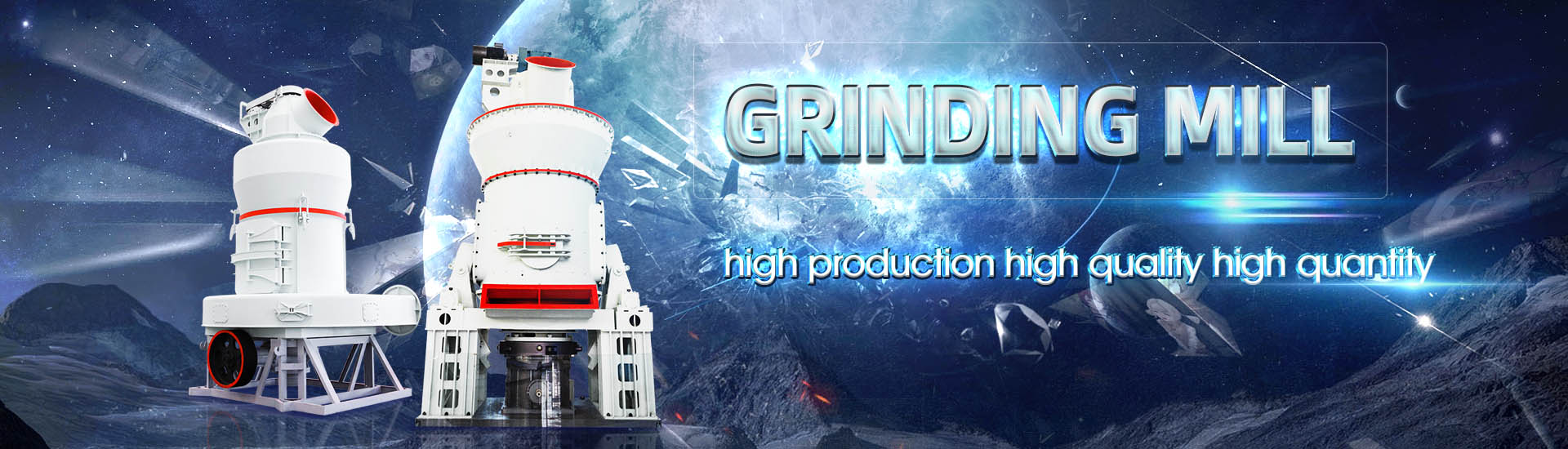
Coal mill takes root
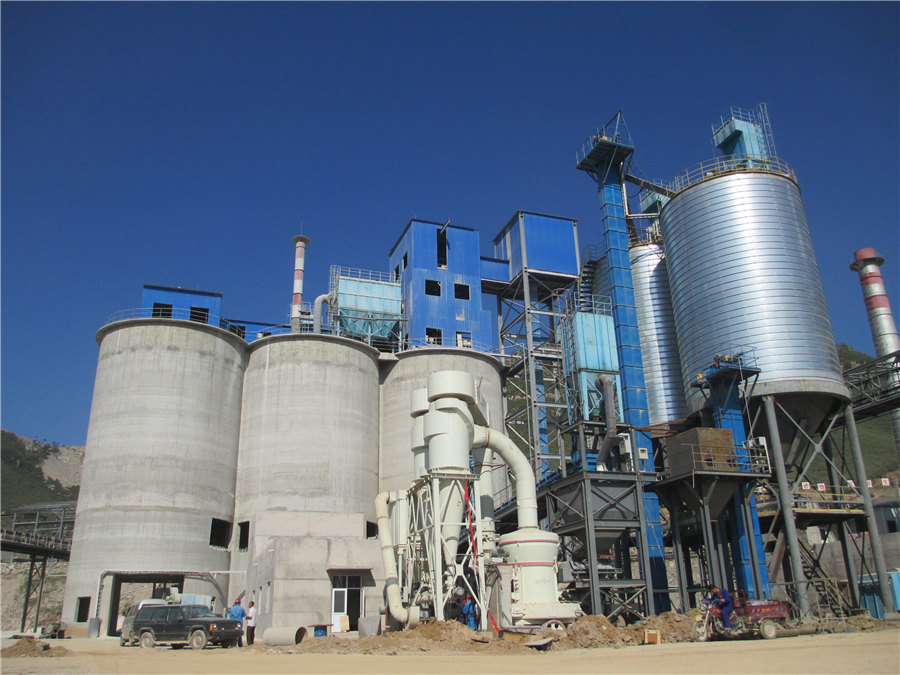
Intelligent Decision Support System for Detection and Root
2016年7月7日 Fuzzy logic is employed for residual evaluation to determine the type and magnitude of the fault, while Bayesian network is used for troubleshooting the root cause The proposed technique is validated using historical data of coal mills obtained from an actual coal 2016年7月7日 Coal mill is an essential component of a coal fired power plant that affects the performance, reliability and downtime of the plant The availability of the milling system is Intelligent Decision Support System for Detection and Root Mills are mechanical devices used to break different types of solid materials in small pieces by grinding, crushing or cutting In pulverised coalfired power plants, a pulveriser coal mill grinds Coal Mill an overview ScienceDirect Topics2022年5月31日 Coal mills is main equipment of pulverizing system, and its main function is to smash coal briquette sent into coal mills, make coal briquette ground into coal power and dry A brannew performance evaluation model of coal mill
.jpg)
Dual fault warning method for coal mill based on
2024年5月1日 To avoid abnormal operating conditions of coal mills in time and effectively, a dual fault warning method for coal mill is proposed Three typical faults of coal mill plugging, coal Coal mill is an essential component of a coalfired power plant that affects the performance, reliability, and downtime of the plant The availability of the milling system is influenced by poor Intelligent Decision Support System for Detection and Root Simulation results can accurately reveal the actual coal mill operating conditions and monitor the effect of changes in operation patterns For the failure diagnostic, the ANFIS method is utilized Decision Support System for Coal Mill Fault Diagnosis in 2023年2月7日 Abstract— Coal pulverizer mill at PLTU Rembang is the main equipment in the boiler that supports the reliability of the generating unit They serve to supply coal fuel in the International Journal of Scientific Engineering
.jpg)
Review of control and fault diagnosis methods applied to coal mills
2015年8月1日 As the significant ancillary equipment of coalfired power plants, coal mills are the key to ensuring the steady operation of boilers In this study, a fault diagnosis model was 2012年5月1日 Coal mill models can trace their roots back to the early 1940s where several groups of researchers worked on the mathematical modeling of mills and the development of Derivation and validation of a coal mill model for control2023年2月7日 failure and provide information for monitoring coal mill operations It can help the plant operators in preventing a derating or trip unit 5 OPERATION PATTERN TO AVOID FAULTS IN COAL MILL To avoid the failure of the coal mill, a change in the operating pattern is carried out from the recommended root causes andInternational Journal of Scientific Engineering tion and root cause analysis in coal mills generated residuals [8] However, measuring several parameters included in the mechanism model proved to be challenging at the production site Early Warning of Critical Blockage in Coal Mills Based on
.jpg)
Root Cause Failure Analysis of Coal Mill Vertical Shaft
2016年9月30日 A root cause failure analysis of coal mill vertical shaft used in thermal power plant has been carried out The failed parts of the shaft showed the signature of fatigue failures The fatigue cracks originated from the top edge of the keyway area, where the bowl is assembled Operating conditions, material of the shaft and2021年8月1日 Yukio et al [7] proposed a model consisting of blending, grinding and classifying processes for pulverizer control Agarawal et al [8] differentiated coal powder into ten size groups, divided the bowl mill into four zones, and developed a unified model Palizban et al [9] derived nonlinear differential mass equations of raw coal, recirculation coal and suspension coal in Coal mill model considering heat transfer effect on mass 2010年6月22日 A root cause failure analysis of coal mill vertical shaft used in thermal power plant has been carried out The failed parts of the shaft showed the signature of fatigue failuresRoot cause failure analysis of coal mill vertical shaft2021年1月28日 A Novel MultiMode Bayesian Method for the Process Monitoring and Fault Diagnosis of Coal Mills January 2021; IEEE Access PP Declare fault of the monitor ed sample and perform root cause A Novel MultiMode Bayesian Method for the Process
.jpg)
Review of control and fault diagnosis methods applied to coal mills
DOI: 101016/JJPROCONT201504006 Corpus ID: ; Review of control and fault diagnosis methods applied to coal mills @article{Agrawal2015ReviewOC, title={Review of control and fault diagnosis methods applied to coal mills}, author={Vedika Agrawal and Bijaya Ketan Panigrahi and P M V Subbarao}, journal={Journal of Process Control}, year={2015}, A root cause failure analysis of coal mill vertical shaft used in thermal power plant has been carried out The failed parts of the shaft showed the signature of fatigue failures The fatigue cracksRoot Cause Failure Analysis of Coal Mill Vertical Shaft3 天之前 2 The hot air is used for transportation of the recirculating coal within the mill and also for transporting the coal from the pulverizer to the furnace As the coal is continuously reduced in size, the smaller/lighter particles are swept from the bowl by the hot air Hot air (and cool tempering air) is provided by the primary air fansBowl Mill Coal Pulverizer COAL HANDLING PLANTS2020年1月1日 Coal mills have a significant influence on the reliability, efficiency, and safe operation of a coalfired power plant Coal blockage is one of the main reasons for coal mill malfunctionEarly Warning of Critical Blockage in Coal Mills Based on
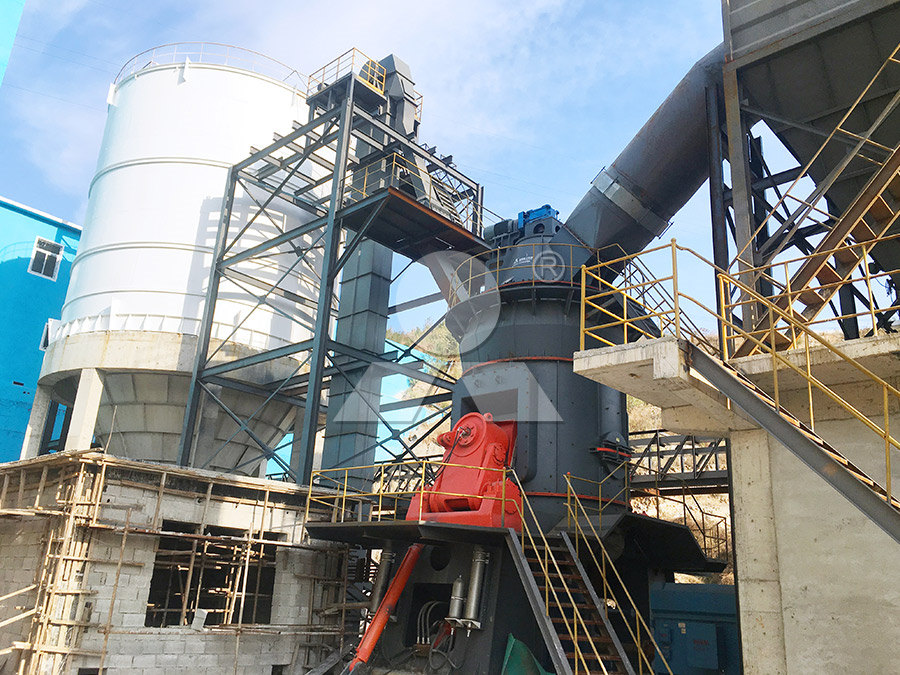
Coal pulverizer mill system modeling for failure simulation
2023年5月8日 The coal pulverizer mills at the coalfired power station PLTU Rembang are the main equipment in the boiler that supports the reliability of the generating unit Intelligent decision support system for detection and root cause analysis of faults in coal mills,”2024年11月14日 The ATOX mill will grind and dry coal containing more than 20% moisture in one operation The possibility of customersupplied parts, along with the low civil costs that accompany compact mill installation, add to the excellent economy of the ATOX coal mill Working principles The raw coal enters the mill via a rotary sluice and feed chuteATOX COAL MILL flsmidthcement2020年8月12日 Vertical Coal Mill (VCM) is equipment for grinding and pulverizing coal into micron size Rotary kilns then use the powders as fuel burners The VCM has a housing section equipped with a lining An investigation of performance characteristics 2021年3月12日 4 Rating of MPS mills for coal grinding The most reliable and comprehensive basis for layout and design is provided by pilotscale grinding tests of the projectrelevant materials At the GPSE test station, extensive test series with the semiindustrial mill type MPS 40 B (refer to Figure 3) are conducted for the grinding of different solid MPS mills for coal grinding AYS Engineering
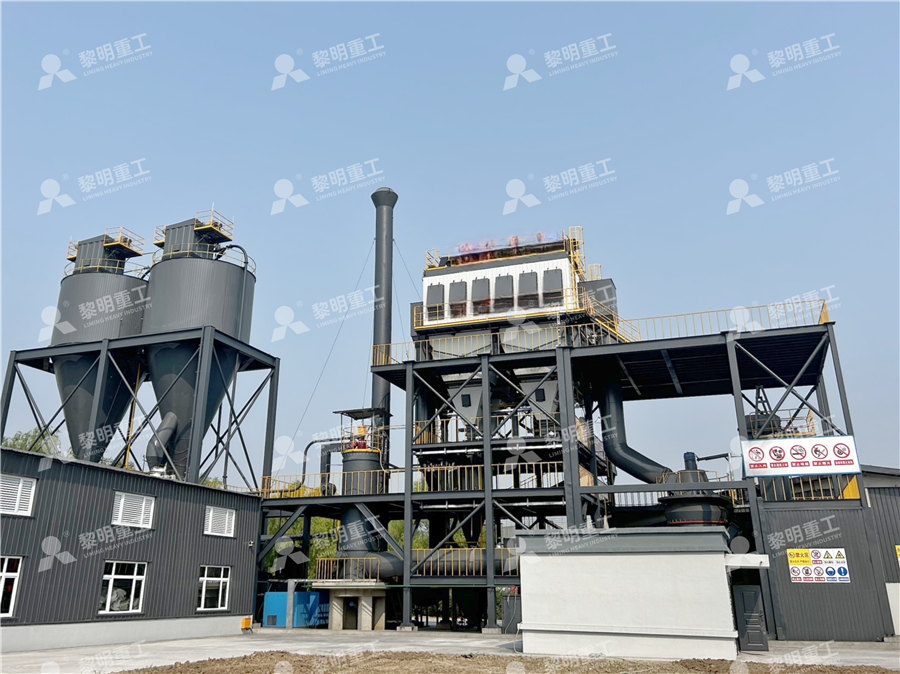
Fault analysis and optimization technology of HP bowl type
2021年8月1日 A root cause failure analysis of coal mill vertical shaft used in thermal power plant has been carried out The failed parts of the shaft showed the signature of fatigue failures2022年7月7日 Coal Mills are used to pulverize and dry to coal before it is blown into the power plant furnace Operation The coal is feed into the coal mill through a central inlet pipe where gravity is used to lead the coal to the bottom of the mill, where the grinding table and some heavy rollers pulverizes the coal to particlesCoal Mills SolidsWiki2021年8月5日 In bowl mill pulveriser raw coal coming from feeder gets ground between the grinding rolls and bull ring segments installed on the revolving Bowl Bowl is made to rotate at medium speed for proper pulverization of coal Springs exert necessary pressure on rolls for grinding Hot air through the mill besides removing coal moisture, picks up the Pulveriser in Thermal Power Plant Bowl Mill Ball MillA simple energy balance model of the coal mill is derived in (Odgaard and Mataji 2006), this model is based on a more detailed model found in (Rees and Fan 2003)In this model the coal mill is seen as one body with the mass m mThe following variables are defined: T(t) is the temperature in the coal dust flow in the mill, ṁ PA (t) is the primary air mass flow, T PA (t) is Coal Mill an overview ScienceDirect Topics
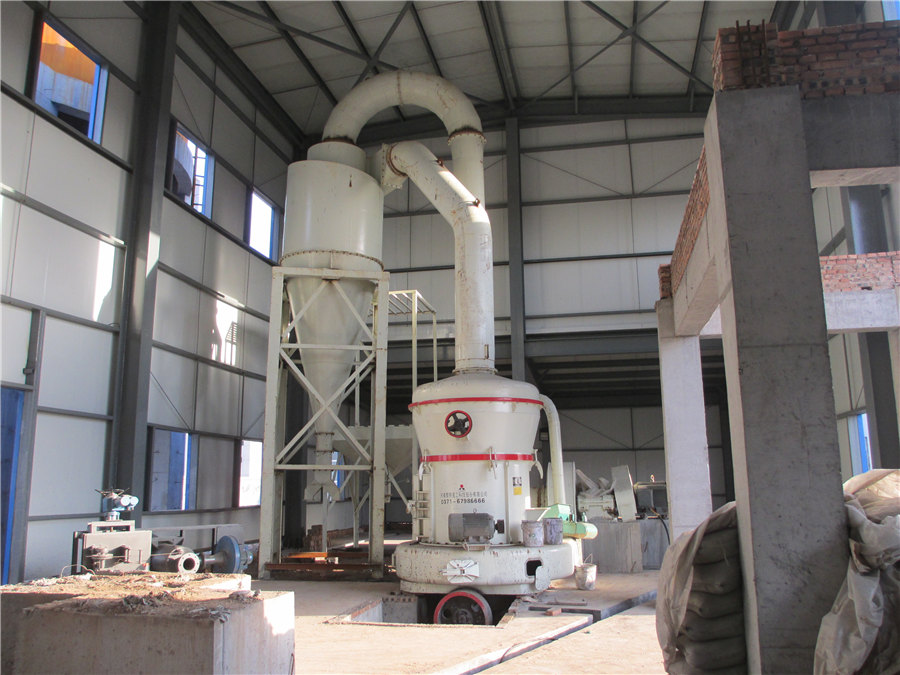
A novel multimode Bayesian method for the process
2023年10月20日 In most modern coalfired power plants, medium speed coal mills are widely equipped because of their flexibility and economic efficiency A OPERATION OF COAL MILLS The work in this part is based 2023年10月30日 an intelligent decision support system for coal mills to conduct a root cause analysis of faults Andrade et al [13] proposed a hybrid framework for automated fault detection and1, Leyuan Liu 1,* , Xiaoyun Kang 1 and Fuli Wang 1,22013年11月20日 Abstract: The paper presents development and validation of coal mill model (including the action of classifier) to be used for improved coal mill control The model is developed by using the mass and heat balance equations of the coal mill Genetic Algorithm is used to estimate the unknown parameters that are used in the model validationModeling and Control of Coal Mill NTNU2024年9月4日 Frequent load changes put tremendous pressure on the generating units and their auxiliary machines, such as coal mills Coal mills operate for a long time under the harsh environment of high temperature, high intensity and variable operating conditions, and are prone to failure As a key auxiliary machine of thermal power units, the operating A Fault Early Warning Method for Coal Mills Based on
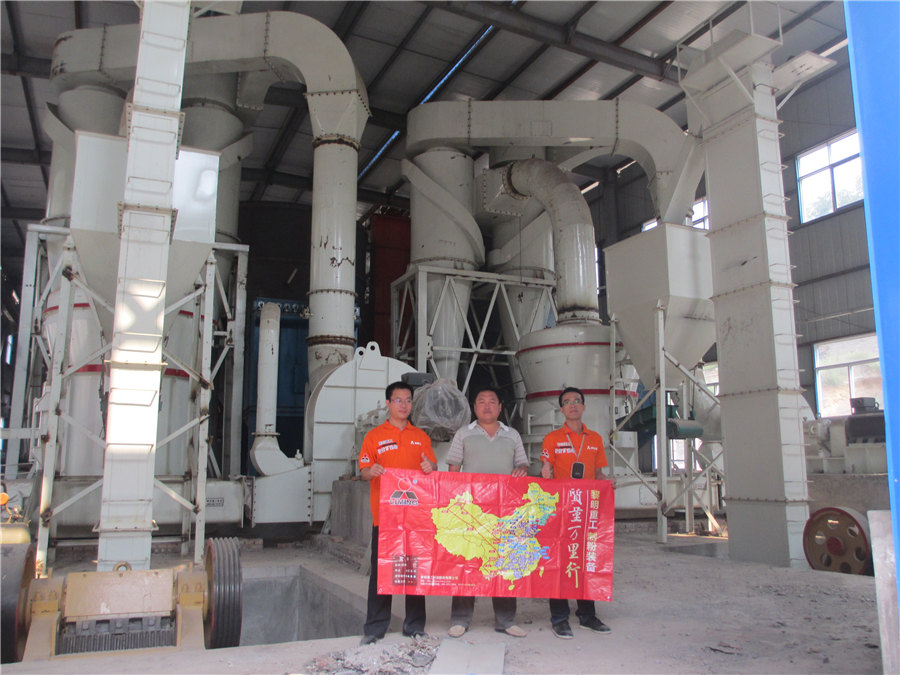
Derivation and validation of a coal mill model for control
2012年5月1日 Coal fired power plants are heavily used due to large and long lasting coal resources compared with oil or natural gas An important bottleneck in the operation of this particular kind of plants, however, is the coal pulverization process, which gives rise to slow takeup rates and frequent plant shutdowns (Rees Fan, 2003)In typical coal fired power plants, 2012年11月17日 20 131Fineness Fineness is an indicator of the quality of the pulverizer action Specifically, fineness is a measurement of the percentage of a coal sample that passes through a set of test sieves usually designated at 50, 100, and 200 mesh A 70% coal sample passing through a 200 mesh screen indicates optimum mill performance The mill wear and Coal mill pulverizer in thermal power plants PPT SlideShare2015年11月1日 As presented by Andersen et al (2009) and Odgaard, Stoustrup, and Mataji (2007), coal moisture imposes limit on the maximum load at which a coal mill can be operated and the load gradient (how fast the mill may change its operating point), if it is desired that the pulverized coal entering the furnace has moisture content less than or equal to A unified thermomechanical model for coal mill operation2024年5月1日 The coal mill is a machine that breaks and grinds coal into pulverized coal It is the core equipment of pulverizing system Coal mills are categorized according to speed as low, medium and high speed mills The low and mediumspeed coal mills are the most popular due to their economy [25] The modeling object is ZGM type mediumspeed roller Dual fault warning method for coal mill based on
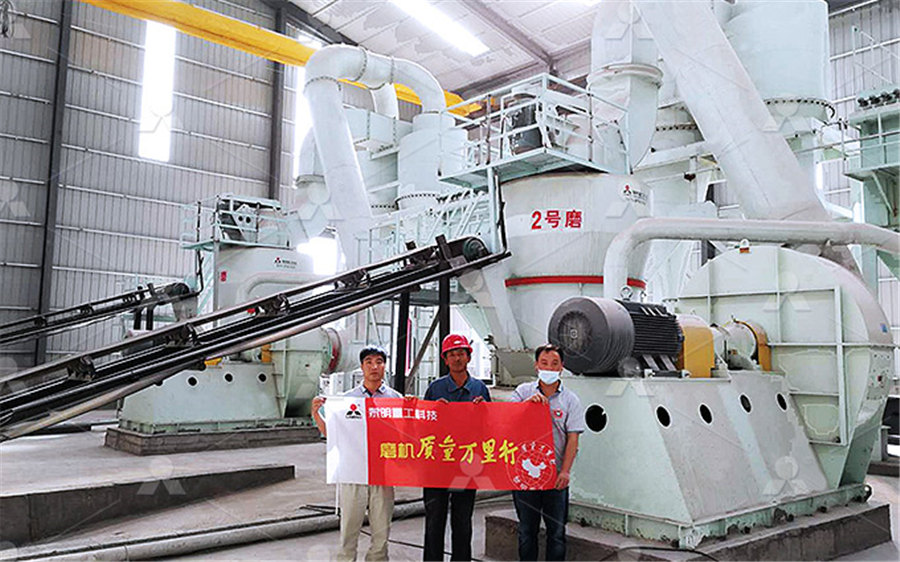
Review of control and fault diagnosis methods applied to coal mills
2015年8月1日 Mill problems originate mainly due to poor controls or faults occurring within the milling system As discussed by GQ Fan and NW Rees [3], the control of mills remains very simple in most of the power plants due to the fact that the mill system is highly nonlinear with strong coupling among the variables and it is very difficult to measure some important DOI: 101109/TFUZZ2016 Corpus ID: ; Intelligent Decision Support System for Detection and Root Cause Analysis of Faults in Coal Mills @article{Agrawal2017IntelligentDS, title={Intelligent Decision Support System for Detection and Root Cause Analysis of Faults in Coal Mills}, author={Vedika Agrawal and Bijaya Ketan Panigrahi and PMV Subbarao}, Intelligent Decision Support System for Detection and Root 2021年6月10日 in the coal mills While appropriate precautions differ at the various stages of the process, this article concentrates on appropriate detection methods for coal mills Each generating unit at Merom has three Riley Power doubleended COAL MILL Land Instruments International2020年9月1日 MPStype mediumspeed coal mill is designed and manufactured by Babcock, Germany, which is characterized by low energy consumption, long maintenance period and smooth output This paper takes the coal mill system of a 330 MW unit as the research object (Fig 1), which is equipped with an MPS180 HP II mediumspeed coal mill (Fig 2)Research on fault diagnosis of coal mill system based on the
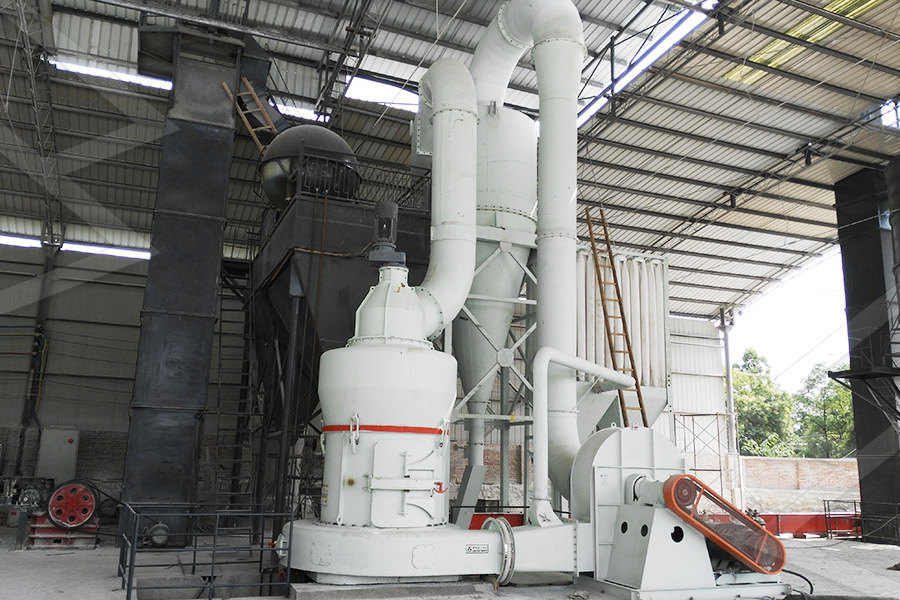
International Journal of Scientific Engineering
2023年2月7日 failure and provide information for monitoring coal mill operations It can help the plant operators in preventing a derating or trip unit 5 OPERATION PATTERN TO AVOID FAULTS IN COAL MILL To avoid the failure of the coal mill, a change in the operating pattern is carried out from the recommended root causes andtion and root cause analysis in coal mills generated residuals [8] However, measuring several parameters included in the mechanism model proved to be challenging at the production site Early Warning of Critical Blockage in Coal Mills Based on 2016年9月30日 A root cause failure analysis of coal mill vertical shaft used in thermal power plant has been carried out The failed parts of the shaft showed the signature of fatigue failures The fatigue cracks originated from the top edge of the keyway area, where the bowl is assembled Operating conditions, material of the shaft andRoot Cause Failure Analysis of Coal Mill Vertical Shaft2021年8月1日 Yukio et al [7] proposed a model consisting of blending, grinding and classifying processes for pulverizer control Agarawal et al [8] differentiated coal powder into ten size groups, divided the bowl mill into four zones, and developed a unified model Palizban et al [9] derived nonlinear differential mass equations of raw coal, recirculation coal and suspension coal in Coal mill model considering heat transfer effect on mass
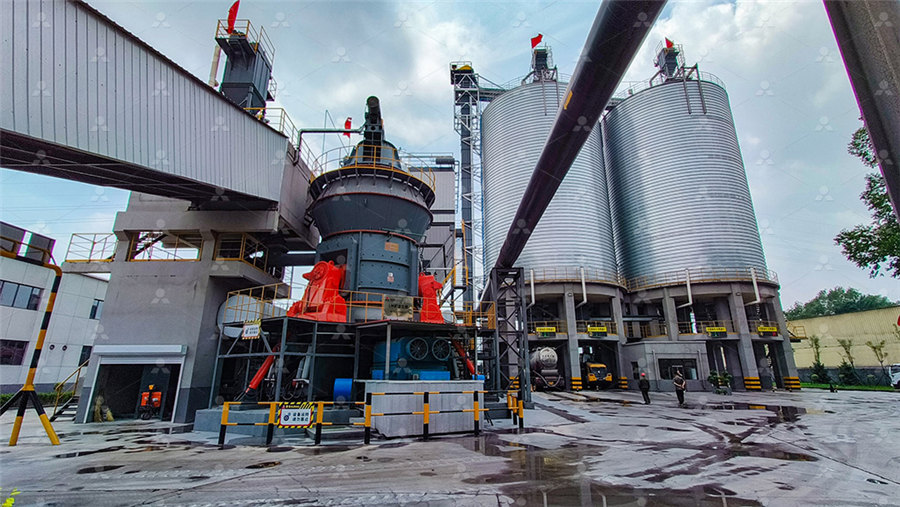
Root cause failure analysis of coal mill vertical shaft
2010年6月22日 A root cause failure analysis of coal mill vertical shaft used in thermal power plant has been carried out The failed parts of the shaft showed the signature of fatigue failures2021年1月28日 A Novel MultiMode Bayesian Method for the Process Monitoring and Fault Diagnosis of Coal Mills January 2021; IEEE Access PP Declare fault of the monitor ed sample and perform root cause A Novel MultiMode Bayesian Method for the ProcessDOI: 101016/JJPROCONT201504006 Corpus ID: ; Review of control and fault diagnosis methods applied to coal mills @article{Agrawal2015ReviewOC, title={Review of control and fault diagnosis methods applied to coal mills}, author={Vedika Agrawal and Bijaya Ketan Panigrahi and P M V Subbarao}, journal={Journal of Process Control}, year={2015}, Review of control and fault diagnosis methods applied to coal millsA root cause failure analysis of coal mill vertical shaft used in thermal power plant has been carried out The failed parts of the shaft showed the signature of fatigue failures The fatigue cracksRoot Cause Failure Analysis of Coal Mill Vertical Shaft
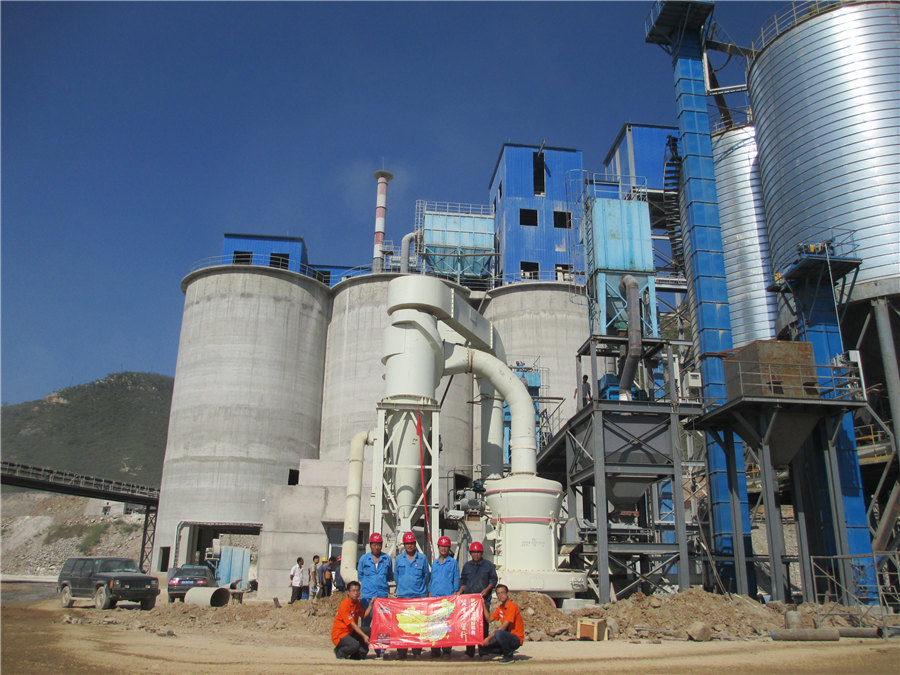
Bowl Mill Coal Pulverizer COAL HANDLING PLANTS
3 天之前 2 The hot air is used for transportation of the recirculating coal within the mill and also for transporting the coal from the pulverizer to the furnace As the coal is continuously reduced in size, the smaller/lighter particles are swept from the bowl by the hot air Hot air (and cool tempering air) is provided by the primary air fans2020年1月1日 Coal mills have a significant influence on the reliability, efficiency, and safe operation of a coalfired power plant Coal blockage is one of the main reasons for coal mill malfunctionEarly Warning of Critical Blockage in Coal Mills Based on