinding process, maintenance and product quality The objective is to achieve a more efficient OPTIMIZATION OF CEMENT GRINDING OPERATION IN 2024年6月1日 Cement production is a complex and essential process that involves several stages and impacts various aspects of the construction industry and the environment The first step in cement production is the extraction of raw materials, primarily limestone, clay and shale [34] These materials are typically obtained from quarries or mines, where Decarbonising cement and concrete production: Strategies, 2021年4月27日 yield substantial benefits in terms of energy savings and capacity increase Optimization of the Cement Ball Mill Operation Optimization addresses the grinding process, maintenance and product quality The objective is to achieve a more efficient operation and increase the production rate as well as improve the run factorOPTIMIZATION OF CEMENT GRINDING OPERATION IN
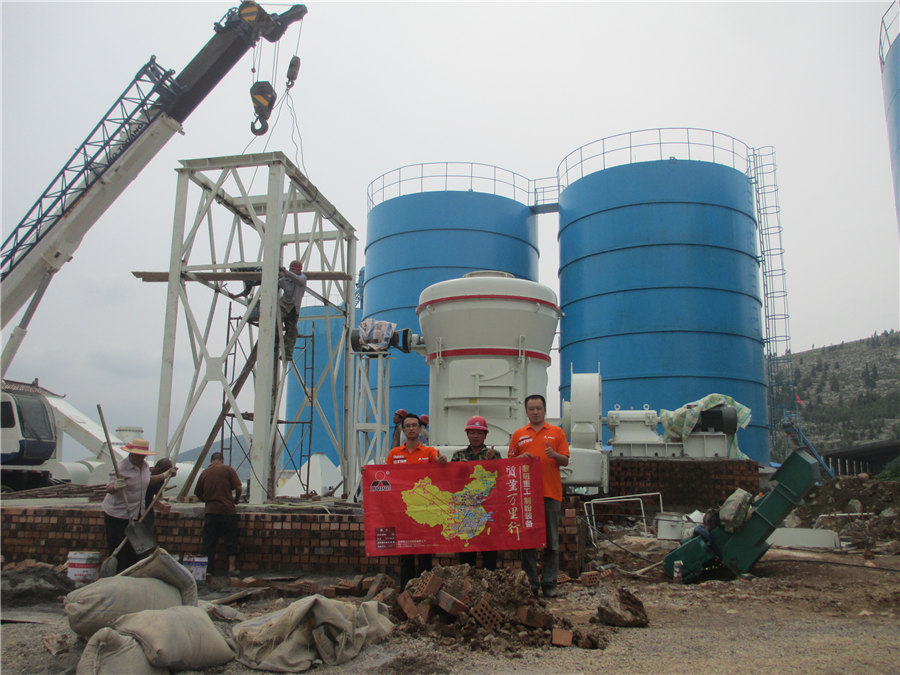
A practical guide to improving cement manufacturing
2024年5月22日 The cement production process 1 The Quarry: The cement production process begins with the extraction of limestone and clay from the quarry 2 Crusher and PreBlending: The material is then crushed to reduce particle sizes and blended to reduce variability in composition 3 Raw Mill and Kiln: Raw materials and additives are2023年12月28日 The ball mill for cement is a crucial equipment in the cement production process, designed to grind hard clinker into fine powder, playing a pivotal role in shaping the quality of cement products Its main structure consists of a hollow rotating cylinder where grinding media, such as steel balls, are placedHow To Improve Working Efficiency Of Ball Mill For Cement Production2024年10月21日 Honing the quality of cement plays a pivotal role in the petroleum industry throughout drilling operations, undoubtedly In cement plants, producing highquality clinker is essential for improving oil well maintenance, reducing expenditures, enhancing safety, and more, demonstrating its importance in the long term Despite tight control of clinker operational Effect of dusty clinker and alite crystal size on the properties 2023年1月1日 The above method of separating the hardened cement mortar from coarse aggregate and grinding this mortar and the device for using this method will simplify the existing technologies for recycling reinforced concrete structures, increase the efficiency of production lines, significantly improve environmental protection conditions, and above all Quality improvement of recycled aggregate ScienceDirect

How to Improve Cement Ball Mill Performance
The closedcircuit grinding system formed by a ball mill and a separator is a type of widely used cement milling system in cement plants and grinding stations There are many factors that may affect the ball mill’s working efficiency and product quality during operation2021年10月22日 While critical to many aspects of the built environment, the high levels of demand for cement currently results in more than 7% of anthropogenic greenhouse gas (GHG) emissions 8 The majority of the CO 2 emissions from cement production are from fossil resources (ie, mineral or energy resources that are not renewable on a short time horizon), Achieving net zero greenhouse gas emissions in the cement 2023年10月29日 The cement industry is a major contributor to carbon emissions, responsible for 5–8% of global emissions This industry is expanding, particularly in emerging economies, and it is expected that CO2 emissions will rise by 4% by 2050 To address this critical concern, this paper identifies ten factors that contribute to carbon emissions in the cement production Evaluation of Carbon Emission Factors in the Cement 2023年2月21日 To improve cement mill production, consider increasing the mill's capacity, optimizing operating parameters, improving the grinding process, enhancing separator efficiency, and implementing online How can we improve cement mill production? LinkedIn
.jpg)
Impacts of booming concrete production on water resources
2018年1月8日 Concrete is the mostused construction material worldwide Previous studies on the environmental impacts of concrete production have mainly focused on the materials involved and energy consumption 2019年3月8日 experience in the cement sector and focus on specific technical measures that could be implemented by cement plants to reduce their operating costs and improve their carbon footprints The IMPROVING THERMAL AND ELECTRIC ENERGY 2022年6月18日 In terms of sustainability, using waste material as a cement substitute in concrete has become a global trend This review article focused on studies that were performed to investigate the effect (PDF) Green concrete production with waste 2019年3月1日 An essential part of modern quality management system in cement production is stateoftheart radiation measurement technologies based on methods of neutron activation, Xray fluorescence and X (PDF) Cement Quality Control By Using Modern Radiation
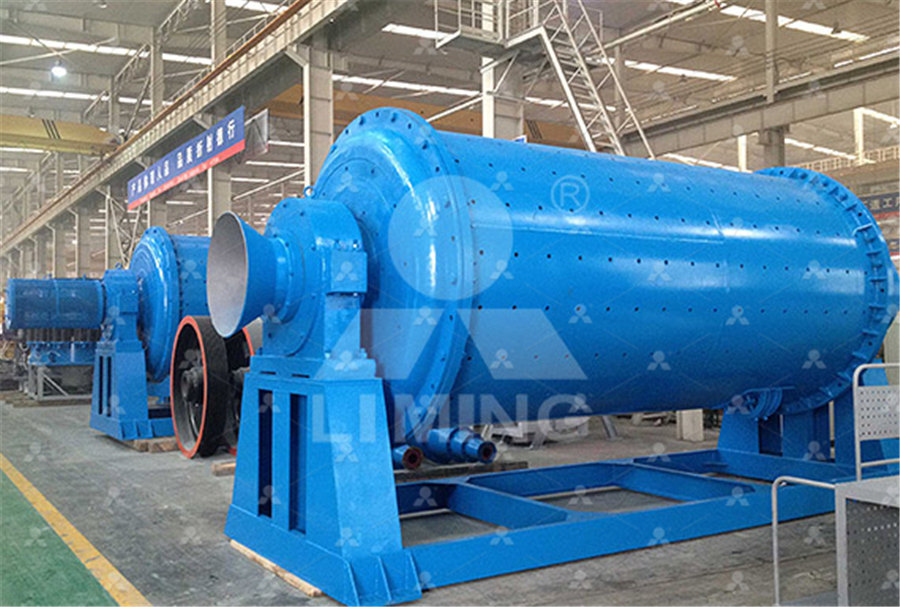
Cement Making Guide: Steps, Impact Green Alternatives
This blending is usually done using automated processes in a raw mill Quality Checks: Quality Control Measures Testing and Adjustments: Throughout the grinding process, quality control is essential to ensure the cement meets industry standards This includes periodic sampling and analysis of the cement to assess its fineness, setting time 2012年8月4日 Approach: It starts off by considering the current status quo and potential alternatives for the production process, right from the raw meal composition stage through to the final application of (PDF) An Overview of Cement production: How “greenVertical roller mills and ball mills represent two clearly distinct technologies However, with proper adjustments to the operational parameters of the vertical roller mill almost identical cement properties can be achieved by the two mills that satisfy the cement user’s demandsNevertheless, the two types of mills have their distinctive meritsCement grinding Vertical roller mills VS ball millsWith the increase of cement mill specifications and the requirement of energy saving, high yield, and high quality of cement grinding plant, the closedcircuit grinding is an inevitable trend of cement grinding unitThe essential equipment of a closedcircuit grinding system is a cement classifier, also known as a cement separatorThe function of the cement classifier is to select How To Measure Your Cement Mill And Cement Classifier? Cement
.jpg)
Sustainable concrete is possible The World Economic Forum
2024年9月13日 Global cement manufacturing is responsible for about 8% of the world's total CO2 emissions And the current trajectory would see emissions from the sector soar to 38 billion tonnes per year A new report from the World Economic Forum outlines four main decarbonization pathways for the cement and concrete industry2003年6月5日 Required water:cement ratio to achieve a slump of 60 to 70 mm in concretes made with different cements Cement E contained a limestone not conforming to the EN 1971 criteriaThe Use of Limestone in Portland Cement: A StateoftheArt 2020年2月1日 Nowadays, ball mills are used widely in cement plants to grind clinker and gypsum to produce cement In this work, the energy and exergy analyses of a cement ball mill (CBM) were performed and Energy and exergy analyses for a cement ball mill of a new 2012年7月1日 The present study aims to describe control charts techniques daily applied in the quality control of cement production and at the same time to develop mathematical models predicting the cement (PDF) Control Charts and Models Predicting
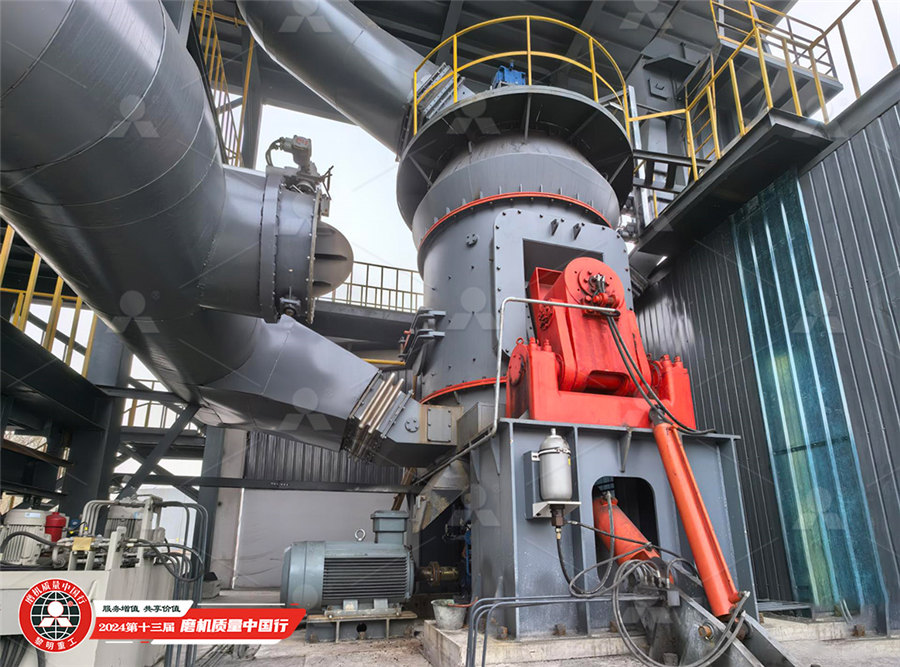
Quality Control of Cement Knowledge Base Applications
To produce highquality cement, the mineralogical and chemical composition of raw materials as well as intermediate and finished products has to be determined At each stage of the production, samples have to be taken, processed and analysed to ensure quality control without gaps2019年4月14日 The results of a specific grinding aid test and its effect on the quantity and quality of the final product were compared with the results obtained from process optimization of cement mill lines 1 (PDF) Investigating and comparing the effect of process 2023年1月25日 Abstract An improved differential evolutionary cement mill operation index decision algorithm based on constraint control and selection strategy is proposed to address the problem that the operation index is usually decided by manual experience in the cement mill operation process, which causes unqualified cement specific surface area and excessive The Decision Algorithm of Cement Mill Operation Index 2019年7月30日 Three of the most important goals of any cementmaking facility is to reduce product variation, extend quarry life, and meet customer requirements Today, there are many types of technologies available that can help cement production owners meet these goals as well as help improve product quality, boost efficiency, lower production costs, and create safer, 6 Points in the Production Process to Optimize Cement Making
.jpg)
(PDF) The improvement of mill throughput using Barmac pregrinding
2007年1月1日 Cement production is an energy intensive process that consumes a significant portion of world energy Production costs and environmental concerns are driving the need to use less energyOptimizing the operation of cement mills is essential to maximize productivity, reduce energy consumption, and improve the quality of the final cement product In this article, we will delve into practical strategies for cement mill optimization, backed by realworld figures and numbers, to enhance efficiency and performanceCement Mill Optimization: Practical Strategies for Enhanced 2022年11月17日 NSP rotary kilns started to account for more than 10% of the market share in 2001, and China’s national cement production peaked in 2014 Therefore, 2001 and 2014 are selected as typical years Modernizing cement manufacturing in China leads to 5 天之前 Before the concrete is even prepared, the quality of raw materials shall be checked, and only then they are mixed in a required proportion to form fresh concrete The quality of raw materials is directly related to the quality of concrete The quality control of concrete in this stage is done in two different steps They are as follows:Step Quality Control Of Concrete Construction Daily Civil
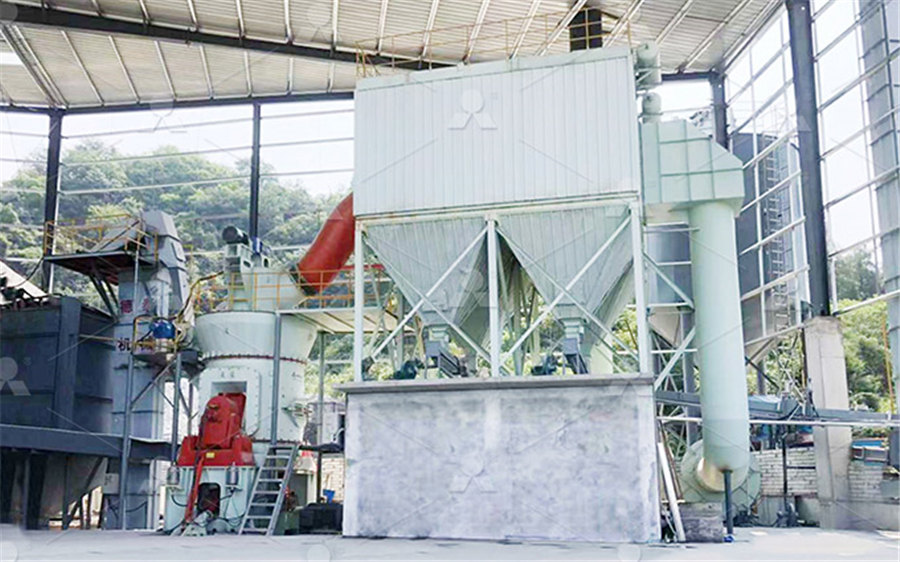
Decarbonising cement and concrete production: Strategies,
2024年6月1日 Cement production is a complex and essential process that involves several stages and impacts various aspects of the construction industry and the environment The first step in cement production is the extraction of raw materials, primarily limestone, clay and shale [34] These materials are typically obtained from quarries or mines, where 2021年4月27日 yield substantial benefits in terms of energy savings and capacity increase Optimization of the Cement Ball Mill Operation Optimization addresses the grinding process, maintenance and product quality The objective is to achieve a more efficient operation and increase the production rate as well as improve the run factorOPTIMIZATION OF CEMENT GRINDING OPERATION IN 2024年5月22日 The cement production process 1 The Quarry: The cement production process begins with the extraction of limestone and clay from the quarry 2 Crusher and PreBlending: The material is then crushed to reduce particle sizes and blended to reduce variability in composition 3 Raw Mill and Kiln: Raw materials and additives areA practical guide to improving cement manufacturing 2023年12月28日 The ball mill for cement is a crucial equipment in the cement production process, designed to grind hard clinker into fine powder, playing a pivotal role in shaping the quality of cement products Its main structure consists of a hollow rotating cylinder where grinding media, such as steel balls, are placedHow To Improve Working Efficiency Of Ball Mill For Cement Production
.jpg)
Effect of dusty clinker and alite crystal size on the properties
2024年10月21日 Honing the quality of cement plays a pivotal role in the petroleum industry throughout drilling operations, undoubtedly In cement plants, producing highquality clinker is essential for improving oil well maintenance, reducing expenditures, enhancing safety, and more, demonstrating its importance in the long term Despite tight control of clinker operational 2023年1月1日 The above method of separating the hardened cement mortar from coarse aggregate and grinding this mortar and the device for using this method will simplify the existing technologies for recycling reinforced concrete structures, increase the efficiency of production lines, significantly improve environmental protection conditions, and above all Quality improvement of recycled aggregate ScienceDirectThe closedcircuit grinding system formed by a ball mill and a separator is a type of widely used cement milling system in cement plants and grinding stations There are many factors that may affect the ball mill’s working efficiency and product quality during operationHow to Improve Cement Ball Mill Performance2021年10月22日 While critical to many aspects of the built environment, the high levels of demand for cement currently results in more than 7% of anthropogenic greenhouse gas (GHG) emissions 8 The majority of the CO 2 emissions from cement production are from fossil resources (ie, mineral or energy resources that are not renewable on a short time horizon), Achieving net zero greenhouse gas emissions in the cement
.jpg)
Evaluation of Carbon Emission Factors in the Cement
2023年10月29日 The cement industry is a major contributor to carbon emissions, responsible for 5–8% of global emissions This industry is expanding, particularly in emerging economies, and it is expected that CO2 emissions will rise by 4% by 2050 To address this critical concern, this paper identifies ten factors that contribute to carbon emissions in the cement production 2023年2月21日 To improve cement mill production, consider increasing the mill's capacity, optimizing operating parameters, improving the grinding process, enhancing separator efficiency, and implementing online How can we improve cement mill production? LinkedIn