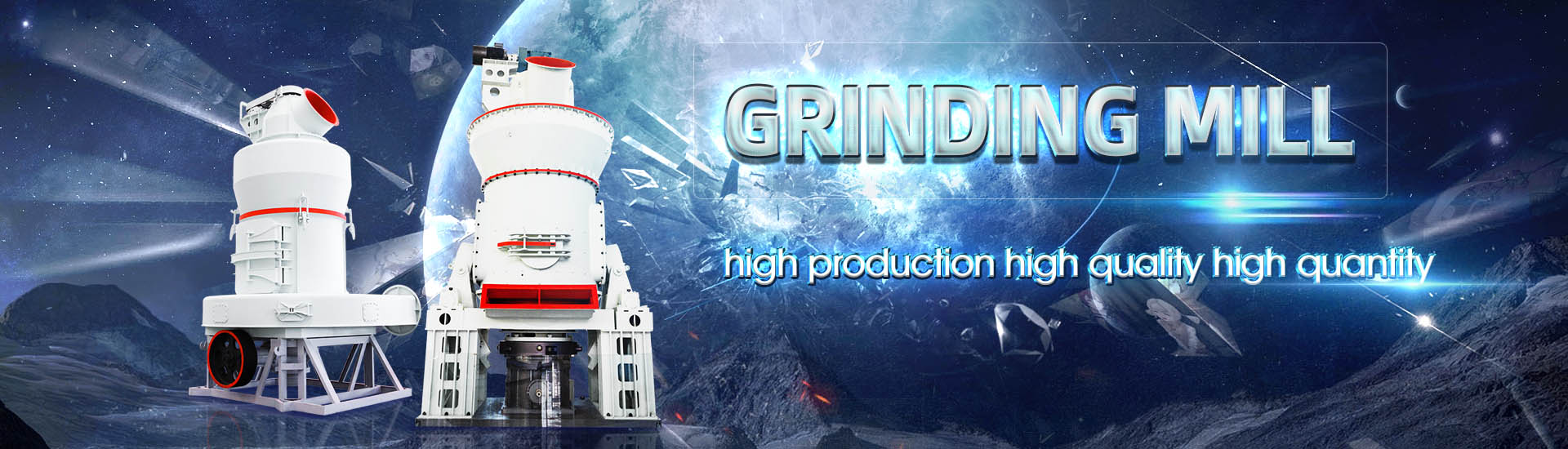
HOME→Hydrogen treatment crushing alloy equipment (HD furnace) Hydrogen treatment crushing alloy equipment (HD furnace ) Hydrogen treatment alloy crushing equipment (HD furnace)
Hydrogen treatment crushing alloy equipment (HD furnace) Hydrogen treatment crushing alloy equipment (HD furnace ) Hydrogen treatment alloy crushing equipment (HD furnace)
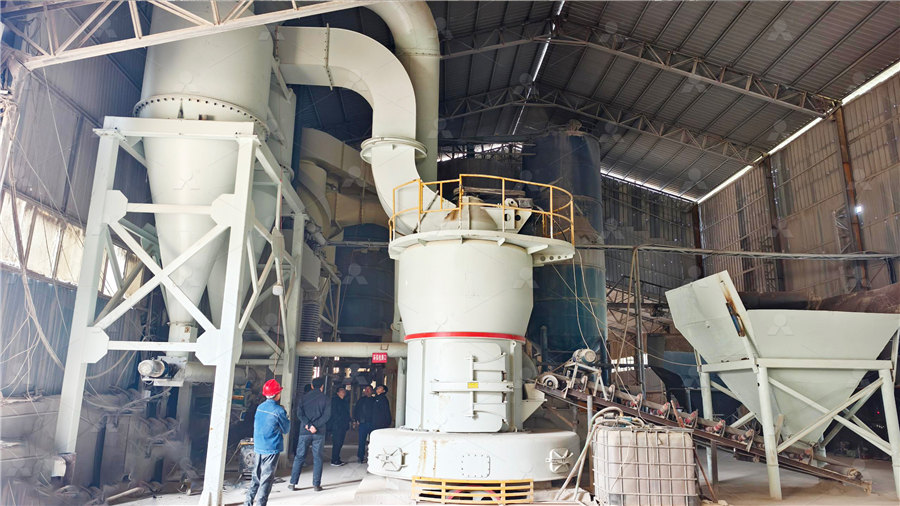
A strong and ductile mediumentropy alloy resists hydrogen
2020年6月17日 Strong and ductile materials that have high resistance to corrosion and hydrogen embrittlement are rare and yet essential for realizing safetycritical energy 2024年9月4日 This study investigates the microstructural evolution, thermal stability, and hydrogen storage behavior of asmilled Ti 5+x V 35 (CrMnFe) 60x (x = 0,10,20,30) high Effect of heat treatment on microstructural evolution and hydrogen Hydrogen atmosphere furnaces play a pivotal role in modern industrial processes, particularly in highend alloy sintering and advanced material manufacturing These specialized furnaces operate under controlled hydrogen environments, Hydrogen Atmosphere Furnaces: Applications, 2020年6月10日 Hydrogen production and storage with an economic and largescale industrialization will promote the further development of a full hydrogen shaft furnace Development and progress on hydrogen metallurgy
.jpg)
Development and progress on hydrogen metallurgy
2020年6月10日 Abstract: Hydrogen metallurgy is a technology that applies hydrogen instead of carbon as a reduction agent to reduce CO2 emission, and the use of hydrogen is beneficial to Hydrogenbased shaft furnace technology holds promise for lowcarbon hydrogen metallurgy Since hydrogenassisted iron ore reduction is highly endothermic, inadequate heat supply relevant to the contact of gas and densely packed A Review on the Modeling and Simulation of 2023年3月4日 The main views include hydrogeninduced phase transformation (HIPT), hydrogenenhanced decohesion (HEDE), hydrogenenhanced local plasticity (HELP), Overview of hydrogenresistant alloys for highpressure hydrogen 2021年12月20日 Hydrogen direct reduction (HDR) is the most promising ironmaking technology The latest developments of H 2 production and HDR in steel industry are Hydrogen direct reduction (HDR) in steel industry—An
.jpg)
Optimization of HydrogenBased Shaft Furnace Raw Material
2023年6月12日 Analyzes in detail the complex physical and chemical changes in the shaft furnace, reveals the effects of reduction gas flow rate and pellet diameter on the physical 2021年7月8日 Here, we introduce a counterintuitive strategy to exploit the typically undesired chemical heterogeneity within the material’s microstructure that enables local enhancement of Chemical heterogeneity enhances hydrogen resistance in 2022年1月15日 In all heat treatment tests, the samples were sealed with quartz tubes to prevent hydrogen escaping during the heat treatment All samples were vacuum dehydrogenated in a tubular hydrogen treatment furnace for 2 h at 700 °C with details summarized in Table 2 After vacuum dehydrogenation treatment, the residual hydrogen was less than 20 ppmThe effect of hydrogen treatment on microstructures evolution 2023年6月12日 In the context of reducing greenhouse gas emissions and achieving carbon neutrality, the steel industry is rapidly developing towards a lowcarbon hydrogen metallurgy path, and the hydrogenbased shaft furnace direct reduction route, which has lower CO2 emissions compared to the conventional blast furnace route, is now receiving widespread attention This Optimization of HydrogenBased Shaft Furnace Raw Material
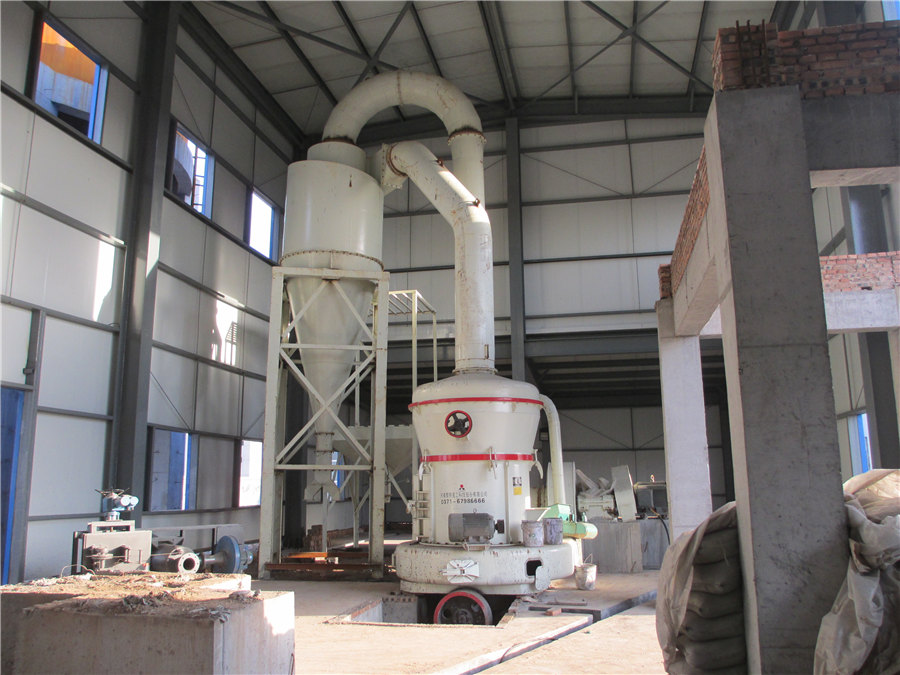
Thermo hydrogen treatment for microstructure refinement
2017年8月4日 Table 1 is the nominal chemical composition of the ascast ZTC4 alloy (the original material for the THT treatment) After a hightemperature static gas treatment (HSGT) of the ascast material, cylindrical specimens of 8 mm in diameter and 5 mm in height were machined from the bulk materialThen the THT treatment was performed on these samples, as 2021年4月18日 The global warming promotes the steel industry to replace part of coke by injecting hydrogenrich fuel into the blast furnace to reduce CO2 emissions and energy consumptionReview of hydrogenrich ironmaking technology in blast furnace2021年9月8日 Right now, the steel industry causes 72% of the total anthropogenic carbon dioxide emissions The total steel demand is forecasted to increase by onethird until 2050, leading to a further increase in carbon dioxide emissions [3]The higher scrap availability results in more steel production via the Electric Arc Furnace route forecasted to more than double from A review on the fundamentals of hydrogenbased reduction and recycling 2020年6月10日 Hydrogen metallurgy is a technology that applies hydrogen instead of carbon as a reduction agent to reduce CO2 emission, and the use of hydrogen is beneficial to promoting the sustainable development of the steel industry Hydrogen metallurgy has numerous applications, such as H2 reduction ironmaking in Japan, ULCORED and hydrogenbased steelmaking in Development and progress on hydrogen metallurgy
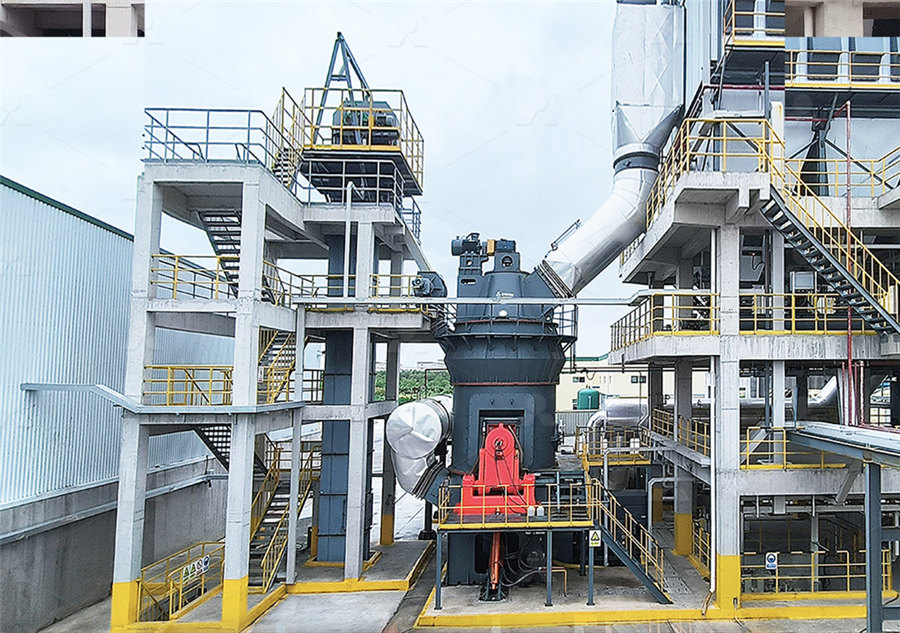
Deformation Characteristics and Microstructure Evolution of
2023年3月27日 The isothermal constant strain rate compression test of Ti6Al4V alloy with a hydrogen content of 031 wt% was carried out on a Gleeble1500 thermomechanical simulator The thermal deformation behavior at temperatures of 700950 °C and strain rates of 000110 s−1 was studied The results show that the flow stress of the alloy is sensitive to the deformation 2021年6月15日 Among all presented methods, only the electrochemical waterfeed processes are free from byproducts like CO2, CO, CH4 and C [19] if the electricity is provided by renewable sourcesAt the moment, 96% of all hydrogen is produced from fossil fuels and only 4% by electrolysis [20, 21]For industrial combustion application, the power to gas (P2G) route, based Assessment of natural gas/hydrogen blends as an alternative 2023年12月11日 The traditional ironmaking technologies (including coking, sintering, pelletizing, and BF ironmaking process) are carbonintensive, which makes the industry a significant contributor to global CO2 emissions Hydrogen replacement of carbon in steelmaking processes is a sustainable way to reduce CO2 emissions First, the reduction thermodynamics and HydrogenBased Reduction Technologies in LowCarbon 2016年11月10日 In the gravimetric measurements made using the high pressure furnace, the TiVZrNbHf sample absorbed hydrogen easily above 200 °C This was observed as a decrease in the hydrogen pressure in the Superior hydrogen storage in high entropy alloys
.jpg)
Hydrogen: A Novel Option in Human Disease Treatment
2020年9月8日 1 Introduction Molecular hydrogen (H 2) is the lightest chemical element in the earth’s atmosphereH 2 is often mixed in gas cylinders for deepsea divers to breathe, to prevent decompression and nitrogen sickness []In mammals, H 2 is spontaneously produced by intestinal bacteria in the process of anaerobic metabolism to produce energy and is enzymatically Hydrideforming alloys are currently considered reliable and suitable hydrogen storage materials because of their relatively high volumetric densities, and reversible H2 absorption/desorption kinetics, with high storage capacity A Comprehensive Review on Hydrogen 2021年11月10日 The effect of hydrogen injection on blast furnace operation and carbon dioxide emissions was simulated using a 1D steadystate zonal model The maximum hydrogen injection rate was evaluated on the Replacement of Pulverised Coal Injection (PCI) 2023年3月4日 With the progressive expansion of hydrogen fuel demand, hydrogen pipelines, hydrogen storage cylinders and hydrogen refuelling stations (HRSs) are the primary components of hydrogen energy systems Overview of hydrogenresistant alloys for highpressure hydrogen
.jpg)
Hydrogen direct reduction (HDR) in steel industry—An
2021年12月20日 The shaft furnace direct reductionelectric arc furnace (DREAF) route (Fig 1) is the primary alternative to the BFBOF route, which reduces lump ore/pellets to direct reduced iron (DRI) primarily using natural gas (NG), and further converts the DRI in an EAF The DREAF route significantly reduced the consumption of coke and coal while 2023年10月6日 The smelting process of blast furnace is carried out in the shaft furnace of a closed countercurrent reactor and heat exchanger The complex physical changes and chemical reactions are completed in the process of the countercurrent movement of the charge and gas in which the raw materials containing iron oxide (sinter, pellets, etc), coke, slag flux (limestone) Blast Furnace Ironmaking SpringerLink2024年2月6日 The minimum consumption of H 2 per ton of iron is 18285 m 3 in hydrogenrich blast furnace which has a ratio of carbon and hydrogen reducing agents of 4/1 If the theoretical minimum energy consumption is considered, compared with the full carbon blast furnace, the hydrogenrich blast furnace only replaces 3495 kg C with 18285 m 3 H 2Physicochemical principles of hydrogen metallurgy in blast furnace 2024年1月17日 33 Efiects of hydrogen treatment and compression on microstructure and phase structure Fig4 shows the microstructure of Ti6Al2Zr1Mo1V alloy before and after hydro genation treatmentHot deformation behavior of a near alpha titanium alloy
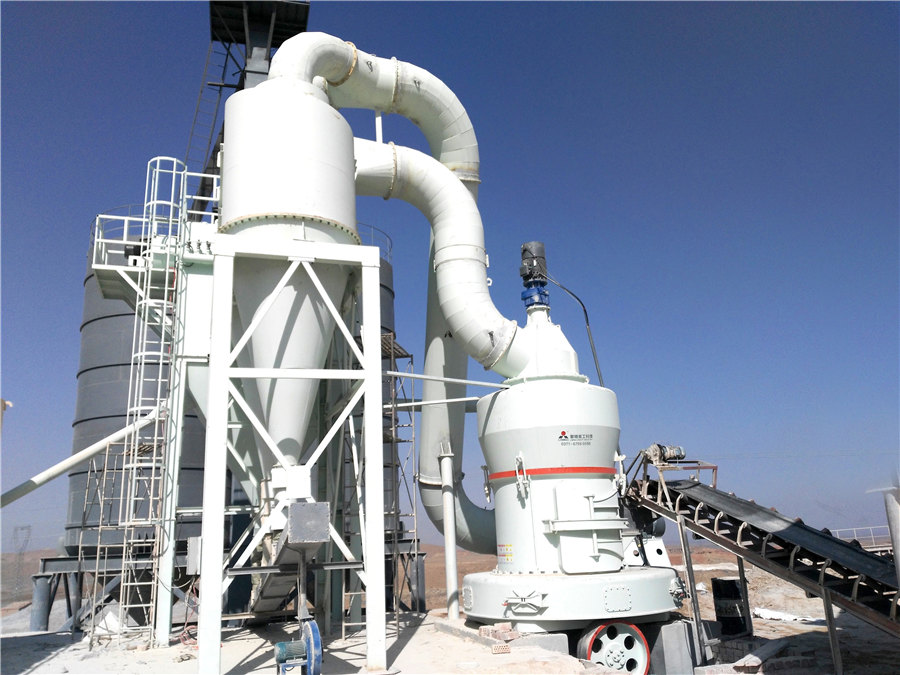
(PDF) Enhanced Hydrogen Generation Performance of Al
2021年12月20日 The main problem for the application of hydrogen generated via hydrolysis of metal alloys is the low hydrogen generation rate (HGR) In this paper, active Al alloys were prepared using a new alloy Ti6Al4V after hydrogen treatment This hydrogen treatment consisted of three stages: hydrogenation in a hydrogen gas atmosphere at 850 °C, a cyclic hydrogen treatment (1 or 3 cycles at 250 °C) and dehydrogenation in a vacuum (550 °C) It was shown that hydrogenEffect of high hydrogen treatment on the macro and 2023年3月4日 In hydrogen energy systems, hydrogenresistant alloys are primarily used for hydrogen refuelling stations (HRSs), hydrogen pipelines and hydrogen storage cylinders Currently, austenitic stainless steel is the most prevalent hydrogenresistant alloy in the aforementioned three applications [31, 34] However, highpressure hydrogen facilities Overview of hydrogenresistant alloys for highpressure hydrogen 2022年11月14日 After the thermal hydrogen treatment as reported in the literature [10], the lamellar β phase of cast titanium alloy was decomposed, and an equiaxed microstructure was formed Specifically, tensile strength of the cast titanium alloy treated by thermal hydrogen treatment increased by 274% without sacrificing plasticity [10]Improvement of mechanical properties and microstructural
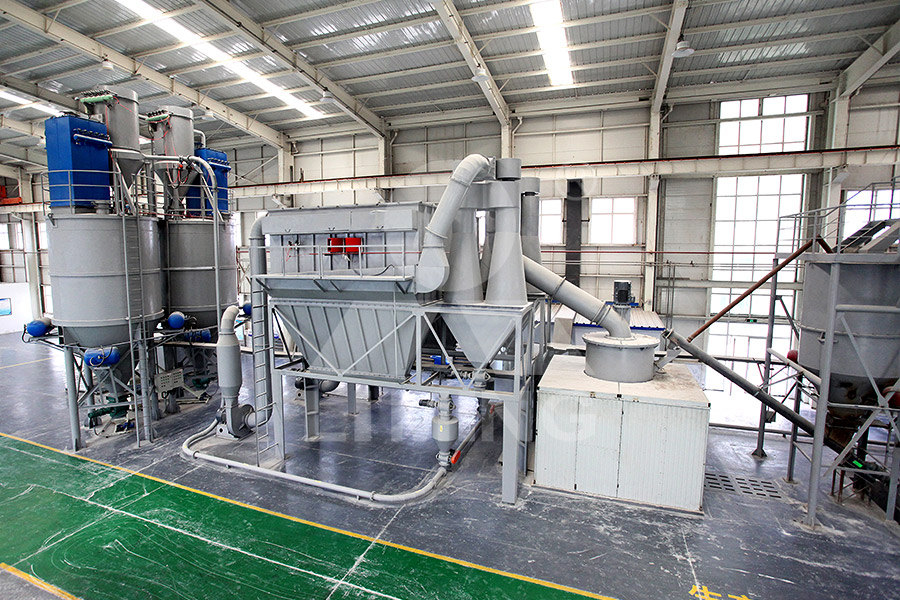
World’s First Hydrogen Combustiontype Continuous
2022年1月14日 *1:Continuous hydrogen combustiontype furnace: Rollertype furnace that performs highquality heat treatment by processing products to pass through the set temperature continuously by roller conveyance *2:CSERTRHKNero; Hydrogen combustion type CSERTRHK C : Ceramic, SERT : Single End Radiant Tube Burner, RHK : Roller Hearth Kiln2021年12月30日 Influence of the method of outoffurnace melt treatment on hydrogen content in 5083 aluminum alloy E G Partyko, Junior Researcher, Department of Foundry Production, School of Nonferrous Metals and Material Science 1, email: elforion@mail A I Bezrukikh, Candidate of Engineering Sciences, Deputy Head of Scientific and Research Department1,Influence of the method of outoffurnace melt 2023年2月14日 The steel industry is one of the major sources of greenhouse gas emissions with significant energy demand Currently, 73% of the world's steel is manufactured through the coalcokebased blast furnacebasic oxygen furnace route (BFBOF), emitting about two tonnes of CO 2 per tonne of steel produced This review reports the major technologies, recent Decarbonisation and hydrogen integration of steel 2017年2月11日 Thermo hydrogen treatment (THT) of titanium is a process in which hydrogen is used as a temporary alloying element in titanium alloys It is an attractive approach for controlling the microstructure and thereby improving the final mechanical properties In the present study, the microstructure of the original (nonhydrogenated) sample has only α phase and the grains is Influence of thermo hydrogen treatment on microstructure
.jpg)
Hydrogen Atmosphere Furnace Alundum Furnace
4 天之前 Alundum ® 99 furnace refractory should be specified in hydrogen atmosphere furnaces that operate from 1,205 1,870°C (2,200 3,400°F) This ultralow silica content refractory will minimize or eliminate the contamination and degradation that results from the reduction and reoxidation of silica, soda and potassium found in many refractory 2022年12月12日 Results revealed a 26% increase in average temperature to 1478K across the furnace for hydrogen which resulted in 645% increase in maximum heat flux into the slabs Similar flue gas flow patterns were seen for both cases and heat transfer mode from the combustion gases to the slabs was primarily by radiation (~97%) for both methane and CHARACTERISTICS OF HYDROGEN FUEL COMBUSTION IN A REHEATING FURNACEThe ascast Ti10V77Cr6Fe6Zr alloy was heattreated at 1373 K for 8 h or 1523 K for 5 min and then quenched in water The influence of heat treatment on the microstructure and hydrogen storage Influence of heat treatment on the microstructure and hydrogen 2024年5月20日 After hydrogen charging, the samples were annealed at 600 °C for 1 h then followed by a slow furnace cooling to RT in high vacuum to homogenize the hydrogen distribution and to form hydrides The hydrogen concentration of the test specimens, including the asreceived, 10 min and 30 min hydrogencharged pure Zr samples, was determined by the Annealing cracking in Zr and a Zralloy with low hydrogen
.jpg)
The effect of hydrogen treatment on microstructures evolution
2022年1月15日 In all heat treatment tests, the samples were sealed with quartz tubes to prevent hydrogen escaping during the heat treatment All samples were vacuum dehydrogenated in a tubular hydrogen treatment furnace for 2 h at 700 °C with details summarized in Table 2 After vacuum dehydrogenation treatment, the residual hydrogen was less than 20 ppm2023年6月12日 In the context of reducing greenhouse gas emissions and achieving carbon neutrality, the steel industry is rapidly developing towards a lowcarbon hydrogen metallurgy path, and the hydrogenbased shaft furnace direct reduction route, which has lower CO2 emissions compared to the conventional blast furnace route, is now receiving widespread attention This Optimization of HydrogenBased Shaft Furnace Raw Material 2017年8月4日 Table 1 is the nominal chemical composition of the ascast ZTC4 alloy (the original material for the THT treatment) After a hightemperature static gas treatment (HSGT) of the ascast material, cylindrical specimens of 8 mm in diameter and 5 mm in height were machined from the bulk materialThen the THT treatment was performed on these samples, as Thermo hydrogen treatment for microstructure refinement 2021年4月18日 The global warming promotes the steel industry to replace part of coke by injecting hydrogenrich fuel into the blast furnace to reduce CO2 emissions and energy consumptionReview of hydrogenrich ironmaking technology in blast furnace
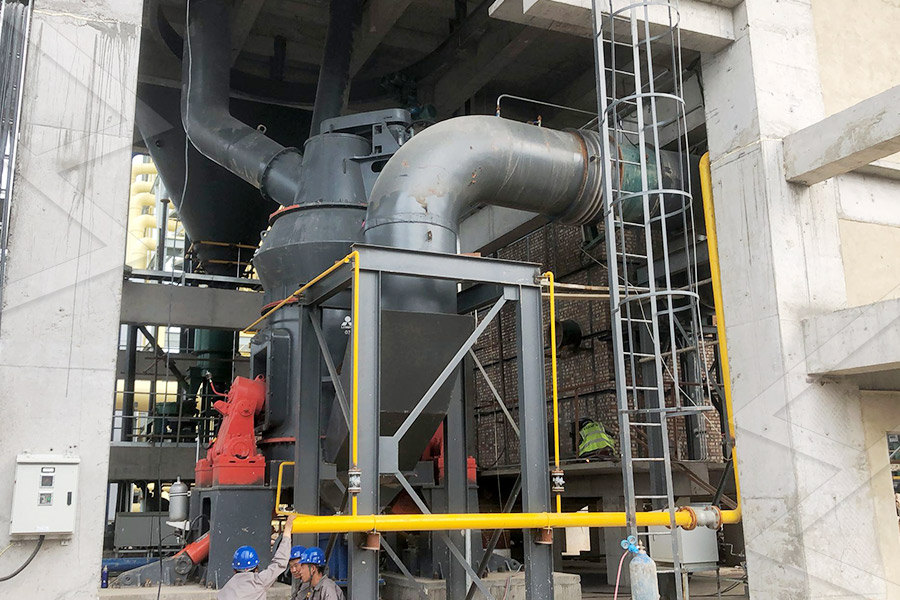
A review on the fundamentals of hydrogenbased reduction and recycling
2021年9月8日 Right now, the steel industry causes 72% of the total anthropogenic carbon dioxide emissions The total steel demand is forecasted to increase by onethird until 2050, leading to a further increase in carbon dioxide emissions [3]The higher scrap availability results in more steel production via the Electric Arc Furnace route forecasted to more than double from 2020年6月10日 Hydrogen metallurgy is a technology that applies hydrogen instead of carbon as a reduction agent to reduce CO2 emission, and the use of hydrogen is beneficial to promoting the sustainable development of the steel industry Hydrogen metallurgy has numerous applications, such as H2 reduction ironmaking in Japan, ULCORED and hydrogenbased steelmaking in Development and progress on hydrogen metallurgy2023年3月27日 The isothermal constant strain rate compression test of Ti6Al4V alloy with a hydrogen content of 031 wt% was carried out on a Gleeble1500 thermomechanical simulator The thermal deformation behavior at temperatures of 700950 °C and strain rates of 000110 s−1 was studied The results show that the flow stress of the alloy is sensitive to the deformation Deformation Characteristics and Microstructure Evolution of 2021年6月15日 Among all presented methods, only the electrochemical waterfeed processes are free from byproducts like CO2, CO, CH4 and C [19] if the electricity is provided by renewable sourcesAt the moment, 96% of all hydrogen is produced from fossil fuels and only 4% by electrolysis [20, 21]For industrial combustion application, the power to gas (P2G) route, based Assessment of natural gas/hydrogen blends as an alternative
.jpg)
HydrogenBased Reduction Technologies in LowCarbon
2023年12月11日 The traditional ironmaking technologies (including coking, sintering, pelletizing, and BF ironmaking process) are carbonintensive, which makes the industry a significant contributor to global CO2 emissions Hydrogen replacement of carbon in steelmaking processes is a sustainable way to reduce CO2 emissions First, the reduction thermodynamics and 2016年11月10日 In the gravimetric measurements made using the high pressure furnace, the TiVZrNbHf sample absorbed hydrogen easily above 200 °C This was observed as a decrease in the hydrogen pressure in the Superior hydrogen storage in high entropy alloys