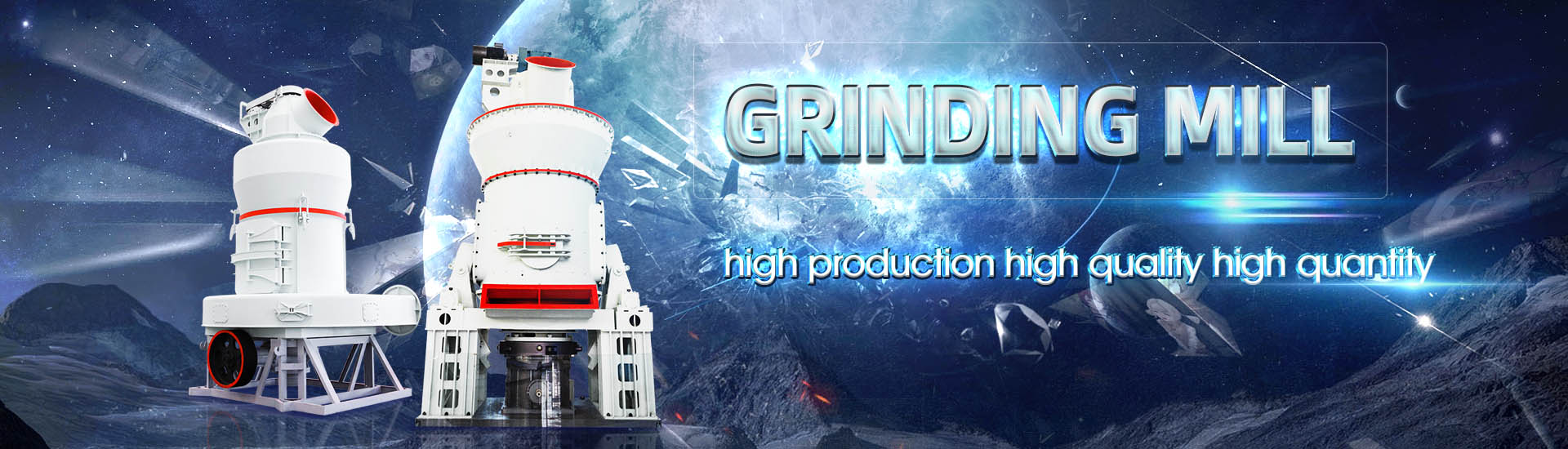
How much is an ore mill
.jpg)
Milling Cost an overview ScienceDirect Topics
Mining is a major cost, and this can vary from only a few pence per ton of ore to well over £50 t −1 Hightonnage operations are cheaper in terms of operating costs but have higher initial capital costs2024年4月26日 Iron ore, a naturally occurring mineral composed primarily of iron oxides, is mined and processed to extract iron for various industrial applications This article provides a comprehensive overview of the iron ore Iron Ore Processing: From Extraction to 2016年3月21日 Example: A mill in closed circuit with a classifier receives 300 dry tons of crude ore per day, and the percentages of solid are respectively 25, 50, and 84% in the classifier overflow, feed to classifier, and sand, equivalent Common Basic Formulas for Mineral 2022年4月25日 The quantity of ore mined and waste rock (ie, overburden or barren rock) removed to produce a refined unit of a mineral commodity, its rocktometal ratio (RMR), is an important metric for undersRocktoMetal Ratio: A Foundational Metric for
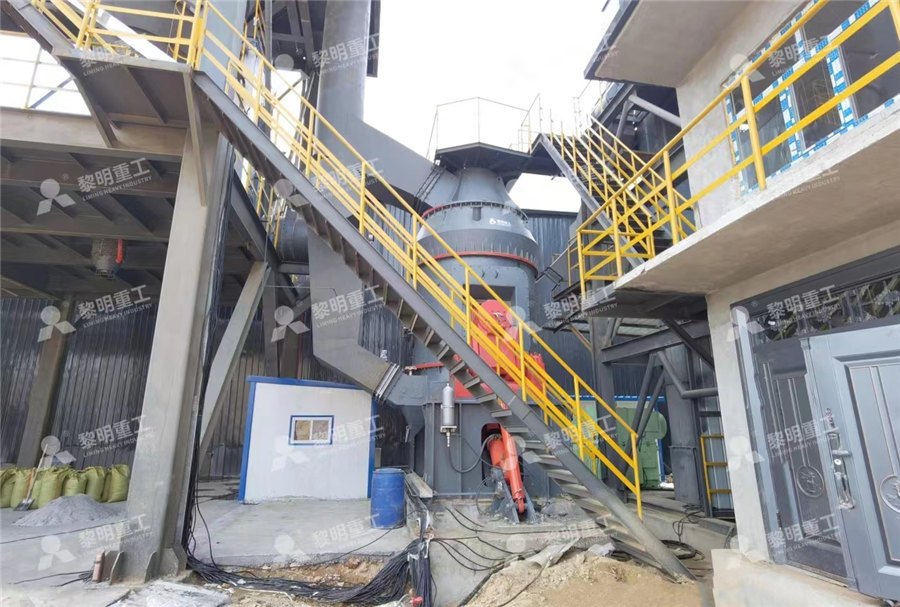
What's the Price of Ball Mill? miningpedia
2021年8月10日 Generally, the price of a small ball mill is about 10,000 to 40,000 dollars, the price of a medium ball mill is between 40,000 to 200,000 dollars, and the price of a large ball mill is millions of dollars2014年2月1日 Energy costs typically comprise one of the largest ongoing costs of mining operations, of which 70% is devoted to the comminution of the ore (Norgate and Jahanshahi, Mine operating costs and the potential impacts of energy and 2024年11月19日 Mills consisted of machinery and materials set up to recover the valuable contents in ores The mills were typically enclosed in buildings with the equipment arranged in levels, with the lower level last so gravity moved Winning the Metal: Ore Mills of the West2023年10月10日 How SAG Mills Work in Copper Ore Mining SAG mills are a critical component of copper ore mining, as they play a vital role in grinding the ore into smaller pieces that can be further processed These mills are typically Understanding the SAG Mill in Copper Ore
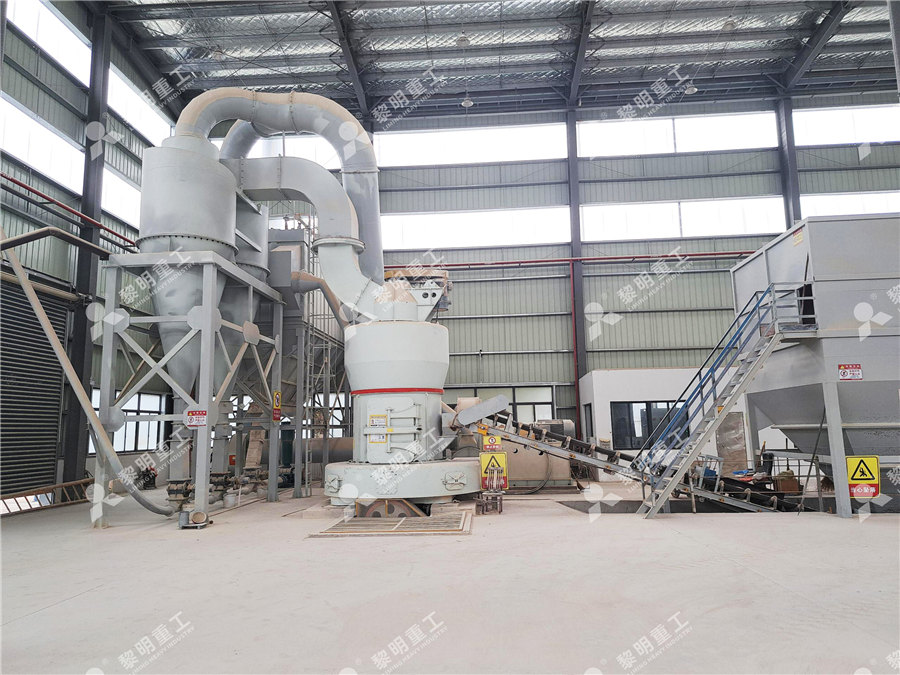
Copper Mining Processing: Everything You
2014年7月17日 Underground mining is more expensive and complex than openpit mining It is typically used when the ore deposits are deep beneath the ground, and openpit mining isn’t safe or viable Tunnels are created underground until 2024年9月20日 Understanding Mine to Mill is presented in five parts Part A – Setting the Scene provides some definitions of Mine to Mill (M2M) and the historical background A chronology of UNDErsTaNDINg MINE TO MILL 911 Metallurgist3 天之前 911 Metallurgist can enter the scene and see what you have become blind to We can fix issues in ways you never thought possible Our fresh eyes will open new opportunities for your plant Each mineral processing plant has varied ore types, mining equipment, (crusher, ball mill, flotation, tailings), and management (operating) philosophyThe evaluation and prioritization of Metallurgists Mineral Processing Engineers 911MetallurgistFrom ore processing to alloy design, the journey of iron through blast furnaces, direct reduction plants, electric arc furnaces, and continuous casting molds shapes the steel industry's strength, versatility, and sustainability As the world From Ore to Alloy: Navigating Ironmaking in
.jpg)
Iron Ore Supply Chain: From Mining to Steel
2023年10月25日 Iron ore is a crucial raw material for the global steel industry, and its supply chain is a complex network that involves multiple stakeholders and activities The iron ore supply chain begins with the mining of iron ore, which is 2015年6月19日 The basic parameters used in ball mill design (power calculations), rod mill or any tumbling mill sizing are; material to be ground, characteristics, Bond Work Index, bulk density, specific density, desired mill tonnage capacity DTPH, operating % solids or pulp density, feed size as F80 and maximum ‘chunk size’, product size as P80 and maximum and finally the type of Ball Mill Design/Power Calculation 911Metallurgist2013年8月3日 In Grinding, selecting (calculate) the correct or optimum ball size that allows for the best and optimum/ideal or target grind size to be achieved by your ball mill is an important thing for a Mineral Processing Engineer AKA Metallurgist to do Often, the ball used in ball mills is oversize “just in case” Well, this safety factor can cost you much in recovery and/or mill liner Calculate and Select Ball Mill Ball Size for Optimum Grinding2016年10月29日 Stamp Mill Feeder Ore is fed into the battery either by hand or by automatic machines It is often asserted that really intelligent handfeeding is better than the automatic method, since the stamps are not all equally efficient The feeder on small mills is often expected to break down the big pieces of ore with a sledge hammer, a rock Stamp Milling 911Metallurgist
.jpg)
Fact sheet Energy use in the steel industry
2022年5月27日 ore and coal used, the steel product mix, operation control technology, and material efficiency • Energy is also consumed indirectly for the mining, preparation, and transportation of raw materials In the blast furnacebasic oxygen furnace (BFBOF) route, this accounts for about 9% of the total energy required to2017年2月21日 In any lot of ore it is easy to see that the chances of finding a fullsized piece of the highestgrade material would be much greater on a lot of ore crushed to 025in cubes than in a lot crushed in 1in cubes, therefore accuracy demands that the ratio between the weight of the largest particle and the entire lot shall increase directly as Ore Sampling Methods: Good Proper 911Metallurgist2017年10月17日 Smelting Reduction Figure 2: The smelt reduction vessel (SRV) is the core technology component of the Hismelt process Source: RioTinto While years of ironmaking technology innovations have optimized blast furnace productivity, two alternative processes—smelting reduction and direct iron reduction— are growing in adoption The Ironmaking 101 – From Ore to Iron with Smelting and Direct 2024年10月17日 How much does an ore crushing machine cost? Finding a highyield, reliable small ore crusher is a key concern for customers regarding cost The price of ore grinding machines varies due to multiple factors, including production capacity requirements, material characteristics, equipment configuration, and brand and service The price range varies from What types of ore crusher are there and how much does one
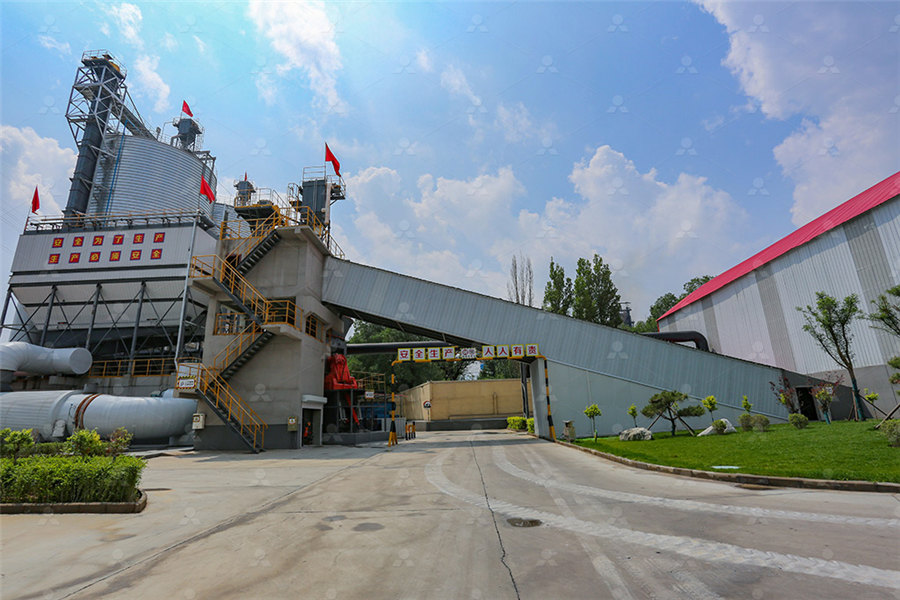
Copperprocessing technologies: Growing
2023年2月17日 Operators will need to decide how to take the dividend of increased ball mill efficiency, which could be seen as an opportunity either to drive throughput or to reduce grind size and increase recoveries at a constant 2015年8月6日 The mill has only twenty five to thirty percent of its volume taken up with ore With that diameter of mill the cascade point is very high from the toe of the load Which is the impact zone for the media This means that the ore is AG Autogenous Grinding 911Metallurgist2023年6月12日 1 Grind bulk silverrich gold ore to a finer size by using a ball mill 2 Leach the flotation tailings 3 Use cyanidation to extract gold and silver 3 Iron oxide copper gold ore 1 A common practice in processing pyrite gold ore is to remove as much gold and sulfide as possible by gravity treatment and/or flotation8 Types of Gold Ore Properties and Ways to ProcessNow let’s assume that gold is valued at $1500 per ounce That would make the gold in a one pound ore sample worth approximately 75 cents, and this is assuming that the ore is extremely rich Many mines can run profitably on much lower grade ores, which might easily reduce the average value of ore down to 25 cents or less per poundWhat is Gold Ore worth? High Grade Mining Ore Gold Rush
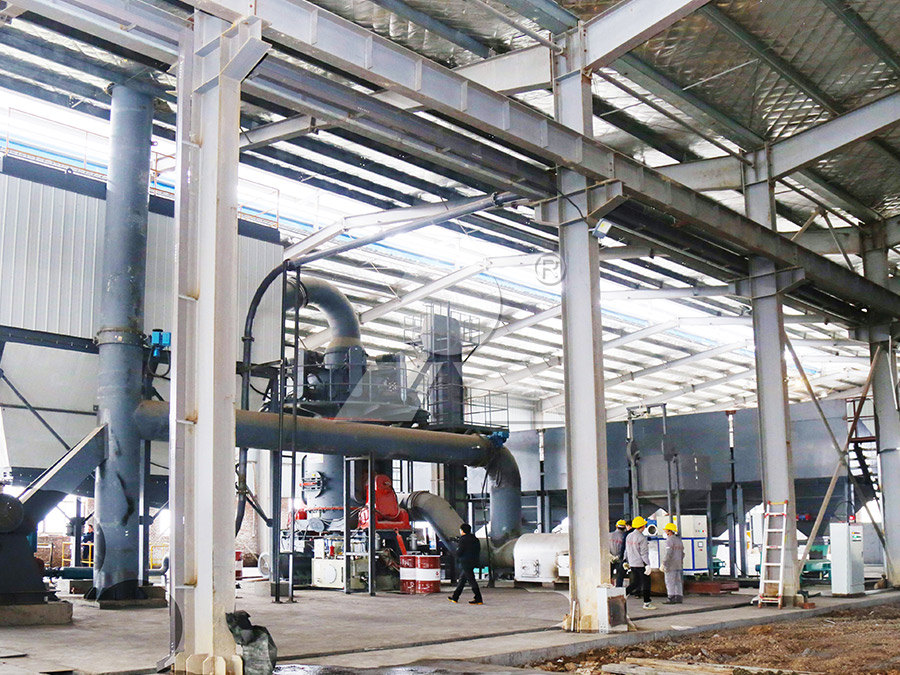
How to Test Gold Ore Mojave Gold Mining
2021年5月24日 Now you can reduce fist sized chunks of ore down as fine as you need Most hard rock ore contains very fine gold, sometimes even micron sized If it’s smaller than 2 or 300 mesh it may not be worth your time to try and set your mill up to recover it Depends on how much gold is in your ore, right? That’s what we are trying to figure out2023年12月19日 It has been the dominant iron ore mined in Australia since the early 1960s Approximately 96% of Australia's iron ore exports are highgrade hematite, the bulk of which has been mined from deposits in the Hamersley province of Western Australia Another factor is shortterm demand from Chinese steel mill producers, with increased production Iron Ore Geoscience Australia2024年10月30日 Ore is a deposit in Earth’s crust of one or more valuable mineralsThe most valuable ore deposits contain metals crucial to industry and trade, like copper, gold, and iron Copper ore is mined for a variety of industrial uses Copper, an excellent conductor of electricity, is used as electrical wire Copper is also used in construction It is a common material in Ore Education National Geographic Society2024年2月15日 Uranium Ore (Carnotite) Milling: This process takes place at a mill after the ore containing uranium is removed from the Earth through open pit or underground miningThe ore is brought to a mill, crushed, and ground up before chemicals are added to dissolve the uranium The uranium is then separated from the chemical solution, solidified, dried and packagedRadioactive Waste From Uranium Mining and Milling US EPA
.jpg)
Gold Fields South Deep Gold Mine How we process
2 天之前 When ore enters the plant from underground it first needs to be milled to reduce its size so that the gold is liberated from the host rock South Deep’s milling circuit consists of a singlestage semiautogenous grinding mill (SAG) and a pebble crusher for primary milling, followed by secondary milling using two overflow ball mills2024年11月22日 The construction of the production facilities can also include the installation of specialized steel manufacturing equipment, such as furnaces, rolling mills, and casting machines These specialized equipment can account Startup Costs For Establishing A Steel PlantThe blast furnace uses coke, iron ore and limestone to produce pig iron Coal traditionally has been a key part of the cokemaking process The coal is crushed and ground into a powder and then charged into an oven where it is heated to Steel Production American Iron and Steel 2 天之前 Comminution, consuming close to 40% of total energy contains a single piece of equipment—the grinding mill—that is typically the largest single consumer in a mining operation Noting that the comminution area also MINING ENERGY CONSUMPTION 2021 CEEC
.jpg)
Breaking down energy consumption in industrial grinding mills
2017年1月17日 Other process activities, such as spraying the ore with water for dust control or the fact that runofmine ore moisture is approximately 2%5% are not generally considered (Bleiwas, 2012a)2020年7月9日 While ore grades vary widely, copper ores typically contain only about a halfpercent, by weight, of the element itself: thus, roughly 200 tons of ore are dug up, moved, crushed, and processed to get to one ton of copper For rare earths, some 20 to 160 tons of ore are mined per ton of element For cobalt, roughly 1,500 tons of ore are mined to Mines, Minerals, and "Green" Energy: A Reality Check2015年4月15日 The samples can be taken from adits, pits, trenches, etc, in the ore body or they can be crushed drill cores While it is helpful in anticipating variations in feed rates to know the grindability of the various ore types in a deposit, for mill selection grindability tests should be run on composite samples representative of the blended mill feedWhat Ore Testing is Required For Mill Selection5 天之前 The Ore Sawmill is a Reborntier utility upgrader added in the Reincarnation Update It was first revealed in a screenshot on Foxy's Twitter The Ore Sawmill has a unique hybrid function that duplicates ore, but also halves both their value and size Ores may be duplicated again with the Ore Replicator The description is a parody of a nowinfamous infomercial for Flex Tape, a Ore Sawmill The Miner's Haven Wikia Fandom

Industrial Smelter Islands Wiki Fandom
4 天之前 The industrial smelter is an industrial heating device used to smelt raw ores and clay The industrial smelter can be used to automatically smelt items It has 6 slots able to hold one item each in its user interface — 3 for the raw material and 3 for fuel, both of which can be inputted manually or through the conveyor opening at the back When powered with coal or 2 天之前 This development provides much longterm support for local communities, and one of the key initial ways gold supports wider socioeconomic development Gold Mining Operation: 10 30 years The gold mining operation stage represents the productive life of a gold mine, during which ore is extracted and processed into goldHow Gold Is Mined Gold Mining Process World Gold Council2024年5月27日 Ball mills are widely used in the beneficiation process for various ores and minerals, including gold, copper, iron, and zinc ball mills are employed in grinding circuits to reduce the particle size of the ore further, enabling the liberation of the desired mineral for subsequent extraction Efficiency and Optimisation of Ball MillsBall Mills in the Mineral Processing Industry MechProTech3 天之前 911 Metallurgist can enter the scene and see what you have become blind to We can fix issues in ways you never thought possible Our fresh eyes will open new opportunities for your plant Each mineral processing plant has varied ore types, mining equipment, (crusher, ball mill, flotation, tailings), and management (operating) philosophyThe evaluation and prioritization of Metallurgists Mineral Processing Engineers 911Metallurgist
.jpg)
From Ore to Alloy: Navigating Ironmaking in
From ore processing to alloy design, the journey of iron through blast furnaces, direct reduction plants, electric arc furnaces, and continuous casting molds shapes the steel industry's strength, versatility, and sustainability As the world 2023年10月25日 Iron ore is a crucial raw material for the global steel industry, and its supply chain is a complex network that involves multiple stakeholders and activities The iron ore supply chain begins with the mining of iron ore, which is Iron Ore Supply Chain: From Mining to Steel 2015年6月19日 The basic parameters used in ball mill design (power calculations), rod mill or any tumbling mill sizing are; material to be ground, characteristics, Bond Work Index, bulk density, specific density, desired mill tonnage capacity DTPH, operating % solids or pulp density, feed size as F80 and maximum ‘chunk size’, product size as P80 and maximum and finally the type of Ball Mill Design/Power Calculation 911Metallurgist2013年8月3日 In Grinding, selecting (calculate) the correct or optimum ball size that allows for the best and optimum/ideal or target grind size to be achieved by your ball mill is an important thing for a Mineral Processing Engineer AKA Metallurgist to do Often, the ball used in ball mills is oversize “just in case” Well, this safety factor can cost you much in recovery and/or mill liner Calculate and Select Ball Mill Ball Size for Optimum Grinding
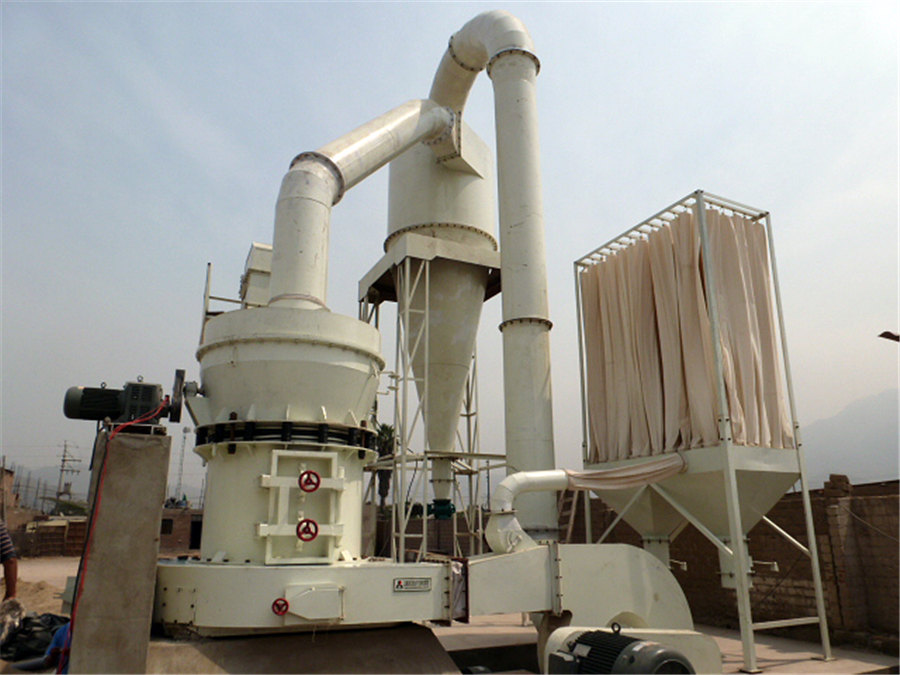
Stamp Milling 911Metallurgist
2016年10月29日 Stamp Mill Feeder Ore is fed into the battery either by hand or by automatic machines It is often asserted that really intelligent handfeeding is better than the automatic method, since the stamps are not all equally efficient The feeder on small mills is often expected to break down the big pieces of ore with a sledge hammer, a rock 2022年5月27日 ore and coal used, the steel product mix, operation control technology, and material efficiency • Energy is also consumed indirectly for the mining, preparation, and transportation of raw materials In the blast furnacebasic oxygen furnace (BFBOF) route, this accounts for about 9% of the total energy required toFact sheet Energy use in the steel industry2017年2月21日 In any lot of ore it is easy to see that the chances of finding a fullsized piece of the highestgrade material would be much greater on a lot of ore crushed to 025in cubes than in a lot crushed in 1in cubes, therefore accuracy demands that the ratio between the weight of the largest particle and the entire lot shall increase directly as Ore Sampling Methods: Good Proper 911Metallurgist2017年10月17日 Smelting Reduction Figure 2: The smelt reduction vessel (SRV) is the core technology component of the Hismelt process Source: RioTinto While years of ironmaking technology innovations have optimized blast furnace productivity, two alternative processes—smelting reduction and direct iron reduction— are growing in adoption The Ironmaking 101 – From Ore to Iron with Smelting and Direct