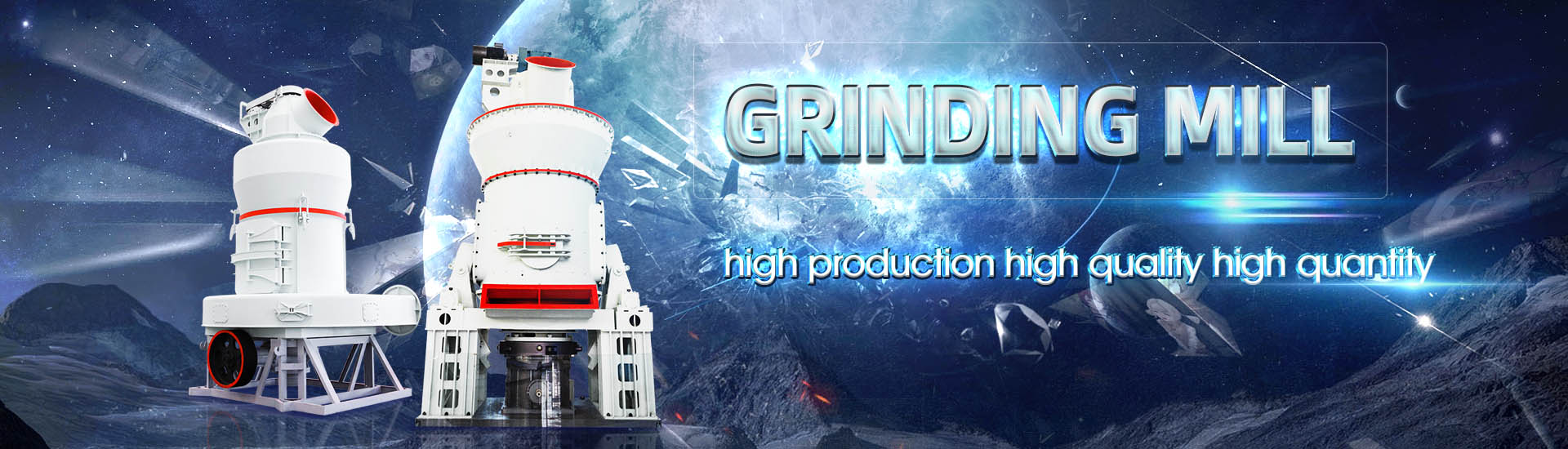
Grinding of cement raw materials

Raw Material DryingGrinding Cement Plant Optimization
Drying of moisture in raw materials is required for effective grinding and subsequent handling of raw meal This is achieved normally by ducting part of the kiln exhaust gas through the mill 2022年2月15日 Electricity consumption is a major energy efficiency indicator in cement raw materials grinding system Advance prediction of electricity consumption provides the basis for SALSTMs: A new advance prediction method of energy2004年11月1日 grinding limestone (and other raw materials to achieve the right chemical composition) to about 90% passing 90 μm in a dry circuit, making cement by the chemical Cement grinding optimisation ScienceDirectGrinding plays a pivotal role in the cement manufacturing process, transforming raw materials into a fine powder suitable for creating cement It’s a crucial step that directly impacts the physical Grinding in Cement Manufacturing: Key Process, Types of Mills,
.jpg)
Overview of cement grinding: fundamentals, additives,
2017年5月19日 PDF Grinding is an essential operation in cement production given that it permits to obtain fine powder which reacts quickly with water, sets in few Find, read and cite all the research2016年10月5日 High quartz content in clay substantially impacts the grinding of raw mix, quality of clinker and final cement produced The presence of quartz requires very fine grinding and a long sintering timeEnergyEfficient Technologies in Cement Grinding2021年4月19日 The developed models can be easily adapted to aid in the formulation of cement blends with different characteristics to the raw materials used in this study Grinding of finished Resistance to Grinding and Cement Paste Performance of Blends Cement production will experience several procedures which include raw materials blending process and burning process, cement clinker grinding process, and packaging process Modeling and Optimization of Cement Raw Materials Blending
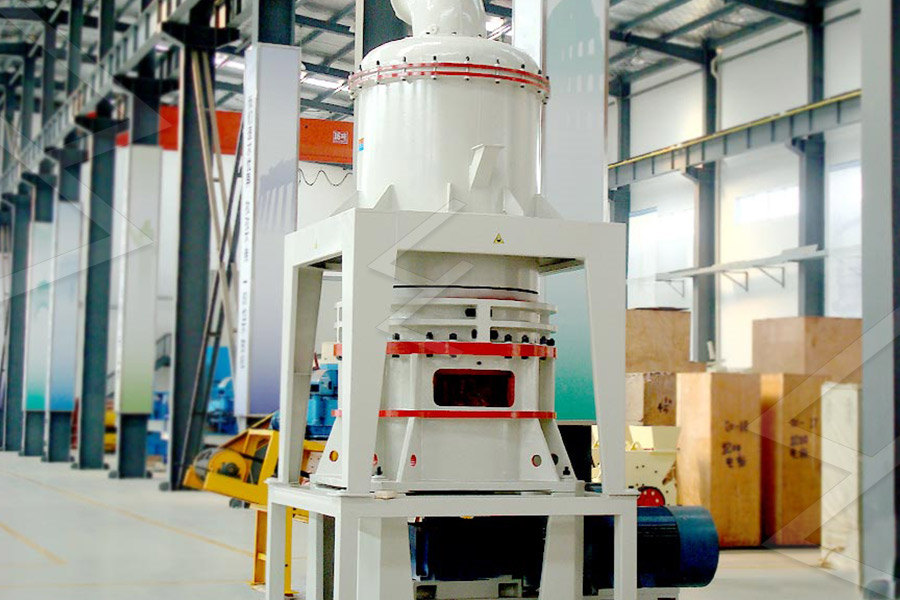
Preparation Of Cement Raw Material Cement Mill,
The cement raw materials is formed with calcareous materials, clayey materials and slight corrective material in appropriate proportion, and grinded into certain fineness The raw material production of cement plant can be classified into 2024年9月5日 2 Raw material grinding After crushing, the raw materials are carried to a grinding mill and made into a fine powder This is done using equipment such as ball mills or vertical roller mills The grinding process A Comprehensive Guide to the Cement Manufacturing 2016年10月5日 In this chapter an introduction of widely applied energyefficient grinding technologies in cement grinding and description of the operating principles of the related equip‐ ments and comparisons over each other in EnergyEfficient Technologies in Cement Grinding2021年4月19日 In Portland cement, oxides’ composition defines final product quality and performance Variations in chemical composition of the oxides are evidenced throughout the cement manufacture process at its different stages, such as mining of raw materials at different quarries, differences in the kiln burning conditions, or the addition of aggregates during the Resistance to Grinding and Cement Paste Performance of Blends
.jpg)
Understanding the Raw Materials for Manufacturing Cement
2024年8月20日 Raw Materials Used in the Manufacturing of Cement The preparation of cement using the raw materials involves the following process: Step 1: MiningThe extraction of raw materials such as limestone and clay from mines and quarries Step 2: Grinding processThese raw materials are grinded and crushed into a fine powderlike form This is called 1 Mixing of raw material The major raw materials used in the manufacture of cement are Calcium, Silicon, Iron and Aluminum These minerals are used in different form as per the availability of the minerals Table shows the raw materials for Portland cement manufacture The mixing procedure of the manufacture of cement is done in 2 methods, Dry Manufacture of Cement Materials and Manufacturing Process of The wear of grinding media when grinding cement raw materials is approx 2050 grams/t of mill throughput The wear of mill liners is approx 618 grams/t of mill throughput The size of the mill feed is up to 210 mm The particle size of the mill product is minus 300 micronsDrying of raw materials INFINITY FOR CEMENT EQUIPMENT2019年10月11日 The cement grinding plant is an individual section of finished cement production If the clinker production line is built near the city, for every 1t of clinker produced, about 16t of cement raw material is needed, and the Cement Grinding Plant Overview Cement Grinding Unit AGICO Cement
.jpg)
Clinker Grinding Techniques in Cement Manufacturing JM
2023年10月19日 Clinker grinders are an important part of the cement manufacturing process They are used to grind clinker into a fine powder and are typically located at the end of the cooler in a cement plant Clinker is a nodular material produced during the cement manufacturing process and is the primary raw material for making cement1 天前 The manufacture of Portland cement is a complex process and done in the following steps: grinding the raw materials, mixing them in certain proportions depending upon their purity and composition, and burning them to sintering in a kiln at a temperature of about 1350 to 1500 ⁰C During this process, these materials partially fuse to form nodular shaped clinker by Manufacturing of Portland Cement – Process and Materials2022年2月15日 However, different from ordinary multivariate time series prediction problems [12], cement raw materials grinding is a dynamic process with nonlinear, strong coupling among input variablesIn the grinding process, the fluctuation of one variable will lead to the fluctuation of other related variables [13]Therefore, it is difficult to extract the dynamic characteristics SALSTMs: A new advance prediction method of energyLime Component Limestone: Common forms of calcium carbonate used as raw material for cement manufacturing are limestone and chalkLimestone is of predominantly fine grained crystalline structure, its hardness is between 18 to 30 of the Mohs scale of hardness and specific gravity 2 To 28 Limestone usually contains admixtures of clay substance or iron compounds, Raw materials for cement manufacturing
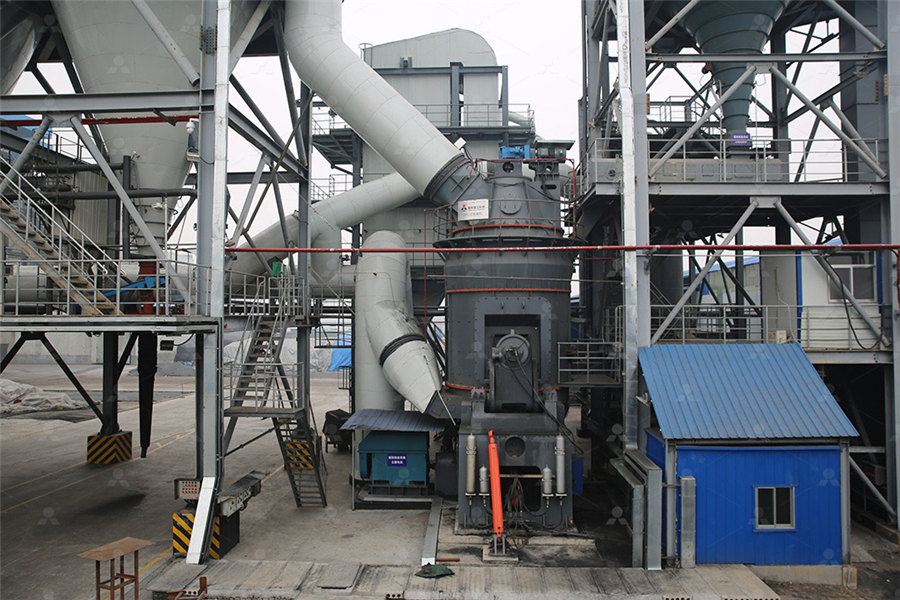
How Cement is Made Cement Manufacturing Process
Stage 2: Grinding, Proportioning, and Blending The crushed raw ingredients are made ready for the cementmaking process in the kiln by combining them with additives and grinding them to ensure a fine homogenous mixture The composition of cement is proportioned here depending on the desired properties of the cement Generally, limestone is 80%, and the remaining 20% In cement raw materials the lime component is generally represented up to an amount of 7680 0/o Therefore, the chemical and physical properties of this component are of decisive influence, when it comes to selecting a method of cement manufacturing as well Raw materials used for Cement Productioncement manufacture – 3 Portland cement in today’s world 2 Raw materials management system – 22 Concrete problems 16 1 Raw materials – 2 Raw mix – 3 Reserves – 4 Crushing – 5 Drying – 6 Preblending – 7 Storage and handling 3 Raw milling and blending 3 Computerised Maintenance Management Systems 30 1 Raw milling The Cement Plant Operations Handbook International Cement 2021年12月6日 In the production of Portland cement, grinding aids are added in small amounts in the range of 001 to 010% by weight of cement, Table 2 shows the mix proportions of raw materials subjected to grinding The reference cement (CEM The Effect of Various Grinding Aids on the Properties of Cement
.jpg)
An overview of alternative raw materials used in cement and
2019年4月23日 Introduction Portland cement underpins modern global development As such, it is the most abundantly produced material in the world (Deolalkar Citation 2016)The world has an abundance of the primary raw materials for cement manufacturing and, compared to other construction materials, cement’s cost is low and it has good durability (Hewlett Citation 2003)Raw material preparation II: drying and raw grinding The desired raw mix of crushed raw material and the additional components required for the type of cement, eg silica sand and iron ore, is prepared using metering devices Roller grinding mills and ball mills grind the mixture to a fine powder at the same time as drying it, before it is How cement is made Heidelberg Materials2021年1月1日 Stacking Reclaiming of Raw material: Swing type stacker Reclaimer: Limestone other raw material are stored in open area into a longitudinal storage unit called stockpile through Stacker These are then extracted transversely from the stockpile through reclaimer: 3: Raw Meal Grinding Homogenization: Grinding Mill Vertical Roller Mill Review on vertical roller mill in cement industry its performance 2018年8月28日 Raw mix is stored in a prehomogenization pile after grinding raw mix to fine powder CEMENT MANUFACTURING PROCESS PHASE III: PREHEATING RAW MATERIAL After final grinding, the material is ready to face the preheating chamber Preheater chamber consists of series of vertical cyclone from where the raw material passes before facing the kilnCement Manufacturing Process The Engineering Community
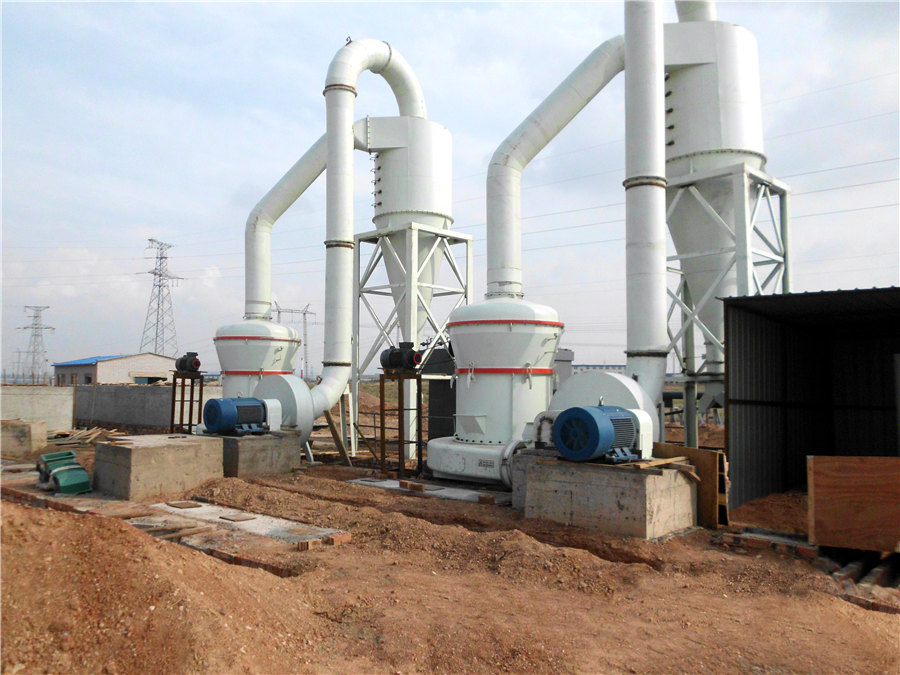
Everything you need to know about clinker/cement
Wear rate is the same for raw material and cement Different for slurry grinding (6 times more) This value can change a lot depending on the cement composition and the abrasivity of these components The [%] of free silica at mill feed for Brundick, H, “Drying and grinding of extremely moist cement raw materials in the Loesche mill,” ZKG International, No2, 1998, pages 6471Brundick, Horst, and Schäfer, HeinzUllrich, “Loesche mills for clinker grinding,” Asian Cement and Everything you need to know about cement Materials Almost any plant for the grinding of cement raw material is a combination of machines specially adapted to the particular physical properties of the material to be ground As our solutions are designed to suit the customers’ requirements, Raw mills for all requirements Gebr PfeifferAn intermediary storage of the raw material is necessary since the material flow has to be divided up after the primary crusher and the secondary crushers should be loaded The jaw crusher should be mentioned as alternative to the primary gyratory crusher However, its use for cement raw materials is advantageous only under very special conditionsEverything you need to know about Crushers in Cement industry
.jpg)
(PDF) Designing Raw Mix for Manufacturing Portland Cement
2021年10月31日 Portland Cement is manufactured by adding 3% gypsum to clinker which is produced by grinding, pulverizing, mixing, and then burning a raw mix of silica, and calcium carbonate2024年11月4日 Gas flow, advantage and disadvantage in the Raw mill and Cement mill installations – Grindability concept and the effects of intergrinding materials of different grindability – Ball mill grinding equations and dimensioning – Describe working principles for a separator – Grinding aids and other tools to boost efficiency – Control concepts – Influence of GRINDING TECHNOLOGY COURSE The Cement Institute1971年8月17日 calcareous raw materials, including limestone, chalk, marl, sea shells, aragonite, and an impure limestone known as "natural cement rock" Typically, these raw materials are obtained from openface quarries, but underground mines or dredging operations are also used Raw materials vary from facility to facility116 Portland Cement Manufacturing US EPA2020年9月22日 The predominant source of GHG emissions in cement production is the production of clinker at the kilning stage, although grinding, sorting of raw materials and packaging of cement bags also have a Environmental impacts and decarbonization strategies in the cement
.jpg)
Overview of cement grinding: fundamentals, additives, technologies
2017年5月19日 Grinding is an essential operation in cement production given that it permits to obtain fine powder which reacts quickly with water, sets in few hours and hardens over a period of weeks i The history of the development of the technology of raw material grinding defines the early history of cement technology Other stages of cement manufacture used existing technology in the early days Early hydraulic materials such as hydraulic limes, natural cements and Parker's Roman cement were all based on "natural" raw materials, burned Rawmill WikipediaThe cement raw materials is formed with calcareous materials, clayey materials and slight corrective material in appropriate proportion, and grinded into certain fineness The raw material production of cement plant can be classified into Preparation Of Cement Raw Material Cement Mill, 2024年9月5日 2 Raw material grinding After crushing, the raw materials are carried to a grinding mill and made into a fine powder This is done using equipment such as ball mills or vertical roller mills The grinding process A Comprehensive Guide to the Cement Manufacturing
.jpg)
EnergyEfficient Technologies in Cement Grinding
2016年10月5日 In this chapter an introduction of widely applied energyefficient grinding technologies in cement grinding and description of the operating principles of the related equip‐ ments and comparisons over each other in 2021年4月19日 In Portland cement, oxides’ composition defines final product quality and performance Variations in chemical composition of the oxides are evidenced throughout the cement manufacture process at its different stages, such as mining of raw materials at different quarries, differences in the kiln burning conditions, or the addition of aggregates during the Resistance to Grinding and Cement Paste Performance of Blends 2024年8月20日 Raw Materials Used in the Manufacturing of Cement The preparation of cement using the raw materials involves the following process: Step 1: MiningThe extraction of raw materials such as limestone and clay from mines and quarries Step 2: Grinding processThese raw materials are grinded and crushed into a fine powderlike form This is called Understanding the Raw Materials for Manufacturing Cement1 Mixing of raw material The major raw materials used in the manufacture of cement are Calcium, Silicon, Iron and Aluminum These minerals are used in different form as per the availability of the minerals Table shows the raw materials for Portland cement manufacture The mixing procedure of the manufacture of cement is done in 2 methods, Dry Manufacture of Cement Materials and Manufacturing Process of
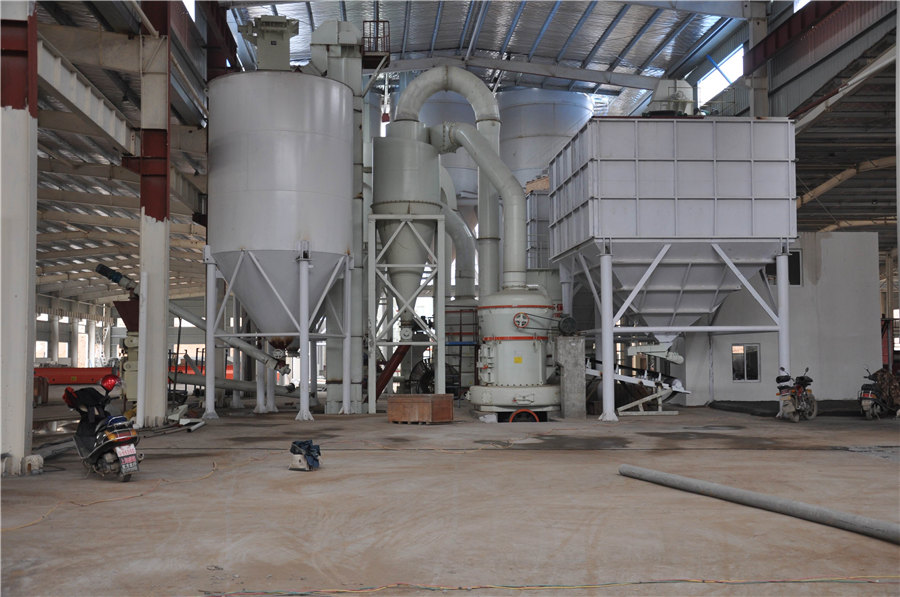
Drying of raw materials INFINITY FOR CEMENT EQUIPMENT
The wear of grinding media when grinding cement raw materials is approx 2050 grams/t of mill throughput The wear of mill liners is approx 618 grams/t of mill throughput The size of the mill feed is up to 210 mm The particle size of the mill product is minus 300 microns2019年10月11日 The cement grinding plant is an individual section of finished cement production If the clinker production line is built near the city, for every 1t of clinker produced, about 16t of cement raw material is needed, and the Cement Grinding Plant Overview Cement Grinding Unit AGICO Cement2023年10月19日 Clinker grinders are an important part of the cement manufacturing process They are used to grind clinker into a fine powder and are typically located at the end of the cooler in a cement plant Clinker is a nodular material produced during the cement manufacturing process and is the primary raw material for making cementClinker Grinding Techniques in Cement Manufacturing JM 1 天前 The manufacture of Portland cement is a complex process and done in the following steps: grinding the raw materials, mixing them in certain proportions depending upon their purity and composition, and burning them to sintering in a kiln at a temperature of about 1350 to 1500 ⁰C During this process, these materials partially fuse to form nodular shaped clinker by Manufacturing of Portland Cement – Process and Materials