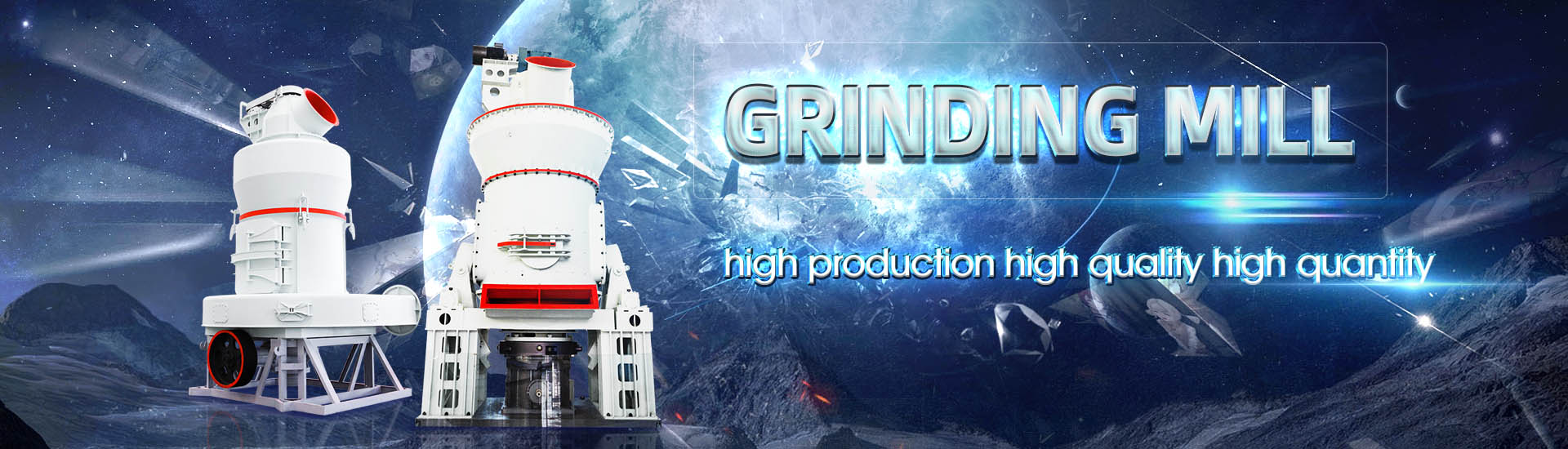
Ultrasonic ore mill for mining
.jpg)
Ultrasonic Waves in Mining Application IntechOpen
2018年9月25日 Some methods had been developed to measure rock diggability, stress distribution near a mine opening, bench blasting efficiency due to structural identification of 2015年1月1日 This chapter deals with the application of power ultrasound in the mining industry The uses of power ultrasound are addressed in three aspects: (1) determination of the stress The use of power ultrasound in mining ScienceDirect2016年10月3日 water jet ultrasound scanning system for condition monitoring of the shell of a rotating mining mill The practical requirements of such a system were first analyzed, which Mining Mill Condition Monitoring Using Water Jet 2015年12月31日 The uses of power ultrasound are addressed in three aspects: (1) determination of the stress state of rock mass for safety reasons and to plan mining work; (2) The use of power ultrasound in mining Request PDF
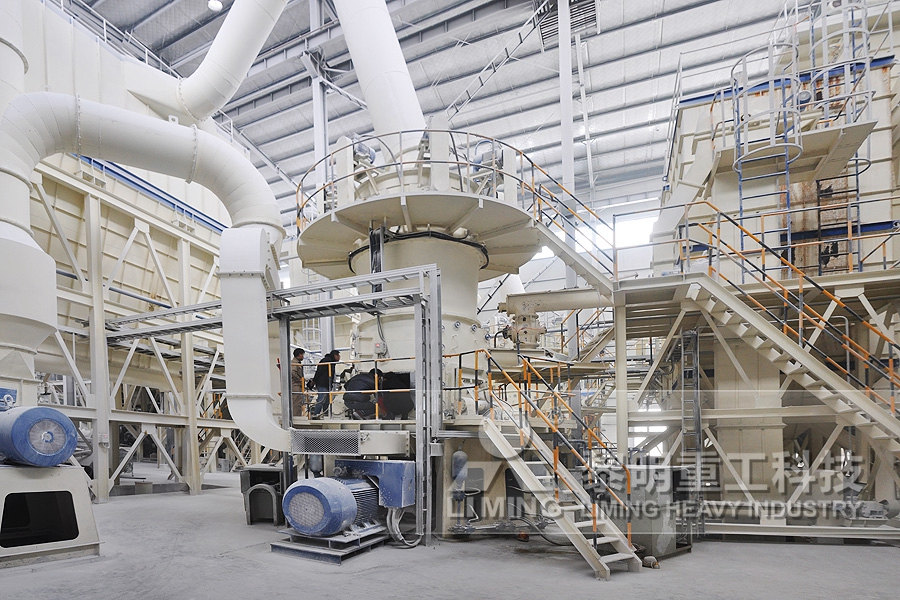
Development and Field Application of Ultrasonic Scanner for Coal Mine
This paper develops the project's ultrasonic excitation module, ultrasonic echo acceptance module, data storage module, and upper computer communication module, and designs and 2023年2月2日 The OPUS ultrasonic extinction system from Sympatec monitors the particle size distribution as well as the solid concentration in opaque and highly concentrated ore and Ultrasonic extinction for full concentration, real time 2014年1月1日 The research aims to improve indicators of mined ore mass extraction when mining rich iron ores through studying and optimizing consumption of explosives, enhancing Ultrasonic facilities for the ground materials characteristics 1993年6月1日 This paper presents grinding results obtained with a Chilean porphyry copper ore in the ultrasonic nip roll grinder of the US Comminution Center Comparison with ball milling is Exploring the ultrasonic comminution of copper ores
.jpg)
Ultrasonic facilities complex for grinding and ore
The principal results of the technical facilities complex creating for ultrasonic control of the ground (milled) materials characteristics and adaptive systems for grinding (milling) and ore 2020年5月9日 The microwave pretreatment results showed positive improvements at pilot scale mining applications in 2017 The results of ore pretreatment using electric and ultrasonic methods showed up to 24% and Methods of Ore Pretreatment for Comminution 2023年7月22日 Ore fine crushing is a process of crushing ore blocks with a feeding particle size of 50–150 mm to 5–25 mm, and the maximum crushing ratio of fine crushing is about five The main equipment suitable for fine crushing operations includes a fine crushing jaw crusher, short head cone crusher, highpressure roller mill, etc Ore superfine crushingOre Crushing SpringerLink2023年6月17日 The aim of a mineral processing operation is to concentrate a raw ore for the subsequent mineral extraction stage Usually, the valuable minerals are first liberated from the ore matrix by comminution and size separation processes (crushing, grinding, and size classification) and then separated from the gangue using processes capable of selecting the particles Automation and Robotics in Mining and Mineral Processing

Mining Mineral Level Sensors Hawk Measurement
Hawk Measurement Systems (HAWK) awardwinning mineral measurement systems, technologies, and complete mining industrylevel measurement products help the mining industry to increase profitability and decrease downtimeThe mining industry presents unique challenges due to dust, mud, impact, abrasion, and buildup of material on sensors and plants, which magnetic separator using ultrasonic methods, developing and substantiating methods to enhance efficiency of iron ore magnetic separation by applying ultrasonic technologies 1 Introduction Sustainable industrial development calls for solving the topical problem of reducing costs and energyintensity of iron ore mining and processing [15]Increasing efficiency of iron ore magnetic separation by 2016年2月1日 The purpose of this study is to understand how ore loss and dilution affect the mine call factor, with the aim of subsequently improving the quality of ore mined and fed to the millMonitoring ore loss and dilution for minetomill integration 2016年10月3日 volved in constructing an ultrasonic inspection system suitable for condition monitoring of a fullscale mining mill If amplitudes of reflected ultrasound waves are to be used to image the interior of the mill shell, the maximum achievable spatial resolution of this image (ie the Cscan) is limitedMining Mill Condition Monitoring Using Water Jet
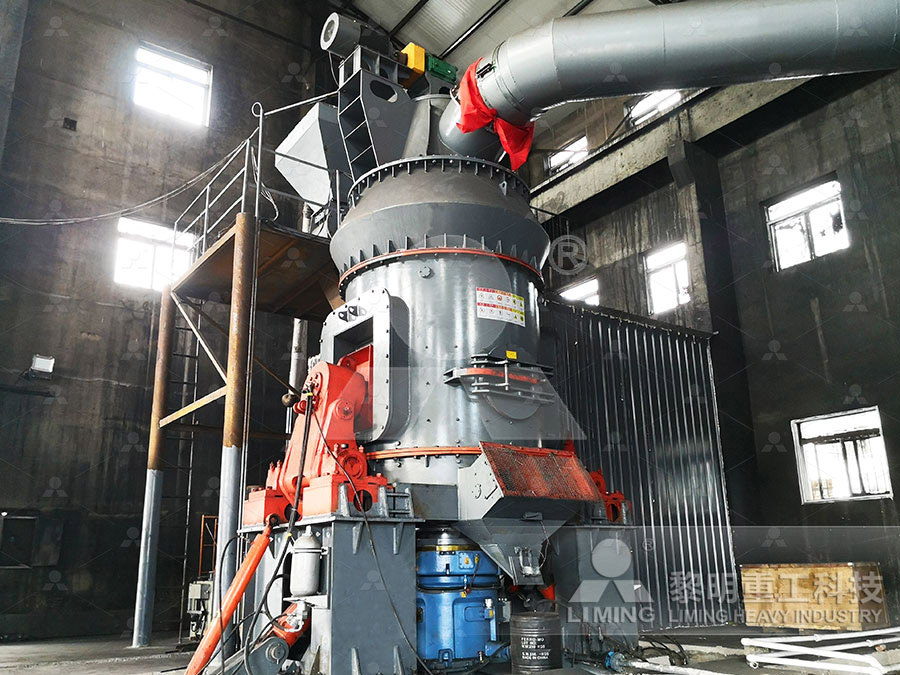
Vortex Air Mill flexicone
Portable mill, best for field tests, prospectors, laboratory tests, smallscale mining projects, processing of black sand to recover encapsulated gold and precious metals 5 We recommend using a Vortex mill with Flexicone centrifugal concentrators for maximum metal recovery In addition, due to the formation of the Ultrasound waves field 2016年9月29日 toring of the lining of mining mills during operation is to be investigated The proposed waterflow ultrasonic technique uses a water beam to transmit the ultrasound to the mill shell and lining By measuring the time of flight (TOF), it can be possible to monitor the thickness of mill linings, without the need of interrupting operation The Ultrasonics for Monitoring of Mining Mill Linings DiVA2017年3月4日 Cemented paste backfill (CPB) is an engineered mixture of fine process tailings (75–85% solids by weight), a hydraulic binder (3–9% by total dry paste weight) and mixing water for a solid density of 70–80% by weight (Fig 23)The addition of a binder is essential for the strength and stability of CPBPractical Importance of Tailings for Cemented Paste BackfillKeywords: Mine call factor, minetomill integration, fragmentation, ore loss, dilution Introduction The mining of high gold grades is obviously very beneficial for the economic viability of an operation, but optimum recovery of the product Monitoring ore loss and dilution for minetomill
.jpg)
Boltstress Mining Technology
The foundation of its knowledge base has been built by measuring the actual bolt tension (not torque) achieved by any tightening method The two key factors are ultrasonic bolt tension measurement, and joint analysis and management In 2024年7月24日 3 Comminution Characterisation Rock breakage characteristics are determined by using a dropweight device This is used to break rocks in a range of sizes under a range ofModelling and Simulation Techniques Applied for 1993年6月1日 This paper presents grinding results obtained with a Chilean porphyry copper ore in the ultrasonic nip roll grinder of the US Comminution Center Comparison with ball milling is performed by scalingdown industrial ball mill behavior to the ultrasonic grinding conditions For small gap setting in the ultrasonic device, size distribution and Exploring the ultrasonic comminution of copper oresCoal mining processing plant in Nigeria This coal mining project is an open pit mine located in Nigeria, announced by mining company Western Goldfields that it has discovered 62,400,000 tonnes of proven reserves of coal deposits worth US$12 billion which could be used for the generation of electric powerultrasonic grinding mill rock china
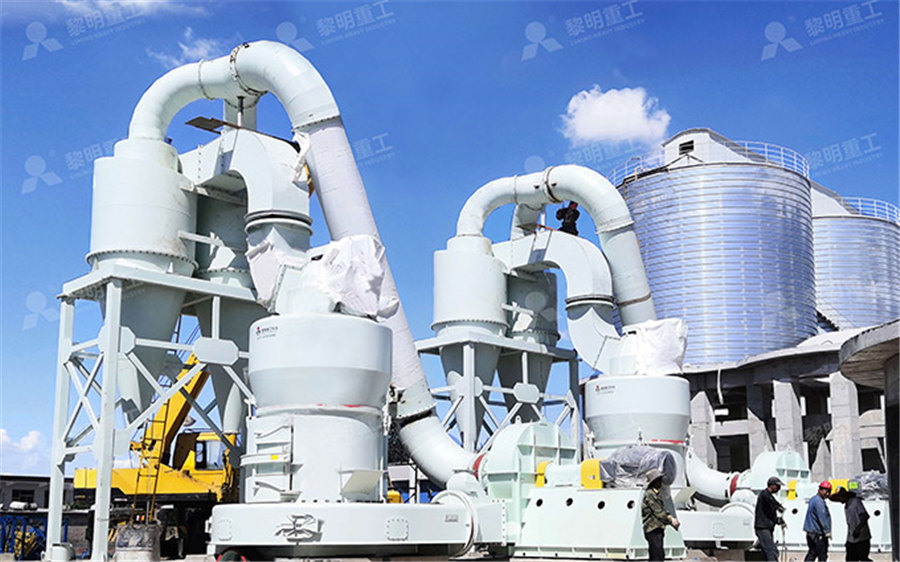
(PDF) Feasibility and necessity of mine to mill ResearchGate
2021年4月19日 Published in MATERIA 2021;23:6366 The idea of minetomill optimization has been tested in various mines in last decades, resulting in higher mill throughput in many mines, but also 2024年6月14日 Boltstress Ultrasonics, the world’s leading provider of ultrasonic bolting solutions, proudly announces its unparalleled expertise and dedication to the mining industry With over three decades of experience, BoltStress has established itself as the goto partner for businesses seeking the most advanced and reliable bolting technologiesSetting the Standard in Ultrasonic Bolting Solutions2016年4月29日 control of ore beneficiation technological processes under parametric uncertainty, Metallurgical and Mining Industry, No 5, pp 711 10 Golik V, Komashchenko V, Morkun V (2015) Feasibility of using the mill tailings for preparation of selfhardening mixtures Metallurgical and Mining Industry, No3, pp 3841Ultrasonic testing of the crushed ore particle size 2024年10月13日 Grinding mills operate on the principle of breaking down ore particles into smaller sizes through the action of abrasion The primary types of grinding mills include ball mills, rod mills, autogenous mills, and semiautogenous mills Each mill type has a distinct working mechanism, but they all share common principles of crushing and grindingUnderstanding the operation of grinding mills in the mining
.jpg)
Reducing operating costs by monitoring chute liner wear in
Variability in ore type and changes in liner materials can impact the wear rates experienced by the liners used to protect the inner walls of transfer and feed chutes This variability can lead to increased operational costs due to unplanned maintenance which may be required to replace highly worn liners2016年9月29日 toring of the lining of mining mills during operation is to be investigated The proposed waterflow ultrasonic technique uses a water beam to transmit the ultrasound to the mill shell and lining By measuring the time of flight (TOF), it can be possible to monitor the thickness of mill linings, without the need of interrupting operation The Ultrasonics for Monitoring of Mining Mill Linings DiVA Our Metso Premier™ mills and Select™ mills are supported by our comprehensive services network to ensure optimization during your mills lifetime Also the Premier™ mills and Select™ mills come ready to be easily integrated Grinding mills for mining and minerals 2024年7月2日 removed from the surface of the ore particles of the pulp; with minimal grinding of the ore particles, radiation intensity is 21 W/cm2, the process duration is from 15 minutes, the reduction in the control class –01 mm was 122% Key words: ultrasonic treatment, ore pulp, laboratory installation, ultrasonic technological apparatus, oxide films,Investigation of oxide films removal process from the
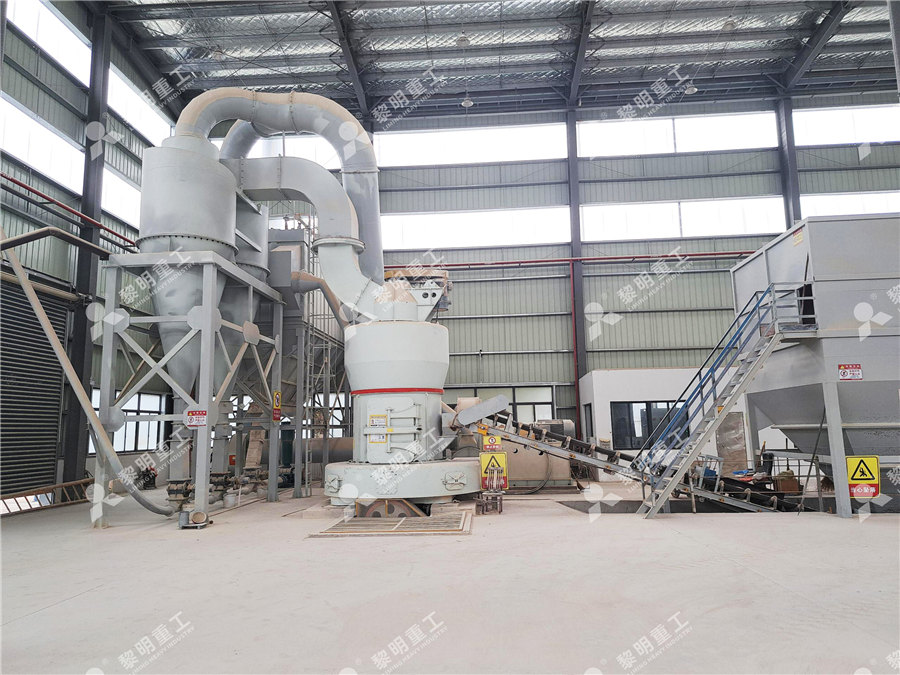
Vortex Air Mill Ore Grinding Ore Grinding Gold Refining
2023年9月26日 Never heard of the term "air mill" Do you mean a rotary impact mill? I have heard of mills which use air for concentrating, but an air mill for grinding, kind of goes against the laws of physics Air will break down silicious ores, just probably take a lot longer than say a ball mill, by maybe a few thousand years or more2017年10月25日 The ultrasonic treatment unit consists of an inclined, flat bottomed metal trough, usually made of stainless steel or aluminum, with the ultrasonic transducer attached near the upper end A typical unit would be 915 cm (36 inches) wide and 244 cm (96 inches) long Figure 1 is a photograph of an ultrasonic treatment unit being water testedUltrasonic Mineral Recovery 911Metallurgist2015年3月1日 Measurement of the liner wear in the mill of an ore dressing plant is one of the critical parameters in the context of mill downtime and production performanceCondition monitoring of cracks and wear in mining mills 2024年2月27日 A subject of particular importance to the hard rock mining industry concerns the safe and efficient size reduction of the runofmine ore materials through grinding A grinding mill, semiautogenous (SAG) or autogenous (AG), is one of the most critical ore processing plants in the entire mineral processing circuit Development of a Wear Sensor for Monitoring Grinding Mill
.jpg)
Planning an Iron Ore Mine: From Exploration Data to Informed Mining
2013年1月1日 An iron ore mining company, operating in Western Australia, trucks ore from three geographically isolated sources to a crusher, where it is blended before and during crushing The company prides Based on the model of mining and processing equipment, the design, putting into production, joint tests of lining with the customer are carried out Warranty is provided Generic Lining Products Overall wearresistant plates Used for cladding large areas of the mill They can also be used to protect the surface of ore passes, trolleys and dump Rubber Lining for Ore Grinding Mills and Mining and Processing 2023年12月1日 The SAG Mill is to reduce the size of the big ore into small size On the other hand, ball mill converts small ore into more refined grains After leaving the SAG mill, the ore goes through a screening process before proceeding to the ball mill A ball mill is essential in the mining process to grind the small ore to fine sandPredictive maintenance on ball mill liner using 3D scanner 2020年5月9日 The microwave pretreatment results showed positive improvements at pilot scale mining applications in 2017 The results of ore pretreatment using electric and ultrasonic methods showed up to 24% and Methods of Ore Pretreatment for Comminution
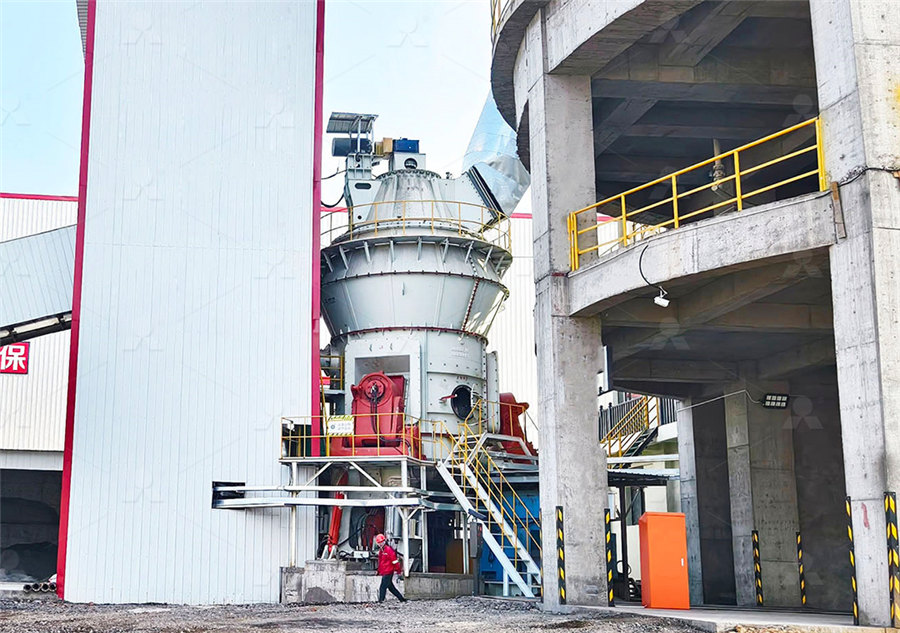
Ore Crushing SpringerLink
2023年7月22日 Ore fine crushing is a process of crushing ore blocks with a feeding particle size of 50–150 mm to 5–25 mm, and the maximum crushing ratio of fine crushing is about five The main equipment suitable for fine crushing operations includes a fine crushing jaw crusher, short head cone crusher, highpressure roller mill, etc Ore superfine crushing2023年6月17日 The aim of a mineral processing operation is to concentrate a raw ore for the subsequent mineral extraction stage Usually, the valuable minerals are first liberated from the ore matrix by comminution and size separation processes (crushing, grinding, and size classification) and then separated from the gangue using processes capable of selecting the particles Automation and Robotics in Mining and Mineral ProcessingHawk Measurement Systems (HAWK) awardwinning mineral measurement systems, technologies, and complete mining industrylevel measurement products help the mining industry to increase profitability and decrease downtimeThe mining industry presents unique challenges due to dust, mud, impact, abrasion, and buildup of material on sensors and plants, which Mining Mineral Level Sensors Hawk Measurementmagnetic separator using ultrasonic methods, developing and substantiating methods to enhance efficiency of iron ore magnetic separation by applying ultrasonic technologies 1 Introduction Sustainable industrial development calls for solving the topical problem of reducing costs and energyintensity of iron ore mining and processing [15]Increasing efficiency of iron ore magnetic separation by
.jpg)
Monitoring ore loss and dilution for minetomill integration
2016年2月1日 The purpose of this study is to understand how ore loss and dilution affect the mine call factor, with the aim of subsequently improving the quality of ore mined and fed to the mill2016年10月3日 volved in constructing an ultrasonic inspection system suitable for condition monitoring of a fullscale mining mill If amplitudes of reflected ultrasound waves are to be used to image the interior of the mill shell, the maximum achievable spatial resolution of this image (ie the Cscan) is limitedMining Mill Condition Monitoring Using Water Jet Portable mill, best for field tests, prospectors, laboratory tests, smallscale mining projects, processing of black sand to recover encapsulated gold and precious metals 5 We recommend using a Vortex mill with Flexicone centrifugal concentrators for maximum metal recovery In addition, due to the formation of the Ultrasound waves field Vortex Air Mill flexicone2016年9月29日 toring of the lining of mining mills during operation is to be investigated The proposed waterflow ultrasonic technique uses a water beam to transmit the ultrasound to the mill shell and lining By measuring the time of flight (TOF), it can be possible to monitor the thickness of mill linings, without the need of interrupting operation The Ultrasonics for Monitoring of Mining Mill Linings DiVA
.jpg)
Practical Importance of Tailings for Cemented Paste Backfill
2017年3月4日 Cemented paste backfill (CPB) is an engineered mixture of fine process tailings (75–85% solids by weight), a hydraulic binder (3–9% by total dry paste weight) and mixing water for a solid density of 70–80% by weight (Fig 23)The addition of a binder is essential for the strength and stability of CPB